Blogs
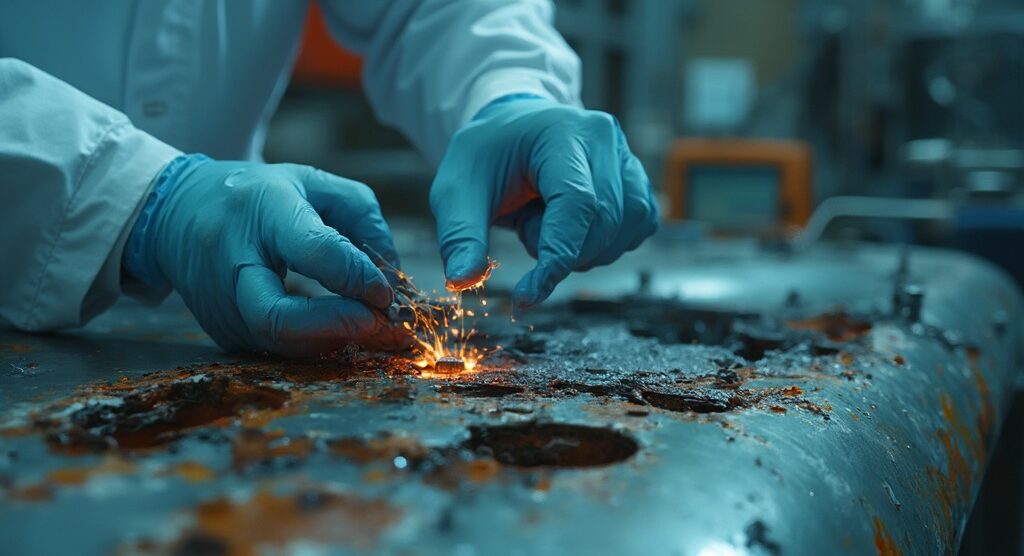
What Is Nickel Corrode? Understanding the Basics of Nickel Corrosion
Introduction
In the realm of materials engineering, understanding the intricacies of nickel’s corrosion resistance is paramount for procurement managers aiming to enhance the durability and reliability of their products. Nickel, renowned for its ability to form a protective oxide layer, offers exceptional resilience against aggressive environments, making it a preferred choice in industries ranging from aerospace to chemical processing. This article delves into the critical factors influencing nickel’s performance, including the role of alloying elements, environmental conditions, and strategic mitigation techniques.
By exploring the economic implications of nickel corrosion and the best practices for selecting and maintaining nickel-based materials, professionals can make informed decisions that not only safeguard their operations but also drive long-term cost efficiency and sustainability.
Understanding Nickel’s Corrosion Resistance Properties
Nickel’s reputation for outstanding durability against deterioration is mainly attributed to the development of a passive oxide layer on its surface. This protective barrier reduces additional oxidation and deterioration, making these metals highly suitable for use in various aggressive environments. Significantly, nickel-based materials can operate efficiently in up to 85% phosphoric acid at boiling temperatures, showcasing their strong durability features.
Recent advancements emphasize the significance of alloying elements like molybdenum and chromium in improving the resistance of nickel-based materials to deterioration. For example, nickel-molybdenum and nickel-chromium-molybdenum compositions are particularly effective in managing ‘wet process’ phosphoric acid, as demonstrated by their performance in phosphoric acid with different purity levels. Specific studies showcase their effectiveness in both high and low purity conditions, reinforcing their reliability in critical applications.
The passive oxide layer plays a crucial role in this context, as it not only provides an initial barrier to corrosion but also enhances the overall durability of metal alloys in corrosive environments. This layer’s capacity to self-repair in the presence of corrosive elements is a key factor in the metal’s long-term performance.
