Blogs
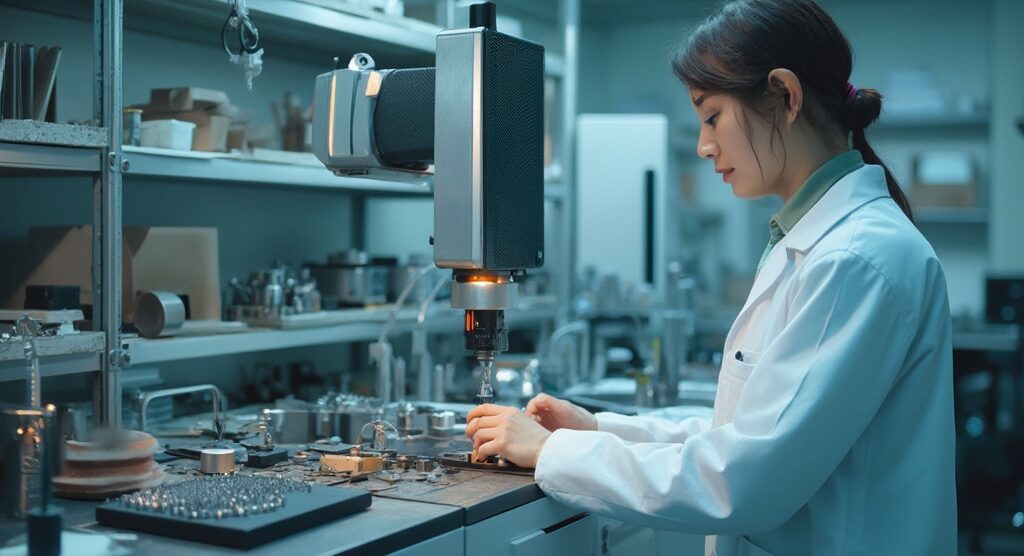
Understanding Beryllium Copper Tensile Strength for Spot and Resistance Welding: An In-Depth Tutorial
Introduction
In the realm of advanced materials, beryllium copper stands out as a high-performance alloy that seamlessly merges the remarkable electrical and thermal conductivity of copper with exceptional mechanical strength. As industries increasingly demand materials that can withstand rigorous applications, understanding the fundamental properties of beryllium copper becomes paramount.
This article delves into the alloy’s key characteristics, including:
- Impressive tensile strength
- Corrosion resistance
- Versatility in welding applications
By exploring the effects of heat treatment and comparing beryllium copper to other welding materials, procurement managers will gain valuable insights into optimizing material selection for their projects. With the beryllium copper market projected to grow significantly, the time to harness its benefits is now.
Fundamental Properties of Beryllium Copper
Beryllium bronze is renowned for its exceptional strength and versatility as a high-strength metal mixture, effectively combining the outstanding electrical and thermal conductivity of this element with superior mechanical attributes. Domadia, a leader in supplying and manufacturing high-performance Beryllium Copper Plates, is committed to fulfilling the requirements of various industrial uses with customized solutions that guarantee customer satisfaction. Its key characteristics include:
High Strength: When subjected to heat treatment, specifically solution annealing and precipitation heat treatment, Beryllium bronze can achieve remarkable tensile strengths of up to 200 ksi (1380 MPa), positioning it among the strongest metal mixtures in use today. These processes are vital as they improve the material’s hardness and microstructure, making it essential in challenging uses, especially aerospace and precision engineering.
Corrosion Resistance: The material demonstrates remarkable resistance to corrosion, a critical characteristic for welding tasks that frequently face severe environmental conditions. This capability guarantees durability and dependability in essential operations, strengthening Domadia’s dedication to quality.
Electrical Conductivity: Beryllium metal retains a high level of electrical conductivity, making it an ideal selection for uses that require efficient current flow. This trait is essential for components in magnetometers and different electrical devices, aiding in their functional efficiency.
Thermal Conductivity: Its excellent thermal conductivity promotes efficient heat dissipation during welding processes, greatly reducing the risk of overheating and improving operational safety.
As the beryllium bronze market is projected to demonstrate a CAGR of 6.1% by 2032, understanding these features is crucial for evaluating the beryllium copper tensile strength for spot welding & resistant welding electrodes in various applications. Recent advancements in its properties in 2024 further solidify its position in modern engineering solutions, particularly as industries recover from the impacts of the COVID-19 pandemic.
Tensile Strength of Beryllium Copper Alloys
Beryllium copper mixtures are known for their beryllium copper tensile strength for spot welding & resistant welding electrodes, which can vary significantly based on their composition and the heat treatment processes they undergo. Among the most notable grades are:
- C17200: Esteemed for its remarkable strength and excellent electrical conductivity, this grade can achieve a tensile strength of approximately 200 ksi (1380 MPa) following proper aging treatments.
