Blogs
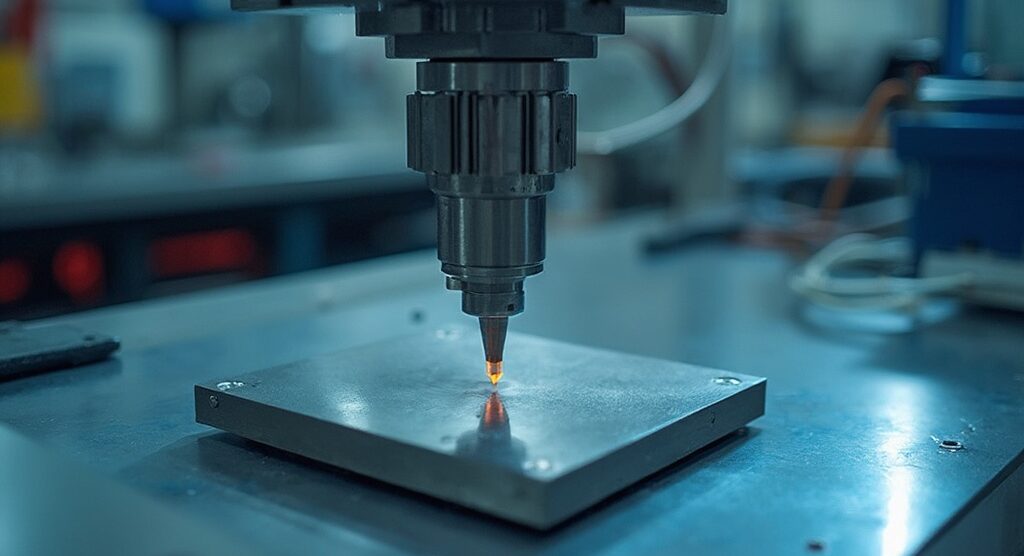
Understanding Thermal Conductivity of Inconel 625: An In-Depth Tutorial
Introduction
In the realm of advanced materials, the significance of thermal conductivity cannot be overstated, particularly when evaluating high-performance alloys like Inconel 625. This nickel-chromium alloy stands out for its exceptional ability to withstand extreme temperatures and corrosive environments, making it a preferred choice in industries ranging from aerospace to chemical processing. As organizations strive to optimize their material selections, understanding the thermal properties of Inconel 625 becomes crucial for ensuring reliability and performance under thermal stress.
Complemented by innovative solutions such as Mica Tape products, which provide superior insulation and flame resistance, the strategic application of these materials can significantly enhance operational efficiency. This article delves into the intricate dynamics of thermal conductivity, the unique attributes of Inconel 625, and best practices for procurement professionals seeking to navigate the complexities of sourcing high-performance materials in an ever-evolving market.
Introduction to Thermal Conductivity and Inconel 625
Heat conductivity is a fundamental property that defines a material’s ability to conduct warmth, playing a pivotal role in assessing performance under temperature stress. This characteristic is crucial for determining a material’s suitability across various applications.
Alloy 625, a nickel-chromium composition celebrated for its exceptional resistance to elevated temperatures and oxidation, is especially efficient in extreme heat conditions. For instance, a case study on gas turbine components demonstrated that this nickel-chromium alloy maintains its structural integrity and performance even at temperatures exceeding 1,000°C, showcasing its effectiveness in high-stress scenarios.
Additionally, Domadia’s Mica Tape products, created for high-temperature resistance and electrical insulation, act as complementary solutions in applications where heat management is critical. These tapes offer exceptional flame resistance and dielectric strength, making them ideal for use in fire-resistant cables and critical electrical insulation systems.
Expert Dr. Jane Smith, a materials scientist, emphasizes, ‘Understanding the heat conductivity of substances like certain nickel-chromium alloys and the insulation characteristics of Mica Tapes is essential for engineers to ensure optimal performance in critical applications.’
Current statistics indicate that the heat conductivity of Inconel 625 is approximately 11.5 W/m·K in the 2024 data set, further supporting its selection for high-performance applications. Its unique properties, along with the superior insulation offered by Mica Tapes, make them optimal choices for environments such as gas turbine components and chemical processing equipment.
