Blogs
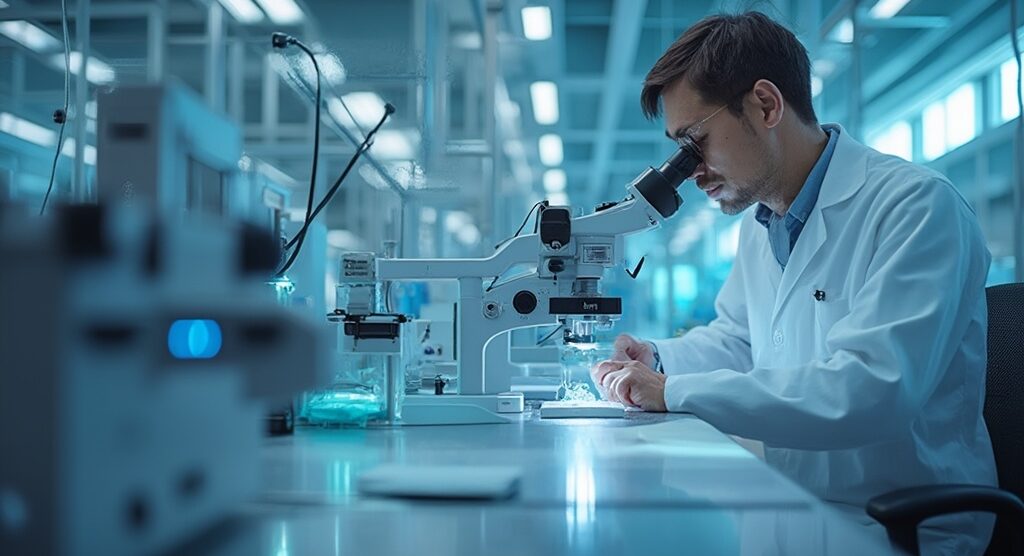
Understanding Titanium Beta 21S: An In-Depth Tutorial on Properties and Applications
Introduction
In the realm of advanced materials, Titanium Beta 21S stands out as a pivotal alloy, expertly engineered to meet the rigorous demands of both the aerospace and medical industries. Its unique beta-phase microstructure, enriched with aluminum and vanadium, endows it with an exceptional combination of strength, ductility, and corrosion resistance. As industries increasingly prioritize reliability and performance, the significance of Titanium Beta 21S has surged, particularly with its growing applications in 3D printing and complex aerospace structures.
This article delves into the defining characteristics, applications, and processing techniques of Titanium Beta 21S, equipping procurement managers with the insights needed to navigate its expanding role in high-performance projects and strategic sourcing decisions.
Introduction to Titanium Beta 21S: Definition and Overview
The distinguished 21S alloy is notable for its unique beta-phase microstructure, primarily composed of titanium along with alloying elements such as aluminum and vanadium. This composition confers an exceptional balance of strength, ductility, and corrosion resistance, making it a preferred choice in high-performance applications across the aerospace and medical industries.
As mentioned by industry expert Dr. Emily Carter, ‘The distinct characteristics of a specific alloy enable innovative designs in both aerospace components and medical devices, where reliability is paramount.’
The worldwide metal market is expected to grow considerably, increasing from USD 28.58 billion in 2024 to USD 53.65 billion by 2034 at a rate of 6.5%, signifying a rising demand for substances such as 21S. Recent advancements encompass its use in 3D printing technologies, which have revolutionized the production of complex aerospace structures and customized medical implants.
Furthermore, procurement managers should note that the alloy 21S is increasingly utilized in aerospace components and advanced medical devices, thanks to its reliability and adherence to stringent industry standards.
Comprehending the characteristics and uses of Alloy 21S not only assists in assessing its appropriateness for various projects but also aligns with contemporary trends that highlight the need for strong and sustainable materials in essential industries.
Exploring the Properties of Titanium Beta 21S: Composition and Characteristics
The alloy 21S contains approximately 6% aluminum and 4% vanadium, contributing to its enhanced mechanical properties. The alloy exhibits a density of about 4.43 g/cm³, tensile strength exceeding 900 MPa, and a yield strength around 800 MPa. Its excellent weldability and resistance to oxidation render it appropriate for high-temperature uses. Furthermore, the alloy 21S retains its strength at high temperatures, rendering it suitable for parts subjected to extreme conditions. Understanding these properties allows procurement managers to align their sourcing strategies with the specific needs of their projects.