- C17500: While it offers slightly lower conductivity than C17200, this grade is engineered for enhanced strength, making it particularly suitable for uses that demand superior mechanical performance.
- C17000: This grade strikes a balance between strength and conductivity, rendering it appropriate for a wide array of general-purpose uses.
At DOMADIA, we adhere to international standards—UNS and ASTM—ensuring that our Beryllium Copper products meet the highest compliance levels. Our extensive range includes foils, sheets, rods, and wires, all designed to cater to the diverse needs of our clients. With available stock and custom fabrication choices, we offer customized Beryllium Copper solutions that improve procurement efficiency.
The strategic use of heat treatment is crucial, as it allows manufacturers to adjust the beryllium copper tensile strength for spot welding & resistant welding electrodes, optimizing these alloys for specific welding purposes. This process not only improves the reliability and performance of components in challenging environments but also enables the customization of properties to meet specific usage requirements. For instance, the heat treatment process can significantly increase the beryllium copper tensile strength for spot welding & resistant welding electrodes of certain grades, making them ideal for high-stress applications. Moreover, tools made from Beryllium Copper are known for their non-sparking and corrosion-resistant properties, which are critical in explosive environments.
Their excellent thermal and electrical conductivity further highlights their importance in contexts requiring precision and reliability. According to materials expert Shivananda Prabhu, ‘The distinctive characteristics of specific metal mixtures render them essential in high-performance uses, particularly where both strength and conductivity are vital.’ Recent case studies have demonstrated that the tensile strength of beryllium bronze is essential in magnetometer uses, where precision and reliability are vital.
For example, one case study demonstrated that components made from C17200 grade Beryllium Copper outperformed competitors in terms of durability and conductivity in a high-stakes environment. As your trusted partner for Beryllium Copper solutions, DOMADIA is committed to delivering the quality and performance you need.
Applications of Beryllium Copper in Welding
Beryllium bronze is a versatile material celebrated for its remarkable characteristics, making it a preferred option in various welding uses. At Domadia, we are committed to providing high-quality, customized Beryllium Copper Plates, enhanced by our expert support to ensure your project’s success. Our customers have consistently praised our products, with one stating, ‘Domadia’s Beryllium Copper Plates exceeded our expectations in both quality and performance, making our projects more efficient.’
Its significant applications include:
Spot Welding: Beryllium alloy electrodes are pivotal for spot welding thin metal sheets, offering remarkable durability and resistance to weld spatter. This capability enhances the efficiency and quality of the welding process.
Resistance Welding: The material’s superior thermal and electrical conductivity is crucial for ensuring the beryllium copper tensile strength for spot welding & resistant welding electrodes, facilitating optimal energy transfer and minimizing heat loss. This efficiency not only enhances weld quality but also prolongs tool life.
Electrical Connectors: With excellent conductivity and mechanical strength, this alloy is ideal for producing reliable electrical connectors. These connectors can withstand considerable mechanical stress while preserving performance, essential for rigorous uses.
Automotive Components: The alloy’s resistance to corrosion and mechanical fatigue positions it advantageously for automotive purposes, such as battery contacts and connectors. Its robustness ensures longevity and reliability in automotive systems, contributing to overall vehicle performance.
Moreover, our inventory includes Beryllium Copper Non-Sparking Wrenches, designed with safety features that make them essential for hazardous environments. Recent research shows that the market share of a specific alloy in welding uses is increasing, reflecting its rising acceptance in sectors emphasizing high-performance and durable materials. As noted by Taiwo et al. (2010), comprehending the characteristics and uses of a certain alloy is crucial for procurement managers seeking to enhance material choice for welding and automotive parts.
Furthermore, our pricing is competitive, and we are happy to provide detailed quotes upon request. The overall yearly cost reductions of around $11.5 million at a 7 percent discount rate linked to the use of a specific alloy highlights its financial advantages. Additionally, the case study on ‘Medical Surveillance Cost Savings‘ highlights the financial implications of compliance with specific standards, reinforcing the importance of careful material selection in procurement decisions. These applications highlight the beryllium copper tensile strength for spot welding & resistant welding electrodes, which is why this alloy is increasingly regarded as a favored material in high-performance welding settings.
Heat Treatment Effects on Beryllium Copper Strength
Heat treatment is pivotal for optimizing the mechanical properties of beryllium copper, and several key processes are utilized to achieve these enhancements, reflecting Domadia’s commitment to providing high-quality solutions tailored to your project needs, including our extensive product range of foils, sheets, rods, and wires, along with custom fabrication options:
Aging: This critical process significantly increases the tensile strength and hardness of the alloy. Research indicates that effective aging temperatures typically range from 300°F to 600°F (150°C to 315°C), with the duration varying based on the target characteristics desired. Notably, a study highlighted that a beryllium copper mixture with a secondary aging process at 460 °C for 120 minutes exhibited remarkable properties, including a tensile strength of 747.28 MPa and a hardness of 245.9 HV. According to Wenweijiao Wang, ‘The results show that, after the secondary aging at 460 °C for 120 min, the material with 0.2 wt% Nb exhibits the best comprehensive properties.’
