Blogs
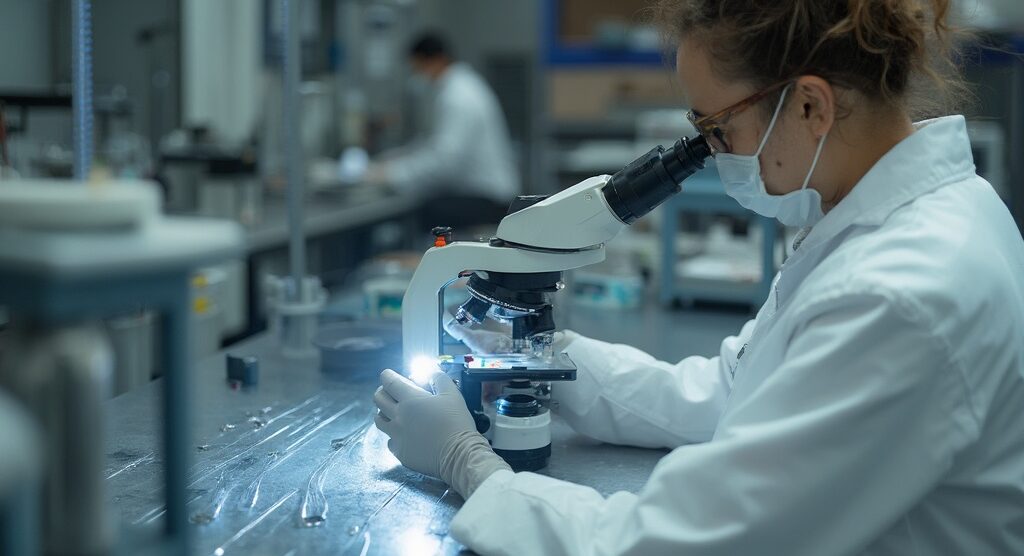
Microstructural Analysis and Applications of Invar 36 Alloy
Introduction
Invar 36, an iron-nickel alloy, is renowned for its unparalleled dimensional stability across varying temperatures, making it a cornerstone in applications requiring precise measurements. Comprising 36% nickel and 64% iron, this alloy retains its mechanical properties even under elevated temperatures, crucial for use in demanding environments. Its low coefficient of thermal expansion is exceptionally beneficial in fields necessitating minimal thermal deformation, such as opto-semiconductor line sensors, where high spatial resolution and stability are essential.
The material’s magnetic properties, maintaining ferromagnetism up to its Curie temperature, further enhance its utility in electronic applications, including sensor ICs with minimal height constraints. These attributes facilitate the integration of ultra-thin components, showcasing the alloy’s versatility. The consistency of Invar 36 under varying conditions is perfectly aligned with the advancements in additive manufacturing technologies, ensuring precise material behavior vital for innovative manufacturing techniques.
Properties and Characteristics of Invar 36
The iron-nickel alloy 36 is greatly appreciated for its outstanding dimensional stability over different temperatures, rendering it essential in contexts requiring accurate measurements. ‘Usually consisting of 36% nickel and 64% iron, this alloy preserves its mechanical characteristics even at high temperatures, which is essential for uses in challenging environments.’. Its low coefficient of thermal expansion is particularly beneficial in fields requiring minimal thermal deformation, such as in opto-semiconductor line sensors, where high spatial resolution and stability are paramount.
Invar 36’s magnetic characteristics are also important; it stays ferromagnetic up to its Curie temperature, increasing its usefulness in particular electronic applications such as those involving sensor ICs with minimal height restrictions. These magnetic characteristics promote the incorporation of ultra-thin components in diverse surfaces, showcasing the substance’s adaptability. The alloy’s ability to retain its properties under varying conditions aligns with the advancements in additive manufacturing technologies, where precise material behavior is crucial for the successful implementation of new manufacturing techniques.
Microstructural Analysis of Invar 36 Alloy
The alloy 36 features a distinctive face-centered cubic (FCC) lattice structure that underpins its exceptional thermal expansion characteristics. Utilizing advanced techniques such as scanning electron microscopy (SEM) and transmission electron microscopy (TEM), researchers have meticulously studied the role of nickel content in influencing grain size and morphology. These investigations highlight that the microstructure of a specific alloy can vary significantly depending on the processing methods employed, such as quenching and annealing. These processes play a crucial role in determining the alloy’s mechanical strength and thermal stability. For instance, during quenching, the rapid cooling can enhance the mechanical properties by refining the grain structure, whereas annealing can improve thermal stability by relieving internal stresses. These findings are essential for customizing the alloy to meet specific application requirements, particularly in sectors demanding high precision and stability under varying thermal conditions.
Applications of Invar 36 Alloy
The alloy 36 showcases exceptional dimensional stability across various industries. This alloy is indispensable in precision instruments, such as measuring devices, clocks, and scientific apparatus, where temperature fluctuations can significantly impact measurement accuracy. The aerospace industry also depends significantly on alloy 36 for parts needing steady performance under different thermal conditions. Furthermore, optical instruments gain from the stability of this material, guaranteeing accurate alignment and performance. Significantly, this alloy is essential in cryogenic settings, preserving structural integrity at very low temperatures, which is vital for uses in scientific inquiry and technology. This alloy’s versatility underscores its importance in modern engineering and manufacturing, aligning with the industry’s drive for precision and reliability.
