Blogs
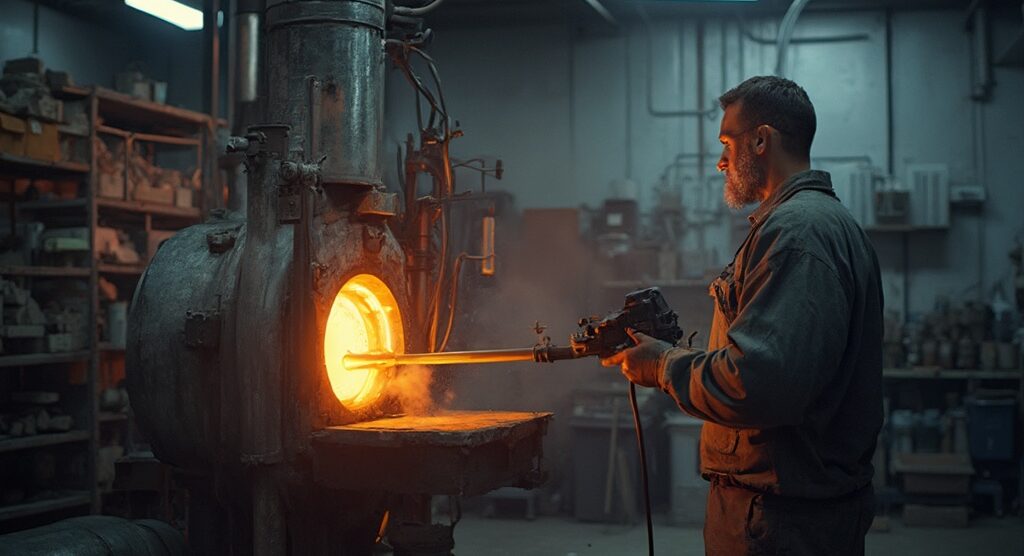
Solution Heat Treat vs. Anneal: A Comparative Analysis of Two Key Metal Treatments
Introduction
In the realm of metal processing, the choice between solution heat treatment and annealing is pivotal for achieving the desired mechanical properties and performance of materials. As industries continue to prioritize efficiency and sustainability, understanding the intricacies of these two heat treatment processes becomes essential for procurement managers.
Solution heat treatment excels in enhancing strength and hardness, making it indispensable for high-performance applications, particularly in sectors like aerospace and automotive.
Conversely, annealing plays a crucial role in softening metals and improving ductility, facilitating easier machining and forming.
This article delves into the comparative benefits, methodologies, and key considerations surrounding these processes, equipping professionals with the insights necessary to navigate the complexities of material selection and treatment. With advancements in technology and increasing environmental regulations, staying informed about the latest developments is not just advantageous—it is imperative for strategic decision-making in procurement and production.
Understanding Solution Heat Treatment and Annealing
Solution thermal processing is an essential procedure employed to improve the mechanical characteristics of heat-treatable substances and alloys. This process involves:
- Heating materials to a precise temperature,
- Maintaining that temperature to facilitate the dissolution of soluble phases, and
- Rapidly cooling the material to stabilize these changes.
Such techniques are vital in industries like automotive and aerospace, where the performance of high-strength materials is paramount.
Recent advancements in solution thermal processing have led to enhanced efficiency and consistency in producing materials that meet stringent industry standards. Significantly, electrically heated furnaces presently possess the largest market share in the thermal processing sector, highlighting their importance in contemporary manufacturing.
On the other hand, the process serves a unique role in working with alloys, mainly focused on:
- Softening the material,
- Alleviating internal stresses, and
- Improving ductility.
This process entails heating the metal to a specified temperature and allowing it to cool slowly, which promotes the rearrangement of its internal structure. The advantages of softening are especially significant in uses needing improved formability and decreased brittleness.
As sectors progress, it is essential to remain updated on the most recent advancements in these thermal processes, especially concerning operational efficiency and environmental sustainability. Electrically heated furnaces have emerged as a leading technology in the thermal treating market due to their operational efficiency and lower environmental impact compared to traditional fuel-fired systems. According to industry insights, these furnaces lead the industry due to their high operational efficiency and higher environmental sustainability than conventional fuel-fired systems.
