Blogs
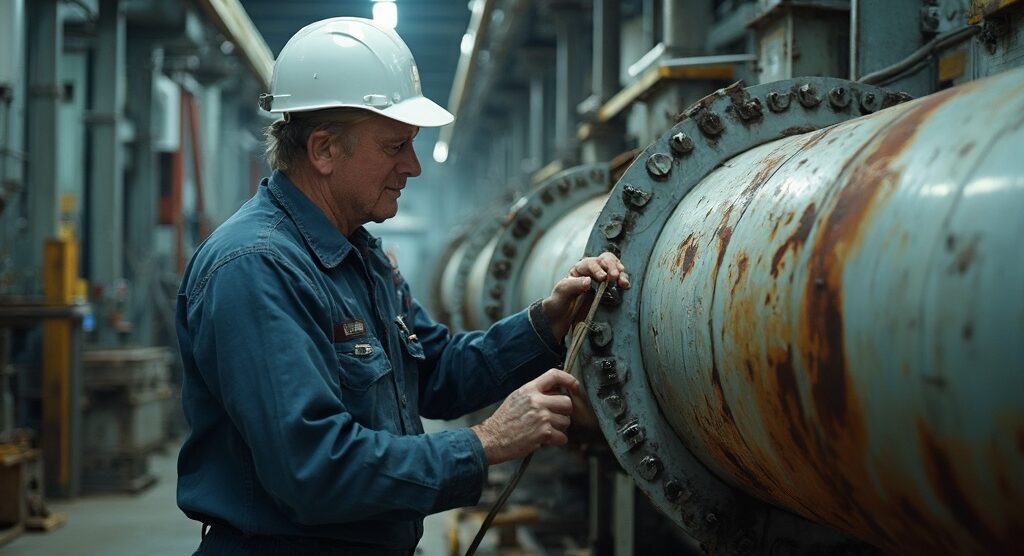
What Causes Metal to Corrode? A Comprehensive Breakdown
Introduction
Metal corrosion poses a significant challenge to industries worldwide, often underestimated yet profoundly impactful. This complex phenomenon, driven by various electrochemical reactions and environmental factors, can lead to substantial financial losses and safety risks if not effectively managed.
Understanding the causes of corrosion, from chemical interactions to the influence of environmental conditions, is crucial for procurement professionals tasked with selecting materials that can withstand these adversities.
With innovative strategies and advanced technologies emerging in corrosion prevention, organizations are equipped with the tools needed to mitigate risks and prolong the lifespan of metal components.
This article delves into the intricacies of corrosion, exploring its economic implications, preventive measures, and the importance of regulatory compliance, providing a comprehensive guide for informed decision-making in procurement practices.
Understanding the Causes of Metal Corrosion
Metal degradation is a multifaceted process influenced by various electrochemical reactions and environmental factors, which contribute to what causes metal to corrode. The primary causes of corrosion can be summarized as follows:
Chemical Reactions: Corrosion occurs when metals encounter moisture, oxygen, and other chemicals within their environment. A classic example is iron, which reacts with oxygen and water, resulting in rust (iron oxide). This degradation is not only a cosmetic issue but can significantly compromise structural integrity.
Environmental Factors: The rate at which deterioration occurs is heavily influenced by environmental conditions such as humidity and temperature. For instance, studies reveal that the deterioration rate of galvanized steel escalates notably between 50 °C and 70 °C. Moreover, the morphological and compositional changes in degradation products become increasingly pronounced when temperatures rise from 70 °C to 90 °C. Coastal regions, defined by salty air, encounter even greater rates of deterioration due to the presence of chlorides.
Electrochemical Processes: Corrosion predominantly manifests through electrochemical mechanisms where substances lose electrons to their surroundings, leading to deterioration. The risk of galvanic deterioration increases when dissimilar metals are in contact, creating a pathway for accelerated degradation.
Microbial Influences: In certain environments, specific bacteria can worsen deterioration processes by producing harmful byproducts. This phenomenon is especially observed in water systems where microbial-induced deterioration can result in considerable substance loss.
