Blogs
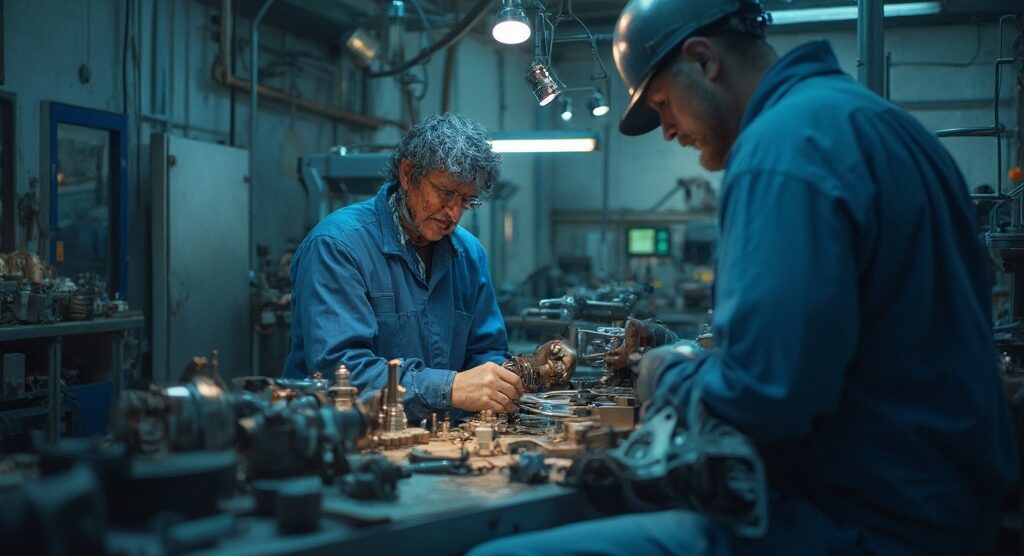
Understanding Alloys Nickel: A Complete Tutorial on Types and Applications
Introduction
Nickel alloys are at the forefront of modern engineering, combining unique properties that cater to the demanding needs of various industries. These materials, celebrated for their remarkable corrosion resistance, strength, and ability to withstand extreme temperatures, play a crucial role in applications ranging from aerospace to renewable energy.
As the global demand for nickel alloys surges, driven by advancements in electric vehicles and sustainable practices, procurement managers must navigate a complex landscape of materials and suppliers. Understanding the intricacies of nickel alloys, including their classifications, applications, and the challenges associated with their processing, is essential for making informed sourcing decisions that align with both operational requirements and industry standards.
This article delves into the essential characteristics of nickel alloys, their diverse applications, and the strategic considerations for procurement professionals in an evolving market.
Introduction to Nickel Alloys: Definitions and Characteristics
These composites are designed substances that merge various elements to enhance particular mechanical and physical properties. Renowned for their exceptional corrosion resistance, alloys nickel also exhibit impressive strength and heat resistance, rendering them ideal for challenging environments, including those with explosive potential. In such environments, the use of Non-Sparking Tools, which are specifically designed to prevent sparks during operation, becomes vital to ensure safety and avoid ignition risks when handling these materials.
These tools are typically made from materials such as brass or bronze, which do not produce sparks when struck against harder surfaces. Understanding the characteristics of these tools is crucial for ensuring safety in explosive environments. Alloys nickel are categorized based on their elemental composition; for instance, iron-nickel combinations, such as Invar, are prized for their stability at varying temperatures, while nickel-copper blends like Monel are favored for their resistance to seawater corrosion.
Comprehending these intrinsic traits is essential for choosing the suitable material for particular uses, especially in vital industries like aerospace and electronics, where performance and reliability are of utmost importance. Approximately 750,000 jobs rely directly or indirectly on this metal, underscoring the economic significance of this industry. With the increasing demand for alloys nickel driven by advancements in electric vehicles and renewable energy storage, as noted by Roskill Pariser, procurement managers must stay informed about the latest developments and innovations in this field to make strategic sourcing decisions.
Emerging trends in the nickel market suggest a notable rise in demand for alloys nickel in the electric vehicle sector and an emphasis on sustainable mining methods, which are predicted to influence the future of nickel technology. Furthermore, it’s crucial for procurement managers to take into account suppliers and manufacturers that focus on electrical insulation and high-temperature substances, like [Supplier A] and [Supplier B], ensuring a thorough strategy for sourcing in safety-critical contexts.