With stringent environmental regulations on fuel-based furnaces, these advancements are essential for compliance and cost-effectiveness moving forward. Comprehending the nuances of solution heat treat vs anneal not only helps in identifying their respective benefits but also guides strategic choices in procurement and production. Furthermore, the competitive landscape of the thermal treating market reveals key players such as:
- Ajax TOCCO International Ltd,
- American Metal Treating Inc, and
- Bodycote plc,
who are contributing to market innovation and service delivery.
Comparative Benefits of Solution Heat Treatment vs. Annealing
Solution thermal processing is acknowledged for its capacity to substantially improve strength, hardness, and wear resistance, making it a favored option for high-performance applications. This process is particularly beneficial for aluminum alloys and specific types of steel, where achieving optimal mechanical properties is paramount. For example, in a comparative analysis, it was noted that aluminum alloys subjected to solution heat treatment demonstrated superior performance metrics, particularly in stress-intensive environments.
On the other hand, the heat treatment plays an essential part in enhancing ductility and machinability, particularly for substances that have experienced prior hardening processes. Bryan Litz’s findings demonstrate this, as he conducted a 10rd group with no heat treatment, one group subjected to heat on the 5th firing, and another group treated after each firing, highlighting the differing impacts of heat treatment on metal performance. However, it’s important to note that most people ‘under anneal,’ meaning they don’t actually anneal properly, leading to wasted time and energy.
By softening the material, heat treatment facilitates easier shaping and forming, making it indispensable in applications requiring extensive machining. The choice between solution heat treat vs anneal methods depends on the desired characteristics of the final product. While discussing solution heat treat vs anneal, it can be noted that solution thermal processing may be preferred for components experiencing high stress, whereas annealing may be more suitable for parts that will undergo significant machining or forming after processing.
The ongoing discussion in the reloading community, as mentioned in the case study titled ‘Anecdotal Evidence vs. Scientific Data,’ emphasizes the dependence on anecdotal assertions versus the need for empirical evidence to support or challenge the advantages of heat treatment, reinforcing the significance of informed decision-making in material processing.
The Processes Behind Solution Heat Treatment and Annealing
The process of solution heat treat vs anneal begins by heating the material to a temperature exceeding its solvus line, facilitating the dissolution of alloying elements. Following a predetermined soaking period at this elevated temperature, the material undergoes rapid cooling, typically achieved through quenching in water or oil. This swift cooling is pivotal for retaining a supersaturated solid solution, which is essential for optimal mechanical properties.
In contrast, the comparison of solution heat treat vs anneal involves a more gradual approach: the substance is heated to a specific temperature, held there for a designated duration, and subsequently cooled slowly, either in the furnace or air. This controlled cooling process is vital for enhancing softness and alleviating residual stresses within the metal structure. Meticulous management of temperature profiles and time parameters is essential in both thermal processes, particularly in the context of solution heat treat vs anneal, to attain the desired material characteristics.
Recent studies, including those published in ‘Materials 2022’, volume 15, issue 1, page 63, emphasize that the appropriate thermal conditions can ensure the stability of the austenite phase at room temperature, which is crucial for the performance of Ni-rich NiTi alloys. Anderson S. Paula notes, ‘The Influence of the Soaking Temperature Rotary Forging and Solution Heat Treatment on the Structural and Mechanical Behavior in Ni-Rich NiTi Alloy,’ highlighting the significance of these processes. Furthermore, optimization research indicates that higher temperatures, particularly at 900 °C and 950 °C with a soaking time of 120 minutes, can create a precipitate-free matrix favorable for achieving B2-austenite at room temperature.
This is backed by a case study named ‘Temperature Optimization for NiTi Alloys,’ which demonstrates the impacts of various heating levels and soaking durations on the microstructural and mechanical characteristics of the alloy. Understanding these intricacies is essential for procurement managers to make informed decisions regarding material processing and application.
