Blogs
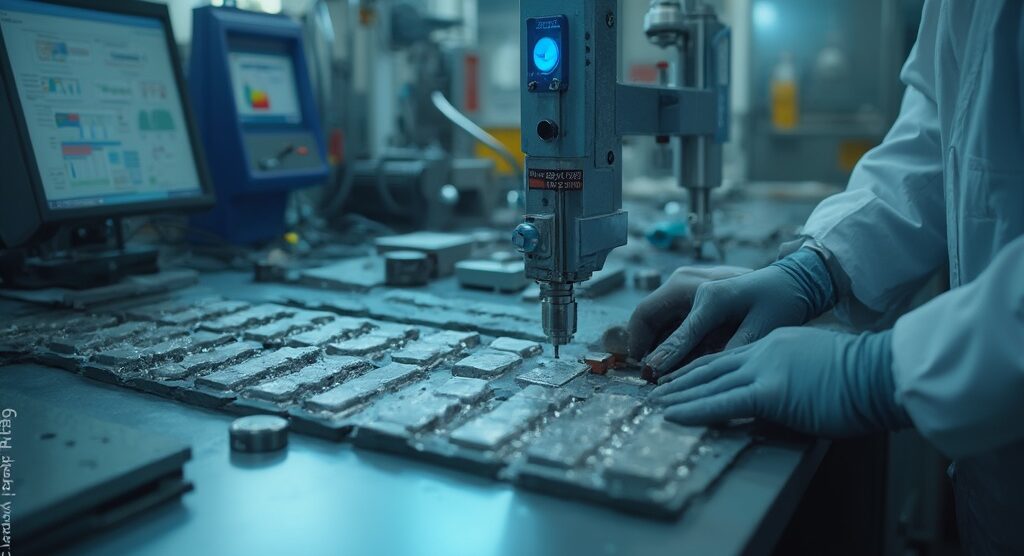
Understanding Inconel 718 Rockwell Hardness: A Complete Tutorial
Introduction
Inconel 718 stands at the forefront of high-performance alloys, renowned for its remarkable strength and unparalleled resistance to corrosion. This nickel-chromium alloy is meticulously engineered, boasting a composition that enhances its mechanical properties, making it a preferred choice for demanding applications across industries such as aerospace, automotive, and energy. The intricate balance of its elements, coupled with specialized heat treatment processes, not only elevates its yield strength but also ensures reliability in extreme environments.
As procurement managers navigate the complexities of material selection, understanding the nuances of Inconel 718’s properties—including its hardness and performance under stress—becomes imperative. This article delves into the composition, testing methods, and comparative advantages of Inconel 718, equipping decision-makers with the insights needed to optimize their material procurement strategies in an ever-evolving industrial landscape.
Introduction to Inconel 718: Composition and Properties
Alloy 718, a premium nickel-chromium material, is highly regarded for its exceptional strength and corrosion resistance, making it ideal for use in extreme environments. Its composition is meticulously balanced, comprising approximately:
- 50% nickel
- 19% chromium
- 3% molybdenum
- 0.9% titanium
alongside trace elements such as lanthanum, with contents in different blocks measuring:
- 0.0077%
- 0.0069%
- 0.0071%
These components, particularly the Nickel (Ni) and Molybdenum (Mo), play critical roles in enhancing its mechanical properties.
Significantly, the exceptional fatigue strength and oxidation resistance of 718 alloy are crucial characteristics for challenging uses. The ability to heat-treat this alloy significantly boosts its yield strength, firmly establishing it as a preferred material in aerospace components, gas turbines, and other high-stress settings. The precision manufacturing method used in creating 718 ensures that it meets the most rigorous standards, enhancing its dependability in essential uses.
Understanding these properties is crucial for evaluating the Inconel 718 rockwell hardness and determining its suitability for specific applications, particularly where reliability and performance are paramount. Recent observations highlight that while the substance approaches full recrystallization after heat treatment, a portion may not fully recrystallize, resulting in mechanical properties that exceed those of castings but fall short of forgings. Additionally, the differences in material behavior seem to become insignificant at higher temperatures (>600 °C), where the material appears to behave in a more homogenous manner.
