Blogs
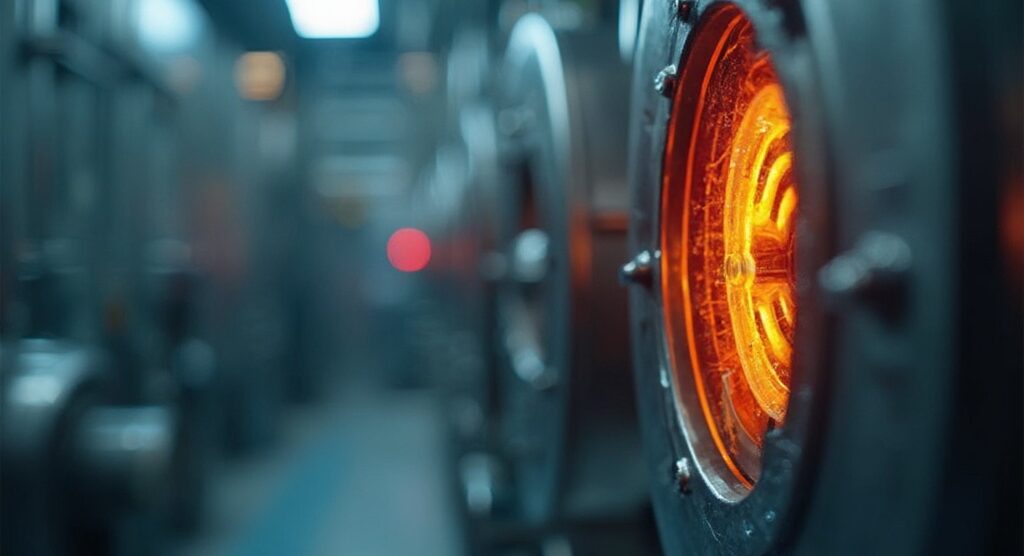
Innovative Uses of Hi Temp Alloys in Modern Industry
Introduction
High-performance alloys have become the backbone of numerous industries, known for their exceptional strength, stability, and resistance to oxidation and corrosion under extreme conditions. Incorporating elements like nickel, cobalt, and titanium, these alloys maintain their mechanical properties at high temperatures, making them crucial for applications in challenging environments. From fossil fuel power stations to nuclear plants and aerospace technology, the durability and resilience of these materials are indispensable.
As industries push the boundaries of what’s possible in extreme environments, the demand for innovative high-temperature alloys continues to grow, driving advancements in efficiency and sustainability.
Properties and Applications of High Temperature Alloys
High-performance materials are carefully designed to withstand severe conditions, characterized by their remarkable strength, stability, and resistance to oxidation and corrosion. These metal mixtures, often incorporating nickel, cobalt, or titanium, are designed to retain their mechanical properties even at elevated temperatures, making them indispensable for applications in challenging environments. For example, while traditional mixtures like steel melt at approximately 2,500 degrees Fahrenheit and aluminum deteriorates when subjected to moisture and oxygen, high-performance materials preserve their integrity under such harsh conditions.
Multi-principal element materials (MPEMs), composed of several components in approximately equal amounts, display remarkable strength, hardness, and toughness across a broad spectrum of temperatures, rendering them especially appropriate for application in extreme settings like outer space and the Arctic. Peas also offer excellent corrosion resistance and thermal stability, alongside unique functional properties beneficial for electronic and magnetic devices.
In various industrial applications, these high-performance materials play crucial roles. For instance, in fossil fuel power plants, nickel-based substances are selected for their excellent corrosion and heat resistance, improving the longevity of boilers and heat exchangers. In nuclear power facilities, nickel materials are crucial in both heat transfer and cooling systems, as well as in containers for radioactive waste. Titanium, known for its exceptional strength-to-weight ratio, high melting point, and excellent chemical resistance, is widely used in aerospace, automotive, medical, and marine industries.
The continuous development and application of these advanced materials are vital to solving complex problems and improving efficiency and performance across multiple sectors. As the requirement for procedures in harsh surroundings increases, so does the demand for materials that can endure such situations, ensuring both performance and durability.
High Temperature Alloys in Aerospace Industry
The aerospace sector relies heavily on high-temperature materials for essential parts like turbine blades and exhaust systems, which endure intense heat and pressure. These mixtures are indispensable for maintaining safety and efficiency in aircraft engines, where materials must consistently perform under harsh conditions. Advanced super materials, known for their exceptional resistance to creep and fatigue, play a crucial role in jet engines and rocket propulsion systems, facilitating the development of more fuel-efficient and powerful aircraft.
At around 2,500 degrees Fahrenheit, steel melts, and aluminum corrodes when exposed to moisture and oxygen. While traditional metal mixtures are suitable for everyday environments, they fail under extreme conditions, such as those in space or the Arctic. This requires materials that maintain their strength under such circumstances. Multi-principal element alloys (MPEAs), consisting of several elements in equal proportions, are better suited for these environments due to their high strength, hardness, and toughness across a range of temperatures. They also demonstrate outstanding corrosion resistance and thermal stability, making them perfect for aerospace uses.
