Blogs
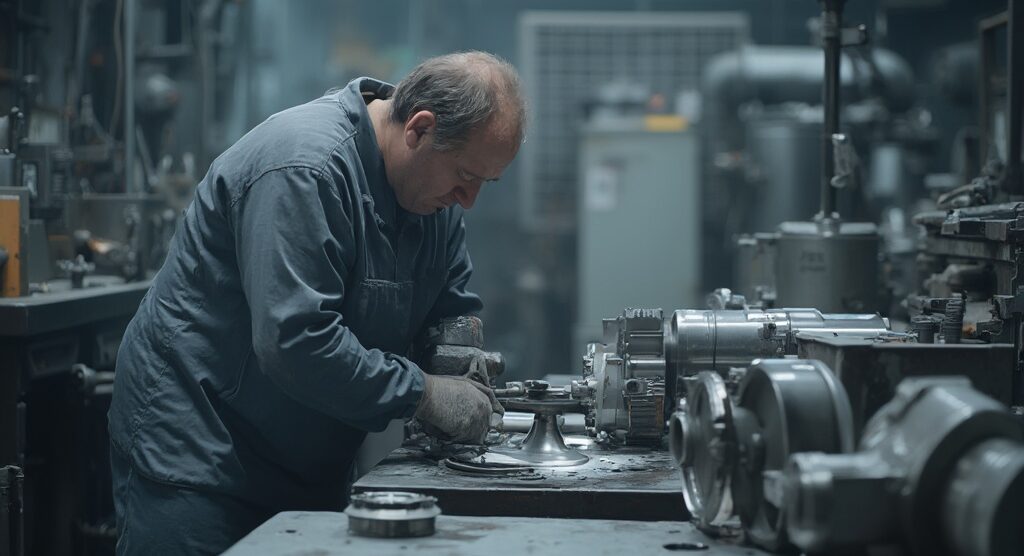
Inconel 625 Forgings: An In-Depth Tutorial on Properties and Applications
Overview:
Inconel 625 forgings are characterized by their exceptional strength, corrosion resistance, and high-temperature durability, making them suitable for demanding applications in industries such as aerospace, oil and gas, and marine environments. The article elaborates on the alloy’s unique composition and mechanical properties, highlighting its ability to withstand extreme conditions without significant degradation, thereby underscoring its value in high-performance engineering applications.
Introduction
Inconel 625, a highly regarded nickel-chromium alloy, has emerged as a cornerstone material in industries that demand exceptional performance under extreme conditions. Its unique composition, featuring a blend of nickel, chromium, and molybdenum, equips it with unparalleled strength, corrosion resistance, and thermal stability, making it ideal for applications ranging from aerospace to oil and gas.
As procurement managers navigate the complexities of material selection, understanding the intricate properties and forging techniques associated with Inconel 625 becomes imperative. This article delves into the alloy’s composition, mechanical properties, and its versatile applications, while also addressing the challenges faced during machining and fabrication.
By highlighting the strategic advantages of Inconel 625, this exploration aims to provide valuable insights for those seeking reliable solutions in high-performance environments.
Understanding Inconel 625: Composition and Properties
The high-quality nickel-chromium blend, referred to as inconel 625 forgings, excels in settings defined by severe oxidation and corrosion. The mixture’s composition typically consists of approximately:
- 58% nickel
- 20% chromium
- 9% molybdenum
- Trace amounts of iron, titanium, and aluminum
This specific formulation endows inconel 625 forgings with remarkable strength and durability, allowing them to endure temperatures reaching up to 2000°F (1093°C).
Its physical attributes are remarkable; inconel 625 forgings feature:
- A hardness range of 145-240 HB
- Excellent weldability, allowing seamless integration into intricate structures
- Impressive fatigue strength, rendering them especially fitting for rigorous uses like aerospace components, chemical processing equipment, and marine environments
Recent studies underscore its corrosion resistance, indicating that post-weld heat treatment is unnecessary for maintaining its integrity, provided standard welding practices, such as those outlined in the case study on the weldability of Alloy 625, are followed. This characteristic, combined with its adaptability in various industrial environments, enhances the desirability of inconel 625 forgings among procurement managers looking for dependable materials for high-performance applications.
