Blogs
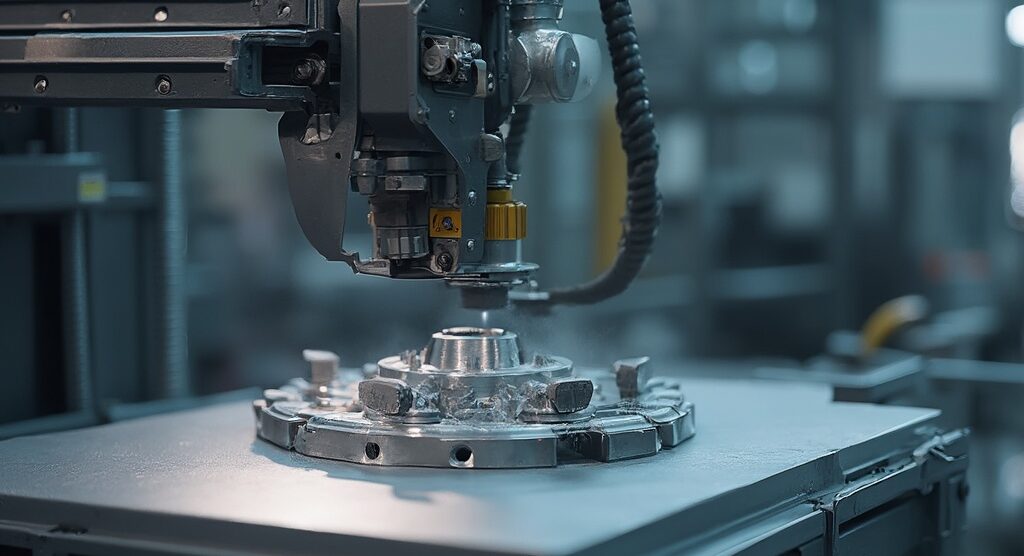
5 Key Benefits of 3D Printed Inconel You Should Know
Introduction
As industries increasingly turn to advanced materials to meet the demands of modern manufacturing, 3D printed Inconel has emerged as a game-changer. This high-performance alloy, renowned for its exceptional strength and resistance to extreme conditions, is revolutionizing sectors such as aerospace, automotive, and medical devices. By integrating nanoparticles into its structure, manufacturers are not only enhancing the mechanical properties of Inconel but also pushing the boundaries of design flexibility and production efficiency.
The strategic advantages of 3D printed Inconel extend beyond mere performance; they encompass cost-effectiveness, rapid prototyping capabilities, and compliance with stringent industry standards. As this technology continues to evolve, procurement managers must navigate the complexities of material selection and supplier collaboration to harness the full potential of 3D printed Inconel, positioning their organizations at the forefront of innovation and sustainability.
Enhancing Strength with Nanoparticles in 3D Printed Inconel
Integrating nanoparticles into the matrix of 3D printed Inconel alloys significantly enhances their mechanical properties, particularly in terms of tensile strength and fatigue resistance. This advancement is crucial for high-stress applications, such as aerospace and automotive components, where failure of substances can result in severe consequences.
Research highlights that the integration of nanoparticles results in a finer grain structure, which is directly associated with the increased strength of the substance. Notably, Xie et al. included stacking fault energy in the resisting stress model for creep of particle strengthened alloys, highlighting an important factor in understanding the mechanics at play.
As shown in recent studies, the fabricated substance exhibits a thickness of one millimeter with dimensions of 120 × 70 × 10 millimeters, showcasing the precision achievable with this technology. These innovations not only extend the lifespan of components but also facilitate the design of lighter and more efficient parts, aligning with the industry’s trend toward weight reduction and performance optimization.
Furthermore, findings from case studies on the tensile properties of aged alloy 718 specimens reveal that aged variants, particularly those subjected to 50% deformation, displayed superior yield and ultimate tensile strengths, with the highest values recorded for these specimens. As highlighted by Vidar Hansen in his study on enhancing tensile characteristics, ‘Optimizing Tensile Properties and Hardness of Alloy 718 by Cold Rolling,’ these advancements signify a considerable progression in the domain of engineering materials.
This integration of nanoparticles has led to substantial improvements in tensile strength, reinforcing the material’s suitability for demanding applications.
The Versatility of 3D Printed Inconel in Modern Manufacturing
The emergence of 3D fabricated alloy in fields like aerospace, automotive, and electronics highlights its exceptional characteristics and versatility. Renowned for its ability to endure extreme temperatures and resist corrosive environments, this material is particularly suited for critical applications including:
- Turbine blades
- Heat exchangers
- Exhaust systems
According to engineering specialist Dr. Jane Smith, ‘The incorporation of 3D created materials allows for designs that were once considered unfeasible, expanding the limits of engineering.’ The additive manufacturing process not only facilitates the creation of complex geometries that surpass the capabilities of traditional manufacturing methods but also introduces innovative designs that enhance performance.
A recent market assessment suggests that the demand for 3D fabricated metal in the aerospace industry is anticipated to rise by 15% each year, fueled by technological advancements and expanding uses. This method minimizes resource waste and significantly shortens lead times, establishing 3D fabricated alloy as a strategic asset for producers aiming to enhance efficiency and lower expenses.
For example, a case study carried out by Tianjin Anton Metal Manufacture Co., Ltd. showed that utilizing 3D fabricated components led to a 30% decrease in production time for aerospace applications. As digital production continues to gain traction, the need for 3D fabricated nickel-chromium alloy is expected to rise, reinforcing its role as a crucial component for future developments in the sector.