Furthermore, comparisons of fatigue test results indicate that hot-rolled bars are stronger than 3D-printed alloy, likely due to work hardening during forging. Consequently, a comprehensive understanding of these dynamics is essential for procurement managers when evaluating this material for various projects, as it represents the essence of Clad Metal and Bimetal, demonstrating exceptional corrosion resistance and mechanical integrity in challenging industrial settings, especially in environments where exposure to harsh conditions is common.
Rockwell Hardness of Inconel 718: Measurement and Significance
Rockwell hardness testing is a crucial method for evaluating the hardness of different metals and alloys, with a specific type 718 being a prime example. This method evaluates hardness by measuring the depth of an indenter’s penetration under a significant load, contrasted with a preliminary lighter load. For Inconel 718 rockwell hardness, the values typically range from 30 to 44 HRC, reflecting its exceptional wear resistance, which is crucial for applications that demand high durability.
Recent studies indicate that variations in heat treatment processes can significantly influence these hardness values, underscoring the importance of tailored heat treatment to achieve desired properties. Moreover, the integration of Slow Speed Static and High Frequency Fatigue Testing – ElectroPuls can further validate the hardness testing results, ensuring reliability in performance assessments. Grasping Rockwell hardness not only serves a vital function in quality assurance but also guides procurement strategies, allowing managers to choose the most appropriate resources tailored to specific operational needs.
Furthermore, it is essential to consider other available resources, such as Chrome Molybdenum Steel – ASTM A387 Grade 22 Class 2, which is currently offered and available for quote, providing procurement managers with alternative options that may meet their needs. As advancements in hardness testing methods continue to evolve, staying updated on the latest techniques will further enhance decision-making processes in material procurement.
Heat Treatment Processes for Inconel 718
Alloy 718 is subjected to precise heat treatment processes designed to optimize its mechanical properties. Typically, the heat treatment begins with a solution annealing phase, conducted at temperatures of 1100 °C or 1250 °C (approximately 2012 °F to 2282 °F). This crucial step aims to dissolve any microsegregated precipitates and carbides, which enhances the alloy’s structural integrity.
Notably, at 1250 °C, while sub-grains and dislocation networks are effectively dissolved, some microsegregated precipitates and carbides may persist. Following this, the aging process occurs at temperatures between 1200 °F to 1325 °F (649 °C to 720 °C) over several hours. This stage facilitates the formation of gamma double prime precipitates, which are instrumental in significantly increasing the yield strength of alloy 718.
The research into these processes was financially supported by the National Center for Research and Development, underscoring the importance of these findings. For producers and purchasing supervisors, a comprehensive grasp of these heat treatment methods is crucial when detailing this alloy to ensure it meets the inconel 718 rockwell hardness required for high-performance uses that necessitate specific hardness and strength traits. Moreover, the case study titled ‘A Review of Mechanical Properties of Additively Manufactured Alloy 718’ offers a detailed summary of the mechanical properties linked to these heat treatment processes, further highlighting their significance in real-world uses.
Applications of Inconel 718 and Hardness Considerations
Alloy 718 is a preferred option in aerospace, automotive, and energy industries, valued for its remarkable strength and resistance to corrosion. This nickel-chromium alloy finds extensive use in critical applications, including components in gas turbines, rocket engines, and oil drilling equipment. The Inconel 718 Rockwell hardness is crucial in these situations, as it greatly affects wear resistance and the material’s ability to withstand high-stress conditions.
For instance, turbine blades crafted from Inconel 718 exhibit significant Inconel 718 Rockwell hardness, which is essential for the performance of high-efficiency engines, translating into improved longevity and reliability. As Amaya from Schlumberger aptly notes,
Despite meeting all the necessary standards and specifications, bolts can still have metallurgical defects that cause them to fail.
This highlights the necessity for procurement managers to consider application-specific hardness requirements critically.
