Blogs
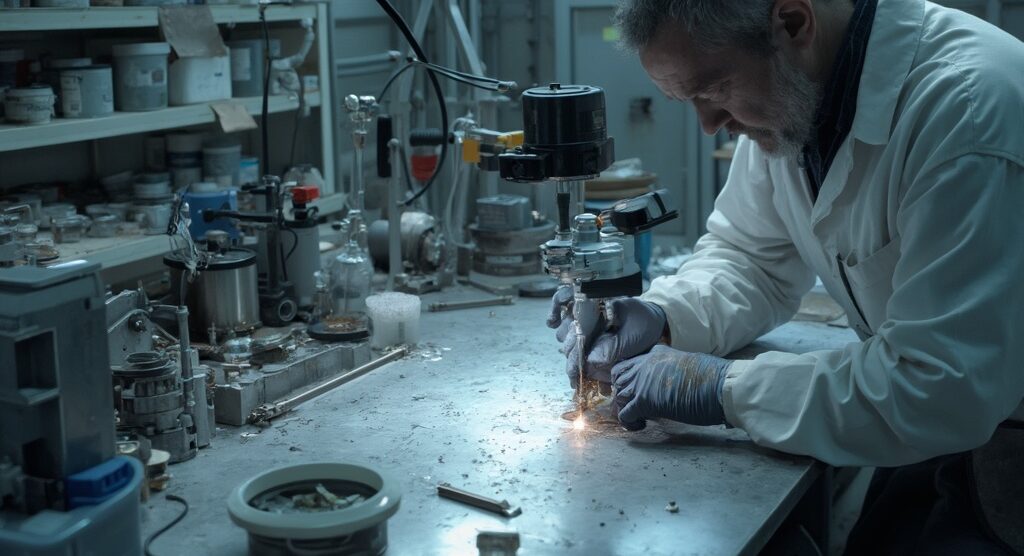
How to Etch Inconel 625: A Step-by-Step Guide for Precision Results
Overview:
The article provides a comprehensive step-by-step guide for etching Inconel 625, emphasizing the importance of preparation, cleaning, and monitoring throughout the process to achieve precision results. This guidance is supported by detailed techniques, safety precautions, and post-etching processes, which collectively ensure effective and reliable outcomes when working with this high-performance nickel-chromium alloy.
Introduction
Inconel 625 stands out in the realm of high-performance alloys, renowned for its impressive strength and unparalleled resistance to oxidation and corrosion. This nickel-chromium alloy is not just a choice; it is the preferred solution for industries operating under extreme conditions, including:
- Aerospace
- Chemical processing
- Marine environments
Its exceptional properties, such as a remarkable elongation percentage and excellent weldability, make it an ideal candidate for complex applications. As organizations increasingly seek materials that can withstand the rigors of modern engineering challenges, understanding the nuances of etching Inconel 625 becomes critical.
This article delves into the properties and applications of Inconel 625, providing a comprehensive guide to effective etching techniques, common challenges, safety precautions, and post-etching processes, ensuring that procurement managers and technical experts are equipped with the knowledge needed to optimize their operations.
Understanding Inconel 625: Properties and Applications
Alloy 625, a nickel-chromium material, is renowned for its remarkable strength and exceptional resistance to oxidation and corrosion, making it a preferred choice in high-stress environments. With an impressive elongation percentage of 51.5% at 1920°F, this alloy is particularly well-suited for applications in aerospace, chemical processing, and marine industries. Its excellent weldability further enhances its versatility, allowing for effective integration into complex assemblies.
To ensure optimal welding results, standard practices such as:
- Maintaining clean surfaces
- Achieving good joint alignment
should be followed. The ability to withstand extreme temperatures is crucial, especially in aerospace and marine applications where durability and reliability are paramount. In real-world applications, Inconel 625 etching has been utilized in Tesla’s battery pack components and NASA’s thruster injectors, showcasing its performance improvements over traditional materials.
Furthermore, the exceptional properties of copper nickel alloys, including excellent corrosion resistance and high thermal and electrical conductivity, make them ideal for demanding environments in marine, automotive, and electrical industries. For instance, copper nickel alloys are widely used in shipbuilding and offshore applications due to their resistance to seawater corrosion. The integration of non-sparking tools is essential in explosive environments, providing safe and reliable alternatives.
These tools are specifically designed to prevent sparks that could ignite flammable substances, ensuring protection in hazardous conditions. Comprehending these essential characteristics is vital for choosing suitable techniques and solutions, as they directly affect the success of the process and the performance of the final product.
