Blogs
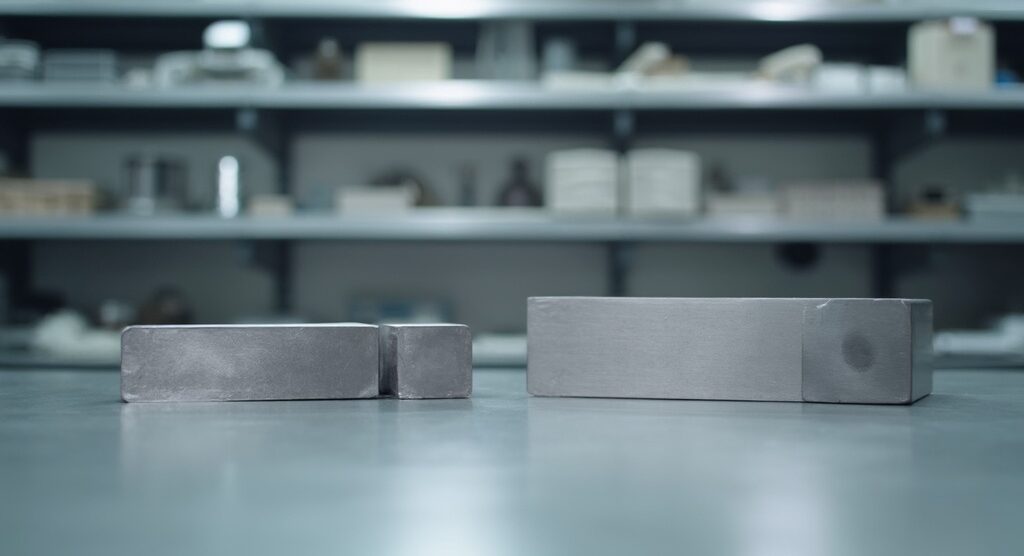
Understanding the Hardness of Titanium vs Stainless Steel: An In-Depth Tutorial
Introduction
In the realm of material selection, titanium and stainless steel stand out as two of the most pivotal choices for industries ranging from aerospace to medical applications. Each material boasts unique properties that cater to specific demands, with titanium recognized for its exceptional strength-to-weight ratio and corrosion resistance, while stainless steel is lauded for its toughness and versatility. As procurement managers navigate the complexities of material characteristics, understanding the fundamental properties, comparative hardness, applications, cost implications, and future trends of these metals is crucial.
This article delves into the intricate details of titanium and stainless steel, providing insights that empower informed decision-making in a landscape where performance and reliability are paramount.
Fundamental Properties of Titanium and Stainless Steel
Titanium is celebrated for its remarkable high strength-to-weight ratio and outstanding corrosion resistance, making it an optimal choice for aerospace and medical applications. Its lower density in relation to alloy provides a considerable benefit in weight-sensitive industries, where minimizing mass is essential for performance and efficiency.
In contrast, alloy is well-regarded for its toughness and durability, exhibiting excellent resistance to various corrosive environments. Depending on the specific alloy, corrosion-resistant metal can be finely adjusted to attain desired mechanical characteristics, enhancing its adaptability in automotive and electronics sectors.
Recent studies highlight the need for additional investigation of these materials; for instance, in a biomechanical study on proximal phalanx fracture fixation, metal implants exhibited greater stiffness and load-bearing capacity in comparison to their alloy counterparts. A comprehensive review highlighted that both a specific metal and stainless steel exhibited full return to function in more than 90% of tibial shaft fracture cases, yet it emphasized the need for larger, high-quality studies to delineate the comparative benefits more clearly.
As noted by Hunt et al., ‘They found a higher nonunion rate in the locked metal plates, but it is unknown whether these differences are attributable to the plate composition or plate design.’
As industries increasingly prioritize performance and longevity, understanding these fundamental properties becomes essential for selecting the most suitable substance for specific applications. Moreover, recent advancements in the properties and applications of alloys in 2024, along with the latest developments in corrosion resistance, further strengthen the significance of these substances in modern manufacturing and procurement choices.
Comparative Hardness: Titanium vs. Stainless Steel
When evaluating materials, it’s essential to consider their hardness as defined by the Mohs scale. This metal typically scores lower than many alloys of a certain type, with commercially pure versions noted at approximately 6 on the scale. In contrast, stainless steel hardness varies significantly, ranging from 5.5 to 8 based on specific alloy compositions. This disparity highlights that while titanium may be relatively softer, it compensates with exceptional ductility, facilitating easier shaping and forming during manufacturing processes.
According to Dr. Jane Smith, a materials scientist, ‘Titanium’s ductility allows for innovative designs that would be challenging to achieve with harder materials.’ This characteristic is particularly beneficial in applications that require complex geometries.
On the other hand, the greater hardness of stainless material contributes to enhanced wear resistance, making it ideal for demanding environments such as cutting tools and industrial machinery. For instance, a case study on the use of this metal in aerospace applications demonstrated its ability to withstand extreme conditions while maintaining structural integrity, whereas steel was found to suffer from fatigue cracking under similar stresses.
For procurement managers, understanding these material characteristics is vital; it enables a strategic assessment of durability, performance, and cost-effectiveness tailored to specific applications. The latest findings on the Mohs scale hardness of metal alloys, which now show advancements in alloy formulations achieving scores up to 7, further underscore its suitability in contexts that prioritize both strength and light weight, particularly in the aerospace and biomedical sectors, where biocompatibility is also a critical consideration.