Furthermore, Brahimi’s expectation of 100 percent acceptance for uni-axle type tests emphasizes the importance of stringent testing standards in ensuring integrity. Moreover, data sharing is vital for comprehending fastener failures and enhancing safety in subsea operations, highlighting the broader implications of performance. Incorporating insights from the case study titled ‘Realistic Testing Scenarios’ also emphasizes the significance of simulating realistic strain rates in testing, ensuring that the performance of the alloy is accurately predicted under actual service conditions.
Understanding these nuances allows for informed decision-making, particularly in selecting materials that meet not only performance criteria but also safety standards, especially in high-stakes environments.
Comparative Analysis with Other Alloys
When comparing the inconel 718 rockwell hardness of alloy 718 to other high-performance materials, such as Hastelloy X and Waspaloy, several differences in hardness and mechanical properties emerge. Alloy 718 typically displays greater inconel 718 rockwell hardness compared to Hastelloy X, particularly after heat treatment, which makes it more suitable for applications requiring enhanced wear resistance.
Furthermore, the use of mica tape products, such as Mica Insulation Tape and Insulating Mica Tapes, for high-temperature resistance and electrical insulation can significantly improve the performance of Inconel 718 in essential contexts.
- Mica Insulation Tape: recognized for its outstanding thermal stability, is especially advantageous in settings subjected to extreme temperatures.
- Insulating Mica Tapes: offer dependable electrical insulation in contexts involving electrical components.
While Waspaloy, despite being slightly lower in hardness, provides superior high-temperature performance, comprehending the characteristics of both the alloy and insulation substances enables procurement managers to choose the most suitable options based on specific application requirements and operational conditions.
Future Trends in Inconel 718 Usage and Hardness Research
As sectors keep advancing, the need for high-performance substances like alloy 718 is expected to rise considerably. For context, February 2007 had 4 entries related to Inconel 718, highlighting its growing relevance in the market. Ongoing research is dedicated to enhancing the alloy’s properties through cutting-edge manufacturing techniques, including additive manufacturing and innovative heat treatment processes.
These advancements not only enhance the substance’s mechanical characteristics but also broaden its usage scope across fields such as aerospace and energy. In parallel, innovations in hardness testing methods are emerging, providing procurement managers with more precise assessments of material properties. As procurement managers evaluate their choices, Mica Tape products arise as essential elements in guaranteeing high-temperature resistance and electrical insulation in crucial uses.
With their excellent flame resistance and dielectric strength, Mica Tapes are integral to the manufacture of fire-resistant cables and other electrical insulation systems. For instance, Mica Tape has been successfully utilized in high-voltage electrical uses, where its properties prevent electrical breakdown and enhance safety. As Antoine pointed out, challenges persist in understanding substance properties, emphasizing the need for clarity in testing methods.
Additionally, case studies suggest exploring new approaches, such as working with ensembles of data and developing non-perturbative tools, to control deterministic non-integrable dynamical systems. These advancements in testing are crucial for ensuring the reliability and performance of Inconel 718 rockwell hardness in challenging uses. It is essential for procurement managers to stay abreast of these trends, as they will directly impact future applications, specifications, and ultimately, the material choices that align with industry advancements.
Conclusion
Inconel 718 is a high-performance alloy that stands out for its exceptional strength and corrosion resistance, making it a vital material across various demanding industries. Its carefully balanced composition, which includes significant amounts of nickel and molybdenum, contributes to its superior mechanical properties. The rigorous heat treatment processes employed further enhance its yield strength, ensuring reliability in critical applications such as aerospace components, gas turbines, and oil drilling equipment.
Understanding the Rockwell hardness of Inconel 718 is essential for procurement managers, as it is directly linked to the alloy’s wear resistance and performance under stress. The variability in hardness due to different heat treatment methods highlights the importance of tailored approaches to meet specific operational requirements. Additionally, comparative analyses with other alloys illustrate Inconel 718’s competitive advantages, particularly in applications demanding high durability and performance.
Looking ahead, the ongoing research and development in manufacturing techniques and hardness testing methods promise to enhance the properties and application scope of Inconel 718. As industries evolve, staying informed about these advancements will empower procurement managers to make strategic decisions that align with both current demands and future trends. Ultimately, the insights gained from this exploration of Inconel 718 will facilitate informed material selection, ensuring optimal performance and reliability in challenging environments.