In practical applications, the metal’s resilience is leveraged in industries requiring reliable performance under corrosive conditions, such as marine equipment, chemical processing, and aerospace components. The capability of nickel mixtures to endure such challenging environments guarantees long-term durability and reliability of the components. This is complemented by the use of Non-Sparking Tools, which serve as an essential alternative in explosive environments, and Mica Tape Products, designed for high-temperature resistance and electrical insulation in diverse applications.
Expert insights further validate these findings. Raul B. Rebak, a corrosion engineer, observes that ‘Nickel-based materials are susceptible to stress corrosion cracking in the presence of aqueous solutions of hydrofluoric acid.’ This emphasizes the necessity of careful material selection based on specific environmental conditions, particularly in applications involving aggressive chemicals.
Understanding these properties is crucial for professionals when selecting materials for specific applications. It ensures that the chosen materials will deliver optimal performance and reliability over extended periods, even in the most challenging environments. Additionally, at Domadia, we offer custom solutions tailored to meet unique requirements for copper nickel alloys, allowing for specific alloy compositions, dimensions, and surface finishes to suit your industrial applications.
Conditions Leading to Nickel Corrosion
Nickel degradation is significantly influenced by environmental factors, including pH levels, temperature, and the presence of chlorides. For instance, weight loss measurements at pH 9 reveal a range of 0.07 mg to 0.13 mg, indicating the nuanced effect of pH on deterioration rates. Highly acidic or alkaline environments can compromise the protective oxide layer, increasing vulnerability to deterioration. This is especially vital in areas like heat exchangers, automotive systems, and marine engineering, where high temperatures and saline conditions can hasten deterioration processes.
Copper nickel alloys, recognized for their excellent durability against deterioration, surpass stainless steel in marine settings, making them perfect for parts such as ship hulls and seawater piping systems. They are also valuable in the automotive sector for brake lines and hydraulic systems, as well as in electronics and coin production due to their excellent conductivity and resistance to deterioration. Chloride ions, common in seawater and de-icing agents, pose a substantial threat by penetrating the protective layer and initiating pitting damage.
The study by Mareci D and associates on the electrochemical behavior of non-precious nickel and cobalt-based alloys in artificial saliva emphasizes the intricate interaction of environmental factors in deterioration dynamics. They discovered that increased iron levels in chromium coatings resulted in the development of a duplex oxide layer, greatly influencing durability and the rate of oxide formation. This finding emphasizes how particular environmental conditions can dramatically change resistance to rust, a crucial consideration for procurement managers.
Additionally, Zahra Ghiasvand’s insights on optimal conditions for synthetic photocatalysts highlight the significance of precise environmental control in degradation processes. She observes that factors such as temperature and pH can dramatically affect the performance of materials, emphasizing the necessity for procurement managers to understand these conditions when assessing alloys for specific applications. By understanding the relationship between environmental factors and metal deterioration, procurement managers can develop effective strategies for reducing deterioration risks while considering high purity sheets and other metal categories like Beryllium Copper and Rare Earth Materials.
Strategies for Mitigating Nickel Corrosion
To effectively mitigate corrosion of the metal, several strategic approaches can be implemented. Primarily, choosing the suitable metal mixture from our diverse product ranges—such as high purity sheets and custom sputtering targets like Chromium—designed for specific environmental conditions is essential. For example, metal mixtures with added chromium or molybdenum exhibit improved performance in highly corrosive settings, providing superior resistance. Recent assessments have shown that alloys like Ni-Cr-Mo are particularly effective in pure phosphoric acid, known for their ability to withstand aggressive chemical attack, while G-30 alloys excel in ‘wet process’ phosphoric acid, providing reliable performance under similar conditions.
One effective strategy involves the application of protective coatings, such as electroplating or specialized paints. These coatings act as an extra layer of defense against corrosive agents, with advancements in coating technologies enhancing their protective capabilities. For instance, recent advancements in polymer-based coatings have demonstrated potential in greatly prolonging the lifespan of nickel components in challenging settings, providing procurement managers a practical approach for managing deterioration.
