Blogs
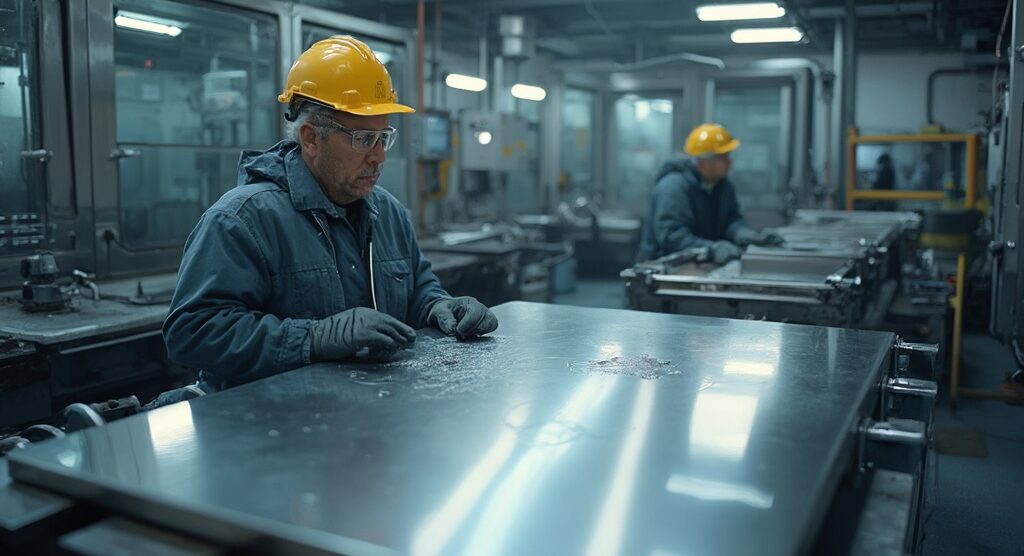
What Is Commercially Pure Titanium? A Comprehensive Overview
Introduction
The significance of commercially pure titanium (CP titanium) in modern manufacturing cannot be overstated. With its exceptional properties, including impressive corrosion resistance and a high strength-to-weight ratio, CP titanium has established itself as a preferred material across various industries.
From aerospace applications where weight reduction is critical to medical devices that demand biocompatibility, the versatility of CP titanium is remarkable. However, as the demand for this material grows, so do the complexities involved in its sourcing and procurement.
This article delves into the characteristics, applications, manufacturing processes, and future trends of commercially pure titanium, providing procurement managers with valuable insights and strategies to navigate the evolving landscape of this essential material.
Defining Commercially Pure Titanium: Characteristics and Importance
Commercially pure titanium is defined as a metal with a minimum content of 90%. It is renowned for its remarkable corrosion resistance, high strength-to-weight ratio, and biocompatibility, especially in the context of commercially pure titanium. CP metal, known as commercially pure titanium, is categorized into grades based on the levels of oxygen, iron, and other impurities, with Grade 1 recognized as the softest and most ductile, while Grade 4 stands as the strongest.
This distinction is crucial, particularly in demanding sectors like aerospace and medical devices, where commercially pure titanium is essential for ensuring reliability and performance are non-negotiable. For instance, Grade 4’s superior strength and corrosion fatigue resistance, similar to that of commercially pure titanium, make it competitive with steels and nickel alloys, exemplifying its suitability for applications where these attributes are critical. As highlighted by Boston Centerless, which boasts 65 years of precision grinding expertise, many alloys of this metal offer good machinability, allowing for efficient and cost-effective fabrication into complex shapes.
This characteristic highlights the strategic benefits of employing CP alloys in manufacturing processes for sectors that demand substances capable of enduring harsh conditions while preserving structural integrity. Moreover, the case study of commercially pure titanium Grade 4 illustrates its application in environments where strength and corrosion resistance are paramount. As we approach 2024, the significance of commercially pure titanium continues to grow, particularly in sectors that demand high-performance materials, solidifying its position as a cornerstone in advanced manufacturing and engineering applications.
Applications and Advantages of Commercially Pure Titanium in Industry
Commercially pure titanium is widely employed across various sectors due to its unique characteristics. In the aerospace sector, it is employed in airframes and engine components because of its lightweight and strong nature, which enhances fuel efficiency. In the medical field, CP metal is favored for surgical implants and prosthetics due to its biocompatibility, ensuring minimal adverse reactions within the human body.