It is essential for procurement professionals to understand what causes metal to corrode in order to select materials and protective coatings that can withstand corrosive environments. In this context, copper nickel alloys offer several benefits: they demonstrate high resistance to degradation in marine environments, outperform stainless steel, and provide excellent thermal and electrical conductivity, making them ideal for heat exchangers and electrical applications. Additionally, their good ductility and ease of fabrication enhance their applicability in various scenarios.
Notably, their antimicrobial properties also render them suitable for applications where hygiene is paramount, such as in medical equipment and food processing environments, where the prevention of bacterial growth is critical.
By making informed choices, organizations can prolong the lifespan of metallic components and minimize costs associated with maintenance and replacements. As emphasized by Almeida E. et al., the atmospheric deterioration of metals varies significantly between rural and urban settings, highlighting the need for tailored solutions based on environmental conditions.
In practical terms, addressing existing deterioration is crucial for minimizing losses, as illustrated in the case study on ‘Rust Removal Solutions,’ where techniques like Shot Blasting, Vibratory Finishing, and Ultrasonic Washing are employed for effective rust removal. This ensures rapid and cost-effective solutions for various part sizes, helping to maintain operational efficiency.
Furthermore, the collaboration in rust research is vital, as noted by Gaoxiang Hu, who provided experimental materials and processed specimens for this study. This collaboration improves our comprehension of deterioration dynamics and guides better procurement decisions.
Preventing Corrosion: Strategies and Best Practices
To effectively reduce deterioration and enhance the longevity of metal components, organizations should implement a series of strategic practices:
Material Selection: Opt for corrosion-resistant materials, such as Beryllium Copper, which is known for its non-sparking, corrosion-resistant, and highly durable properties. This alloy is particularly ideal for explosive environments due to its excellent thermal and electrical conductivity. A thorough understanding of what causes metal to corrode is essential for making informed decisions that enhance longevity.
Protective Coatings: The application of protective coatings—ranging from paints and varnishes to advanced galvanization techniques—can drastically reduce deterioration rates. These layers act as essential barriers, preventing moisture and corrosive agents from infiltrating the metal surface. Notably, Metal Coatings Corp. leverages over four decades of expertise in this field, utilizing their state-of-the-art 150,000 square foot facility to meet urgent project needs with precision and professionalism. As protective coatings can extend equipment life by nearly 300%, their importance in preventing rust cannot be overstated.
Regular Maintenance: Establishing a routine maintenance schedule that includes thorough inspections and cleaning is crucial, especially for Beryllium Copper tools. Regular cleaning helps maintain their properties and avoids exposure to harsh chemicals that could affect their performance. It is crucial to carry out inspections to detect early indications of deterioration and address them before they escalate into severe damage, thereby protecting investments and extending the service life of equipment.
Cathodic Protection: Implementing cathodic protection techniques, such as sacrificial anodes or impressed current systems, can be particularly effective in safeguarding materials, especially in critical applications like pipelines and storage tanks.
Managing the environmental elements in which substances are stored or used is crucial in preventing deterioration by understanding what causes metal to corrode. Strategies may include reducing humidity levels, ensuring adequate drainage, and minimizing exposure to corrosive substances.
By integrating these strategies into procurement and maintenance practices, organizations can significantly diminish the risk of corrosion. Specifically, the use of Beryllium Copper tools not only meets safety standards in explosive environments but also enhances the durability and operational reliability of their components. Additionally, customization services for Beryllium Copper tools are available to meet specific industrial requirements, ensuring that tools are tailored to the unique needs of each application. The effectiveness of protective layers is exemplified by Metal Coatings Corp.’s Fluorokote#1®, which is engineered for extreme chemical applications and excels in harsh environments. This unique coating has been shown to provide robust protection against humidity, saltwater, and chemicals, enhancing the durability and lifespan of metal components across various industries.
