Blogs
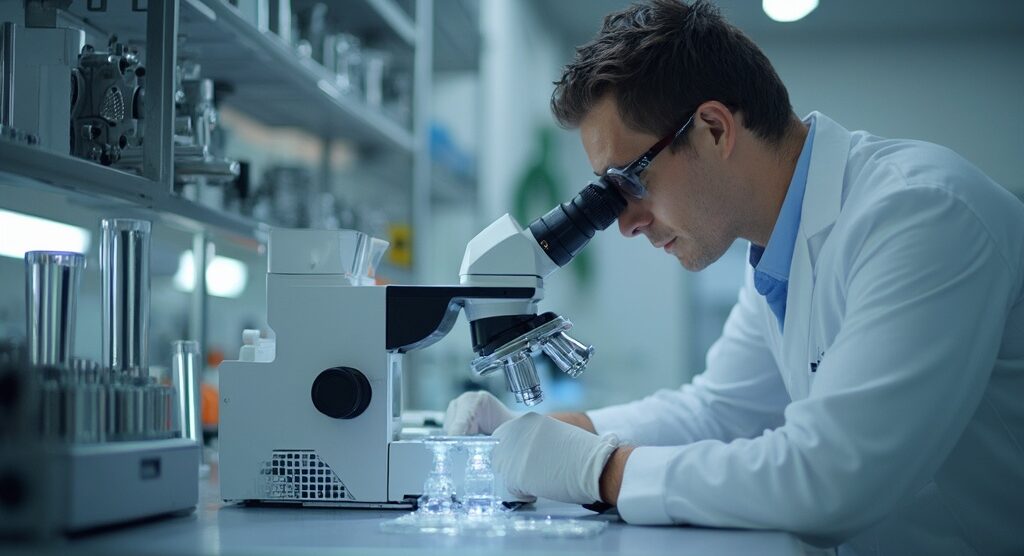
Understanding the Characteristics of Titanium: A Complete Tutorial
Introduction
In the realm of advanced materials, titanium stands out as a paragon of strength and versatility, captivating industries from aerospace to medical applications. Its remarkable strength-to-weight ratio and exceptional corrosion resistance make it a preferred choice for engineers and procurement managers alike, who seek to optimize performance without sacrificing reliability. As organizations navigate the complexities of material selection, understanding the unique properties of titanium and its alloys becomes paramount.
This article delves into the multifaceted world of titanium, exploring its properties, comparative advantages over other metals, and best practices for sourcing, empowering professionals to make informed decisions that enhance operational efficiency and drive innovation.
Exploring the Versatility of Titanium: Properties and Applications
Titanium is renowned for its exceptional strength-to-weight ratio, making it an ideal choice in industries where reducing weight without compromising strength is critical, such as aerospace and automotive. Additionally, this metal exhibits excellent corrosion resistance, ensuring longevity in harsh environments, which is essential for marine and chemical processing applications. Its biocompatibility renders this metal a favored choice in the medical domain for implants and prosthetics. Applications range from aircraft components and automotive parts to medical devices and chemical processing equipment, showcasing this metal’s versatility across multiple sectors.
Comprehending the properties of this metal is vital for guaranteeing its appropriateness for diverse uses. Key properties include:
- Density
- Moisture absorption
- Tensile strength
- Tear strength
- Electrical characteristics
All of which are defined according to ASTM standards. For instance, the ASTM standards provide critical benchmarks for assessing the substance’s performance in different environments.
In addition to titanium, the use of non-sparking tools is paramount in explosive environments, where safety is a primary concern. These tools prevent sparks that could ignite combustible substances, making them essential for industries such as oil and gas. Furthermore, DOMADIA Oxygen Free Copper (OFE/OHFC) plays a vital role in critical medical components, ensuring high conductivity and reliability in sensitive uses. This emphasizes the significance of material selection in specialized contexts, where the characteristics of each material must correspond with the specific requirements of their use.
Comparative Analysis: Titanium vs. Other Metals
Titanium is distinguished by its exceptional strength-to-weight ratio, significantly exceeding that of both aluminum and steel. This feature is especially advantageous in scenarios where weight reduction is critical, such as in the aerospace and automotive industries. Our metal sputtering targets, which include high conductivity options like Aluminum, Copper, Gold, Silver, and Titanium, are designed for durability and performance that meet the demands of these sectors. Despite its increased expense, the distinctive blend of strength and corrosion resistance provides significant benefits in different settings, making it a superb option for metal sputtering uses.
Recent studies comparing a certain metal, aluminum, and steel 2024 reveal that while this particular metal may be more expensive, its durability and performance often justify the investment. In aerospace uses, for instance, the metal’s superior strength-to-weight ratio improves fuel efficiency and overall aircraft performance. Similarly, in the automotive sector, lightweight components contribute to reduced vehicle weight, leading to improved fuel economy without compromising safety.
To address specific material properties, we offer custom alloy sputtering targets, including:
– Aluminum-Copper
– Nickel-Chromium
– Titanium-Aluminum
providing tailored solutions for various uses. Additionally, innovative wear-resistant steels developed by Industeel France, such as ENDURA and ENDURA Dual, showcase the advantages of the metal’s properties. These steels utilize a unique ‘trip effect’ to enhance durability, making them ideal for high-performance and reliability applications.
