Blogs
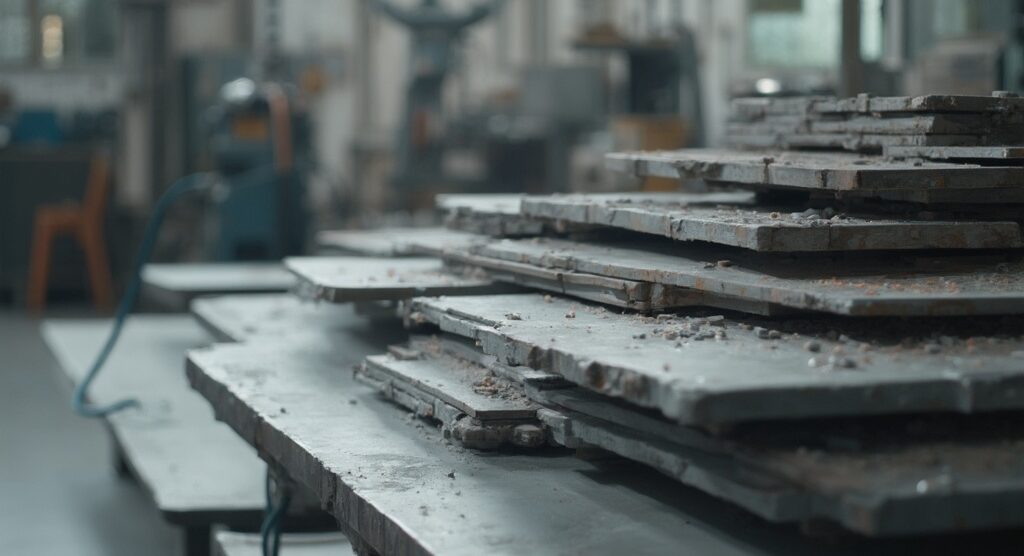
Understanding the Cost of Invar: A Complete Tutorial on Pricing and Applications
Introduction
Invar, a unique alloy primarily composed of iron and nickel, has garnered significant attention in precision engineering due to its exceptionally low coefficient of thermal expansion. This remarkable property allows components made from Invar to maintain their dimensional stability across a range of temperatures, making it invaluable in high-stakes industries such as aerospace and electronics.
As procurement managers navigate the complexities of material selection, an in-depth understanding of Invar’s composition, properties, and applications becomes essential. From its critical role in satellite instruments to its use in high-quality electronic components, Invar’s advantages extend far beyond mere functionality, offering durability and reliability that directly impact performance and safety.
This article delves into the intricacies of Invar, exploring its pricing dynamics, diverse applications, and the strategic benefits it offers across various sectors, equipping professionals with the insights needed to make informed procurement decisions.
Introduction to Invar: Composition and Properties
The alloy, primarily composed of iron and nickel, is distinguished by its remarkably low coefficient of thermal expansion (CTE), making it particularly valuable in precision engineering. The alloy referred to as 36 consists of approximately 36% nickel and 64% iron, a composition that contributes to its exceptional dimensional stability across varying temperatures. This stability is paramount for applications such as precision instruments and aerospace components, where even minute changes in dimensions can lead to significant deviations in functionality.
Significantly, the exposure duration for measurements associated with the alloy’s heat properties was established above 15 seconds, ensuring precise evaluations of its performance. Michael Wack, an expert in substance science, emphasizes that the Curie temperature of a substance defines the temperature at which a ferromagnetic entity loses the capacity to carry remanent magnetization and behaves like a paramagnetic substance. This insight emphasizes the importance of understanding the heat-related characteristics of specific materials in engineering applications, especially considering recent studies that have confirmed the significance of low heat expansion in substances.
Additionally, a case study named ‘Magnetic Domain Influence on Heat Expansion’ illustrates how heat treatment impacts Invar’s characteristics, uncovering a connection between magnetic properties and heat expansion coefficients. Results from this research showed that the bending degree of magnetic domains and domain wall energy density changed with heat treatment, affecting the magnetostriction and, in turn, the expansion coefficient. As such, a thorough understanding of the material’s composition, properties, and thermal expansion characteristics is crucial for procurement managers evaluating its suitability for specialized applications.
Understanding Invar Pricing: Factors and Calculations
The pricing of the alloy, including the cost of invar, is influenced by a range of essential factors, particularly the expenses related to raw materials, production methods, market demand, and supply chain dynamics. A pivotal element in this equation is nickel, whose significant presence in the alloy directly affects pricing. As industry expert John Doe states, ‘The volatility of nickel prices can dramatically impact the overall cost of invar, making it essential for procurement managers to stay informed.’
Recent market analysis suggests that the cost of invar in 2024 is expected to be approximately $XX per pound, reflecting ongoing fluctuations in raw resources costs. Moreover, pricing details for related materials, such as Tungsten Copper W80Cu20, are similarly influenced by market conditions, with prices around $1,890. The method of production—whether casting, rolling, or fabrication—also affects the cost of invar.
For instance, a recent case study highlighted how a major manufacturer adjusted its pricing strategy in response to a 20% increase in nickel costs, demonstrating the importance of real-time market analysis.
Procurement experts should also take into account the benefits of copper nickel alloys compared to stainless steel, especially their enhanced corrosion resistance and durability in marine settings, which render them a favored option for uses such as ship hulls and offshore platforms. Additionally, copper nickel alloys are widely utilized in automotive systems for brake lines and hydraulic systems due to their excellent performance. They also discover uses in electronics, heat exchangers, and coinage.