The DOMADIA Group, a reliable provider of Nickel Molybdenum Iron Alloy and specialty metals since 1952, guarantees that inconel 625 forgings meet the highest standards of quality and performance. Additionally, our comprehensive catalog assists procurement managers in choosing the appropriate materials, including a specific alloy and our Mica Tape products, which offer outstanding electrical insulation and high-temperature resistance, rendering them essential in numerous sectors, from aerospace to electrical engineering. As one expert noted, ‘Thank you for your quick response,’ highlighting the importance of timely information in material selection.
Applications of Inconel 625 in Modern Industries
Alloy 625 stands out for its exceptional performance across various demanding industries, including aerospace, oil and gas, and marine applications. In the aerospace sector, this nickel-chromium mixture is crucial for manufacturing components subjected to extreme thermal and mechanical stress, such as exhaust systems and combustion chambers. Its ability to maintain structural integrity at elevated temperatures makes it a preferred material for aerospace engineers, who emphasize its reliability in high-performance environments.
Moreover, when combined with Non-Sparking Tools, Inconel 625 enhances safety in explosive environments, ensuring that operations can proceed without the risk of ignition. As noted by Hakaru Masumoto, ‘The hardness shows a very complicated change with the process of heat treatment, cold reduction rate and alloy composition, showing the Vickers hardness of about 100 to 550.’ This insight underscores the material’s complex properties that engineers must consider during application.
In the oil and gas sector, inconel 625 forgings are essential, as they are utilized in valves, piping, and subsea components that require outstanding corrosion resistance. The growing emphasis on longevity and durability in offshore explorations has resulted in a rise in the adoption of inconel 625 forgings, especially as industry activities escalate in 2024. Real-world applications highlight the effectiveness of inconel 625 forgings in harsh environments, as engineers note that their resistance to pitting and crevice corrosion significantly enhances operational safety and efficiency.
The production of nickel-based alloy 625 and similar materials often utilizes Direct Energy Deposition (DED) processes, which are crucial for forming intricate shapes and enhancing material characteristics.
Moreover, the versatility of inconel 625 forgings extends to marine environments, where they are used in heat exchangers and components of nuclear reactors. This alloy’s reliability in corrosive environments demonstrates its versatility and the strategic benefit it offers when choosing materials for essential uses. A relevant case study on 718-W7Ni3Fe bimetallic structures demonstrates the potential of additive manufacturing in creating complex bimetallic structures, although specific outcomes and mechanical properties were not detailed.
Additionally, Mica Tape Products play a crucial role in high-temperature resistance and electrical insulation, further complementing the applications of alloy 625 in demanding environments. Overall, the incorporation of this alloy in these industries underscores its vital role in advancing technology and ensuring reliability under extreme conditions.
Forging Techniques for Inconel 625: An Overview
Forging alloy 625 necessitates meticulous temperature and process control to ensure the desired mechanical properties are achieved. However, for uses requiring high-temperature resistance and electrical insulation, Mica Tape products are essential. Our Mica Insulation Tape, designed for high-temperature resistance, can be used alongside inconel 625 forgings in various critical applications, ensuring reliability and durability.
The mixture should be heated to around 2100°F (1150°C) for optimal workability, and techniques such as hot forging and upset forging are prevalent in the industry, allowing for effective shaping while minimizing the risk of defects. It is crucial to maintain uniform heating throughout the process and to avoid excessive deformation, as this can compromise the integrity of the material. Additionally, post-forging heat treatment may be required to enhance mechanical properties, relieve stresses, and facilitate improved performance.
As noted in studies, the mechanical behavior of this alloy at elevated temperatures illustrates the significance of precise temperature management during forging operations. The average rupture strength at 1600°F (871°C) for 1000 hours is 6.7 ksi (46 MPa), emphasizing the alloy’s durability under extreme conditions. Renato Baldan commented on the essential aspect of temperature control in his study of the mechanical properties of 625 alloy at high temperatures.
Recent advancements, such as induction heating techniques, have demonstrated potential in enhancing the heat treatment of cold-sprayed alloy 625, leading to better ductility and adhesion strength in comparison to traditional methods. This emphasizes the continuous advancement of forging methods and the significance of embracing modern best practices to attain superior outcomes with nickel compositions, while also taking into account the incorporation of Mica Tape products for improved performance in high-temperature applications.
