Blogs
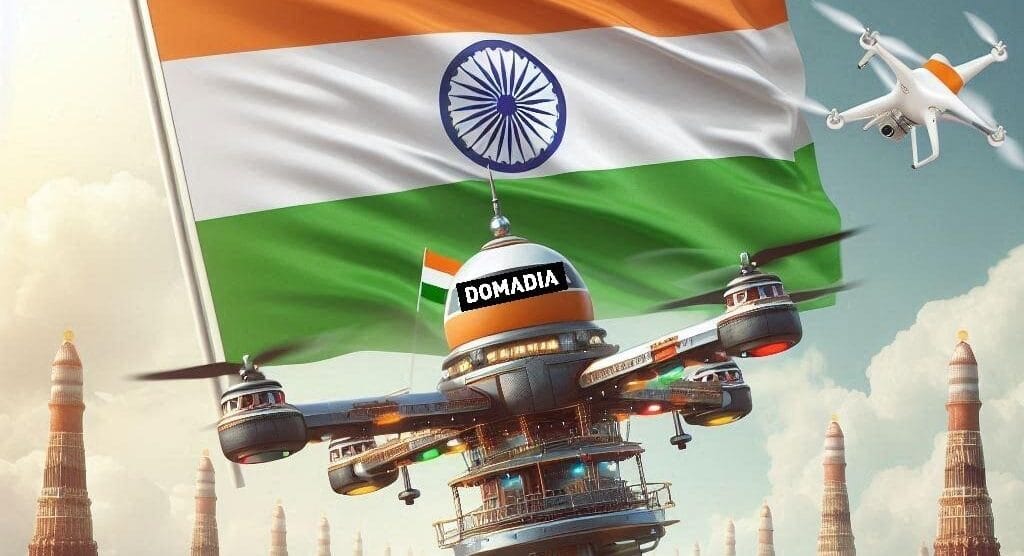
The Future of Lightweight Engineering | Innovations
In today’s fast-evolving world, lightweight engineering stands at the forefront of innovation, driving advancements across industries like automotive, aerospace, and consumer electronics. The future of lightweight engineering promises to reshape how products are designed and manufactured, emphasizing efficiency, performance, and sustainability. This approach uses advanced materials like magnesium alloys, carbon fiber-reinforced polymers, and high-strength steel to reduce weight without compromising strength or functionality, making it essential for modern technological progress.
As industries push towards greener and more efficient solutions, the adoption of lightweight engineering techniques is becoming crucial. By embracing cutting-edge materials and innovative design strategies, companies can achieve significant cost savings, reduced environmental impact, and improved product performance. This article explores the key materials, industry applications, and future outlook of lightweight engineering, highlighting why it’s a pivotal trend in the engineering landscape. Let’s delve deeper into the future of lightweight engineering and its transformative impact across various sectors.
The Rise of Lightweight Engineering
The Future of Lightweight Engineering revolves around the strategic use of advanced materials and innovative design methods to reduce the weight of structures while maintaining their strength and durability. Lightweight engineering is not just about making things lighter; it’s about enhancing overall efficiency, reducing environmental impact, and meeting stringent regulatory standards that drive industry growth.
Lightweight engineering utilizes materials like magnesium, carbon fiber, and advanced polymers, which offer exceptional strength-to-weight ratios compared to traditional metals. These materials are revolutionizing industries by allowing designers to push the boundaries of what’s possible—creating products that are not only lighter but also more energy-efficient and environmentally friendly. By reducing the weight of vehicles, aircraft, and machinery, lightweight engineering plays a critical role in cutting down fuel consumption and emissions, contributing to global sustainability goals.
Key Drivers of Lightweight Engineering:
- Efficiency Gains: Lighter components mean less energy consumption, which is crucial for industries like automotive and aerospace, where fuel efficiency and extended battery life are top priorities. For example, in electric vehicles (EVs), lighter body structures lead to improved range, making EVs more appealing to consumers.
- Sustainability: By reducing the amount of raw material used, lightweight engineering contributes to a smaller carbon footprint. The production processes for lightweight materials often consume less energy and produce fewer emissions compared to traditional materials like steel.
