Blogs
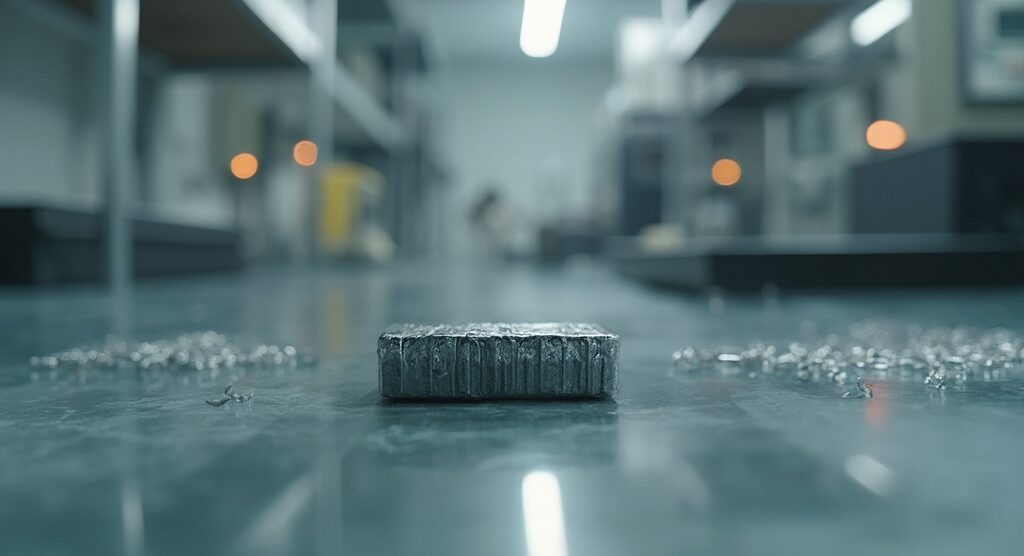
Comparative Study of Titanium and Steel Alloys in Modern Engineering
Introduction
In the realm of advanced engineering and material science, the choice between titanium and steel alloys can significantly influence the performance and longevity of critical components across various industries. Each material brings a unique set of physical, mechanical, and economic properties that cater to specific applications. Understanding these differences is pivotal for procurement managers and engineers striving to optimize their designs for efficiency, durability, and cost-effectiveness.
This article delves into a comprehensive comparison of titanium and steel alloys, examining their physical and mechanical properties, corrosion resistance, biocompatibility, and economic considerations. It provides valuable insights into how these materials are utilized in sectors such as aerospace, medical, chemical, and beyond, helping professionals make informed decisions in selecting the right alloy for their engineering needs.
Physical Properties Comparison
Titanium and metal mixtures display unique physical characteristics that affect their use in different engineering fields. Titanium is prized for its low density, making it significantly lighter than most steel alloys. This characteristic is crucial in the aerospace industry, where reducing weight enhances fuel efficiency. Furthermore, the metal’s high melting point makes it suitable for high-temperature environments, such as aircraft engines, including components like the fan, compressor, combustion chamber, and turbine. However, the titanium market has faced challenges; a significant decrease in production from Ukraine has led to a global reduction in supply, driving up costs and impacting the aviation supply chain.
Conversely, metal alloys are recognized for their exceptional thermal and electrical conductivity, rendering them perfect for uses that demand effective heat dissipation. For instance, the capacity of this metal to maintain structural integrity at both high and low temperatures is a vital consideration in the design of materials for extreme conditions. Despite historical challenges—such as the embrittlement of metal at low temperatures that contributed to the Titanic disaster—ongoing research aims to enhance its performance across a broader temperature spectrum.
In contrast to titanium’s lightweight benefits, the development of new steel mixtures continues to focus on balancing strength and ductility, as seen in recent advancements with scandium and zirconium additions to enhance mechanical properties. These innovations underscore the essential trade-offs between material characteristics and their uses, stressing the significance of choosing the appropriate metal for specific engineering needs.
Mechanical Properties: Strength, Hardness, and Elastic Modulus
‘Titanium mixtures are renowned for their high strength-to-weight ratio, making them indispensable in applications where weight reduction is crucial.’. For example, certain metal mixtures can reach tensile strengths similar to specific high-strength iron mixtures while keeping a notably lighter mass, which is particularly advantageous in aviation and vehicle manufacturing sectors. Regardless, metal mixtures frequently demonstrate greater hardness and stiffness, which are beneficial in building and other industries where resilience under pressure is crucial.
The elastic modulus of this metal is lower than that of steel, indicating that it can deform more easily under load. This characteristic must be factored into design considerations, particularly in engineering contexts where rigidity and minimal deformation are critical. For instance, Grade 5 metal mixture, also referred to as Ti6Al4V, merges a certain metal, aluminum, and vanadium to provide exceptional strength and performance in high-stress applications such as aerospace and military uses.
Recent advancements in metal composite manufacturing, such as 3D printing and forging, have further improved their mechanical properties. A study released in the journal Advanced Materials emphasized a new lattice structure design that produced a material 50% stronger than the next most durable metal of comparable density utilized in aerospace applications. Such advancements highlight the capability of these metals to satisfy the rigorous needs of contemporary engineering and industrial uses.
Corrosion Resistance: Titanium vs. Steel
The ability to withstand deterioration is a key differentiator between titanium and iron-based materials. Titanium is famous for its remarkable ability to withstand corrosion, especially in harsh conditions like seawater or chemical exposure. This remarkable property stems from the formation of a stable oxide layer that protects the underlying metal. In contrast, steel alloys are more vulnerable to rust and corrosion unless treated or mixed with elements like chromium to improve durability. Consequently, the selection among these substances frequently depends on ecological factors, with the favored choice for uses demanding long-lasting resilience in severe environments.
