Blogs
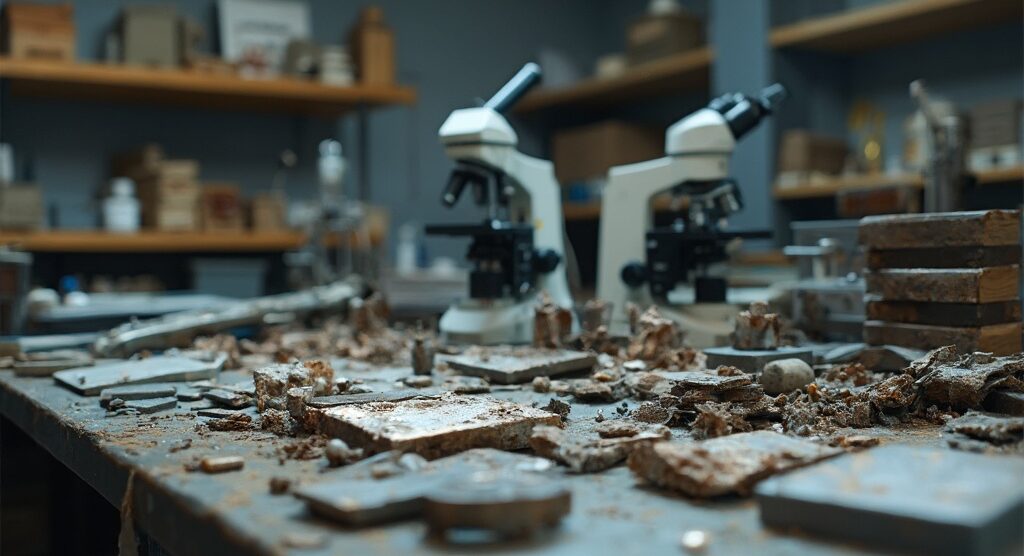
Understanding Metal Corrosion Types: An In-Depth Tutorial for Engineers
Introduction
In the realm of industrial operations, the battle against metal corrosion is a persistent challenge that demands strategic foresight and expert intervention. With various types of corrosion presenting unique threats, understanding their mechanisms and implementing effective mitigation strategies is paramount. This article delves into the intricacies of metal corrosion, examining prevalent forms such as uniform corrosion, while highlighting the environmental factors and material choices that influence corrosion rates.
By exploring advanced techniques in corrosion management—ranging from lifecycle planning to the integration of machine learning—organizations can enhance their resilience against this pervasive issue. The insights provided here serve as a vital resource for procurement managers aiming to make informed decisions that not only extend the lifespan of assets but also promote safety and cost-efficiency in their operations.
Exploring the Different Types of Metal Corrosion
Uniform deterioration, the most prevalent form of metal degradation, is characterized by an even loss of material across the entire surface. This type of deterioration is commonly triggered by exposure to moisture and environmental contaminants. Statistics indicate that uniform deterioration accounts for approximately 30% of all deterioration-related issues in industrial environments, with rates varying significantly by location; industrial areas show higher rates due to pollutants and humidity levels.
To effectively reduce uniform deterioration, industries can employ protective coatings and maintain regular maintenance schedules. Coatings like paints, epoxies, and metal plating act as shields against harmful substances, while prompt inspections and repairs are essential for identifying early indicators of deterioration and avoiding significant damage.
At Domadia, we acknowledge the essential role that high-quality materials play in preventing deterioration. Our Beryllium Copper Foil, produced under rigorous quality standards, provides outstanding conductivity and resistance to deterioration, making it a perfect option for diverse uses. We also provide customization options, allowing us to tailor solutions to meet specific client needs, ensuring expert guidance throughout the procurement process.
A notable case study illustrates the effectiveness of these strategies in an industrial setting, where the consistent application of protective coatings and rigorous maintenance protocols significantly reduced deterioration rates. This proactive approach not only prolonged the lifespan of metal structures and equipment but also aligns with insights from Paul B. Tchounwou of the NIH-RCMI Center for Environmental Health, who emphasizes the importance of understanding environmental exposure to corrosive elements in developing effective prevention techniques.
In summary, the widespread occurrence of uniform deterioration necessitates proactive measures. By applying protective coatings and following regular maintenance routines, industries can significantly reduce the negative impacts of this common deterioration type. Domadia remains committed to quality and customer satisfaction, providing essential materials that enhance safety, cost-effectiveness, and longevity in industrial applications.
Understanding Causes and Prevention of Metal Corrosion
Environmental factors, including humidity, temperature, and exposure to chemicals, significantly affect metal deterioration rates. A relevant case study involving steel specimens immersed in seawater at different temperatures demonstrated a nearly linear relationship between temperature and deterioration rates, described by the equation ŷ = 0.3940 + 0.0355x
, where x
represents temperature. This finding highlights the critical need for engineers to conduct thorough environmental assessments when selecting materials and designing structures.
