Blogs
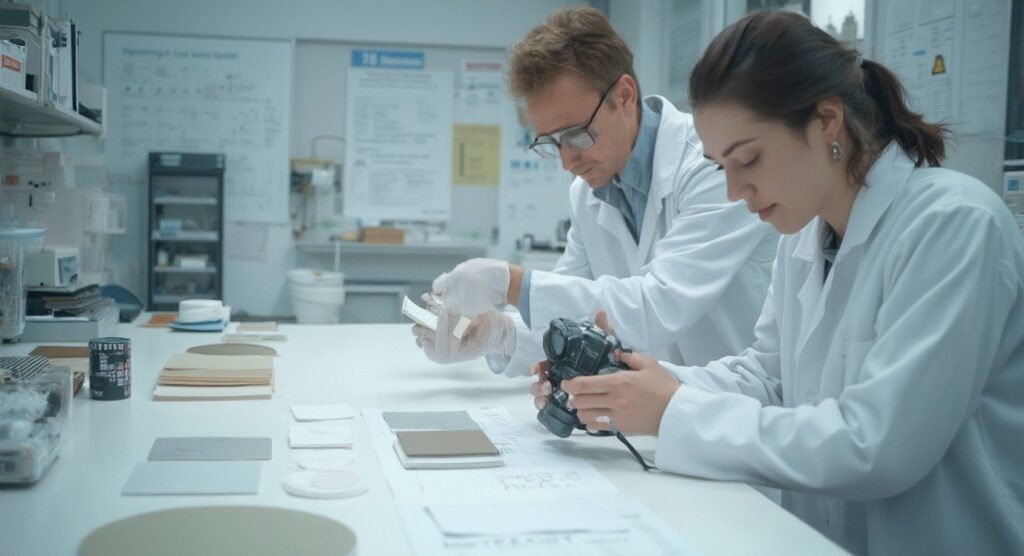
Understanding the Science of Lowest Coefficient of Friction Materials: A Complete Tutorial
Introduction
In the realm of engineering, the coefficient of friction (CoF) stands as a vital parameter that influences the performance and longevity of materials across various applications. Understanding this dimensionless value is not merely an academic exercise; it plays a crucial role in the selection of materials that can withstand demanding environments, from high-temperature settings to explosive atmospheres.
As industries increasingly rely on low-friction materials to enhance operational efficiency and safety, procurement professionals must navigate a complex landscape of factors, including:
- Surface properties
- Environmental conditions
- Advanced testing methodologies
This article delves into the fundamentals of CoF, explores the significance of low-friction materials, and examines the latest advancements in measurement techniques, providing invaluable insights for making informed procurement decisions that align with strategic engineering goals.
Understanding the Coefficient of Friction: Basics and Importance
The coefficient of friction (CoF) is a crucial metric in engineering, defined as the dimensionless value that expresses the ratio of the frictional force between two surfaces to the normal force pressing them together. This parameter is essential for understanding how substances behave under varying conditions, particularly in applications requiring precision and durability. For instance, in high-temperature environments, materials like Domadia’s Mica Tapes provide effective electrical insulation solutions, showcasing the importance of selecting materials that can withstand demanding conditions.
A lower CoF is often preferable, especially when using the lowest coefficient of friction materials, as it signifies reduced resistance, leading to enhanced operational efficiency, minimized wear, and prolonged lifespan of components. Recent tribological tests conducted on Duplex CRN/DLC and Nano-Multilayer DLC-W coatings demonstrated that the use of the lowest coefficient of friction materials can significantly influence results, as seen in the wear volumes and friction behavior observed under different loads and temperatures. Specifically, for an entry of 0.5 mm and an exit of 2300 mm, the speed was recorded at 6050 mm/s, with an average stress of 432.6655243 MPa, highlighting the performance under operational conditions.
Furthermore, environmental elements, such as temperature and humidity, can significantly influence the performance of the lowest coefficient of friction materials, making it essential for engineers and procurement professionals to take these variables into account when choosing resources. Furthermore, Non-Sparking Tools serve as a critical alternative for use in explosive environments, emphasizing safety and reliability. These tools prevent sparks that could ignite flammable substances, making them essential for industries such as oil and gas, mining, and chemical manufacturing.