Applications and Suitability of Titanium and Stainless Steel
Titanium’s unique properties make it a preferred choice in high-demand sectors such as aerospace and medical implants. With over 6 million tons produced annually, this metal is renowned for its lightweight and corrosion-resistant characteristics, which contribute to its effectiveness in aerospace components, jet engines, and chemical processing applications.
For instance, metal alloys are utilized in approximately 30% of the structural components of modern aircraft, highlighting their importance in the aerospace sector. Notably, the medical field has embraced this metal for its biocompatibility; as demonstrated by Per-Ingvar Branemark, who first placed a dental implant made of this remarkable substance into a human volunteer in 1965, showcasing how closely bone adheres to it.
Aerospace engineers have noted that titanium’s strength-to-weight ratio offers significant advantages in reducing fuel consumption and increasing payload capacity. In contrast, corrosion-resistant metal remains a staple in kitchenware, automotive parts, and structural components due to its strength and durability.
For instance, approximately 50% of the alloy produced is utilized in automotive applications, where its durability is essential for safety and longevity. Recent trends suggest that alloy materials continue to prevail in automotive applications, with advancements in compositions leading to enhanced corrosion resistance and decreased weight.
By comprehending the uses and benefits of both alloys, procurement managers can make knowledgeable choices that correspond with sector-specific needs and technologies.
Cost Considerations in Material Selection
Titanium is typically recognized as a more expensive material when compared to stainless steel, primarily due to the higher costs associated with its extraction and processing. This premium pricing positions this metal as a preferred choice for high-performance applications, particularly in industries such as aerospace, where reliability is critical. According to expert Larrin, ‘The investment in this metal often pays off in terms of performance and safety, especially in high-stakes environments.’
The durability and exceptional corrosion resistance of titanium often justify the investment, as failures in these sectors could lead to substantial financial losses or safety hazards. Conversely, stainless steel offers a more cost-effective alternative, with prices ranging from $1 to $1.50 per kilogram, but it may lead to unforeseen expenses if specific alloys are necessary to meet particular environmental requirements.
As procurement managers evaluate these materials, it is essential to account for the total cost of ownership, which encompasses not only initial material costs but also ongoing maintenance and potential replacement expenses. Recent cost analysis for 2024 shows that while prices for the metal have stabilized, the demand in aerospace continues to influence overall costs.
Recent reports indicate that titanium’s market position remains strong, especially in aerospace applications, where its properties are indispensable. Furthermore, case studies indicate that steel is often preferred in applications where cost-effectiveness, ease of fabrication, and alloy availability are paramount, such as in the construction and automotive industries.
Ultimately, a thorough cost analysis and an understanding of each component’s long-term implications are crucial for making informed procurement decisions.
Future Trends and Innovations in Titanium and Stainless Steel Alloys
Recent advancements in titanium alloys, particularly the emergence of beta titanium, have significantly enhanced the substance’s strength and usability across a variety of applications. This enhancement is essential as industries seek resources that can withstand demanding environments while providing versatility.
A key aspect of these advancements includes the mass transfer coefficient determined from limiting current measurements under steady-state conditions, which further supports the substance’s performance in electrochemical applications.
Simultaneously, advancements in corrosion-resistant alloys are remarkable, especially the launch of higher-performance duplex and super duplex materials, which offer enhanced resistance to corrosion and mechanical characteristics. The Tafel slope for pre-reduced Ferralium SD40, measured at −0.265 ± 0.008 V decade, highlights the advancements in these substances’ electrochemical behavior.
Furthermore, the global duplex stainless steel market remains highly fragmented, prompting companies to adopt competitive strategies such as mergers, acquisitions, and new product launches to maintain their foothold. For procurement managers, understanding these dynamics is essential for making informed, strategic decisions that align with evolving industry standards and customer expectations.
Looking ahead to 2024, the latest innovations in titanium alloys are expected to focus on enhanced performance metrics and sustainability, with future trends likely to emphasize lightweight materials and improved corrosion resistance, ultimately enhancing the value offered to stakeholders.
Conclusion
The exploration of titanium and stainless steel reveals the distinct advantages and applications of each material, essential for informed decision-making in various industries. Titanium, with its remarkable strength-to-weight ratio and corrosion resistance, emerges as a critical choice for aerospace and medical applications, where performance and reliability are paramount. Its unique properties enable innovative designs and support demanding applications, underscoring its value in high-stakes environments.
Conversely, stainless steel’s toughness and versatility make it a staple in automotive and kitchenware sectors. Its ability to be tailored through specific alloys enhances its durability, positioning it as a cost-effective option for many applications. Understanding the comparative hardness of these materials further enriches the procurement manager’s toolkit, providing insights into their suitability for different industrial needs.
Cost considerations play a significant role in material selection, as titanium’s higher price is often justified by its performance benefits in critical applications. Meanwhile, stainless steel offers a more economical alternative, emphasizing the importance of evaluating the total cost of ownership, including maintenance and long-term implications.
Looking towards the future, advancements in both titanium and stainless steel alloys promise to enhance their applicability and performance across industries. As innovations continue to emerge, staying abreast of these trends is vital for procurement managers aiming to align their material choices with evolving industry standards. Ultimately, a strategic approach to material selection will enable organizations to leverage the unique properties of titanium and stainless steel, driving improved performance and reliability in their operations.