Blogs
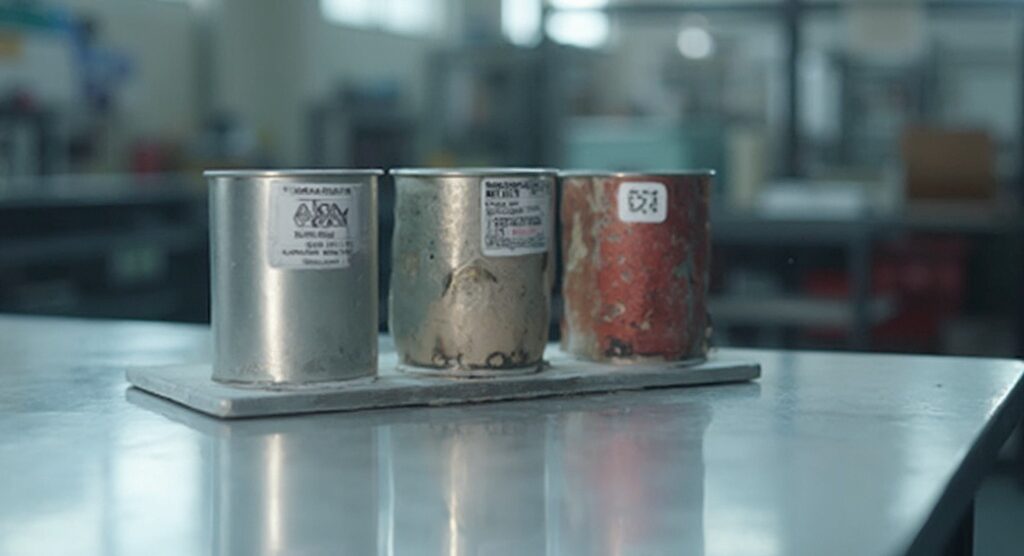
Evaluating Performance Metrics in Steel vs Titanium Applications
Introduction
In the realm of material science and engineering, understanding the differences between steel vs titanium presents a critical decision that significantly influences the performance, durability, and cost-efficiency of various applications. This article delves into a comparative analysis of steel and titanium, scrutinizing their physical properties, corrosion resistance, tensile strength, and machinability. By exploring these factors, procurement managers and industry professionals can gain valuable insights to make informed decisions that align with their strategic objectives.
The discussion includes expert perspectives and recent advancements, providing a comprehensive understanding of how these two materials can be optimally utilized in sectors ranging from aerospace to offshore engineering.
Physical Properties Comparison
Steel and another metal exhibit notable differences in their physical properties, each offering unique advantages. Steel, an alloy primarily composed of iron and carbon, boasts a higher density, which translates to greater yield strength and durability. This makes the metal an ideal material for applications requiring robust structural integrity. However, its higher density also results in increased weight, which can be a drawback in certain industries.
On the other hand, this metal is celebrated for its remarkable combination of strength and lightness. Weighing approximately 40% less than steel, this metal’s low density significantly reduces overall weight without compromising tensile strength. This characteristic is particularly advantageous in sectors where weight reduction is crucial, such as aerospace engineering. The ongoing shortage of this metal, exacerbated by geopolitical factors such as the conflict in Ukraine, underscores its critical role in high-tech industries. As Toma Matutyte, CEO of Locatory.com, points out, the disruption in metal supply chains has profound implications for the aerospace and aviation sectors, necessitating agile and innovative supply chain strategies.
The aerospace sector’s dependence on this metal is further emphasized by its excellent resistance to corrosion and compatibility with biological systems, rendering it essential for both aircraft parts and medical implants. The progress in metal alloy processing, as shown by the studies on severe plastic deformation methods, continue to improve its mechanical characteristics and broaden its range of uses. The strategic choice between iron and titanium thus relies on a balance among strength, weight, and cost, customized to the particular needs of each use.