Titanium’s exceptional ability to withstand corrosion makes it a perfect material for various sectors, including chemical processing, where it is utilized in heat exchangers, valves, and tanks. Its ability to withstand aggressive chemicals and environments ensures longevity and reliability. Likewise, in the oil and gas sector, the durability of this metal against chloride corrosion is essential for machinery subjected to severe marine conditions, like oil platforms.
The aerospace industry also gains greatly from the corrosion durability of this metal. Its strength-to-weight ratio, along with its capacity to withstand elevated temperatures, makes this metal essential for aircraft and spacecraft parts, in addition to jet and rocket engines. This not only improves performance but also reduces maintenance costs over time.
In the medical field, titanium’s biocompatibility and durability against bodily fluids make it the material of choice for implants such as artificial joints and dental implants. Its durability ensures that these medical devices remain functional and safe over extended periods.
Steel alloys, although frequently utilized, need extra processes to improve their ability to withstand corrosion. These treatments can increase the overall expense and intricacy of utilizing metal in settings where rust is a significant concern. Consequently, for uses requiring high durability and resistance to tough conditions, this metal remains the superior choice.
Applications in Modern Engineering: Aerospace, Medical, and Chemical Industries
Titanium and steel combinations find diverse applications across various industries due to their unique properties. In aerospace engineering, metal mixtures, recognized for their remarkable strength-to-weight ratio and superior performance, are essential for aircraft components and structures. The healthcare sector greatly depends on the biocompatibility and durability against corrosion of this metal, establishing it as the preferred substance for implants, prosthetics, and surgical tools.
Steel mixtures, on the other hand, dominate the construction and automotive sectors. Their strength and cost-effectiveness make them ideal for building infrastructure and manufacturing vehicles. In the chemical sector, the superior resistance of this metal to aggressive substances makes it suitable for equipment like heat exchangers, valves, and tanks. Conversely, steel alloys are preferred for more general applications due to their durability and versatility.
Furthermore, this metal is essential in the military field for armored vehicles, aircraft, and naval equipment, due to its strength and durability. The sports sector gains from the lightweight characteristics of this metal for producing high-performance gear such as bicycle frames and golf clubs. In the oil and gas sector, the metal’s resistance to harsh marine environments makes it essential for offshore platforms and equipment, ensuring longevity and reliability in demanding conditions.
Biocompatibility and Use in Medical Implants
Titanium is highly regarded in the medical field due to its exceptional biocompatibility, a property that allows it to interact safely with biological systems. This means that metal implants can integrate seamlessly with bone and tissue, significantly reducing the risk of rejection. In contrast to steel alloys, which can lead to issues such as allergic reactions or corrosion in the body, this metal stays stable and non-reactive. This biocompatibility, along with its corrosion resistance, makes this metal the preferred material for a wide range of medical implants, including dental fixtures and orthopedic devices. As Dr. Alexei Mlodinow of Surgical Innovation Associates noted, advancements in titanium-based implants are pivotal in improving outcomes for patients undergoing procedures such as joint replacements and dental surgeries. The distinctive characteristics of this metal not only enhance patient safety but also promote faster healing and better integration with the body.
Economic and Commercial Considerations: Cost, Availability, and Fabrication
From an economic perspective, metal alloys are generally more cost-effective and widely available compared to titanium. The reduced raw material expenses and well-established manufacturing methods for this metal make it an appealing choice for large-scale production. For instance, North America is experiencing significant market growth in the stainless material sector, driven by its extensive use in automotive, construction, and renewable industries. This accelerated production highlights the region’s potential in the global steel market.
On the other hand, this metal is frequently pricier, partly because of the difficulties associated with its extraction and processing. Ukraine’s abundant mineral resources have historically played a crucial role in global supply, but recent geopolitical conflicts have severely disrupted this supply chain. This disruption has notably impacted the aerospace and aviation industries, leading to delays and resource shortages in critical components.
Although the initial expenditure for metal components may be higher, their long-term advantages, including decreased upkeep and durability, can validate the expenses in particular uses. For example, Grade 5 titanium alloy, known for its outstanding properties, is a popular choice in various high-performance industries due to its exceptional strength and durability. Evaluating these economic factors is essential for making informed procurement decisions, especially in sectors where material performance and longevity are paramount.
Conclusion
The comparison between titanium and steel alloys reveals critical insights into their respective properties and applications, which are vital for making informed decisions in engineering and procurement. Titanium, with its lightweight and exceptional corrosion resistance, stands out in industries such as aerospace and medical, where performance and longevity are paramount. Its high strength-to-weight ratio and biocompatibility make it the preferred choice for applications that demand durability and safety, such as aircraft components and surgical implants.
Conversely, steel alloys maintain a strong presence in construction and automotive sectors due to their cost-effectiveness and availability. Their superior hardness and rigidity make them suitable for applications that require durability under stress. However, the economic factors associated with titanium, such as higher initial costs and complex fabrication processes, must be weighed against its long-term benefits, particularly in high-performance environments where reduced maintenance and increased lifespan can offset upfront expenses.
Ultimately, the choice between titanium and steel alloys should be guided by the specific requirements of each application, including environmental conditions, mechanical demands, and economic considerations. Understanding the unique strengths and limitations of each material enables engineers and procurement managers to optimize their designs for efficiency, durability, and cost-effectiveness, ensuring that the right alloy is selected for each critical component.