Research from the Johns Hopkins Applied Physics Laboratory (APL) is accelerating the design of MPEAs by creating complex microstructures that provide detailed composition information from minimal samples. This innovation is crucial as the aerospace sector increasingly operates in more extreme environments, necessitating materials that can withstand such rigorous conditions. Cooperation among researchers and engineers worldwide is essential to promote the use and acceptance of these high-performance materials, guaranteeing the progress of safer, more efficient aerospace technologies.
High Temperature Alloys in Energy and Power Generation
High temperature materials are essential in the energy sector, particularly in the generation of electricity and renewable energy systems. These advanced materials are crucial in the operation of gas turbines, nuclear reactors, and heat exchangers. Their superior ability to withstand high thermal loads and corrosive environments significantly enhances the efficiency and reliability of power generation technologies. This is particularly vital for combined cycle and concentrated solar power plants, where operational efficiency is paramount.
The advancement of high-entropy materials (HEAs) has further transformed the industry. Comprising five or more elements in near-equal amounts, HEAs exhibit unique properties such as exceptional strength, toughness, and corrosion resistance. Recent research highlights their impressive fatigue behavior, which is critical for industrial applications subjected to high-cycle and low-cycle fatigue, fatigue-crack growth, and other stressors.
As the U.S. aims for net-zero emissions by 2050, the role of high temperature alloys in advancing high-impact energy technologies cannot be overstated. These resources will be central to the decarbonization efforts, enabling a shift from fossil fuels to more sustainable energy solutions, including hydrogen turbines. Collaborative efforts between scientists and engineers are essential to drive the adoption and widespread application of these innovative materials, ensuring they meet the rigorous demands of modern energy systems.
Furthermore, the advancement of high-temperature heat storage systems, capable of retaining heat at over 700 °C using renewable electricity, demonstrates the potential of these materials in facilitating resource-intensive production processes. These systems assist in preserving production consistency during times of varying renewable energy availability, further highlighting the significance of high temperature materials in attaining a sustainable energy future.
Technological Innovations in High Temperature Alloy Production
Recent advancements in manufacturing techniques, such as additive manufacturing and advanced casting processes, have revolutionized the production of high-temperature alloys. Additive manufacturing, also known as 3D printing, allows for precise control over complex geometries and material properties. According to a study by Baldur Steingrimsson et al., the optimization of additive manufacturing parameters through multi-dimensional functions can significantly enhance the quality of components made from superalloys like Inconel 718. This technology enables the creation of lighter and stronger components, which are crucial for modern industrial applications.
Advanced casting processes are also making significant strides. Dr. Griffiths’ research, funded by the Engineering and Physical Sciences Research Council (EPSRC), aims to develop an accurate model for the behavior of oxidized surfaces in melted metal flows. This research could lead to a better understanding of the encapsulation process, improving the mechanical properties of cast components.
Continuous investigation into new metal mixtures is another essential field of progress. For example, the advancement of high-strength magnesium compositions, which are lighter and stronger than conventional substances such as aluminum and iron, is anticipated to enhance fuel efficiency in automotive and aircraft parts. This innovation not only minimizes resource waste but also removes the use of harmful greenhouse gases, significantly reducing environmental impact.
The combination of these advancements is paving the way for broader applications of high-temperature alloys. As Morgan Trexler from APL’s Science of Extreme and Multifunctional Materials program noted, the ability to predict the microstructure and mechanical properties of printed components before manufacturing is key to the success of additive manufacturing. This predictive capability will accelerate the development of new materials, ensuring they meet the stringent performance demands of extreme environments, such as space and the Arctic.
Conclusion
High-performance alloys are essential across various industries, particularly in environments that demand exceptional strength and resilience. Their unique properties, including stability and resistance to oxidation and corrosion, make them indispensable in sectors such as aerospace and energy production. Alloys containing nickel, cobalt, and titanium are designed to maintain their mechanical integrity at elevated temperatures, addressing the growing need for efficiency and sustainability.
In aerospace, these alloys are critical for components like turbine blades and exhaust systems, where they ensure safety and performance under extreme conditions. Advanced super alloys and multi-principal element alloys (MPEAs) enhance the efficiency of aircraft engines, while ongoing research promotes collaboration among experts to further innovate these materials.
In the energy sector, high-temperature alloys improve the efficiency and reliability of technologies such as gas turbines and nuclear reactors. The emergence of high-entropy alloys (HEAs) provides unique properties that support the shift toward sustainable energy solutions, essential for meeting net-zero emissions goals.
Innovations in manufacturing, including additive manufacturing and advanced casting techniques, are transforming the production of high-temperature alloys. These advancements enable the creation of lighter and stronger components that fulfill the demanding requirements of modern applications. As research into new alloy compositions progresses, high-performance alloys will continue to play a vital role in driving efficiency and sustainability across industries, ensuring they are well-equipped to tackle future challenges in extreme environments.