A thorough understanding of these variables is essential when assessing supplier quotes and negotiating contracts. By conducting regular market analysis, managers can better anticipate price fluctuations and adjust purchasing strategies accordingly, ensuring they remain competitive in a volatile market landscape.
Applications of Invar: Where and Why It Is Used
This alloy’s unique properties render it indispensable across various applications, particularly in the aerospace and electronics sectors. Supported by the Korea Institute of Industrial Technology under project PJA20073, this alloy is integral to components in the aerospace industry that demand exceptional dimensional stability and precision under fluctuating temperatures, such as satellite instruments and advanced guidance systems. Aerospace engineers have observed that the substance’s low thermal expansion is essential for preserving accuracy in critical measurements, which can greatly influence performance.
One notable case study, titled ‘Cross-Shaped Structure of Invar Alloy Using Cold Wire Laser Fillet Welding,’ investigates the feasibility of welding this alloy and provides insights into its weldability and potential in creating intricate structures. This lays the groundwork for innovative applications in aerospace engineering.
In the electronics manufacturing realm, this alloy is widely employed for producing high-quality transformers and coils, where its stability and electromagnetic properties enhance efficiency and reliability. Adam Hecht, an industry expert, emphasizes the product’s superior attributes, stating,
Some of the technologies can get such small, fine details. You just can’t machine parts that small.
You can’t mold parts that small.
This emphasizes the necessity of the material in crafting intricate electronic components that require precision and durability. As procurement managers evaluate material choices for their projects, understanding the cost of invar and its demonstrated effectiveness becomes crucial to fulfill specific needs efficiently.
For further details, the original article can be accessed via the DOI link: https://doi.org/10.3390/cryst14121097.
Advantages of Invar: Benefits for Various Industries
The alloy stands out because of its exceptional heat stability and minimal expansion, making it an essential option for precision-critical applications. Its high dimensional accuracy ensures that components retain their integrity under varying temperature conditions, thereby minimizing the risk of deformation. For instance, recent testing of K-TIG welded joints revealed a microhardness of 441.0 HV, showcasing the strong mechanical properties of the material that are critical in demanding environments.
This inherent resistance to thermal fluctuations not only reduces the cost of invar but also significantly enhances the longevity of components, leading to substantial savings over time. In the aerospace and electronics sectors, the reliability provided by this material translates directly into enhanced product performance and safety, characteristics that are essential for engineers and designers. As mentioned by a specialist from AAT, ‘The groundbreaking structure of substances prevents problems that could jeopardize safety and efficiency in critical scenarios.’
For procurement managers, grasping these advantages is vital when evaluating options, as they can impact both operational efficiency and cost-effectiveness in manufacturing processes. Moreover, the integration of high-temperature resistant materials such as Mica Tape, which provides outstanding flame resistance and dielectric strength, can further improve electrical insulation performance in contexts where this material is used. Mica Tape’s mechanical strength and capacity to endure extreme conditions make it an ideal addition to this material in high-precision uses.
Moreover, case studies on tensile testing of welded joints indicate that even with minor changes in heat inputs, the alloy maintains excellent mechanical properties, reinforcing its value in high-precision uses. The latest advancements highlight the importance of this material in these sectors, establishing it as a favored choice for high-precision uses.
Types of Invar Products: Sheets, Plates, and More
The alloy is available in different shapes, such as sheets, plates, rods, and custom-made parts, each tailored to fulfill particular requirements. Especially, alloy sheets and plates are crucial in manufacturing processes where dimensional stability is paramount, ensuring that products maintain their shape and integrity under varying conditions. As mentioned by Lee H.-K. in a study on the weldability of a specific alloy, understanding the properties of the substance is crucial for maximizing its applications in various industries.
On the other hand, rods are frequently employed in precision instruments and mechanical assemblies, where exact measurements are critical for performance. The ability to produce custom-fabricated components is particularly valuable, enabling tailored solutions that satisfy unique project specifications. Additionally, considering the energy storage densities—iron at 16 kWh per liter and aluminum at 24.5 kWh per liter—can provide procurement managers with a comparative context for evaluating substances based on performance requirements.
Recognizing the diverse types of such products available is essential for procurement managers aiming to source materials that align effectively with project requirements, thereby enhancing operational efficiency, product reliability, and managing the cost of invar. Furthermore, insights from the case study on semiconductor bands can illustrate the practical implications of Invar’s properties, particularly in applications demanding precision and reliability.
Conclusion
Invar’s unique composition and properties position it as a critical material in precision engineering, particularly in aerospace and electronics. With its low coefficient of thermal expansion, Invar ensures dimensional stability, which is essential in applications where accuracy is paramount. The insights provided regarding Invar’s thermal properties and the impact of nickel pricing highlight the need for procurement managers to remain vigilant and informed about market trends and material performance.
The diverse applications of Invar underscore its versatility, from high-stakes aerospace components to intricate electronic devices. The various forms of Invar products—sheets, plates, rods, and custom-fabricated components—further illustrate its adaptability to meet specific project requirements. Understanding these applications allows procurement professionals to make strategic decisions that enhance operational efficiency and product reliability.
Ultimately, the advantages of Invar extend beyond mere functionality; they encompass long-term durability, reduced maintenance costs, and improved safety outcomes. As industries continue to evolve, the strategic utilization of Invar will remain a cornerstone in achieving precision and excellence in engineering applications. For procurement managers, leveraging this knowledge is key to navigating the complexities of material selection and ensuring optimal performance in their projects.