- Technological Advancements: New materials and manufacturing processes, such as additive manufacturing (3D printing), enable the creation of complex, lightweight components that were previously impossible to produce. This allows for greater design flexibility and the potential to integrate multiple functions into a single lightweight part.
Key Materials Shaping the Future of Lightweight Engineering
The success of lightweight engineering hinges on the development and application of high-performance materials that offer superior strength-to-weight ratios. These materials are crucial for industries striving to meet the ever-growing demands for efficiency and sustainability.
- Magnesium Alloys
- Properties: Magnesium is the lightest structural metal, significantly lighter than both steel and aluminum. It offers excellent strength and machinability, making it ideal for high-performance applications. Magnesium alloys are also highly recyclable, contributing to circular economy goals.
- Applications: Widely used in automotive (engine blocks, transmission cases), aerospace (aircraft fuselages, wings), and consumer electronics (laptop casings, smartphone frames). The use of magnesium in automotive applications can significantly reduce vehicle weight, leading to improved fuel economy and reduced emissions.
- Carbon Fiber-Reinforced Polymers (CFRP)
- Properties: Known for their exceptional strength-to-weight ratio and corrosion resistance, CFRPs are lighter yet stronger than traditional metals. These properties make CFRP a preferred choice for high-stress applications where weight reduction is critical.
- Applications: Predominantly used in aerospace for aircraft components, in automotive for high-end sports cars, and in renewable energy for wind turbine blades. For example, the use of carbon fiber in aircraft reduces overall weight, which translates to lower fuel consumption and increased range.
- Aluminum and High-Strength Steel Alloys
- Properties: Aluminum is lightweight, corrosion-resistant, and recyclable, making it an attractive option for industries focused on sustainability. High-strength steel offers enhanced durability and safety without the bulk of traditional steel.
- Applications: Utilized in automotive body structures, aerospace frames, and even in consumer products like bicycles and portable devices. The use of high-strength steel in automotive applications, for example, helps improve vehicle safety while maintaining a lighter structure.
Industry Applications of Lightweight Engineering
The future of lightweight engineering is being realized across various industries, each benefiting from enhanced performance, improved energy efficiency, and reduced environmental impact.
- Automotive Innovations
- Impact: Lightweight materials play a critical role in the shift towards electric and hybrid vehicles, directly improving range, efficiency, and overall vehicle dynamics. By using lightweight components, automakers can reduce the weight of battery packs, increase acceleration, and extend the life of electric vehicle batteries.
- Examples: Cars like the Tesla Model S and BMW i3 use aluminum and carbon fiber extensively to reduce weight, enhancing acceleration and battery life. The integration of lightweight materials helps these vehicles achieve higher performance standards while meeting stringent environmental regulations.
- Aerospace Advancements
- Impact: Aircraft manufacturers are replacing traditional metals with advanced composites to boost fuel efficiency, expand payload capacity, and meet stringent environmental regulations. Lightweight materials enable the production of aircraft that are lighter, stronger, and more fuel-efficient.
- Examples: Boeing’s 787 Dreamliner and Airbus A350 use a significant amount of composite materials, which reduce weight and improve fuel efficiency. These advancements are crucial as the aerospace industry seeks to minimize its environmental impact and meet global emission standards.
- Renewable Energy Sector
- Impact: Lightweight engineering is essential in the production of wind turbines and solar panels, making them more efficient and easier to install. The use of lightweight materials in renewable energy technologies enhances performance, reduces installation costs, and increases scalability.
- Examples: Longer, lighter wind turbine blades allow for greater energy capture, increased efficiency, and reduced operational costs. In solar power, lightweight panel structures simplify transportation and installation, making renewable energy more accessible.
- Consumer Electronics
- Impact: The trend toward thinner, lighter devices is driven by the use of advanced materials that offer durability without the bulk. Lightweight engineering helps manufacturers create compact, portable electronics that do not compromise on performance or strength.
- Examples: Smartphones, laptops, and tablets use magnesium alloys and carbon composites to reduce weight while enhancing structural integrity. This allows companies to produce sleek, user-friendly devices that are easy to carry and use.