Exploring Different Types of Nickel Alloys: From Iron-Nickel to Specialty Alloys
Nickel combinations are essential materials in various industries, and they can be classified into several distinct categories, each with unique properties and applications:
Iron-Nickel Compositions: These materials, exemplified by Invar, exhibit minimal thermal expansion, making them particularly valuable in precision instruments where dimensional stability is crucial. The ability to maintain performance under varying temperature conditions underscores their importance in high-precision engineering. According to market research, the demand for iron-nickel mixtures in precision instruments has been steadily increasing, reflecting their critical role in high-tech applications.
Nickel-Copper Mixtures: Model, a notable nickel-copper mixture, stands out for its remarkable resistance to corrosion, especially in marine environments. This characteristic makes it an ideal choice for applications involving seawater, where durability and reliability are paramount. Recent case studies have shown that Monel materials are increasingly utilized in marine hardware, highlighting their effectiveness in harsh conditions.
Nickel-Chromium Alloys: Alloys such as Hastelloy are recognized for their exceptional high-temperature performance, which is vital in chemical processing industries. Their ability to withstand extreme conditions while maintaining integrity makes them indispensable in manufacturing processes that involve aggressive chemicals. Insights from metallurgists suggest that the market for alloys nickel, including nickel-chromium mixtures, is expanding as industries seek materials that can endure rigorous processing environments.
Specialty Materials: These materials are designed for specific applications and often incorporate additional elements like titanium or molybdenum. This customization improves their performance in niche markets, addressing specialized needs that standard materials may not satisfy. The growing trend towards customized solutions in various sectors is driving demand for these specialty alloys.
Understanding these categories is essential for procurement managers, as it enables them to make informed decisions about material selection that align with project requirements and industry standards. With the alloys nickel composite market expected to expand considerably, remaining knowledgeable about the latest innovations and market trends is essential for strategic procurement.
Applications of Nickel Alloys: Industries and Innovations
Alloys nickel are essential in numerous sectors, mainly due to their outstanding characteristics that meet the rigorous standards of diverse uses. In the aerospace sector, these materials are pivotal in the manufacturing of jet engines and gas turbines, where material performance directly influences safety and operational efficiency. The energy sector benefits immensely from metallic compounds, particularly in nuclear and oil and gas applications, where their remarkable resistance to corrosion and ability to endure high temperatures are crucial.
Furthermore, in the marine sector, alloys nickel, such as nickel-copper mixtures, are favored for shipbuilding and offshore operations, owing to their resilience against harsh environmental conditions. The electronics sector also employs metal mixtures for connectors and other components, capitalizing on their excellent conductivity and resistance to oxidation. Significantly, the Asia Pacific market for alloys nickel and other nickel-based materials is anticipated to expand at a CAGR exceeding 9.5% until 2027, propelled by the booming manufacturing sector in nations such as Japan and China.
This growth is particularly significant in the aerospace sector, as highlighted in the case study titled “Asia Pacific Market Growth,” which discusses how the shift of the global aerospace manufacturing industry towards emerging economies will significantly increase the demand for alloys nickel in the region. Additionally, a representative from one of the largest companies in the defense industry stated, “Thank you for sending the market report and data. It looks quite comprehensive and the data is exactly what I was looking for.
I appreciate the timeliness and responsiveness of you and your team.” These insights highlight the increasing significance of alloys nickel in current and upcoming advancements across these sectors.
Key Properties of Nickel Alloys: Why They Matter
Copper-based mixtures, especially Domadia’s premium copper-copper mixtures, are characterized by several important features that increase their worth in diverse industrial uses, enabling you to purchase with assurance. Experience the Domadia difference with alloys that offer:
Corrosion Resistance: Copper nickel alloys exhibit exceptional resistance to oxidation and corrosion, particularly beneficial in challenging environments such as chemical processing and marine applications. For example, these metals provide high resistance to corrosion, making them essential in marine environments where traditional materials may fail. They can significantly outperform stainless steel, which usually exhibits corrosion rates for the 316L and 800H materials at around 1 mm/year, while the 347H material can experience rates up to 10 mm/year, emphasizing the durability of copper copper-based compositions against corrosive agents. Alloy 400 (N04400), which is one of the alloys nickel, is frequently utilized in marine and chemical processing contexts, showcasing its practical utility in environments prone to corrosion.
