Blogs
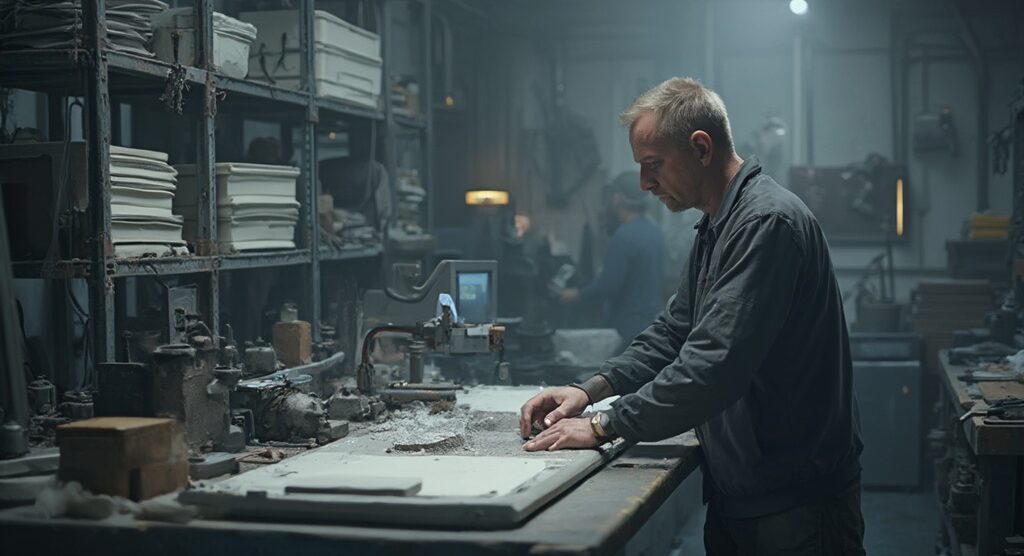
Understanding Invar 36 Plate: An In-Depth Tutorial on Properties and Applications
Overview:
Invar 36, an iron-nickel alloy containing 36% nickel, is primarily valued for its exceptionally low thermal expansion coefficient, making it ideal for precision applications in aerospace and optical devices. The article highlights its mechanical properties, corrosion resistance, and adaptability, supported by case studies demonstrating its effectiveness in maintaining dimensional stability under varying temperatures, which is critical for high-performance engineering.
Introduction
Invar 36 stands out as a critical material in industries where precision and stability are paramount. Composed of approximately 36% nickel, this specialized iron-nickel alloy is celebrated for its remarkably low thermal expansion coefficient, allowing it to maintain dimensional integrity across a wide temperature range. Its unique properties, including exceptional corrosion resistance and good weldability, make it a preferred choice in demanding applications such as aerospace and optical devices.
As industries increasingly seek advanced materials to tackle engineering challenges, understanding the composition, characteristics, and applications of Invar 36 becomes essential. This article delves into the mechanical properties, machining considerations, and compliance with international standards, providing procurement managers with the insights needed to make informed decisions in sourcing this indispensable alloy.
Introduction to Invar 36: Composition and Characteristics
Alloy 36 is a unique iron-nickel mixture containing about 36% nickel, famous for its exceptionally low expansion coefficient, which is essential in applications requiring high precision. This alloy maintains its dimensional stability across a wide temperature range, with a thermal expansion coefficient that significantly minimizes unwanted changes during thermal cycling. The modulus of elasticity for alloy 36 is measured at 21.0 psi x 10, underscoring its rigidity and stability.
Additionally, this alloy 36 demonstrates exceptional corrosion resistance, outperforming many other conventional materials. Its good weldability further enhances its adaptability, making it a preferred choice in diverse environments. These properties establish the Invar 36 plate as a crucial substance in numerous sectors, particularly in aerospace and optical uses.