Procurement managers must carefully navigate the cost-performance dynamics associated with this material. Although the initial investment may be higher, the long-term benefits, including reduced maintenance and extended lifecycle, can outweigh the costs. A strategic sourcing approach that incorporates titanium, alongside advanced materials like ENDURA and ENDURA Dual steels, can yield significant advantages in industries where performance and reliability are paramount.
Understanding Titanium Alloys: Types and Benefits
Titanium mixtures are systematically classified into three main categories: alpha types, beta types, and alpha-beta types, each providing unique benefits suited to particular industrial uses. As a leading metal supplier specializing in Copper, Nickel, Titanium, and Rare Earth materials since 1952, Domadia offers premium metal solutions that improve industrial operations and satisfy various requirements.
Alpha materials, such as Ti-6Al-4V, are highly valued for their exceptional weldability and strength, characteristics that render them especially fitting for aerospace uses, where reliability and performance are crucial. These materials maintain their mechanical properties at both low and high temperatures, making them versatile and robust under varied operating conditions.
In contrast, beta materials are celebrated for their excellent formability and high strength. Their ability to be easily shaped and processed makes them an ideal choice for automotive components, where complex geometries and durability are crucial. Remarkably, the resource savings with beta metals are substantial, attaining about 60% efficiency in comparison to conventional production methods, which generally show a buy-to-fly ratio that can go as high as 20:1. This efficiency is particularly relevant in contexts where cost and material usage must be optimized for competitive advantage.
Alpha-beta mixtures provide a synergistic combination of the characteristics found in both alpha and beta materials. They provide high strength, fracture toughness, and good weldability, making them suitable for demanding environments such as the oil and gas industry. Their balanced characteristics enable these alloys to withstand extreme conditions while maintaining structural integrity.
Moreover, the use of this metal for long-term nuclear waste storage exemplifies its protective capabilities. Titanium containers have been studied for their potential to last over 100,000 years under proper conditions, ensuring safe and effective long-term containment solutions in sensitive applications. A titanium ‘drip shield’ can also be placed over other types of containers to enhance containment further.
Simon Ford, an authoritative figure in the field, emphasizes the strategic importance of selecting suitable resources:
‘The shift from a centralized system of manufacturing to a more decentralized one implies that the environmental impact of transportation will be reduced while at the same time supporting and empowering local communities.’ This perspective highlights the broader implications of material selection, underscoring not just performance but also sustainability.
By understanding the distinct characteristics and uses of alpha, beta, and alpha-beta metal mixtures, procurement managers can make informed choices that align with their performance needs and cost factors, ultimately driving efficiency and innovation within their operations. Domadia’s dedication to quality guarantees that you have access to the best alloys for your projects.
Sourcing Titanium: Best Practices for Procurement Managers
When sourcing this metal, it is essential to prioritize suppliers who adhere to international standards such as ASTM and ISO, as well as other relevant specifications like AMS and MIL. Adhering to these standards guarantees that resources meet stringent quality and safety requirements, which is crucial for maintaining high production standards. Establishing long-term relationships with reliable suppliers can lead to better pricing and enhanced reliability, providing a solid foundation for sustained success.
Based on recent sector data, firms that obtain resources from approved vendors report up to a 30% decrease in defects and a 20% rise in overall production efficiency. To maintain a competitive edge, regular evaluation of supplier performance is essential; monitoring key metrics such as delivery times, material quality, and pricing is vital. It’s important to look beyond the initial purchase price and consider the total cost of ownership, which encompasses machining costs, lifecycle performance, and potential downtime. For instance, a case study conducted by an aerospace manufacturer revealed that over a five-year period, investing in higher-quality metal from compliant suppliers resulted in a 15% decrease in overall manufacturing costs due to reduced rework and failure rates.
As Todd Ecless emphasizes, ‘Clearly stating your production goals and then quantifying them provides a baseline to evaluate the contribution a water jet cutting system can make in your application.’ Applying this principle to sourcing materials, clear and quantifiable goals enable better assessment of supplier performance and system contributions.
To foster strong supplier relationships, engaging in transparent and mutually beneficial negotiation tactics is vital. Transparency builds trust, while collaboration ensures that both parties work towards common goals, ultimately improving procurement outcomes. By emphasizing these best practices, procurement managers can secure high-quality titanium materials and sustain productive supplier partnerships.
Conclusion
Titanium’s remarkable properties and versatility make it an invaluable asset across various industries, from aerospace to medical applications. Its exceptional strength-to-weight ratio and resistance to corrosion are key factors that enhance performance while ensuring reliability. Understanding the different types of titanium alloys—alpha, beta, and alpha-beta—enables procurement managers to make strategic decisions that align with specific operational needs, maximizing efficiency and innovation.
The comparative analysis of titanium against other metals highlights its long-term value despite higher upfront costs. The durability and performance characteristics of titanium often justify the investment, particularly in applications where weight reduction is critical for efficiency. Furthermore, sourcing titanium from compliant suppliers who adhere to international standards not only mitigates risks associated with material defects but also fosters lasting partnerships that can lead to improved pricing and reliability.
In conclusion, the strategic selection and sourcing of titanium and its alloys should be a priority for professionals seeking to enhance operational efficiency and drive innovation. By leveraging the unique properties of titanium and establishing robust supplier relationships, organizations can achieve significant competitive advantages while ensuring high performance and reliability in their applications. Embracing these best practices will empower procurement managers to navigate the complexities of material selection with confidence, ultimately leading to successful outcomes in their projects.