Step-by-Step Guide to Etching Inconel 625: Techniques and Solutions
Preparation: Begin by gathering all necessary materials including nickel-chromium alloy samples, an appropriate solution for surface treatment—such as a Hydrochloric Acid and Hydrogen Peroxide mixture prepared with 6 mL of Hydrochloric Acid to 4 drops of 30% Hydrogen Peroxide—protective gear, and a well-ventilated workspace to ensure safety and efficiency. It is important to note that alloy 625 has an average dynamic modulus of elasticity at room temperature of 30.2 psi x 10(6) (MPa), which is a critical property to consider during processing.
Cleaning the Surface: It is essential to thoroughly clean the surface of the 625 samples to eliminate any contaminants that could disrupt the engraving process. Employing an ultrasonic cleaner or an appropriate solvent will enhance the adhesion of the solution, which is vital for attaining accurate results. According to Ken Vlach, ‘The excellent resistance to oxide spalling makes alloy 603XL an excellent choice for applications where oxide contamination cannot be tolerated,’ highlighting the importance of effective cleaning methods in preventing contamination during etching.
Applying the Inconel 625 etching solution: Immerse the cleaned Inconel 625 sample in the prepared solution, ensuring complete coverage for uniform treatment. The duration of immersion will vary based on the desired depth and detail; therefore, it is advisable to monitor the process closely.
Monitoring the Process: Regular observations during the engraving phase are critical to achieving the desired results. Adjust the engraving time as needed, considering the progress noted on the sample. This step is vital to accommodating variations in material response.
Rinsing and Neutralizing: After achieving the desired engraving effect, carefully remove the sample and rinse it thoroughly with water to neutralize the acid. In cases where a more effective neutralization is necessary, apply a suitable neutralizing agent to ensure complete safety and stability of the sample. The pickling process for Alloy 625 involves descaling with sodium hydride baths followed by immersion in sulfuric and nitric-hydrofluoric acid baths, which may provide insights into effective cleaning techniques that can be adapted for etching.
Drying: Allow the etching sample to dry completely before further handling. Ensuring no moisture remains is crucial to preserving the integrity and finish of the alloy 625, as moisture can adversely affect the final outcome.
Common Challenges in Etching Inconel 625 and How to Overcome Them
Addressing Etching Challenges in Inconel 625
- Inconsistent Engraving Depth: Achieving uniform engraving depth is crucial for accurate results. Irregular use of the solution can result in different depths throughout the sample.
To mitigate this, ensure that the solution is applied uniformly—consider utilizing a spray application method for more controlled coverage.
- Surface Contamination: The presence of contaminants can significantly impair engraving quality. A thorough cleaning of the sample before engraving is essential.
Wearing gloves while handling prevents the introduction of oils or particulates that could compromise the engraving process.
Over-Etching: Overexposure of the sample to the engraving solution can result in excessive material removal, leading to inaccurate data. Closely observe the engraving process and set a timer to manage exposure duration effectively, thus preventing over-engraving.
Chemical Reactions: Alloy 625 can demonstrate unpredictable reactions with specific substances in the engraving solution, especially considering the maximum variations of 5 at% in chromium (Cr) and iron (Fe) concentrations. It is advisable to conduct preliminary tests on small samples to determine how the material interacts with the chosen engraving agents, as these variations can significantly affect the engraving process. Such testing can prevent unforeseen results and guarantee dependable outcomes.
In the context of engraving nickel alloys, challenges such as surface contamination and variable engraving depth are frequent. A recent analysis of WC-Co sintered carbide cutting tools demonstrated the importance of effective engraving techniques, utilizing hydrochloric acid saturated with ferric chloride. This approach not only helped in uncovering tungsten carbide grain edges but also highlights the importance of exact application techniques for successful results in processing methods.
Ben Britton’s insights on the complexities faced in processing nickel alloys, particularly in his work titled > The Performance of Different Etchants on the Carbides of Ni600 and Ni625 <, emphasize the challenges that practitioners encounter when dealing with inconel 625 etching. As the industry evolves, addressing these challenges becomes increasingly critical, especially as the 2024 landscape presents new considerations for engraving processes.
Safety Precautions and Best Practices for Etching Inconel 625
Personal Protective Equipment (PPE): The foundation of protection in chemical etching begins with appropriate PPE. To mitigate the risk of chemical exposure, always wear gloves, goggles, and a lab coat. These items are essential in protecting against corrosive substances and should be selected based on the specific chemicals in use. Expert recommendations emphasize that proper cleaning after use, as noted by Polly, ‘thorough scrubbing with baking soda neutralizes the etchant,’ plays a crucial role in maintaining security and preventing accidental exposure during subsequent handling. Additionally, investing in Non-Sparking Tools, such as the Beryllium Copper Non-Sparking Wrench, is critical in explosive environments. These tools are specifically designed to reduce the risk of sparks that could ignite flammable chemicals, thus improving protection during operations. Their non-sparking characteristics make them the best option for non-sparking uses, ensuring adherence to regulations and safeguarding personnel and assets alike. The cost-efficiency of chemical processing, particularly for large-scale production, highlights the significance of incorporating protective measures, including the use of Non-Sparking Tools, to secure operations and improve overall protection protocols.
