Blogs
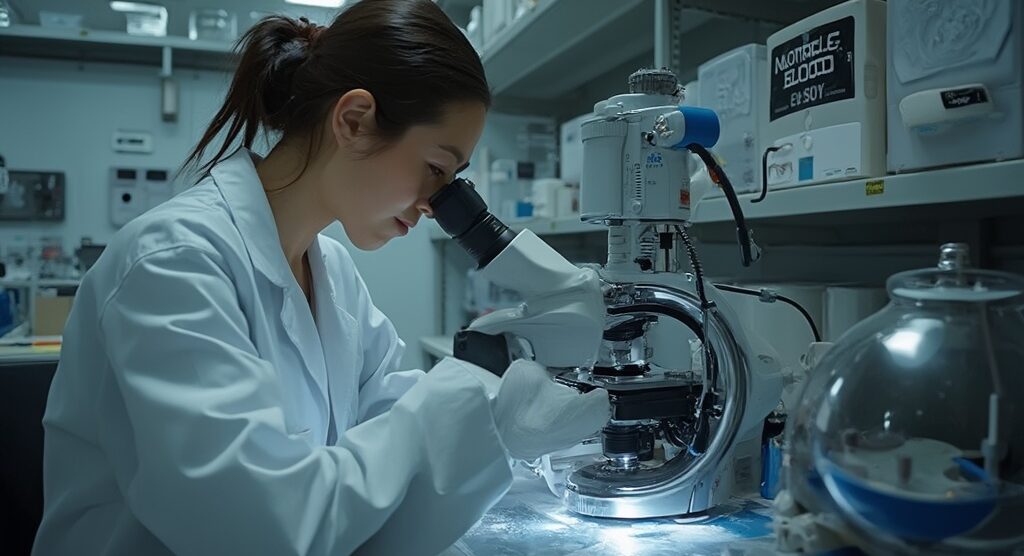
What Is Monel Alloy? A Detailed Overview of Composition and Uses
Introduction
In the realm of advanced materials, Monel alloys stand out as a vital component across diverse industries, renowned for their exceptional strength and remarkable resistance to corrosion. Comprising primarily nickel and copper, these alloys are engineered to thrive in harsh environments, making them indispensable in sectors ranging from marine engineering to aerospace.
As procurement managers navigate the complexities of material selection, understanding the unique characteristics, applications, and limitations of Monel becomes paramount. This article delves into the defining traits of Monel alloys, exploring their composition, mechanical properties, and the strategic advantages they offer in various applications, while also addressing the challenges that may arise in their use.
By equipping decision-makers with expert insights, this comprehensive overview aims to facilitate informed choices that align with both performance requirements and budget considerations.
Defining Monel Alloy: Characteristics and Composition
This alloy, known for its unique properties, is what is monel alloy, primarily composed of approximately 63% nickel and 28% copper. Renowned for its exceptional strength and ability to withstand corrosion, what is monel alloy known for is its remarkable durability in challenging environments. Its significant durability against seawater, acids, and alkaline solutions makes it the preferred material for uses in marine environments, which leads to the question of what is monel alloy, as demonstrated by its implementation in the first major roofing installation at Pennsylvania Railroad Station in New York City in 1909, projected to endure for up to 300 years.
Furthermore, Domadia provides a diverse selection of copper nickel blends, including those with different levels of corrosion resistance and conductivity, perfect for numerous uses such as marine engineering and electronics. Our extensive product catalog ensures that procurement managers can find the perfect solution for their project needs. The material’s capacity to endure elevated temperatures and pressures broadens its applicability across industries, particularly in chemical processing.