Challenges and Limitations of Invar 36 Alloy
Invar 36, while acclaimed for its low thermal expansion characteristics, presents certain challenges that must be addressed for optimal use. Its susceptibility to corrosion in specific environments necessitates the application of surface treatments or protective coatings. The high nickel content, critical for maintaining its unique properties, can lead to increased costs and complicate welding processes. Specialized welding methods are frequently necessary to guarantee joint integrity, a point emphasized by industry specialists concentrating on the future advancement and challenges of welding various substances. As noted by Andrew Coleman, Head of Additive Manufacturing at Sandvik, advancements in materials and manufacturing technology are essential to overcome these hurdles and enhance customer benefits. Tackling these challenges is essential for maximizing the full potential of alloy 36 across numerous applications, from automotive to aerospace, where durability and precision are crucial.
Enhancing Strength and Hardness of Invar 36
Enhancing the strength and hardness of Invar 36 can be achieved through alloying with elements such as chromium or molybdenum. These additives not only enhance the substance’s mechanical properties but also maintain its unique low thermal expansion characteristics. Moreover, specific heat treatment processes like aging and solution treatment can be employed to refine the alloy’s microstructure. For instance, during press hardening, boron steel blanks are heated to high temperatures and then rapidly cooled, transforming the material into ultra-high-strength steel with exceptional stability. ‘This technique enables the creation of intricate forms with excellent dimensional precision, which can be utilized on a specific alloy to make it appropriate for more challenging applications.’.
Manufacturing Techniques for Invar 36 Components
Producing alloy 36 parts entails sophisticated methods such as casting, precision machining, and additive manufacturing. Precision machining is crucial for achieving the tight tolerances required in sectors like metrology and aerospace. Recent advancements in additive manufacturing have revolutionized the production of complex geometries with Invar 36. This innovation not only enables more intricate designs but also utilizes the unique characteristics of the substance.
A prime example of additive manufacturing’s impact is its application in large format productions. Industries such as automotive and construction benefit from the ability to create large, complex parts efficiently. However, challenges like material warpage during printing need to be managed to ensure high-quality outcomes.
Further, the integration of advanced analytics and IoT platforms into the manufacturing process enhances real-time decision-making and predictive maintenance. This comprehensive method, as observed in firms such as Flex, enhances the manufacturing ecosystem and guarantees the dependability and performance of 36 components.
Future Perspectives and Research Directions
Ongoing research into Invar 36 is advancing through innovative alloying techniques and processing methods, aiming to enhance its properties and explore new applications. This interdisciplinary project, backed by the Naval Nuclear Laboratory, the Scott Institute for Energy Innovation, and the Army Research Laboratory, combines processing, simulation, and characterization to create substances capable of withstanding extreme temperatures. Seven doctoral students and postdoctoral researchers contribute to this work, using data curated by Professor John Kitchin to perform integrated computational engineering simulations. These simulations, paired with generative AI, investigate the design space effectively, decreasing the time required for new substance development.
In the additive manufacturing laboratory at Mill 19, Professor Bryan Webler employs laser powder bed fusion and powder-feed direct energy deposition methods to create these alloys. This research is especially important as the need for lightweight and long-lasting substances increases across industries such as automotive, aerospace, and construction. Innovations in hybrid substances that combine Invar 36 with other advanced alloys are particularly promising, expanding its application range in high-tech industries. With the continuous evolution of performance requirements, these advancements are poised to meet the increasing demand for efficient and sustainable materials.
Conclusion
Invar 36 stands out as a crucial material in various industries due to its exceptional dimensional stability and low thermal expansion properties. Its unique composition, primarily of 36% nickel and 64% iron, enables it to maintain mechanical integrity even in demanding thermal environments. This characteristic is particularly vital in applications such as opto-semiconductor line sensors and precision instruments, where measurement accuracy is paramount.
The microstructural characteristics of Invar 36, influenced by processing methods like quenching and annealing, further enhance its mechanical strength and thermal stability. Understanding these properties allows for tailored applications in sectors that demand high precision and reliability, including aerospace and optical devices. However, challenges such as corrosion susceptibility and increased costs associated with high nickel content must be addressed to maximize the alloy’s potential.
Advancements in manufacturing techniques, particularly additive manufacturing, are revolutionizing how Invar 36 components are produced. These innovations not only facilitate the creation of complex geometries but also ensure the material’s unique properties are effectively utilized. Ongoing research into alloying techniques and processing methods promises to enhance Invar 36’s capabilities, expanding its applications in high-tech industries.
In summary, Invar 36’s remarkable stability, combined with continued research and advancements in manufacturing technologies, positions it as a vital material for the future. Its ability to meet the demands of various applications underscores the importance of strategic procurement and investment in this versatile alloy, ensuring that industries can rely on its performance and durability in an ever-evolving landscape.