Choosing Between Solution Heat Treatment and Annealing: Key Considerations
Choosing between solution heat treat vs anneal requires a systematic assessment of various essential factors. Foremost among these is the type of material being treated; for instance, hypereutectoid steels, which contain more than 0.8% carbon, may exhibit differing responses to these processes. Alloys that withstand high stress or wear are frequently more appropriate for solution thermal processing, which improves hardness and durability.
However, it is crucial to note that components hardened through heat processing may pose significant challenges for machining, particularly when the hardness exceeds HRC60. Conversely, if the application requires greater ductility or enhanced machinability, the choice between solution heat treat vs anneal becomes the preferred option. This method not only alleviates residual stresses but also facilitates the processing of thin-cutting machined products, resulting in enhanced accuracy and performance, as evidenced in recent case studies that demonstrate how timely annealing can significantly improve the final product’s outcomes.
Additionally, verifying core hardness through testing actual samples when using material selection design aids is essential, as it ensures that the selected method aligns with the material’s properties. Cost considerations, time constraints, and equipment availability further complicate the decision-making landscape. Consequently, procurement managers must carry out a comprehensive examination of material characteristics alongside operational needs to identify the most efficient thermal process.
As one materials scientist aptly mentioned,
Laser surface hardening is utilized to improve the mechanical properties and surface hardness of highly stressed machine components like gears, highlighting the strategic significance of customizing processing choices to particular material features.
Key Differences and Similarities Between Solution Heat Treatment and Annealing
Understanding the differences between solution heat treat vs anneal is essential for effective application in material processing, as both have different objectives and methods. Both techniques, namely solution heat treat vs anneal, involve the heating and subsequent cooling of metals to modify their properties, yet their objectives diverge notably. The main purpose of solution heat treat vs anneal is to improve strength and hardness through solution thermal processing, which typically uses rapid cooling to achieve specific microstructures.
For instance, a file hardening process can result in a hardness of approximately 58 HRC, showcasing the effectiveness of solution heat treatment in achieving desired mechanical properties. In contrast, the discussion of solution heat treat vs anneal highlights how heat treatment focuses on softening the metal and improving ductility, requiring a slow cooling process to relieve internal stresses. As noted by Bodycote Heat Treatment, one of the primary uses of heat treatment is reversing the effects of work hardening.
Additionally, recent discoveries show that differences in cooling rates greatly influence the mechanical properties obtained, highlighting the significance of choosing the suitable process for each application. The decline in the use of salt bath furnaces due to health and environmental concerns also reflects ongoing changes in industry practices, emphasizing the need for procurement managers to stay informed about these trends. Moreover, the case study on aging emphasizes the significance of precipitation hardening in alloys such as aluminum and maraging steels, further illustrating the practical uses of both solution heat processing and annealing.
Recognizing these key differences and similarities, particularly in solution heat treat vs anneal, is essential for procurement managers in navigating the complexities of metal treatment and ensuring the optimal choice for their specific operational needs.
Conclusion
Understanding the nuances between solution heat treatment and annealing is critical for ensuring the optimal performance of metals and alloys in various applications. Solution heat treatment is essential for enhancing the strength, hardness, and wear resistance of materials, particularly in high-performance sectors such as aerospace and automotive. In contrast, annealing serves to soften metals, relieve internal stresses, and improve ductility, making it indispensable for applications requiring extensive machining and forming.
The decision-making process surrounding these heat treatment methods hinges on several key factors, including the type of material and the intended application. While solution heat treatment is ideal for components that endure high stress, annealing is preferable for those requiring improved machinability and formability. Moreover, the latest advancements in heat treatment technologies, particularly the rise of electrically heated furnaces, highlight the importance of operational efficiency and environmental sustainability in modern metal processing.
Ultimately, procurement managers must leverage a thorough understanding of these processes to make informed choices that align with their operational requirements and industry standards. By carefully evaluating the specific needs of their materials and applications, professionals can optimize their metal processing strategies, ensuring both performance excellence and compliance with evolving environmental regulations. The intricate balance of strength, ductility, and efficiency achieved through the right heat treatment process will pave the way for successful manufacturing outcomes in a competitive landscape.