Environmental Benefits of Lightweight Engineering
Lightweight engineering isn’t just about performance—it’s also about environmental responsibility. By reducing the weight of vehicles, aircraft, and other equipment, industries can lower fuel consumption and emissions, contributing to a greener planet.
Key Environmental Benefits:
- Lower Emissions: Lighter vehicles and planes consume less fuel, resulting in reduced greenhouse gas emissions. This is particularly important for the automotive and aerospace industries, where reducing carbon footprints is a key objective.
- Resource Efficiency: Lightweight materials often use fewer raw materials, promoting resource conservation. This not only reduces environmental impact but also helps industries cut costs and improve overall sustainability.
- Recyclability: Materials like aluminium and magnesium are highly recyclable, supporting circular economy practices and reducing waste.
Challenges and Future Outlook
While the benefits of lightweight engineering are clear, the field faces challenges, including the need to balance cost, safety, and scalability. The development of new materials and manufacturing methods requires significant investment, and transitioning to lightweight components can be complex.
Challenges in Lightweight Engineering:
- High Costs: Advanced materials like carbon fiber and magnesium alloys can be more expensive than traditional materials, posing a challenge for widespread adoption.
- Safety Considerations: Ensuring that lightweight components meet safety standards, especially in critical applications like automotive and aerospace, is essential.
- Scalability: Producing lightweight materials at scale requires advanced manufacturing technologies and infrastructure investments.
Future Outlook:
- Continued Innovation: Advances in material science, such as the development of new alloys and composites, will drive the next wave of lightweight engineering solutions. As research progresses, we can expect even lighter, stronger materials to emerge, pushing the boundaries of what is possible.
- Cross-Industry Collaboration: Partnerships between material scientists, engineers, and manufacturers will be crucial in overcoming current limitations and expanding applications. Collaborative efforts will help accelerate the adoption of lightweight engineering across various sectors.
Case Study: Magnesium Alloys by DOMADIA
DOMADIA plays a crucial role in advancing the future of lightweight engineering by providing premium magnesium alloys and other advanced materials. Known for their exceptional lightweight properties, DOMADIA’s materials are used extensively in the automotive and aerospace sectors to enhance performance while reducing environmental impact.
Benefits of DOMADIA’s Magnesium Alloys:
- Superior Performance: Lightweight and high-strength properties make them ideal for demanding applications, from car components to aerospace parts.
- Sustainability: Magnesium alloys contribute to reduced emissions and fuel consumption, aligning with global efforts to reduce environmental impact.
Call to Action: Partner with DOMADIA for Premium Lightweight Materials
Discover the unmatched benefits of DOMADIA’s magnesium alloys and other advanced materials. Contact us today to revolutionize your engineering projects with cutting-edge, lightweight solutions. VisitDOMADIA to learn more and see how our materials can transform your products for the better.
Frequently Asked Questions
Q1. What is lightweight engineering?
Lightweight engineering involves using advanced materials and design methods to reduce weight while maintaining strength and functionality.
Q2. Why is lightweight engineering important?
It enhances efficiency, reduces fuel consumption, and meets sustainability goals across industries like automotive and aerospace.
Q3. What are the main materials used in lightweight engineering?
Key materials include magnesium alloys, carbon fiber-reinforced polymers, aluminum, and high-strength steel.
Q4. How does lightweight engineering benefit the automotive industry?
It improves fuel efficiency, reduces emissions, and enhances vehicle performance, especially in electric and hybrid cars.
Q5. What role does lightweight engineering play in aerospace?
It allows for lighter aircraft with improved fuel efficiency, payload capacity, and reduced operational costs.
Q6. What are the environmental benefits of lightweight engineering?
It reduces emissions, promotes resource efficiency, and often involves recyclable materials, supporting a greener planet.
Q7. What challenges does lightweight engineering face?
Challenges include high material costs, safety considerations, and the need for advanced manufacturing technologies.
Q8. How is DOMADIA contributing to lightweight engineering?
DOMADIA supplies premium magnesium alloys that are widely used in industries like automotive and aerospace, offering superior lightweight solutions that drive performance and sustainability.