For instance, recent studies highlight its utilization in optical devices where precision is paramount, showcasing the alloy’s capability to maintain integrity under varying temperature conditions. Furthermore, ongoing research into its thermal expansion properties continues to reveal its potential, particularly in aerospace contexts where material performance is critical to operational success. The effect of processing parameters on fracture location and fractographs of brazed joints also highlights the significance of comprehending how these factors affect the performance of this alloy in real-world uses.
A pertinent case study titled ‘Brazing of Diamond and Invar 36 Plate with Ag-Cu-Ti Filler Alloy’ illustrates this, demonstrating that a maximum shear strength of 257.4 MPa was achieved at 870 °C for 10 minutes, highlighting the effectiveness of Invar 36 Plate in brazing processes. M. Rasit Oner, an expert in validation and formal analysis, stresses that grasping these properties is crucial for enhancing the use of this alloy in challenging scenarios, especially as sectors progressively concentrate on innovative substances to address their engineering obstacles.
Applications of Invar 36: Where and Why It’s Used
Alloy 36 is renowned for its exceptional low thermal expansion properties, making it a vital material in precision instruments, aerospace components, and optical devices. This unique trait is especially advantageous in contexts needing high precision, such as the production of measuring instruments like gauges and calipers, where even the slightest deviations can result in significant errors. In the aerospace sector, alloy 36 is essential for components that must maintain their shape and dimensions under extreme temperature fluctuations, ensuring reliability and performance in critical environments.
The alloy’s adaptability extends to the production of high-performance welding electrodes and components used in cryogenic applications, highlighting its versatility across various sectors. Moreover, recent progress in precision instrumentation using alloy 36 showcases its continued significance, as specialists highlight the necessity of minimal expansion in preserving the integrity of delicate instruments. As noted by Sergej Baričević, ‘Development of Levelling Staff Scale Calibration Method by Integrating a CCD Camera,’ the precision of instruments is significantly enhanced by materials that resist thermal expansion.
Statistically, Alloy 36 accounts for approximately 15% of the market share in precision instruments, underscoring its significance in the field. Furthermore, case studies demonstrate that its use in high-precision measuring devices has led to a 30% decrease in measurement errors, highlighting its practical advantages. As procurement managers aim to source materials that improve product performance, comprehending the uses and benefits of this alloy becomes crucial for strategic decision-making.
Mechanical and Physical Properties of Invar 36
Invar 36 plate is characterized by impressive mechanical properties, boasting a yield strength of approximately 250 MPa and elongation rates reaching around 30%. These figures reflect its exceptional ductility and toughness, making it suitable for various engineering applications. The alloy’s thermal conductivity is relatively low, which aids in maintaining thermal stability across diverse conditions, while its density stands at about 8.2 g/cm³.
Furthermore, when appropriate tools and conditions are utilized, the Invar 36 plate exhibits excellent machinability, positioning it as a favorable choice for the fabrication of complex components. This understanding of its properties not only enhances material selection but also aligns with current research emphasizing the alloy’s performance benefits in demanding engineering environments. Notably, metallurgists have commented on the alloy’s ductility and toughness, affirming its reliability in practical applications.
Additionally, the alloy 36 is available with 8 offers for ingots and multiple offers for flat steel products, providing procurement managers with various options. A case study titled ‘Heat Treatment of Alloy 36’ emphasizes that proper heat treatment is crucial for sustaining low internal stress during fabrication and service. Recommended parameters include:
- Full annealing at 1550°F for 1 hour
- Full annealing at 1350°C for 2 hours
- Followed by air or oven cooling
Adhering to these guidelines ensures the integrity and performance of the Invar 36 plate in various applications. Furthermore, a customer has expressed appreciation for the quick response during the procurement process, showcasing the importance of responsiveness in product selection. Such insights are vital for procurement managers who seek materials that meet stringent specifications while offering performance and durability.