High-Temperature Strength: Many alloys nickel, including Alloys 600 and 800, retain their strength and mechanical stability at elevated temperatures, a critical requirement in sectors like aerospace and energy. These metal mixtures are significantly utilized in pulp and paper mills because of their resistance to chloride stress corrosion cracking, rendering them dependable materials for challenging uses. This resistance is crucial for maintaining structural integrity in harsh operational conditions.
Good Weldability: The capability to join nickel-based materials without compromising their mechanical properties is a significant advantage. This characteristic facilitates efficient fabrication and repair processes, ensuring that components can be constructed and maintained effectively in industrial settings.
Magnetic Properties: Certain combinations, such as Invar, have distinct magnetic characteristics, which are essential for precision instrumentation and scenarios where minimal thermal expansion is needed.
Antimicrobial Characteristics: Copper and its mixtures are also recognized for their antimicrobial characteristics, making them appropriate for uses where cleanliness is crucial, such as in healthcare and food processing settings.
Real-World Insights: A case study titled “SEM Analysis of Crevice Attack Morphology” demonstrates the corrosion behavior of Alloy 718 samples exposed to seawater at varying temperatures. The analysis revealed that at 20°C and 50°C, the aerospace-grade samples showed signs of crevice and pitting corrosion, while the API 6ACRA grade primarily suffered crystallographic attacks. This emphasizes the significance of comprehending corrosion mechanisms in the choice of specific metals for particular uses.
Comprehending these characteristics, especially those of Domadia’s premium copper materials, is crucial for procurement managers when choosing the suitable material for particular applications. This knowledge ensures optimal performance and longevity, aligning material choices with operational demands and environmental conditions, and reinforces the confidence in purchasing from Domadia.
Challenges in Machining and Processing Nickel Alloys
Machining and processing nickel alloys pose distinct challenges, primarily due to their unique physical properties:
Hardness: Nickel alloys are generally harder than many other metals, resulting in increased tool wear and necessitating lower machining speeds. According to recent findings, tool wear rates when machining materials like Inconel 718 can significantly impact production efficiency. For example, research shows that the wear rates can be up to 50% greater in comparison to softer substances, which directly influences machining expenses and downtime.
Work Hardening: A notable characteristic of many alloys nickel is their tendency to work harden during the machining process. This phenomenon complicates cutting and shaping operations, often requiring specialized tools and techniques to ensure effective removal. Research conducted by Senkathir et al. exemplifies this, optimizing wire-EDM machining of Nimonic 80a to enhance machinability.
Heat Generation: The machining process can produce significant heat, which poses risks to both the substance and tooling. The application of cryogenic coolants, such as liquid nitrogen and liquid carbon dioxide, can effectively reduce machining temperatures but may introduce challenges like material embrittlement and increased operational costs.
To address these challenges, procurement managers should prioritize sourcing high-quality, specialized cutting tools designed for specific metals. Furthermore, implementing proper machining techniques, including adequate lubrication—as demonstrated in the case study on lathe threading practices—ensures improved effectiveness during threading operations. This case study demonstrates that adhering to traditional methods and providing sufficient lubrication can improve the efficiency of threading tasks on certain metals.
Additionally, as noted by Faraz, M. I., “the evaluation of machining variables on machinability of alloys nickel Inconel 718 using coated carbide tools highlights the critical factors influencing performance and efficiency in machining operations.” By adopting these strategies, organizations can enhance processing efficiency and achieve cost-effective production, ultimately optimizing their operations in a competitive market.
Conclusion
Nickel alloys are undeniably pivotal in modern engineering, offering unparalleled properties that meet the rigorous demands of various industries. From their exceptional corrosion resistance to their remarkable strength and heat resistance, these materials are indispensable in critical applications ranging from aerospace and energy to marine and electronics. Understanding the different classifications of nickel alloys, such as iron-nickel and nickel-copper variants, is crucial for procurement managers tasked with sourcing the right materials for specific operational needs.
As the demand for nickel alloys continues to grow, particularly with the rise of electric vehicles and sustainable practices, procurement professionals must navigate an evolving landscape. Staying informed about the latest innovations, market trends, and the challenges associated with machining and processing these alloys is essential for making strategic sourcing decisions. The insights gained from understanding the properties and applications of nickel alloys empower procurement managers to select materials that not only meet industry standards but also enhance operational efficiency and safety.
Ultimately, the strategic procurement of nickel alloys is not just about material selection; it’s about aligning sourcing decisions with broader industry advancements and sustainability goals. By leveraging their unique attributes and understanding the complexities of the market, procurement managers can significantly contribute to their organizations’ success while ensuring compliance with safety and operational requirements.