Mechanical Properties of Inconel 625: Strength and Durability
Inconel 625 forgings are renowned for their remarkable mechanical properties, boasting a tensile strength of approximately 100 ksi (690 MPa) and a yield strength of around 75 ksi (515 MPa) at room temperature. Notably, the average dynamic modulus of elasticity for a plate measuring 3/8 in. thick and annealed at 1925°F is approximately 30.2 psi x 10^6 (MPa) at room temperature, decreasing to 18.7 psi x 10^6 (MPa) at 1290°F.
This metal demonstrates exceptional resistance to creep and fatigue, maintaining structural integrity even under high-stress conditions. Furthermore, a case study titled ‘Corrosion Resistance of Inconel 625 forgings’ highlights the exceptional resistance of these forgings to various corrosive environments, including:
– alkaline
– salt water
– fresh water
– neutral salts
– air
with minimal attack due to their nickel and chromium content. Engineers recognize that Inconel 625 forgings effectively prevent pitting and crevice corrosion, resist scaling and oxidation at high temperatures, and exhibit excellent resistance to chloride stress-corrosion cracking.
Its versatility is further underscored by its ability to withstand both oxidizing and reducing environments, making it an invaluable material across various sectors. As highlighted by Jing Shi, this alloy’s remarkable characteristics arise from its distinctive composition, which improves its performance in crucial uses. Furthermore, research published in ‘Materials & Design, Volume 186, 2020, Article 108359’ further supports these findings, establishing Inconel 625 forgings as a preferred option for applications demanding high performance under challenging conditions.
While mica tape products are not directly related, both materials share common applications in high-temperature environments, highlighting the importance of selecting the right insulation and structural materials for specific engineering challenges.
Challenges in Machining and Fabricating Inconel 625
Machining inconel 625 forgings presents a series of formidable challenges, primarily due to its remarkable strength and work-hardening characteristics. Standard cutting tools often experience accelerated wear rates, necessitating the adoption of specialized tooling, typically crafted from carbide or ceramic materials, to achieve effective results. The alloy’s propensity to work-harden requires operators to implement slower feed rates, ideally maintaining a cutting speed around 250 m/min and a feed rate of 0.15 mm/rev, to mitigate overheating and prolong tool life.
Furthermore, effective cooling strategies are critical; recent advancements in machining techniques, such as the application of nanofluids, have shown promise in enhancing cooling performance by reducing cutting zone temperatures and friction at the chip-tool interface. Experimental studies have demonstrated that nanofluids enhance lubricity and wettability, leading to better machining performance compared to conventional cutting fluids. For precision fabrication of alloy 625 components, advanced methodologies such as electrical discharge machining (EDM) or water jet cutting are often employed, ensuring the integrity of the material is maintained throughout the process.
As noted by Soumik Roy, ‘Most skin disorders are caused by mineral-based lubricants,’ highlighting the importance of selecting appropriate lubrication methods to address the unique challenges of machining Inconel 625 forgings. The intricacies of machining this alloy underscore the necessity for strategic planning and specialized equipment to overcome its inherent challenges.
Conclusion
Inconel 625 is a leading material for industries that demand exceptional performance under extreme conditions, thanks to its unique composition and exceptional mechanical properties. Its strength, corrosion resistance, and thermal stability make it indispensable in applications across aerospace, oil and gas, and marine sectors. The alloy’s ability to maintain integrity in harsh environments, combined with excellent weldability, positions it as a reliable choice for procurement managers.
The diverse applications of Inconel 625 highlight its strategic advantages. In aerospace, it is critical for components facing intense thermal and mechanical stress, while in the oil and gas industry, its corrosion resistance enhances safety and efficiency. Ongoing advancements in forging and machining techniques further optimize its use, ensuring it meets the demands of modern engineering.
However, the challenges associated with machining Inconel 625 must be acknowledged. Its work-hardening characteristics necessitate specialized tooling and effective cooling strategies. By understanding these complexities, procurement managers can successfully integrate Inconel 625 into high-performance applications.
In summary, Inconel 625 is not only a preferred material due to its remarkable properties but also a strategic asset in high-performance environments. Its adaptability and continued advancements in processing techniques solidify its role as a vital solution for industries striving for reliability and excellence under demanding conditions.