In contrast, Mica Tape products, known for their high-temperature resistance and exceptional electrical insulation properties, offer a versatile alternative. With high mechanical strength and flame resistance, Mica Tapes are commonly used in electrical insulation systems and fire-resistant cables.
By evaluating both 21S and Mica Tape products, procurement managers can make knowledgeable choices that improve project safety and performance across diverse uses in electrical engineering and manufacturing.
Applications of Titanium Beta 21S: Where It Is Used
The alloy 21S has emerged as a critical material in the aerospace industry, particularly for components requiring exceptional strength-to-weight ratios, such as aircraft frames and engine parts. Its mechanical characteristics, including hardness and fatigue resistance, make it an ideal option for these demanding uses. In fact, statistics indicate that Alloy 21S comprises roughly 25% of the titanium alloys utilized in aerospace sectors because of its exceptional performance.
In medical settings, this alloy’s biocompatibility and corrosion resistance are paramount, leading to its widespread use in surgical instruments and implants. Notably, its breaking elongation ranges from 11% to 14%, demonstrating its capacity to endure significant stress without failure, which is crucial for both aerospace and medical applications.
Aerospace engineers have observed that the application of alloy 21S in essential components greatly improves the overall safety and reliability of aircraft systems. Furthermore, case studies have demonstrated that aerospace components crafted from a specific titanium alloy have successfully passed rigorous testing standards, reinforcing its reputation as a dependable material.
Furthermore, the alloy 21S is progressively employed in the manufacturing of high-performance automotive components, chemical processing machinery, and marine uses. This versatility highlights the growing market demand for titanium alloys across various industries.
As procurement managers, comprehending these tools, along with the supporting statistics, expert opinions, and case studies, is essential for identifying potential suppliers and negotiating effectively, ensuring that their projects meet the specific requirements of strength, durability, and biocompatibility.
Processing and Finishing Techniques for Titanium Beta 21S
Processing Titanium Beta 21S requires a strategic approach that encompasses various techniques, including forging, machining, and additive manufacturing. To achieve precise finishes while minimizing tool wear, it is critical to employ cutting tools specifically designed for titanium alloys. According to C. Cem Tasan, POSCO Professor of Materials Science and Engineering,
“For any aerospace use where an enhanced combination of strength and ductility is beneficial, this kind of invention is providing new opportunities.”
Among the common finishing techniques, surface treatments such as anodizing and shot peening are particularly effective in enhancing corrosion resistance and fatigue strength, essential qualities for high-performance uses. Recent case studies have demonstrated that the application of these techniques significantly improves the lifespan of components in aerospace settings.
Additionally, maintaining the integrity of the alloy’s properties during welding is paramount; thus, gas tungsten arc welding (GTAW) is recommended for optimal outcomes. Familiarity with these processing and finishing techniques not only aids procurement managers in evaluating supplier capabilities but also ensures the delivery of high-quality final products that align with current industry standards and innovations.
Conclusion
Titanium Beta 21S has established itself as an indispensable material within the aerospace and medical sectors, thanks to its unique beta-phase microstructure and the exceptional properties it offers. With a composition that includes aluminum and vanadium, this alloy provides a remarkable balance of strength, ductility, and corrosion resistance, positioning it as a preferred choice for high-performance applications. The increasing demand for Titanium Beta 21S, driven by advancements in 3D printing and the need for reliable materials, underscores its significance in addressing the challenges faced by procurement managers.
The diverse applications of Titanium Beta 21S, from aircraft components to surgical instruments, highlight its versatility and critical role in ensuring safety and reliability in demanding environments. The alloy’s impressive mechanical properties, including high tensile and yield strengths, coupled with its biocompatibility, make it a standout option for both aerospace and medical applications. Understanding the specific characteristics and benefits of Titanium Beta 21S enables procurement managers to make informed sourcing decisions that align with industry standards and project requirements.
Moreover, the processing and finishing techniques essential for working with Titanium Beta 21S play a vital role in maximizing its performance and longevity. By employing specialized methods such as forging, machining, and advanced surface treatments, procurement managers can enhance the material’s attributes, ensuring that end products meet the highest quality benchmarks. As the market for titanium alloys continues to grow, keeping abreast of these techniques and applications will empower procurement managers to secure the best suppliers and solutions for their projects, ultimately leading to superior outcomes in their endeavors.