Solution Treatment: This involves elevating the metal to high temperatures followed by rapid cooling. This process preserves a stable solution of one metal within another, which is later aged to enhance the intended mechanical characteristics. The management of metastable precipitates such as γ″ and γ′ during this phase is essential for maintaining the integrity of friction stir welded joints in beryllium-based materials.
Stress Relief: This treatment is designed to alleviate residual stresses within the material, thus improving its performance during welding operations. Efficient stress alleviation is crucial for improving the dependability of alloys in real-world uses.
Furthermore, it is crucial to observe that at 450 °C, the C17200 alloy has a maximum stress of 270 MPa and a fatigue life of 0.64 × 10 cycles, which offers additional understanding of the material’s performance under various conditions. Recent findings highlight the substantial influence of these processes, rendering them essential factors in the procurement of materials for specialized uses. Furthermore, the case study titled ‘Effects of a Post-Weld Heat Treatment on the Mechanical Properties and Microstructure of a Friction-Stir-Welded Beryllium-Copper Alloy’ illustrates the practical relevance of heat treatment by investigating its impact on mechanical properties and microstructure, reaffirming Domadia’s role as your trusted partner in navigating these complexities while offering tailored solutions to meet your specific needs.
Comparative Analysis: Beryllium Copper vs. Other Welding Materials
When evaluating beryllium copper against other prevalent welding materials, several factors warrant consideration:
Copper Alloys: While traditional copper exhibits conductivity comparable to that of beryllium copper, it lacks the superior tensile strength required for demanding applications. This makes the alloy the preferred option in situations where durability is essential, particularly in settings where non-sparking tools are required to avoid ignition hazards.
Aluminum Alloys: Although aluminum alloys offer a lighter option, they generally show lower tensile strength and electrical conductivity compared to a specific alloy of copper. In high-stress applications, such deficiencies can significantly impact performance and reliability, particularly in explosive potential environments where non-sparking tools are essential.
Steel Alloys: While steel is often preferred for its cost-effectiveness, it does not provide the same electrical and thermal performance as beryllium-bronze. This disparity can be pivotal in certain welding processes where enhanced conductivity is essential for optimal results and safety.
Nickel Compositions: Although nickel compositions offer admirable resistance to corrosion, they typically lack in both conductivity and strength compared to certain copper-based materials. This limitation can hinder their effectiveness in applications where these properties are paramount, especially in marine environments where certain metal mixtures excel due to their corrosion resistance and antimicrobial characteristics.
Moreover, beryllium-free compositions perform approximately five to seven percent better than beryllium-based materials from a cycle time perspective. As Gildersleeve from NGK Metals states, “Whether you are using a beryllium-containing alloy or a non-beryllium-containing alloy, don’t use either as a license to lower your guard about health and hygiene.” This emphasizes the importance of safety considerations in material selection.
Dealing with an alloy dust presents considerable health risks, requiring rigorous safety measures that procurement managers must take into account when choosing materials for their uses.
Regarding pricing, it’s crucial to assess the expenses related to alloy strips compared to other materials to guarantee budget adherence while fulfilling safety and performance criteria.
This comprehensive comparison reinforces the distinct advantages of beryllium copper in specialized welding applications, equipping procurement managers with the insights needed to make informed and strategic material selections.
Conclusion
Beryllium copper emerges as a superior choice for industries demanding high-performance materials, thanks to its exceptional combination of strength, conductivity, and corrosion resistance. The analysis of its fundamental properties reveals the alloy’s impressive tensile strength, which can reach up to 200 ksi through effective heat treatment processes. This characteristic positions beryllium copper as a critical material in high-stress applications, particularly in aerospace and precision engineering.
Moreover, its remarkable corrosion resistance ensures longevity and reliability in harsh environments, while its excellent thermal and electrical conductivity makes it indispensable in various welding applications. As highlighted, the versatility of beryllium copper extends to its use in:
– Spot welding
– Resistance welding
– Automotive components
– Electrical connectors
showcasing its adaptability across multiple sectors.
As the beryllium copper market is projected to grow significantly, understanding its comparative advantages over other welding materials is crucial for procurement managers. The insights gained from this analysis underscore the importance of selecting materials that not only meet performance requirements but also align with safety and economic considerations. By leveraging the unique properties of beryllium copper, industries can enhance efficiency and reliability in their operations, making this alloy an invaluable asset in modern engineering solutions.
In conclusion, now is the opportune moment to harness the benefits of beryllium copper. Its proven performance, coupled with ongoing advancements in material properties, offers a strategic advantage for industries looking to optimize their material selection and achieve superior outcomes in their projects.