For instance, nickel-chromium-molybdenum mixtures, which contain 45–60% nickel, are mainly utilized in the chemical processing sector, with the Hastelloy C series demonstrating effectiveness in high-temperature uses. The challenges of using this material are emphasized by a quote from The New York Times, stating that ‘the yacht’s steel skeleton deteriorated due to electrolytic interaction with it.’ Recent advancements suggest that chromium-containing materials are favored for oxidizing circumstances, whereas nickel and its compounds thrive in reducing settings, further emphasizing the strategic significance of this metal in both marine and chemical uses.
Additionally, for high-temperature resistance and electrical insulation needs, our Mica Tape products, which offer excellent flame resistance and dielectric strength, are indispensable in critical applications across various sectors.
Exploring the Composition of Monel Alloys: Key Elements and Their Roles
Nickel-copper mixtures, known as what is monel alloy, are mainly made up of nickel and copper, along with trace elements like iron, manganese, carbon, and silicon. When considering what is monel alloy, Alloy 400, the most prevalent variant, comprises approximately 66% nickel and 30% copper, with minimal amounts of iron and manganese. This unique composition of what is monel alloy imparts exceptional resistance to corrosion, while the copper content significantly enhances its strength and machinability.
Notably, the hardness for hot worked or solution-annealed alloy 400 reaches a minimum of 552 MPa, showcasing its robust mechanical properties even under extreme conditions. Variations in composition enable the creation of different grades of this alloy, including what is monel alloy, which is specifically designed for a range of applications such as:
- Marine engineering
- Chemical processing
- Hydrocarbon processing
- Heat exchangers
- Valves
- Pumps
Furthermore, certain metal mixtures are employed in transfer piping from oil refinery crude columns, uranium refining facilities, and in pumps and valves for producing perchlorethylene and chlorinated plastics.
Expert insights from Alloy Wire International affirm this versatility, stating,
Monel® 400 is known to be suitable for marine engineering, chemical processing, hydrocarbon processing, heat exchangers, valves, and pumps.
Furthermore, alloy 400 retains good mechanical properties from sub-zero temperatures to 549°C, making it suitable for critical aerospace components like fuel tanks and exhaust systems, demonstrating its adaptability in environments where durability and resistance to harsh conditions are essential.
Mechanical and Physical Properties of Monel: Why It Matters
These metal mixtures are distinguished by their impressive mechanical properties, characterized by high tensile strength and excellent ductility. Notably, these alloys can endure temperatures reaching up to 1000°F (538°C) without compromising structural integrity, positioning them as a go-to choice for high-temperature applications. The density of the alloy is recorded at 8.80 g/cm³, a factor that contributes to its overall mechanical performance.
Additionally, this material exhibits low thermal expansion and high thermal conductivity, enhancing its utility across various engineering domains. Significantly, these metal mixtures are slightly magnetic at room temperature, which can affect their use in specific settings. For example, The New York Times covered the decline of a yacht’s steel framework due to electrolytic interaction with a specific metal, highlighting its implications in practical situations.
In addition to Model, non-sparking tools represent an essential alternative in explosive potential environments, ensuring safety and compliance. Furthermore, copper nickel alloys offer significant advantages over stainless steel, particularly in marine engineering, automotive systems, electronics, heat exchangers, and coinage, due to their excellent corrosion resistance and durability. Common applications include:
- Ship hulls
- Offshore platforms
- Seawater piping systems
These applications highlight their versatility.
The characteristics of Alloy 400, which features a density of 0.319 lb/in³ and a modulus of elasticity of 26.0 X 10^6 psi, underscore its capacity for stable performance under varied conditions. When contrasted with other metal mixtures, this nickel-copper combination’s mechanical characteristics, along with the strategic application of non-sparking instruments and copper-nickel mixtures, offer essential solutions for modern engineering challenges where dependability and performance are crucial. For procurement managers, pinpointing trustworthy suppliers and producers of non-sparking tools and copper nickel mixtures is essential for guaranteeing quality and adherence in these areas.