The Economic Impact of Corrosion
Corrosion is often likened to a ‘hidden tax’ on the economy, reflecting its extensive yet frequently underestimated financial ramifications. The economic effect of deterioration can be categorized into several key areas:
Direct Costs: These costs include expenditures for repairs, replacements, and maintenance of corroded structures and equipment. Industries face staggering annual expenses, with corrosion-related repairs in infrastructure, pipelines, and vehicles amounting to billions. For instance, deterioration in the pulp and paper sector alone results in a staggering $6 billion in losses each year, while petroleum refining suffers $3.7 billion, and food processing experiences losses of $2.1 billion. This highlights the critical need for effective management.
Indirect Costs: These costs stem from operational downtime related to maintenance and repairs, which can severely disrupt productivity. In the manufacturing sector, equipment malfunctions caused by rust can halt production lines, leading to substantial financial setbacks. As the direct and indirect expenses related to deterioration in the U.S. reach a combined total of approximately $552 billion, the financial urgency for proactive management practices is evident.
Safety Risks: The implications of corrosion extend beyond financial metrics, posing significant safety threats. The degradation of critical components can compromise structural integrity, resulting in hazards that may lead to injuries, legal liabilities, and increased insurance premiums. It is essential for procurement managers to consider these risks when sourcing resources and solutions.
Environmental Impact: Corrosion also presents environmental challenges, particularly when it leads to leaks or failures, such as in pipelines. Such incidents not only incur costly cleanup expenditures but can also attract regulatory fines, further amplifying financial burdens.
Understanding these economic implications allows procurement professionals to make informed decisions regarding investments in corrosion-resistant materials and preventive measures. By doing so, organizations can not only mitigate current costs but also safeguard against future financial losses, ultimately enhancing operational efficiency and sustainability. As emphasized in the case study ‘Savings Through Protection Against Deterioration’, effective management can result in savings of 25% to 35% of yearly deterioration-related expenses, reinforcing the case for proactive strategies in procurement choices.
Here’s a breakdown of how much money each industry loses due to deterioration:
- Pulp And Paper: $6 billion
- Petroleum Refining: $3.7 billion
- Food Processing: $2.1 billion
- Chemical, Petrochemical, and Pharmaceutical: $1.7 billion
- Oil and Gas Exploration and Production: $1.4 billion
- Home Appliances: $1.5 billion
- Agricultural: $1.1 billion
- Mining: $0.1 billion
Innovative Technologies in Corrosion Prevention
Recent advancements in technology have ushered in innovative solutions for corrosion prevention that procurement professionals should consider:
Smart Finishes: These advanced layers possess the ability to adapt their properties in response to environmental changes, delivering real-time protection against corrosion. For instance, self-repairing layers can autonomously mend minor damages, significantly extending the lifespan of the substrate and minimizing maintenance expenses. According to industry studies, these coatings can reduce maintenance costs by up to 30% over the lifecycle of assets.
Degradation Monitoring Systems: By utilizing sensors and IoT technology, these systems provide continuous oversight of metallic components, identifying early indicators of deterioration. A recent study found that implementing monitoring systems for deterioration can lead to a 25% reduction in unexpected downtime, enabling timely interventions and maintenance, ultimately extending the operational life of assets.
Advanced Alloys: Ongoing research into new metal alloys has produced substances with improved rust resistance, particularly suited for harsh environments. Nickel-based alloys, for example, are widely adopted in the aerospace and marine sectors due to their exceptional performance under challenging conditions.
Nanotechnology: The incorporation of nanotechnology in the creation of finishes and treatments has significantly enhanced the protective attributes of substances. By utilizing silica-based layers, which take advantage of the stability and versatility of silica, manufacturers can improve the durability of materials against deterioration. This approach draws inspiration from natural organisms like diatoms and certain bacteria, which have evolved unique protective mechanisms. The case study titled “Understanding Silica” highlights how silica, primarily composed of silicon dioxide, is used to create protective coatings for nanoparticles, demonstrating its effectiveness in enhancing performance in challenging environments.