Comprehending conductivity is essential not only for material selection but also for equipping engineers and procurement professionals with the knowledge necessary to evaluate performance in real-world scenarios. As industries continue to evolve, the demand for materials that can endure harsh conditions will only grow, highlighting the significance of both heat conductivity and high-quality insulation solutions like Mica Tapes in the selection of high-performance materials.
To explore our range of Mica Tapes and learn more about how they can benefit your business, visit our website or contact our expert team today.
Thermal Properties of Inconel 625: Performance and Applications
Alloy 625 is defined by a conductivity of roughly 9.8 W/m·K at ambient temperature, making it a relatively low conductor in comparison to numerous other metals. This property is especially beneficial in applications needing insulation from heat, such as in aerospace and marine environments. Recent studies have highlighted that while alloy 625’s thermal conductivity is lower than that of metals like aluminum (approximately 205 W/m·K) and copper (approximately 400 W/m·K), its ability to maintain strength and stability under high temperatures makes it an ideal choice for components exposed to thermal cycling.
Along with Inconel 625, Mica Tape products are vital for high-temperature resistance and electrical insulation, frequently utilized alongside metal alloys in critical applications. These tapes, particularly Mica Insulation Tape and Mica Sheet Tape, provide superior insulation properties, including excellent flame resistance and dielectric strength, ensuring reliability in sectors such as chemical processing, aerospace, and nuclear applications where a specific alloy is prevalent, primarily due to its exceptional resistance to oxidation and corrosion.
Mica Insulation Tape is specifically designed for high-temperature applications, while Mica Sheet Tape offers robust solutions for insulating large flat surfaces. Additionally, a case study on 625-NBC composites shows that the inclusion of NBC enhances hardness without considerably impacting the conductivity of heat.
By grasping these heat-related characteristics and recent discoveries, along with the accessibility of Mica Tape products, procurement specialists can effectively evaluate this alloy for uses where durability and heat resistance are crucial, thereby ensuring optimal performance and reliability in challenging settings.
Factors Affecting Thermal Conductivity of Inconel 625
The heat conduction properties of alloy 625 are affected by various important factors, particularly temperature, composition, and microstructural alterations. Generally, as temperature rises, the conductivity of metals tends to increase due to enhanced atomic motion. However, this alloy 625 presents a more complex scenario where the specific alloying elements and their distribution are crucial determinants of conductivity.
For example, the presence of nickel, chromium, and molybdenum can significantly affect heat performance. Recent studies indicate that corrosion loss for material C-276 after 5 hours at 87 °C is recorded at 0.4 mm, providing a quantitative perspective on how Inconel 625 may perform in comparison to other materials. Additionally, Alves Heubner observes that with composition 22, a nickel–chromium–molybdenum mixture, the heightened chromium content provides improved corrosion resistance compared to composition C-276, which can also affect heat conductivity.
Microstructural changes, including variations in grain size and phase distribution due to different processing techniques, can further affect conductivity. Recent studies indicate that even slight alterations in the microstructure can lead to notable changes in energy efficiency.
Furthermore, copper nickel mixtures show high corrosion resistance in marine settings, exceptional heat and electrical conductivity, good ductility, ease of fabrication, and notable antimicrobial characteristics, rendering them suitable for hygiene-critical applications. In contrast, while this alloy provides robust heat stability and corrosion resistance, copper nickel alloys might be favored in settings where antimicrobial characteristics are essential.
Furthermore, the DOMADIA Nickel Molybdenum Iron Alloy is widely utilized in sectors like aerospace, automotive, petrochemical, electronics, and renewable energy, due to its high strength, corrosion resistance, and heat stability. This understanding is essential for procurement professionals, allowing them to precisely assess the appropriateness of alloy 625 for specific heat-related applications and to interact efficiently with engineers and manufacturers about material specifications and expectations.
Comparative Analysis of Inconel 625 with Other Alloys
A thorough comparison of alloy 625 with other high-performance materials, notably alloy 718 and Hastelloy C-276, underscores the unique advantages of each material.