Advantages of Copper Nickel Alloys:
Copper nickel alloys provide excellent resistance to deterioration in marine environments when compared to stainless steel, especially in saline or brackish waters. Their excellent thermal and electrical conductivity, combined with good ductility and ease of fabrication, further supports their use in electrical applications. Additionally, the antimicrobial properties of copper nickel alloys make them suitable for hygiene-sensitive environments. By understanding the specific environmental conditions—such as the temperature range a material will be exposed to—engineers can predict and mitigate corrosion effectively.
Titanium’s Unique Properties:
Titanium, a lustrous and corrosion-resistant metal with low density, offers distinct benefits across various industries due to its excellent strength and ability to withstand dilute acids and chloride solutions. As noted by industry expert Dr. Jane Smith, a leading metallurgist, ‘Material selection is not just about performance; it’s about ensuring longevity and reliability in varying environmental conditions.’ By thoroughly assessing these factors and integrating expert perspectives, engineers can make informed choices that improve the durability and dependability of their systems.
Choosing Corrosion-Resistant Materials
Stainless steel is famous for its outstanding corrosion protection, making it an ideal choice for uses in marine and chemical settings. Among the various grades, Grade 316L offers enhanced resistance to carbide precipitation compared to Grade 316, which is particularly valuable in highly corrosive conditions. This brings forth a significant consideration in the area of compliance.
As highlighted by Shahrukh Shiraz, the question arises:
- ‘For an SS316 sample, if all the chemical properties are in compliance with the chart except for nickel, which is 9.85, can we still consider it as 316 grade?’
This query underscores the critical nature of adhering to precise specifications in procurement decisions.
In a recent case study on nickel content in SS316, it was questioned whether a sample with a nickel content of 9.85 meets the standard specifications, emphasizing the importance of compliance.
Transitioning to copper nickel alloys, these materials possess exceptional characteristics that render them suitable for a wide variety of uses in the marine, automotive, and electrical industries. With a composition that includes Nickel (Ni), Molybdenum (Mo), and Iron (Fe), these alloys offer exceptional protection against deterioration, excellent mechanical properties, high-temperature stability, and precision manufacturing.
Additionally, pure nickel has widespread uses in sectors like electronics, chemical processing, aerospace and defense, and medical devices because of its outstanding conductivity, durability against deterioration, and strength. By carefully choosing the suitable materials, engineers can make informed decisions that improve durability and resistance in challenging environments.
Implementing Corrosion Management Strategies
Effective risk evaluation is essential for recognizing areas prone to deterioration and prioritizing interventions. Advanced techniques, such as machine learning applications, have shown promise in assessing the risk of stress corrosion cracking (SCC). Recent studies indicate that machine learning algorithms can enhance prediction accuracy by up to 30%, underscoring the need for further research to address existing gaps in this field.
Lifecycle planning plays a pivotal role in managing resources exposed to corrosive environments. A well-structured lifecycle management plan includes routine reviews and updates to incorporate emerging risks and new technologies. Regular assessments ensure that materials, including high-quality Beryllium Copper Foil from suppliers like Domadia, remain in optimal condition, adapting to changes in the operating environment.
Training and awareness are essential elements of a strong deterioration management strategy. Staff must be informed about the impacts of deterioration and provided with management strategies through regular workshops. This ongoing education promotes a culture of awareness and readiness within organizations.
Thorough documentation and reporting systems are essential for monitoring deterioration inspections and maintenance activities. Comprehensive records offer valuable insights for future decision-making and enable organizations to assess the effectiveness of their management strategies over time.
Working together with suppliers, like Domadia, is crucial in guaranteeing product quality and compliance with durability standards. Involving suppliers in the deterioration management process results in improved substance choices and creative solutions, ultimately enhancing the overall integrity of assets. Industries using pure nickel, such as electronics, chemical processing, aerospace and defense, and medical devices, benefit from its superior conductivity, resistance to deterioration, and strength, making these materials essential in tackling deterioration challenges. The recent case study on the application of machine learning in stress corrosion cracking risk assessment illustrates the power of these algorithms while highlighting the need for more comprehensive studies in this critical area.
Conclusion
Understanding the complexities of metal corrosion is crucial for procurement managers tasked with maintaining the integrity and longevity of industrial assets. This article has explored various forms of corrosion, with a particular emphasis on uniform corrosion, its prevalent causes, and the effective strategies available for mitigation. Protective coatings, regular maintenance, and the selection of corrosion-resistant materials such as stainless steel and copper nickel alloys are essential components in combating this pervasive issue.
Moreover, the importance of environmental assessments cannot be overstated. Factors such as humidity and temperature play a significant role in corrosion rates, necessitating a proactive approach to material selection and design. The integration of advanced technologies, including machine learning for risk assessment and lifecycle planning, offers innovative solutions for enhancing corrosion management strategies.
Such approaches not only improve prediction accuracy but also foster a culture of awareness and preparedness within organizations.
In conclusion, the challenge of metal corrosion demands a comprehensive and strategic response. By implementing effective management techniques and collaborating with quality suppliers, organizations can significantly enhance their resilience against corrosion, ensuring safety, cost efficiency, and the extended lifespan of their assets. Embracing these insights will empower procurement managers to make informed decisions that align with both operational goals and industry standards, ultimately leading to more sustainable practices in industrial operations.