By staying informed about these innovative technologies, procurement professionals can enhance their strategies and ensure the implementation of the most effective solutions in the fight against deterioration. As noted by industry experts, by harnessing their reflective properties, these versatile substances offer the potential to mitigate urban heat islands, enhance energy efficiency, and foster a more sustainable and cooler future for our planet. This highlights the essential role that contemporary substances and technologies have in promoting sustainability while tackling deterioration issues.
Regulatory Standards and Compliance in Corrosion Management
Ensuring compliance with regulatory standards is paramount for effective corrosion management, particularly in understanding what causes metal to corrode across various industries. Regulatory authorities require thorough assessments of substances and processes to protect against corrosion-related failures. Domadia’s Beryllium Copper Plates exemplify this commitment to quality, manufactured with ALLOY 25 and compliant with numerous industry standards such as ASTM C17200 and ISO certifications, ensuring that procurement managers can select options that not only meet but exceed regulatory requirements.
Key considerations include:
Industry Standards: Organizations like ASTM International and ISO create essential guidelines for substances and coatings relevant in particular contexts. A deep understanding of these standards empowers procurement professionals to choose products like Domadia’s Beryllium Copper Plates, which are designed to withstand rigorous demands while ensuring compliance with biocompatibility and toxicity evaluations.
Environmental Regulations: Compliance with environmental laws is crucial, especially those governing hazardous substances and emissions. Procurement strategies must account for the entire lifecycle of resources, including safe disposal methods, to ensure compliance and mitigate environmental impacts while also reviewing manufacturing processes to understand what causes metal to corrode and minimize regulatory risks.
Safety Standards: Sectors like construction, aerospace, automotive, and electrical manufacturing are governed by rigorous safety regulations that necessitate regular inspections and maintenance of metallic components.
Domadia’s ultra-thin metal foils, produced with unmatched expertise and stringent quality control, exemplify the proactive approach needed to minimize the effects of what causes metal to corrode and ensure operational safety, emphasizing the need for performance testing to validate integrity.
- Documentation and Reporting: Maintaining meticulous records of compliance with deterioration management practices is crucial for audits and regulatory inspections. This documentation should encompass material specifications, maintenance schedules, and inspection results to demonstrate adherence to established standards, reflecting a commitment to quality assurance in manufacturing processes.
By prioritizing compliance with these regulatory frameworks and leveraging superior materials like Domadia’s Beryllium Copper Plates, procurement professionals not only mitigate risks associated with corrosion but also enhance safety and contribute to sustainable practices within their organizations.
As highlighted in the case study on evaluating quality assurance methods for medical devices with metal coatings, which emphasized the importance of rigorous quality control and compliance checks, a robust compliance strategy is essential for protecting health and ensuring the integrity of manufacturing processes.
Conclusion
Metal corrosion remains a critical issue that demands attention from procurement professionals across various industries. Understanding the multifaceted causes of corrosion—ranging from chemical reactions and environmental factors to electrochemical processes and microbial influences—equips decision-makers with the knowledge needed to select appropriate materials and protective measures. Innovations such as corrosion-resistant alloys and advanced protective coatings play a pivotal role in mitigating these risks, ultimately prolonging the lifespan of metal components and reducing maintenance costs.
Moreover, the economic implications of corrosion cannot be overlooked. With billions lost annually due to direct and indirect costs associated with corrosion, proactive management strategies are essential. Investing in effective corrosion prevention methods not only safeguards against financial losses but also enhances operational efficiency and safety. As demonstrated, industries can achieve substantial savings through diligent corrosion management, reinforcing the necessity for informed procurement practices.
Emerging technologies, including smart coatings and corrosion monitoring systems, provide further avenues for organizations to enhance their corrosion management strategies. By embracing these innovations, procurement professionals can ensure their operations remain resilient against the challenges posed by corrosion, while also aligning with regulatory standards that govern material use and environmental impact.
In conclusion, an informed, strategic approach to corrosion management is vital for organizations aiming to protect their investments and maintain operational integrity. By prioritizing advanced materials, innovative technologies, and regulatory compliance, procurement professionals can effectively combat corrosion and contribute to a more sustainable and economically viable future for their industries.