As emphasized by Alaa M. Razzaq in the Encyclopedia of Smart Materials, comprehending the CoF is essential for making knowledgeable choices in substance selection and product design, particularly when selecting the lowest coefficient of friction materials, ultimately guiding the success of engineering endeavors. The case study on ‘Tribological Testing of Duplex CRN/DLC and Nano-Multilayer DLC-W Coatings‘ offers valuable insights into practical uses, demonstrating the critical role of the lowest coefficient of friction materials in enhancing the performance of engineering substances. To explore our range of Mica Tapes and learn more about how they can benefit your business, visit our website or contact our expert team today.
Exploring Low-Friction Materials: Key Examples and Applications
Low-friction substances, particularly the lowest coefficient of friction materials such as polytetrafluoroethylene (PTFE), widely recognized by its brand name Teflon, play an essential role in modern engineering. PTFE is renowned for its remarkable non-stick characteristics, which makes it one of the lowest coefficient of friction materials, ideal for uses such as bearings and seals. In addition to PTFE, thermoplastic elastomers, nylon, and acetal, which are notable for their durability and low wear rates, the lowest coefficient of friction materials are often utilized in gears and bushings.
The automotive sector, in particular, benefits from the use of lowest coefficient of friction materials as coatings on engine components, which can substantially enhance efficiency and fuel economy. This innovation is essential as the Friction Products Market is projected to grow at a CAGR of 4.4%, highlighting the increasing dependence on materials with the lowest coefficient of friction. Recent advancements, such as the mechanical milling of nanostructured Al 2024 alloy, have decreased grain size to less than 100 nm, resulting in increased strength, hardness, and wear resistance, which are essential for applications involving the lowest coefficient of friction materials.
Moreover, Solvay’s purchase of Cytec Industries and Mitsubishi Chemical’s purchase of Renegade Materials demonstrate the sector’s dedication to enhancing substance efficiency in critical applications. As mentioned by industry specialists,
- “Ensure your team analyzes data consistently with these strategies.”
- Use clear metrics
- Regular meetings
- Training to achieve alignment.
By utilizing the lowest coefficient of friction materials, engineers can achieve superior performance and reliability in their designs, with case studies like Solvay’s comprehensive aerospace plastics range showcasing the practical advantages of these components in advanced aerospace engineering.
Factors Affecting Friction: Surface Properties and Environmental Conditions
The coefficient of resistance (CoR) is influenced by several critical factors, including surface roughness, material hardness, and environmental conditions such as temperature and humidity. Research indicates that smoother surfaces typically yield lower resistance coefficients; however, a delicate balance must be maintained. Excessively smooth surfaces can result in unfavorable occurrences like adhesion or stick-slip behavior, which can undermine functionality.
Furthermore, lubrication plays a pivotal role in managing resistance. Specific lubricants have been demonstrated to greatly reduce resistance between interacting surfaces, rendering them crucial for optimal performance of substances. Recent advancements, such as a simpler indirect measurement strategy for assessing resistance forces via microscopy, highlight the evolving landscape of research in this field.
For instance, a study by Hou et al. on zinc oxide nanowires (ZnO NWS) demonstrates the impact of substrate characteristics on frictional behavior. Their findings revealed that NWS on natural graphite exhibited a constant frictional shear stress of 0.48 MPa, while on highly oriented pyrolytic graphite, the stress varied significantly with diameter, ranging from 0.25 to 2.78 MPa.
This highlights the significance of comprehending interactions of substances in various environments. Notably, the effectiveness of nano-multilayer DLC-W coatings has been statistically shown to be between 90–97%, highlighting a significant advancement in wear management technologies. As mentioned by Smrithi Padmakumar Deepthy Menon, ‘The engineering aspects of suture fabrication are crucial in optimizing substance selection for performance.’
As procurement experts navigate these complexities, understanding how surface characteristics and lubrication affect the lowest coefficient of friction materials is crucial for selecting substances that operate effectively under working conditions.
Measuring Friction: Testing Methods and Standards
Procurement managers must be knowledgeable about different techniques for evaluating the coefficient of resistance, as these assessments are essential for selection of substances. Two common techniques utilized in the industry are the Pin-On-Disk Test and the Inclined Plane Test. The Pin-On-Disk Test assesses frictional characteristics under controlled conditions, providing an accurate measurement of how substances act during interaction.
