Blogs
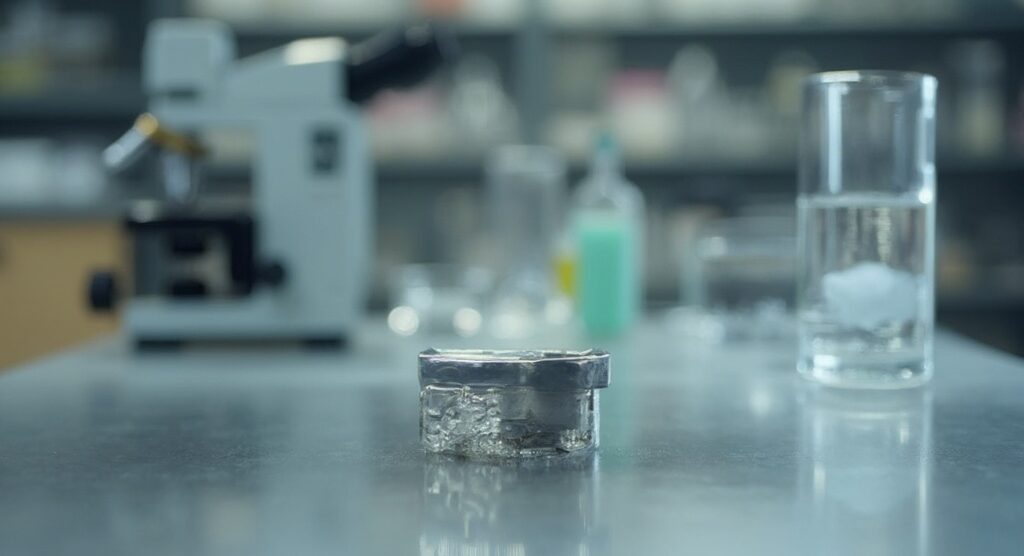
Evaluating Titanium: How Strong Is This Remarkable Metal?
Introduction
Evaluating Titanium is essential to understanding why this metal plays a key role in engineering and innovation across various industries. Known for its impressive physical and chemical properties, titanium has become a foundation of modern material science.
This article highlights titanium’s unique qualities—such as its strength-to-weight ratio, corrosion resistance, high melting point, and biocompatibility. These traits make it vital in aerospace, automotive, medical, and chemical sectors.
We also explore the latest processing techniques and the urgent need for stable supply chains due to global disruptions. This evaluation reveals titanium’s long-term value and future potential in advanced engineering.
Evaluating Titanium’s Physical Properties
Titanium is a transition metal known for its exceptional characteristics. It has a low density, making it much lighter than many other metals. This is highly beneficial for industries that prioritize weight reduction.
Its melting point is around 1,668°C (3,034°F), providing excellent thermal stability. Titanium maintains its shape and strength even under extreme heat.
One standout feature is its corrosion resistance. A passive oxide layer forms on the surface, shielding the metal in harsh conditions. This makes it ideal for aerospace, medical, and marine use.
Titanium also offers a high strength-to-weight ratio. It delivers robust performance without unnecessary weight. In manufacturing, titanium forgings undergo intense processes to gain top-level mechanical strength. These are crucial for demanding applications.
Recent advancements, like severe plastic deformation, continue to enhance its strength and corrosion resistance. These improvements help titanium meet new challenges in cutting-edge industries.
Chemical Characteristics of Titanium
Titanium is reactive, especially at high temperatures. It easily forms bonds with elements like oxygen, nitrogen, and carbon. This affects its behavior and properties.
In everyday conditions, titanium quickly develops a layer of titanium dioxide. This stable oxide increases its durability and shields it from corrosion.
The metal is highly resistant to acids such as sulfuric and hydrochloric, often used in chemical processing. It also performs well in non-oxidizing environments. This makes titanium suitable for a wide range of high-performance applications.
How Strong Is Titanium? A Look at Its Mechanical Power
Titanium is celebrated for its excellent strength-to-weight ratio. It’s often compared to steel but is significantly lighter. With a yield strength reaching up to 880 MPa, it can handle intense pressure without deforming.
It also retains strength at high temperatures, making it ideal for aerospace, medical, military, and automotive industries.
Titanium forgings, crafted through precise processes, provide durability and precision. These forged components are strong and lightweight—perfect for high-performance roles.
Recent global events have affected titanium supply, especially due to conflicts in Ukraine. This has raised costs and created shortages. As a result, companies are turning to alternate sources like China to stabilize supply chains and maintain access to aerospace-grade titanium.
In summary, titanium’s blend of strength, heat tolerance, and lightness makes it invaluable across many high-demand sectors.
Top Industrial Applications of Titanium
Titanium serves critical roles in several industries because of its superior strength, lightness, and corrosion resistance.
In aerospace, titanium alloys are used in airframes, engines, and landing gear. They withstand high stress and extreme temperatures.
The medical field values titanium for its biocompatibility. It’s commonly used in implants, prosthetics, and surgical tools. Titanium rarely causes adverse reactions, making it safe for long-term use in the human body. One notable example is the rise of 3D-printed titanium wrist implants.
In the automotive world, titanium is found in high-performance vehicles. It’s used in exhaust systems and structural parts to cut down on weight without sacrificing strength. This supports better fuel efficiency and helps meet environmental standards.
Across all these industries, ongoing innovation ensures titanium’s continued growth and relevance.
Titanium vs Other Metals: A Performance Comparison
Titanium beats aluminum and rivals steel when it comes to strength-to-weight ratio. It also resists corrosion far better than either.
Steel, though strong, is prone to rust. Titanium’s oxide layer offers built-in protection. Aluminum is lightweight but lacks the durability and heat resistance of titanium.
These factors make titanium a top choice for high-performance and high-stakes applications. Forged titanium parts, made through detailed processes, ensure both strength and precision.
The recent titanium shortages caused by geopolitical tensions highlight the need for flexible sourcing strategies. A stable titanium supply is crucial to keep modern manufacturing running smoothly.
Biomedical Engineering: Evaluating Titanium in Healthcare
Titanium’s ability to work well with the human body, combined with its strength and durability, makes it ideal for medical applications.
It’s commonly used in dental implants, joint replacements, and surgical instruments. Its smooth integration with bone and tissue ensures long-lasting results and minimal complications.
Titanium alloys offer advantages over other metals. Their porous structure supports cell growth, which is essential in scaffolds for tissue regeneration.
The FDA stresses the importance of chemical characterization in medical device testing. Titanium meets these standards with minimal toxicity and strong biochemical compatibility.
New technologies like 3D printing are also expanding its role in medicine. Today, we see 3D-printed blood vessels and custom implants moving closer to reality.
As Dr. Alexei Mlodinow noted, advancements in titanium-based medical research are helping improve care for patients undergoing life-changing procedures, such as mastectomies.
In short, titanium plays a vital role in advancing biomedical engineering and improving patient outcomes.
Conclusion: Why Evaluating Titanium Matters for the Future
Titanium’s outstanding qualities—strength, low weight, and corrosion resistance—make it a key material in aerospace, automotive, medical, and industrial engineering.
Its high strength-to-weight ratio offers performance without excess weight. This is critical in industries where efficiency is everything.
Technological advances, including 3D printing, are expanding how titanium is used, especially in healthcare. Meanwhile, global supply chain issues underline the need for smart procurement and sourcing strategies.
Evaluating titanium confirms its continued relevance and growing value. As industries evolve, titanium will remain a crucial building block for the future of innovation and engineering.