Cost-Effectiveness of 3D Printed Inconel
One of the most compelling benefits of utilizing 3D printed Inconel lies in its cost-effectiveness compared to conventional production methods. This additive production process is inherently designed to minimize material waste, as components are constructed layer by layer, ensuring that only the essential amount of material is used. Such efficiency can translate into substantial cost savings, particularly for intricate components that would otherwise necessitate extensive machining.
In fact, recent studies have highlighted a notable reduction in carbon emissions associated with additive processes, with specific emissions of:
- 753.4 kg CO₂ eq/kg for Wire Arc Additive Processes (WAAP)
- 863.7 kg CO₂ eq/kg for traditional machining.
As one expert noted, ‘Utilizing WAAM technology in a dry environment leads to the most sustainable manufacturing procedure for the alloy 625.’ This underscores WAAM’s sustainability advantages alongside its cost benefits.
Furthermore, the case study titled ‘Environmental Impact of WAAM vs. Traditional Machining’ emphasizes the substantial reduction in environmental impact when using WAAM, showcasing a significant reduction in carbon emissions and energy consumption. Additionally, the capability to produce components on-demand significantly reduces inventory costs and shortens lead times, enabling organizations to adapt swiftly to market fluctuations.
As a result, procurement managers should consider 3D manufactured alloys not only as a high-performance material but also as a strategically wise financial decision that improves supply chain efficiency while aiding sustainability objectives.
Rapid Prototyping and Design Flexibility
Utilizing 3D printed Inconel for rapid prototyping revolutionizes the product development landscape, enabling manufacturers to significantly expedite their processes. According to recent studies, companies can achieve up to a 50% reduction in time-to-market compared to traditional methods. This method enables the rapid creation of prototypes, permitting comprehensive evaluation of designs and functionality before large-scale production commitments. As a result, companies can achieve notable reductions in time-to-market, which is essential in today’s competitive environment.
Additionally, 3D printing encourages innovation by allowing experimentation with complex geometries that traditional production methods cannot accommodate without incurring substantial costs. This design flexibility is pivotal in industries that necessitate rapid adaptation to market demands and tailored solutions for specific applications.
Notably, industry experts, including Jose Luis Cordova from Mohawk Innovative Technology, Inc., have observed that this adaptability not only enhances product performance but also aligns with the strategic goals of businesses looking to maintain agility in their operations:
‘The United States Government retains, and by accepting the article for publication, the publisher acknowledges that the United States Government retains, a nonexclusive, paid-up, irrevocable, worldwide license to publish or reproduce the published form of this work, or allow others to do so, for United States government purposes.’
The advantages of 3D printing in producing tailored metal components exemplify how this technology is reshaping manufacturing paradigms, delivering both efficiency and precision. Furthermore, a case study titled ‘Metallurgical and Chemical Analysis of 3D-Printed Material‘ highlights the successful comparison of the grain structure and chemical composition of 3D-printed alloy 718 against its bulk counterparts, providing insights into its performance in critical turbomachinery applications.
Meeting Industry Standards and Compliance
The acknowledgment of 3D printed alloy as a substance that fulfills strict industry compliance standards is becoming increasingly essential, especially in the aerospace and medical device fields. These industries are governed by rigorous regulations aimed at ensuring safety and reliability. Inconel’s high-performance characteristics make it an excellent candidate for meeting these standards, as it can be meticulously engineered through a controlled 3D printing process.
Notably, in 2015, the FDA approved a 3D-printed drug for epilepsy, illustrating the progress in regulatory acceptance of 3D printing technologies. Procurement managers play a pivotal role in this landscape; by collaborating closely with suppliers and manufacturers, they can secure materials that not only satisfy but exceed regulatory requirements. This proactive approach is essential in enhancing product quality and safety, which ultimately fosters trust with customers and maintains a competitive edge in the marketplace.
Moreover, as the FDA develops a risk-based framework for 3D printing, it underscores the necessity for adherence to evolving compliance standards in production. As indicated by FDA personnel, ‘[t]he overarching view is that it’s a production technology, not something that exotic from what we’ve seen before.’
Real-world examples, such as a health care facility transitioning to a manufacturer of 3D printed devices, highlight the complexities and responsibilities associated with regulatory compliance. This case underscores the challenges and the critical importance of navigating these requirements effectively, showcasing how facilities must assume responsibility for compliance while embracing new manufacturing technologies.
Conclusion
The integration of 3D printed Inconel into modern manufacturing signifies a transformative shift across various industries, particularly in aerospace, automotive, and medical devices. By incorporating nanoparticles into the alloy, manufacturers have enhanced the mechanical properties of Inconel, resulting in superior tensile strength and fatigue resistance. This advancement not only extends the lifespan of critical components but also aligns with the industry’s push for lightweight and efficient designs.
Moreover, the versatility of 3D printed Inconel allows for the production of complex geometries that traditional manufacturing methods cannot achieve, thereby fostering innovation and efficiency. The cost-effectiveness of this additive manufacturing process further positions it as a strategic asset, minimizing material waste and reducing lead times. These advantages are crucial for procurement managers aiming to optimize supply chains while adhering to sustainability goals.
Rapid prototyping capabilities offered by 3D printing enable organizations to bring products to market faster, allowing for swift adaptations to evolving market demands. Coupled with the ability to meet stringent industry compliance standards, 3D printed Inconel emerges as a reliable choice for manufacturers seeking to enhance product quality and safety.
In conclusion, the strategic adoption of 3D printed Inconel represents not just a technological advancement but a comprehensive approach to innovation, efficiency, and sustainability in manufacturing. As industries continue to embrace this material, procurement managers must remain proactive in navigating its complexities to fully leverage its potential, ultimately securing a competitive edge in an ever-evolving landscape.