Blogs
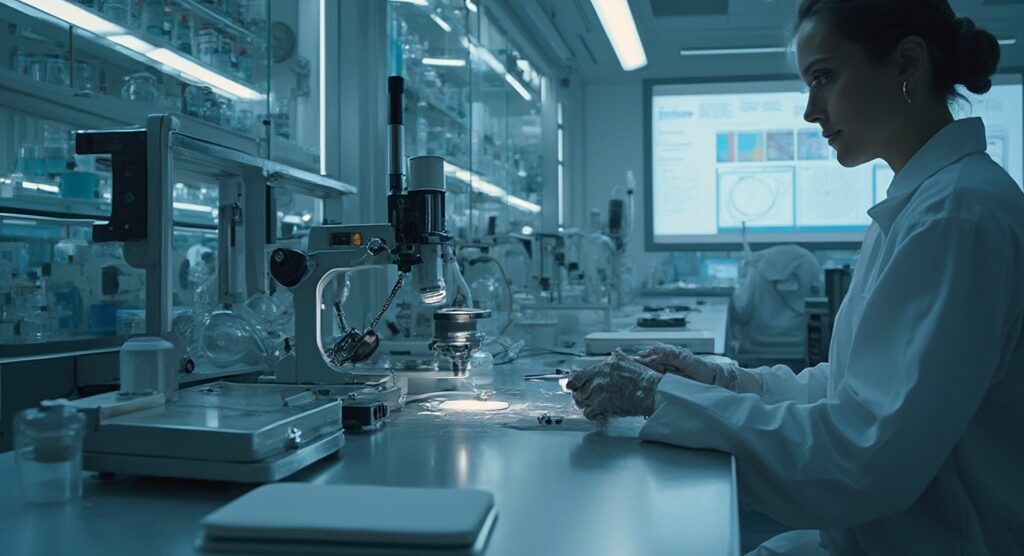
Understanding UNS N06625: A Complete Tutorial on Properties and Applications
Introduction
In the realm of advanced materials, UNS N06625, commonly known as HAYNES 625, stands out as a premier nickel-chromium-molybdenum superalloy, engineered to excel under extreme conditions. Its unique composition, featuring a significant percentage of nickel, chromium, and molybdenum, grants it exceptional strength and remarkable resistance to oxidation and corrosion, making it an indispensable choice for industries such as aerospace, chemical processing, and marine applications. As organizations seek to enhance performance and reliability in high-temperature environments, understanding the key characteristics and applications of this alloy becomes crucial.
This article delves into the various aspects of UNS N06625, exploring its composition, corrosion resistance, fabrication techniques, and the strategic advantages it offers to procurement managers navigating the complexities of material selection in demanding industrial settings.
Overview of UNS N06625: Key Characteristics and Description
UNS N06625, referred to as HAYNES 625, is a nickel-chromium-molybdenum alloy acknowledged for its exceptional strength and ability to withstand oxidation at high temperatures. This superalloy, made up of around 58% nickel, 22% chromium, and 9% molybdenum, along with minor components like titanium and aluminum, is designed for high-performance uses. Its composition, which includes Nickel (Ni), Molybdenum (Mo), and Iron (Fe), offers superior corrosion protection, excellent mechanical properties, and high-temperature stability, making it essential for sectors such as aerospace, chemical processing, and power generation.
HAYNES 625 demonstrates strong performance in short-term uses up to 815°C (1500°F), with light forging suggested down to 926°C (1700°F). Recent advancements highlight its utilization in heat exchangers and gas turbine components, emphasizing its versatility and reliability. In real-world uses, like the ones outlined in the Super Alloy HAYNES 625 case study, the substance shows remarkable durability against stress-corrosion cracking, preserving integrity even in extreme conditions.
For professionals seeking high-temperature electrical insulation solutions, Domadia offers a comprehensive range of Mica Tapes designed for demanding environments. These products, along with other electrical insulation substances like papers, fabrics, and metals, offer dependable choices for procurement managers concentrating on high-temperature applications. Domadia is committed to delivering quality solutions that meet the rigorous demands of modern engineering.
Applications of UNS N06625: Industries and Use Cases
UNS N06625 is extensively utilized in the aerospace, chemical processing, and marine sectors because of its outstanding strength and durability against corrosion and oxidation. In aerospace, it is utilized in components such as turbine engines and exhaust systems. Similarly, in chemical processing, it is ideal for heat exchangers and reactors exposed to harsh environments. The marine industry employs UNS N06625 for offshore oil and gas platforms, where resilience against seawater corrosion is critical.
Furthermore, the use of Non-Sparking Tools is crucial in explosive environments, ensuring safety while handling substances that may include pure nickel. Sectors like electronics, aerospace, and medical devices depend on pure nickel for its outstanding conductivity and durability against corrosion, which enhances the use of high-temperature substances like electrical insulation papers and fabrics from various suppliers.
These high-temperature materials are critical in maintaining performance and safety in extreme conditions, further highlighting the importance of selecting the right tools and materials in these industries.
Corrosion Resistance of UNS N06625: Performance Insights
UNS N06625, a significant copper nickel mixture, demonstrates exceptional durability against pitting, crevice corrosion, and stress corrosion cracking, making it a superb option for conditions that involve seawater, hydrochloric acid, and sulfuric acid. Its ability to maintain integrity under high temperatures and pressures further enhances its performance.
