Blogs
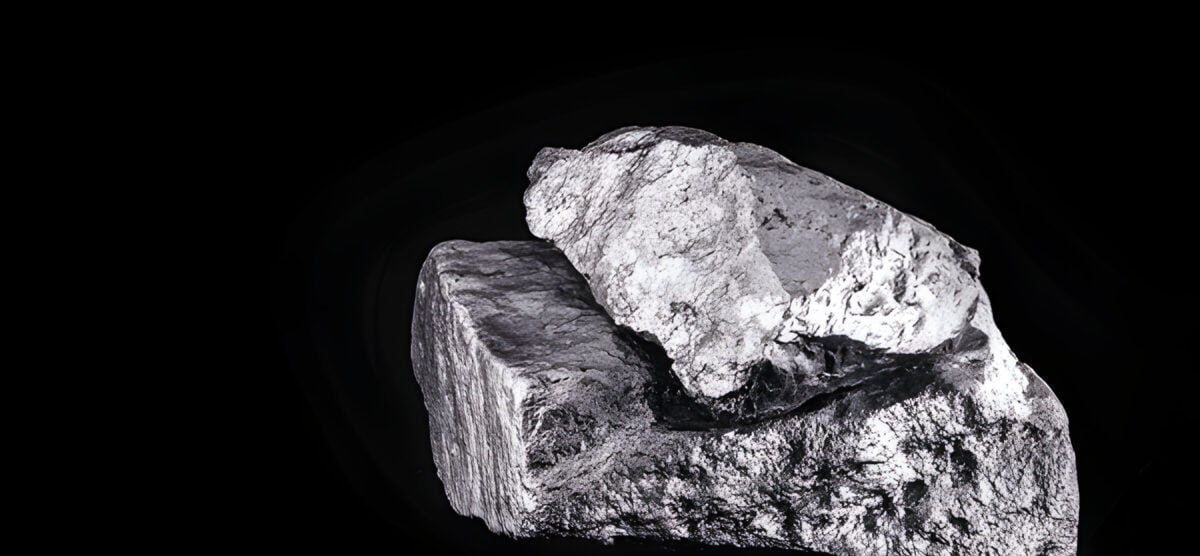
Exploring the Properties of Titanium: A Comprehensive Guide
Titanium is an extraordinary metal known for its high strength, lightweight nature, and superior resistance to corrosion. Thanks to these properties, it has become essential in industries like aerospace, medicine, and marine engineering.
In this guide, we’ll explore everything you need to know about titanium—from its chemical and physical characteristics to its thermal behavior and real-world applications. Whether you’re an engineer, a manufacturer, or just someone curious about advanced materials, this guide will help you understand why titanium is so valuable.
Understanding Titanium
What Is Titanium?
Titanium (symbol Ti, atomic number 22) is a lightweight, silver-grey metal that’s the ninth most abundant metal in the Earth’s crust. It’s commonly found in minerals like rutile and ilmenite.
What sets titanium apart is its incredible strength and natural resistance to corrosion—qualities that make it a top choice in high-performance applications.
Chemical Composition
Titanium’s chemical strength lies in its ability to form a protective oxide layer—titanium dioxide (TiO₂)—when it comes in contact with oxygen. This layer acts like armor, preventing further corrosion even in harsh conditions such as seawater or acidic environments.
Titanium alloys often include elements like aluminum, vanadium, and molybdenum to enhance its performance for specific industrial needs.
Key Physical Properties of Titanium
1. High Strength-to-Weight Ratio
Titanium is as strong as steel but about 40% lighter. This makes it a favorite in the aerospace industry, where reducing weight can improve fuel efficiency and performance.
2. Non-Magnetic and Low Conductivity
Titanium is non-magnetic and has low electrical and thermal conductivity, which makes it useful in specialized applications—especially in electronics and precision instruments.
Core Strengths of Titanium
Exceptional Strength and Durability
- Tensile Strength: Ranges between 30,000 psi to 200,000 psi
- Withstands extreme pressure, cyclic loads, and repeated stress
- Maintains structural integrity under challenging conditions
- Comparable strength to steel, at a fraction of the weight
Corrosion Resistance
Titanium is highly resistant to rust and corrosion, even in:
- Seawater
- Chloride-rich environments
- Acidic or chemical settings
Unlike many metals, titanium doesn’t suffer from pitting or crevice corrosion, making it ideal for long-term durability in hostile environments.
Lightweight Advantage
Titanium is about 60% lighter than steel, which:
- Improves efficiency in aircraft and automotive applications
- Reduces logistics and handling costs
- Enhances performance in sports gear and medical tools
Thermal Properties of Titanium
Heat Resistance
- Melting point: ~1,668°C
- Withstands extreme heat without losing strength
- Perfect for jet engines, automotive parts, and industrial furnaces
Low Thermal Expansion
Titanium doesn’t expand or contract much with temperature changes. This makes it great for:
- Precision components
- Electronics
- Aerospace assemblies, where dimensional accuracy is crucial
Where Titanium is Used
1. Aerospace and Aviation
Titanium is used in:
- Airframes
- Engines
- Landing gear
Its lightweight and strength help reduce fuel usage while maintaining durability. Corrosion resistance also extends the lifespan of aircraft parts.
2. Medical Implants and Devices
Titanium is biocompatible, meaning it’s accepted by the human body. It’s commonly used for:
- Hip and knee replacements
- Dental implants
- Surgical tools
- Cardiac devices
Bonus: Its non-magnetic nature makes it safe for MRI and other scans.
3. Marine and Chemical Industries
Because it withstands corrosion from seawater and chemicals, titanium is a go-to material for:
- Ship hulls
- Propellers
- Chemical reactors
- Desalination equipment
These applications benefit from titanium’s long life and low maintenance needs.
How Titanium Is Made
The Kroll Process
Titanium production is complex and energy-intensive. The main method, the Kroll Process, involves:
- Converting titanium ores into titanium tetrachloride (TiCl₄)
- Reducing TiCl₄ with magnesium to create titanium sponge
- Melting and forming into bars, sheets, and other products
Machinability and Handling
- Titanium doesn’t harden during machining like steel, which makes it easier to shape.
- However, it reacts easily with other materials during manufacturing, requiring special tools and controlled environments.
- Proper cooling and cutting techniques are essential for clean, high-quality finishes.
Conclusion
Titanium is a true modern marvel—strong, lightweight, corrosion-resistant, and biocompatible. These properties make it an essential material for industries ranging from aerospace and defense to healthcare and marine engineering.
As technology continues to evolve, titanium will remain a cornerstone material in the future of innovation and engineering.
FAQs
Q1. Does titanium rust?
No, titanium forms a protective oxide layer that prevents rusting.
Q2. Is titanium stronger than steel?
Yes, it has a higher strength-to-weight ratio than steel.
Q3. Can titanium be welded?
Yes, but it requires special techniques due to its reactivity.
Q4. What are the main uses of titanium?
Aerospace, medical implants, marine equipment, and chemical reactors.
Q5. Is titanium safe for the body?
Absolutely—it’s biocompatible and widely used in medical implants.
Q6. How is titanium produced?
Mainly through the Kroll Process, involving reduction of titanium tetrachloride with magnesium.
Q7. What is the melting point of titanium?
Around 1,668°C (3,034°F).
Q8. Can titanium handle high temperatures?
Yes, it remains stable and strong even at elevated temperatures.
🔗 Discover more on our website https://domadia.net/contact/