Corrosion Resistance
Titanium’s impressive corrosion resistance stems from its ability to form a stable oxide layer, making it ideal for use in harsh environments such as marine and offshore applications. This natural protection reduces the need for additional coatings, which are often necessary for steel to fend off rust. For instance, offshore wind farms, which are expanding rapidly due to the shift towards renewable energy, benefit significantly from titanium’s durability. According to the International Energy Agency, global offshore wind capacity is projected to increase fifteen-fold by 2040, underscoring the importance of materials that can withstand harsh conditions with minimal maintenance. In contrast, the reliance on protective measures not only increases initial costs but also elevates long-term maintenance expenditures. Consequently, this metal’s exceptional resistance to corrosion provides a significant benefit for sectors where durability and dependability are essential.
Tensile Strength and Weight Considerations
Tensile strength serves as a crucial factor in material selection, and both iron and titanium excel in this aspect. Steel typically boasts higher tensile strength, making it particularly suitable for structural applications that bear heavy loads. For example, in the automotive industry, steel’s robustness ensures safety and durability in vehicle frames. Conversely, this metal’s exceptional strength-to-weight ratio allows for substantial weight reduction while maintaining structural integrity. This characteristic proves invaluable in aerospace components, where minimizing weight without compromising strength is crucial. Remarkably, research from Chalmers University of Technology highlights advancements in substances like carbon fiber composites, which combine stiffness and energy density, further emphasizing the innovative strides in engineering of these substances.
Cost and Machinability Comparison
Cost is a significant factor when comparing steel and another metal. Steel is generally more affordable and widely available, making it the go-to material for many manufacturing processes. However, this metal, although pricier, provides distinct benefits in particular uses because of its characteristics. High-strength metal forgings, for example, are valued for their exceptional mechanical properties and are extensively used in high-performance industries such as aerospace, automotive, and medical sectors.
With recent technological progress introduced by Industry 4.0, manufacturing procedures are swiftly changing, resulting in more advanced uses for substances such as metal. Despite its higher cost, the investment in titanium can be justified by its superior strength-to-weight ratio and corrosion resistance, which are critical in demanding environments.
Machinability also varies significantly between the two substances. Steel is easier to cut and shape, making it more cost-effective in terms of production time and tooling. Titanium, on the other hand, requires specialized techniques and tools, potentially increasing production costs and time. This trade-off between cost and performance must be carefully evaluated based on the project requirements. ‘Based on a poll carried out by Sapio Research, dependability is a key focus for companies, and investing in resources that improve durability and performance can have a beneficial effect on business reputation and financial success.’.
In summary, while steel remains the economical choice for many applications, the long-term benefits of titanium in specific high-performance scenarios cannot be overlooked. The decision between these two materials should be driven by a thorough analysis of project-specific needs, balancing initial cost with performance and reliability gains.
Conclusion
The comparative analysis of steel and titanium reveals critical insights that can guide procurement managers in making informed decisions tailored to their specific applications. Steel, with its higher density and tensile strength, serves as a robust choice for structural applications, particularly in industries like automotive and construction. However, its susceptibility to corrosion necessitates protective measures, which can increase both initial and long-term costs.
In contrast, titanium stands out for its exceptional strength-to-weight ratio and superior corrosion resistance, making it indispensable in sectors such as aerospace and offshore engineering. The ongoing advancements in titanium processing and its ability to withstand harsh environments highlight its strategic value, despite the current challenges in supply chains. As industries increasingly prioritize weight reduction and longevity, titanium’s role becomes ever more vital.
Ultimately, the decision between steel and titanium should be guided by a comprehensive evaluation of project requirements, balancing factors such as cost, performance, and durability. While steel may offer immediate economic advantages, the long-term benefits of titanium in high-performance applications can yield significant returns on investment. A strategic approach to material selection will ensure that procurement managers align their choices with the overarching goals of performance and sustainability in their respective industries.