Additionally, regular maintenance and thorough monitoring are critical components of a robust deterioration management strategy. Routine inspections can detect early signs of corrosion, enabling timely corrective actions and preventing extensive damage. This proactive approach not only safeguards the integrity of metal components but also optimizes their performance over time, aligning with best practices in procurement management.
Proper storage and handling procedures are equally vital. By minimizing exposure to harmful conditions, the lifespan of metal components can be significantly extended. For example, nickel alloys have been proven to withstand up to 85% pure phosphoric acid at boiling temperatures, underscoring their resilience when appropriately managed.
These strategies underscore the importance of a proactive approach in ensuring the longevity and reliability of nickel-based materials. By adopting these best practices, including considerations for Beryllium copper and Kovar in related applications, procurement managers can enhance their resistance protocols, ultimately contributing to more sustainable and efficient operations.
The Economic Impact of Nickel Corrosion
Nickel deterioration can lead to significant economic repercussions, particularly in sectors where downtime and maintenance costs are paramount. Corrosion-related failures often result in expensive repairs, production delays, and potential safety hazards, all negatively impacting a company’s profitability. For example, in the automotive sector, deterioration of metal parts can lead to expensive recalls and warranty requests. A significant case involved a leading automotive producer facing an estimated $100 million in losses due to a metal deterioration problem that required a large-scale recall of impacted vehicles. The expense of replacing corroded materials is also considerable, factoring in both labor and downtime.
At Domadia, we provide a variety of copper-based mixtures specifically crafted for various industrial uses, including shielding, electronics, and power transformers. Investing in corrosion-resistant materials, such as those enhanced with SilcoTek coatings, can significantly mitigate these issues. SilcoTek coatings form a non-stick, highly resistant barrier against corrosion, enhancing the durability of stainless steel and decreasing the dependence on expensive alloys in various applications. This presents a cost-effective alternative for businesses looking to enhance their product durability.
Additionally, our DOMADIA Polyimide Film provides high temperature, chemical, and mechanical resistance, further contributing to overall product resilience.
Proactive maintenance strategies can also enhance product longevity, yielding long-term cost savings and operational efficiency. Recent projections estimate demand for the metal to reach 3.18 million metric tons in 2022, with anticipated growth to between 4.5 and 5.9 million tons by 2030. This highlights the significance of efficient metal utilization and recycling to meet future needs. Grasping the economic effect of nickel deterioration is essential for procurement managers seeking to make informed choices aligned with their organization’s financial goals. By prioritizing corrosion resistance and tapping into our custom solutions for tailored composition, dimensions, and surface finishes, businesses can avoid the high costs associated with corrosion failures and achieve sustained economic benefits.
Conclusion
Nickel’s corrosion resistance plays a vital role in ensuring the longevity and reliability of components across various industries. The formation of a passive oxide layer, enhanced by strategic alloying elements such as molybdenum and chromium, provides nickel and its alloys with exceptional protection against aggressive environments. Understanding the environmental factors that influence corrosion, including pH levels, temperature, and the presence of chlorides, is essential for procurement managers to make informed material selections that optimize performance.
Implementing effective mitigation strategies—such as selecting appropriate nickel alloys, applying protective coatings, and conducting regular maintenance—can significantly enhance the resilience of nickel components. These proactive measures not only safeguard material integrity but also contribute to long-term cost efficiency and sustainability. Furthermore, recognizing the economic implications of nickel corrosion, particularly in sectors prone to costly repairs and downtime, underscores the importance of investing in high-quality, corrosion-resistant materials.
In conclusion, a comprehensive understanding of nickel’s properties, the conditions leading to its corrosion, and the strategic approaches to mitigate these risks empowers procurement managers to make decisions that enhance product durability and operational efficiency. By prioritizing corrosion resistance, organizations can not only protect their investments but also drive sustainable growth in an ever-evolving marketplace.