Additionally, in the chemical processing industry, its corrosion resistance makes it suitable for piping and storage tanks that handle aggressive substances. The benefits of utilizing commercially pure titanium include:
- Lower maintenance expenses
- Prolonged product longevity
- Enhanced performance in harsh conditions
This makes it a valuable material option for numerous uses.
Manufacturing Processes for Commercially Pure Titanium
The production of commercially pure titanium involves several essential steps, including melting, forging, and machining. The most prevalent technique for generating metal is the Kroll method, which entails reducing titanium tetrachloride using magnesium. This method ensures high purity levels and allows for the production of various grades of commercially pure titanium.
Following the melting procedure, titanium is often subjected to forging and machining to create specific shapes and forms required for various applications. In these activities, the use of Non-Sparking Tools is crucial to prevent ignition risks, particularly during melting and forging, where sparks can pose a significant hazard in explosive environments. Quality control is paramount throughout these processes to ensure that the final product meets the necessary specifications and standards required in industries such as aerospace and medical devices.
Additionally, suppliers and manufacturers of electrical insulation and high-temperature materials, such as electrical insulation papers and PTFE coated fabrics, play a vital role in providing the necessary tools and components that support safety and efficiency in these critical applications.
Challenges in Sourcing and Procuring Commercially Pure Titanium
Sourcing commercially pure titanium presents several challenges, including:
- Fluctuating market prices
- Supply chain disruptions
- Compliance with international standards
The titanium market can be volatile, influenced by global demand and geopolitical factors. Additionally, ensuring compliance with industry standards and regulations can complicate procurement processes.
To address these challenges, procurement managers should:
- Build strong relationships with dependable suppliers
- Include those specializing in high-temperature products such as Mica Tape, which provide excellent flame resistance and dielectric strength, crucial for applications requiring electrical insulation and high-temperature durability
- Consider Mica Sheet Tape, with its high mechanical strength, which is particularly suited for demanding environments in industries like aerospace and automotive
By applying strategic sourcing methods and keeping updated on market trends, procurement managers can optimize expenses while ensuring the quality and availability of commercially pure titanium and related products like Mica Tape.
Future Trends in the Use of Commercially Pure Titanium
The forecast for commercially unalloyed metal is exceptionally encouraging, propelled by continuous technological progress and a rising demand for lightweight, high-strength substances across various sectors. In particular, the aerospace, automotive, and medical technology industries are poised for significant growth, with innovative applications emerging consistently. The role of additive manufacturing (AM) and 3D printing is pivotal in this evolution, enabling the production of more complex geometries while minimizing material waste.
Significantly, commercially unalloyed metal shows a consistent ductility of 12%, which boosts its attractiveness in these applications. As industries shift their focus towards sustainability and enhanced performance, the role of commercially pure titanium is set to be crucial in future developments. Recent studies suggest that AM techniques, such as binder jetting and directed energy deposition, lead to lower energy usage and greenhouse gas emissions, highlighting the substance’s viability in sustainable manufacturing.
Specifically, a case study titled ‘Impact of Additive Manufacturing on Titanium Supply Chain‘ assesses how AM processes compare with conventional manufacturing methods, revealing that most AM processes can reduce energy consumption and GHG emissions, except for laser-based powder bed fusion (L-PBF). The strategic alignment of commercially pure titanium with industry demands and environmental considerations positions commercially pure titanium as a key material for the future.
Conclusion
The exploration of commercially pure titanium (CP titanium) highlights its essential role in modern manufacturing, driven by its unmatched properties such as:
- Corrosion resistance
- Strength-to-weight ratio
- Biocompatibility
These attributes make CP titanium indispensable across various sectors, including aerospace and medical applications, where performance and reliability are critical. The understanding of different grades, particularly the advantages of Grade 4, further emphasizes its suitability for high-stress environments, showcasing its ability to compete with traditional materials like steels and nickel alloys.
Manufacturing processes for CP titanium, particularly the Kroll process, ensure high purity and adaptability while maintaining stringent quality control. However, the challenges in sourcing this material, such as market volatility and compliance with international standards, require procurement managers to adopt strategic sourcing practices. Building strong relationships with reliable suppliers and staying informed about industry trends can facilitate effective procurement strategies.
Looking ahead, the future of CP titanium appears bright, particularly with the growing demand in aerospace, automotive, and medical sectors. The integration of additive manufacturing technologies promises to enhance efficiency and sustainability, aligning with the industry’s shift towards innovative and environmentally friendly practices. As advancements continue, CP titanium is poised to maintain its status as a cornerstone material in advanced manufacturing, providing procurement managers with significant opportunities to leverage its benefits in their operations.