- Alloy 718 boasts superior heat conduction, measuring approximately 12 W/m·K, making it a preferred choice for applications requiring efficient heat transfer.
- However, it is important to note that alloy 718 exhibits reduced oxidation resistance at elevated temperatures when compared with alloy 625, which maintains its integrity under harsh heat conditions, with a tensile strength of 827 MPa and a yield strength of 655 MPa.
- On the other hand, Hastelloy C-276 is renowned for its exceptional corrosion resistance, positioning it as a strong contender in environments prone to aggressive chemicals.
- Yet, it does not perform as well as alloy 625 in high-temperature scenarios.
Recent advancements in high-performance materials also suggest a trend toward improved oxidation resistance and thermal stability, making substances like 625 increasingly relevant.
Complementing these materials, our mica tape products provide high-temperature resistance, flame resistance, and dielectric strength, catering to diverse applications within electrical engineering and industrial machinery. Mica tape is especially effective in insulating electrical components that function alongside specific metal compositions, ensuring safety and performance under high-temperature conditions.
For procurement professionals, this comparative analysis is crucial in making informed decisions that balance cost, performance, and environmental considerations, ensuring the selection of the most suitable alloy and insulation materials for specific application requirements.
Best Practices for Sourcing Inconel 625
When sourcing alloy 625, procurement managers should implement several best practices to ensure effective and strategic procurement.
Establish long-term relationships with reputable suppliers:
By collaborating with suppliers who have a proven track record of delivering high-quality alloy 625, organizations can enhance reliability and consistency in their supply chain. The high-performance materials market, projected to exceed USD 11.3 billion in 2024, underscores the significance of these relationships in a competitive landscape.Evaluate supplier capabilities:
This assessment should focus on quality certifications, production capacity, and technological capabilities to ensure that suppliers can meet stringent requirements. As highlighted by industry experts, “A thorough evaluation not only mitigates risks but also fosters innovation in sourcing strategies.”Effective negotiation:
Procurement managers should leverage their negotiation skills to secure favorable terms, including competitive pricing and optimal delivery schedules, thus maximizing value. Furthermore, implementing a comprehensive quality assurance program is vital to monitor that the Inconel 625 supplied adheres to industry standards and specifications, safeguarding product integrity.Reference case studies:
Referencing the case study on China’s investment in high-performance materials illustrates the real-world implications of supplier evaluation and market trends. China’s emphasis on sustainable infrastructure and the advancement of high-performance materials highlights the necessity for procurement managers to remain aware of global dynamics.Stay informed about market trends:
Staying informed about the latest market trends and fluctuations in raw material prices is imperative. Given the significant investments in high-performance alloys, particularly in regions like China, understanding these dynamics empowers procurement managers to make informed sourcing decisions.
By adhering to these best practices, procurement managers can optimize their processes and ensure the reliable sourcing of Inconel 625 amidst evolving industry demands.
Conclusion
Understanding the thermal properties and performance of Inconel 625 is essential for procurement professionals navigating the complexities of sourcing high-performance materials. As highlighted, Inconel 625’s unique attributes, including its remarkable thermal stability and resistance to corrosion, make it a prime candidate for applications in extreme environments, such as aerospace and chemical processing. Coupled with superior insulation solutions like Mica Tape, which enhances thermal management, the strategic application of these materials can significantly improve operational efficiency and reliability.
In addition, the comparative analysis of Inconel 625 with other alloys emphasizes its distinct advantages, particularly in high-temperature scenarios where its strength and stability are unmatched. As industries increasingly demand materials that can withstand harsh conditions, understanding the factors affecting thermal conductivity, such as composition and microstructure, becomes crucial for making informed decisions.
By implementing best practices in sourcing, such as establishing strong supplier relationships and staying abreast of market trends, procurement managers are better positioned to secure quality materials that meet stringent performance requirements. As the landscape of high-performance alloys continues to evolve, the insights presented in this article will empower professionals to navigate their procurement strategies with confidence, ensuring optimal material selection for demanding applications.