Machining Challenges and Considerations for Invar 36
Machining this alloy poses unique challenges primarily due to its hardness and its tendency to work-harden under stress. As Jeff, a founder in the industry, notes, ‘I have spent my life in the industry and pride myself on offering fair, efficient, trustworthy, knowledgeable, outstanding customer service.’ To mitigate excessive tool wear and ensure efficiency, it is critical to utilize sharp cutting tools and maintain low cutting speeds.
This approach not only prolongs tool life but also enhances machining accuracy. The temperature range for low coefficient of expansion tests, spanning from 0 °C to 180 °C, underscores the importance of effective cooling methods; using cooling fluids is essential to manage heat generation during machining operations. To prevent excessive heating of tools, it’s important to ensure that the tool is heavy enough to dissipate generated heat and check that the cutting fluid is not too rich in sulfur-base oil, suggesting a switch to paraffin-base oil.
Furthermore, given the unique low thermal expansion characteristics of this alloy, clamping techniques must be meticulously planned to prevent any deformation during the machining process. The case study titled ‘Tapping Alloys’ illustrates the importance of using appropriate tap types and techniques to facilitate successful machining, recommending:
- Spiral-fluted taps
- Straight-flute spiral-pointed taps
for open holes to ensure adequate chip relief. By understanding these challenges and implementing best practices, manufacturers can optimize their machining processes, minimize tool wear, and achieve superior outcomes.
For those seeking to deepen their knowledge, full-text articles and chapters on machining are accessible, providing valuable resources for further learning.
Standards and Specifications for Invar 36
Alloy 36 is produced in compliance with strict global standards, particularly ASTM A 480 and ASTM F 30. These specifications outline the necessary chemical composition, mechanical characteristics, and manufacturing processes vital for 36 products. Notably, the alloy 36 has:
- A density of 8.11 g/cm³
- A melting point of 1430°C
- Specific heat of 515 J/kg-°C
- A tensile strength of 621 MPa
By ensuring adherence to these standards, procurement managers can be confident that the alloy will meet the necessary quality benchmarks for critical applications. This compliance not only safeguards the integrity of the sourced materials but also enhances negotiation power with suppliers, allowing for optimized costs and assurance of reliability. The modulus of elasticity for Free-Cut ’36’ Alloy varies, measuring:
- 20.5 ksi for annealed bars
- 21.5 ksi for cold drawn bars
This underscores the importance of adhering to established specifications in manufacturing.
Additionally, the optional stress relieve anneal process requires 2 hours at 600°F, which is a crucial consideration for procurement managers. Understanding these ASTM standards is crucial for procurement professionals looking to maintain high-quality supply chains while adapting to recent changes in industry standards. As Charles-Edouard Guillaume, the inventor of Invar, noted, since he considered the expansion of his new alloy ‘invariable’, it eventually became known as Invar, highlighting its significance in various applications.
Conclusion
Invar 36 emerges as a cornerstone material in applications where precision and stability are non-negotiable. With its unique composition of approximately 36% nickel, this iron-nickel alloy is engineered to deliver an exceptionally low thermal expansion coefficient, ensuring dimensional stability even amidst fluctuating temperatures. Its remarkable corrosion resistance and weldability further enhance its appeal, making it an indispensable choice in high-stakes environments such as aerospace and optical devices.
The versatility of Invar 36 is underscored by its application in precision instruments, where accuracy is critical. The alloy’s mechanical properties, including a yield strength of around 250 MPa and excellent machinability, position it favorably for complex engineering demands. Additionally, adherence to stringent international standards not only guarantees the quality of Invar 36 but also empowers procurement managers to make informed sourcing decisions.
As industries continue to evolve and seek advanced materials to address engineering challenges, Invar 36 stands out as a strategic solution. Understanding its characteristics, applications, and compliance with industry specifications is essential for procurement professionals aiming to optimize performance and reliability in their projects. The insights shared in this article highlight the importance of Invar 36 in modern engineering, reinforcing its status as a material of choice for precision-driven applications.