Applications of Monel Alloys: From Marine to Aerospace
Certain alloys, including what is monel alloy, are recognized for their remarkable properties, making them indispensable across multiple industries. In the marine industry, understanding what is monel alloy is essential as it is widely used for ship construction and underwater uses, especially in parts like propeller shafts and valves, due to its remarkable resistance to seawater corrosion. The industrial importance of this alloy, specifically what is monel alloy, is demonstrated by its use in aerospace, where it is preferred for aircraft parts and structures that require high strength and resilience under extreme conditions.
Recent advancements in the use of this alloy highlight what is monel alloy, which extends to chemical processing and oil and gas sectors, as well as in the food industry, where equipment must withstand harsh conditions. Shafiq Ahmad’s research highlights the innovative applications of 400 alloy, particularly in milling microchannels through wire EDM techniques, showcasing the material’s versatility and efficiency in real-world scenarios. His findings, published in Micromachines, emphasize the practical implications of alloy 400 in modern manufacturing processes.
Furthermore, the research was backed by funding from the Deanship of Scientific Research at King Saud University, highlighting the academic and industrial collaboration in investigating the material’s capabilities. Continuous advancements in machine learning and optimization methods, including Multi-objective Particle Swarm Optimization (MOPSO), are improving the performance and use of these materials. MOPSO demonstrates effective convergence speed and optimization capabilities, successfully estimating values for surface roughness, tool wear, and material removal rate (MRR) in machining processes, further solidifying Monel’s position in contemporary engineering solutions.
Advantages and Limitations of Monel Alloys: A Comprehensive Overview
These alloys are renowned for their exceptional corrosion resistance, high strength, and durability, which make them particularly well-suited for demanding industrial applications. Their ability to withstand harsh environments is often unmatched, providing a strategic advantage in sectors such as marine and chemical processing. Notably, 316 stainless steel is frequently compared to another alloy due to its similar properties, making it a popular choice in various industries.
However, procurement managers must also consider the limitations associated with that material. The cost of certain alloys tends to be higher than that of alternatives like stainless steel, which can impact budgetary constraints. Additionally, the toughness of this alloy can present challenges during machining, necessitating specialized tools and techniques.
As Kat de Naoum, a noted writer and content specialist, observes,
It’s also not as readily available as some other materials, so you might find yourself struggling to get a hold of some.
This scarcity, coupled with the need for careful machining, can complicate procurement decisions. Furthermore, it’s important to note that stainless steel hardness ranges from 28 to 40 HRC, which provides a point of comparison for the mechanical properties between these materials.
The recent anti-dumping ruling in India concerning welded stainless pipes from Thailand and Vietnam also provides a timely context that may influence procurement choices related to nickel alloys and stainless steel. Therefore, it is essential for procurement managers to thoroughly evaluate what is monel alloy along with its advantages and limitations, ensuring that they select the most appropriate material based on specific application requirements and cost considerations.
Conclusion
Monel alloys are integral to a multitude of industries due to their unique characteristics, including exceptional strength and corrosion resistance. Comprising primarily nickel and copper, these alloys excel in harsh environments, making them particularly valuable in:
- Marine engineering
- Aerospace
- Chemical processing
Their remarkable durability is evidenced by historical applications, such as the long-lasting roofing at Pennsylvania Railroad Station, which highlights Monel’s ability to withstand the test of time.
The mechanical and physical properties of Monel, including high tensile strength, low thermal expansion, and good performance at elevated temperatures, further underscore its versatility. However, while Monel offers numerous advantages, such as superior corrosion resistance, it also presents challenges, including:
- Higher costs
- Machining difficulties
These factors necessitate a careful evaluation during the procurement process, ensuring that decision-makers select the most suitable materials for their specific needs.
Ultimately, understanding the defining traits, applications, and limitations of Monel alloys empowers procurement managers to make informed choices that align with both performance requirements and budgetary constraints. As industries continue to evolve, the strategic use of Monel will remain a critical component in achieving reliable and efficient engineering solutions across diverse sectors.