Laboratory tests have indicated that UNS N06625 can endure corrosive assaults notably better than many other materials, solidifying its status as a preferred selection in challenging conditions. Moreover, copper nickel mixtures, including UNS N06625, are acknowledged for their exceptional corrosion durability, outstanding thermal and electrical conductivity, good ductility, ease of fabrication, and antimicrobial characteristics, making them especially beneficial in marine settings and electrical uses.
For those obtaining supplies, our selection of mica tape products provides high-temperature resistance and electrical insulation, ensuring reliability across various applications, thus enhancing the advantages of copper nickel mixtures.
Fabrication and Heat Treatment of UNS N06625: Techniques and Considerations
When working with UNS N06625, employing the correct fabrication techniques is crucial to preserving its advantageous properties. For welding, gas tungsten arc welding (GTAW) and gas metal arc welding (GMAW) are advised, using compatible filler substances to ensure cohesion and preserve the integrity of the metal. Heat treatment processes typically involve temperatures ranging from 1000°F to 2100°F (538°C to 1150°C), which are essential for enhancing the mechanical properties of the alloy.
Alongside UNS N06625, various high-temperature materials, including Mica Tape products, play a critical role in electrical insulation uses. Mica insulation tape is renowned for its high-temperature durability and exceptional electrical insulation properties, making it indispensable in sectors such as aerospace and industrial machinery. This tape offers flame protection and dielectric strength, which are vital for scenarios involving fire hazards, further enhancing the safety and reliability needed in crucial electrical insulation systems.
The mechanical properties of Alloy 6Mo in the annealed temper include:
1. A minimum tensile strength of 675 MPa
2. A minimum yield strength of 310 MPa
3. A minimum elongation percentage of 40%
These properties underscore the importance of precise heat treatment to achieve desired outcomes. Post-fabrication heat treatments are especially effective in alleviating residual stresses and enhancing resistance to cracking, which is essential for the long-term performance of the substance.
Practical uses, like those seen in the aerospace and chemical processing sectors, showcase the effectiveness of these techniques. For example, case studies have demonstrated that using suggested welding practices significantly decreased occurrences of failure and improved overall durability in high-stress environments. Moreover, pure nickel, known for its outstanding conductivity and corrosion resistance, is widely utilized in electronics, chemical processing, aerospace and defense, and medical devices, further highlighting the significance of choosing the appropriate substances for particular purposes.
Expert insights, such as those from experienced foremen, provide valuable perspectives on best practices. Emphasizing the importance of meticulous attention to detail in welding, one foreman noted the criticality of avoiding defects to ensure product integrity. Advancements in heat treatment processes for superalloys continue to evolve, offering new methods to further enhance the performance of substances like UNS N06625.
In summary, the combination of appropriate welding techniques and accurate heat treatment processes is crucial for attaining the optimal performance of UNS N06625, ensuring its mechanical properties are fully realized and its longevity is maximized, while also considering the essential role of high-temperature substances like Mica Tape in various critical uses.
Chemical Composition of UNS N06625: Understanding Its Makeup
The DOMADIA Nickel Molybdenum Iron Alloy is a high-performance material designed for demanding industrial applications. Composed primarily of nickel, molybdenum, and iron, this mixture exhibits superior corrosion resistance, making it ideal for use in aggressive environments. Its mechanical properties ensure structural integrity and longevity, while high-temperature stability allows it to maintain performance under extreme conditions. Precision manufacturing methods guarantee that the material meets the most exacting requirements of various industries.
In addition to its robust properties, the DOMADIA Nickel Molybdenum Iron Alloy is relevant in the context of Non-Sparking Tools, which are essential for applications in explosive environments. The inherent characteristics of this material provide the necessary safety and reliability for tools used in such settings, preventing sparks that could lead to dangerous situations. As part of the DOMADIA group’s legacy of sourcing exceptional substances since 1952, this composition stands out for its quality and performance, reinforcing our commitment to delivering unmatched customer satisfaction.
Barry Myers, a materials specialist, highlights the importance of high-performance mixtures such as the DOMADIA Nickel Molybdenum Iron composition, stating that such combinations not only offer exceptional strength but are also essential for industrial uses needing durability and reliability. This aligns with real-world applications where this alloy is utilized in various sectors, including aerospace and chemical processing, ensuring optimal performance in high-stress environments.
Conclusion
UNS N06625, or HAYNES 625, emerges as a standout superalloy in demanding industrial applications, characterized by its exceptional strength, oxidation resistance, and corrosion resilience. Its unique composition—predominantly nickel, chromium, and molybdenum—enables it to thrive in high-temperature environments, making it a go-to choice for aerospace, chemical processing, and marine industries. The alloy’s outstanding performance against stress-corrosion cracking and its versatility in applications such as turbine engines and heat exchangers underscore its importance in modern engineering.
Moreover, the superior corrosion resistance of UNS N06625, particularly in aggressive environments, further solidifies its status as a preferred material. Its ability to withstand harsh conditions, such as those found in seawater and various acids, positions it as an ideal candidate for critical applications, from offshore platforms to high-temperature electrical insulation solutions. The insights into fabrication techniques, including recommended welding practices and heat treatment processes, highlight the necessity of precise handling to maintain the alloy’s integrity and mechanical properties.
In summary, understanding the characteristics and applications of UNS N06625 is essential for procurement managers navigating the complexities of material selection. By leveraging its unique properties and employing best practices in fabrication, organizations can optimize performance and reliability in their high-temperature and corrosive environments. As industries continue to evolve, the strategic use of HAYNES 625 will remain pivotal in enhancing operational efficiency and safety.