On the other hand, the Inclined Plane Test evaluates sliding resistance by positioning substances on an incline, offering insights into their performance in practical situations. Both methods are grounded in ASTM standards, which ensure that the results are reproducible and reliable across different tests and materials. ASTM International is located at 100 Barr Harbor Drive, PO Box C700, West Conshohocken, PA, 19428-2959 USA, reinforcing the authority of the standards applied.
Additionally, the Polywater Friction Table has been essential in comprehending resistance measurements, particularly for extended pulling distances and lower tensions with Polywater Pulling Lubricants. Information from this resistance table assists in planning and enhancing cable installations in conduits. As noted by Hongjun Cao,
In general, the development trend of coefficient measurement methods can be summarized as three characteristics: from simple to complex, from rough to precision, and from single function to platform integration.
This insight emphasizes the changing landscape of friction measurement, making it crucial for procurement managers to remain aware of current testing methodologies related to the lowest coefficient of friction materials, such as those showcased in recent videos, to verify performance and adherence to industry standards before making purchasing decisions.
Applications of Low-Friction Materials Across Industries
The use of the lowest coefficient of friction materials is becoming increasingly crucial across various sectors, including automotive, aerospace, medical devices, and electronics. Within the automotive industry, these substances are essential to components such as piston rings and bearings, where they significantly enhance efficiency and contribute to emissions reduction. In aerospace sectors, low-friction substances are vital for enhancing aircraft design by reducing drag, thus boosting fuel efficiency—an element that is critical as the industry expects around 8,700 new deliveries in China by 2040, with a market service value estimated at USD 1,800 billion.
The medical field also benefits from low-friction coatings applied to surgical instruments, which reduce tissue damage during procedures, thereby improving patient outcomes. Furthermore, the use of DOMADIA Oxygen Free Copper (OFE/OHFC) in critical medical components ensures reliability and performance in high-stakes environments due to its excellent conductivity and resistance to corrosion, which are vital for maintaining the integrity of medical devices. In addition, non-sparking tools are vital in explosive potential environments, as they are specifically designed to prevent ignition sources during maintenance and assembly tasks, thereby ensuring safety in hazardous settings.
Staying informed about these applications enables procurement managers to strategically choose resources that not only fulfill specific operational requirements but also correspond with current industry trends, such as the increasing demand for lightweight and high-performance substances in electric and hybrid vehicles. Furthermore, the market for vehicle components is evolving, with key trends including the adoption of lightweight substances and regenerative braking systems. Insights from automotive engineers highlight the critical role that the lowest coefficient of friction materials play in enhancing vehicle performance and lowering emissions, making it imperative for industry stakeholders to consider these materials in their procurement strategies.
The anticipated growth rate of 4.6% for the Middle East and Africa underscores the expanding market opportunities in this sector.
Conclusion
Understanding the coefficient of friction (CoF) is essential for making informed material selections that enhance performance and safety across various engineering applications. The exploration of CoF reveals its critical role in determining how materials interact under diverse conditions, emphasizing the need for procurement professionals to consider:
- Surface properties
- Environmental factors
- Advanced testing methodologies
The advancements in low-friction materials, from PTFE to innovative coatings, demonstrate their significant impact on:
- Operational efficiency
- Durability
- Ultimately, the success of engineering projects
As industries increasingly prioritize low-friction solutions, the implications of these materials extend beyond mere performance enhancements. They play a vital role in:
- Meeting regulatory standards
- Improving safety in hazardous environments
- Driving innovation in sectors such as automotive, aerospace, and healthcare
By leveraging insights from recent tribological studies and understanding the evolving landscape of friction measurement techniques, procurement managers can align their strategies with industry advancements to optimize material selection.
In conclusion, a thorough grasp of the coefficient of friction and its influencing factors is indispensable for procurement professionals aiming to enhance engineering outcomes. By prioritizing low-friction materials and adopting strategic testing methods, organizations can not only improve their product performance but also position themselves competitively in a rapidly evolving market. The future of engineering relies on these informed decisions, ensuring that materials not only meet but exceed the expectations of modern applications.