Ventilation: Ensure that your workspace is well-ventilated or, preferably, utilize a fume hood. This precaution is vital to reduce inhalation risks associated with harmful vapors emitted from etching solutions. The most recent guidelines highlight that a well-ventilated environment not only protects operators but also improves overall operational efficiency.
Storage and Disposal: Proper storage and disposal of chemicals are critical to preventing environmental contamination. Always store hazardous materials in clearly labeled containers, and adhere to local regulations when disposing of waste. Implementing these practices not only ensures compliance but also protects the surrounding ecosystem from potential chemical spills. Effective cleaning protocols, like those utilized in anodizing processes, are crucial for preserving security and efficiency in chemical handling.
Emergency Procedures: Familiarization with emergency response protocols is essential. Make certain that eyewash stations and spill kits are accessible and staff are trained to use them effectively. Additionally, incorporating Non-Sparking Tools into your protection protocols ensures that in the event of an incident, the risk of ignition is minimized. This preparedness can significantly mitigate the impact of accidents, ensuring a quick and efficient response to any incidents that may arise during chemical processing operations. A proactive approach to safety can drastically lower the likelihood of injuries and enhance workplace safety culture.
Post-Etching Processes: Finishing Techniques for Inconel 625
Polishing: Following the inconel 625 etching process, it is crucial to polish the alloy 625 to achieve a superior surface finish. Employ fine abrasives or specialized polishing compounds tailored for metal applications. Research indicates that effective polishing can significantly improve surface characteristics, as demonstrated in studies showcasing the effectiveness of various abrasives. Britton, B. emphasizes this by stating,
The Performance of Different Etchants on the Carbides of Ni600 and Ni625
, highlighting the importance of appropriate polishing techniques in enhancing the performance of nickel alloys. Additionally, it is noteworthy that the as-built cladding bond consists of a 25 – 50 μm wide transition zone, which underscores the necessity for meticulous polishing to ensure a smooth surface transition.Passivation: Implement a passivation treatment to enhance the corrosion resistance of alloy 625. This involves exposing the alloy to an acid solution that effectively removes free iron and fosters a robust protective oxide layer. The importance of passivation cannot be overstated, as it directly impacts the longevity and reliability of the material in demanding applications.
Inspection: A meticulous inspection of the inconel 625 etching surface is essential to confirm that the desired quality standards have been met. Evaluate for imperfections, surface irregularities, or areas requiring further finishing to ensure optimal performance in its intended application. Optical microscopy and scanning electron microscopy are valuable tools for assessing surface integrity, allowing for detailed characterization of the material. The insights gained from similar studies, such as the wettability of a specific nickel-chromium alloy with BNi-3 brazing filler metal, can provide valuable context for understanding the significance of surface preparation methods in achieving high-quality outcomes.
Final Cleaning: It is imperative to conduct a thorough cleaning of the finished product to eliminate any residues resulting from the inconel 625 etching and polishing processes. This step ensures that the Inconel 625 is prepared for its specific application, maintaining its integrity and performance standards. In recent analyses, effective cleaning protocols have been shown to enhance the overall quality of nickel alloys, reinforcing the importance of this final step.
Conclusion
Inconel 625 is an exceptional alloy that excels in demanding environments due to its outstanding strength and resistance to oxidation and corrosion. This article has thoroughly explored its properties, highlighting its impressive elongation and weldability, which are critical for applications in aerospace, chemical processing, and marine industries. The successful etching of Inconel 625 is paramount for optimizing its performance, and understanding the associated techniques and challenges is essential for procurement managers and technical experts.
Effective etching techniques have been outlined, emphasizing the importance of preparation, cleaning, and monitoring during the etching process. Common challenges, such as inconsistent etching depth and surface contamination, can hinder results, but these can be effectively managed through meticulous procedures and adherence to safety precautions. The integration of personal protective equipment, proper ventilation, and emergency preparedness further underscores the commitment to safety in chemical handling.
Finally, post-etching processes like polishing, passivation, and thorough inspection are vital for ensuring that the final product meets the highest quality standards. By following these best practices, organizations can harness the full potential of Inconel 625, ultimately enhancing the reliability and performance of their applications. As industries continue to evolve, the strategic understanding of etching techniques for Inconel 625 will be a key factor in maintaining a competitive edge in high-performance environments.