Blogs
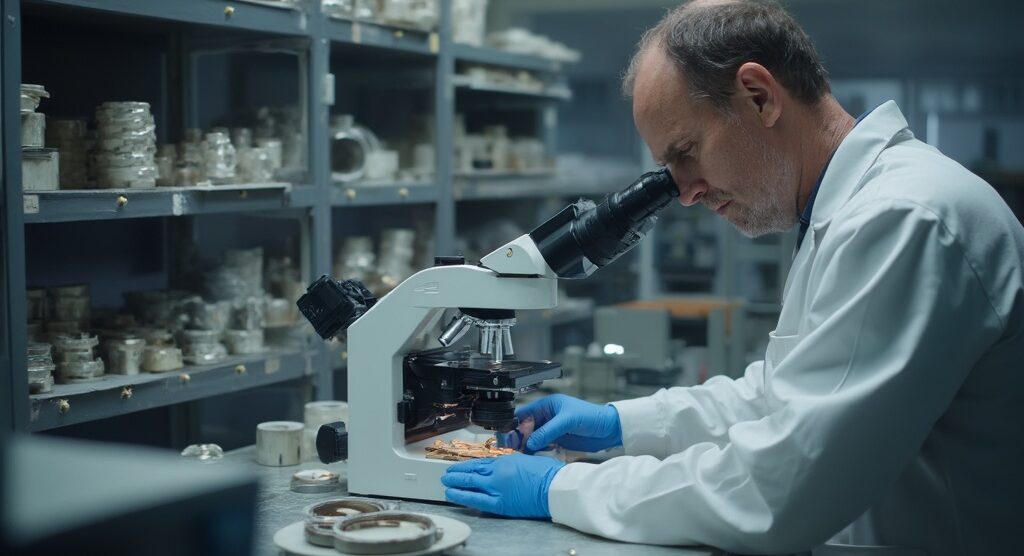
Understanding AMS 5581: An In-Depth Tutorial on Nickel Alloy Properties
Introduction
In the realm of advanced engineering materials, AMS 5581 stands out as a highly specialized nickel-based alloy, renowned for its exceptional properties and versatility across various industries. Predominantly composed of nickel, this alloy exhibits remarkable strength and resistance to oxidation and corrosion, even under extreme temperatures. Its application spans critical sectors such as aerospace, automotive, and electronics, where reliability and performance are non-negotiable.
As procurement managers navigate the complexities of sourcing this alloy, understanding its composition, compliance standards, and best practices becomes imperative. This article delves into the intricacies of AMS 5581, offering insights into its key properties, applications, and strategies for ensuring quality and reliability in procurement processes.
Overview of AMS 5581: Composition and Key Properties
AMS 5581 is a highly specialized nickel-based material, predominantly composed of nickel, ranging from 80% to 90%. Its unique formulation includes significant amounts of chromium and iron, along with smaller quantities of molybdenum and titanium, which contribute to its outstanding mechanical properties. This metal is recognized for its high strength and exceptional resistance to oxidation and corrosion, even at elevated temperatures. Notably, copper nickel mixtures also provide excellent resistance to corrosion and oxidation, making them suitable for demanding environments in marine, automotive, and electrical industries. Inconel X750, another nickel-based material, demonstrates creep-rupture strength at temperatures up to 1290°F (700°C), underscoring the high-temperature capabilities common to these substances.
Nickel alloys, as highlighted by Continental Steel & Tube Company, exhibit uniform strength qualities, efficiently resisting shear, tension, and compression forces. The excellent weldability and formability of AMS enhance its suitability for diverse manufacturing processes. For instance, AMS is frequently utilized in aerospace applications, where its capacity to endure extreme conditions is essential. The robust performance of this material in extreme environments, such as those outlined in recent developments for 2024, reinforces its status as a preferred choice for demanding applications, where maintaining structural integrity and longevity is critical.
Machining nickel compositions, including AMS specifications, requires specialized tools and techniques due to their unique properties. Comprehending these particular requirements can result in efficient and cost-effective manufacturing, as shown in various case studies that highlight the significance of customized machining strategies for AMS. Furthermore, our mica insulation tape products are designed for high-temperature resistance and electrical insulation, ensuring reliability in critical applications across various industries. The strategic application of this combination and complementary substances like mica tape in real-world uses demonstrates their versatility and dependability, reinforcing their status as essential components in advanced engineering and industrial sectors.
Applications of AMS 5581 Nickel Alloy in Industry
AMS 5581 nickel material exhibits exceptional versatility and durability, making it indispensable in several high-stakes industries. In aerospace, it is integral to the construction of jet engines and gas turbines, where its superior resistance to high temperatures and oxidation ensures optimal performance. This alloy is part of a broader range of substances, including:
- Beryllium copper
- Kovar
- Metal
- Nickel
These are categorized under our extensive metal and alloy offerings. The variations in Poisson’s ratio for annealed and solution-treated conditions across different temperatures underscore the substance’s adaptability in extreme environments, enhancing its reliability in critical applications.
Transitioning to automotive applications, AMS is extensively utilized in exhaust systems that endure harsh operational conditions. Recent studies emphasize that relative humidity significantly impacts the formation of secondary species in aerosol particles, providing valuable insights into the material’s robustness under varying atmospheric conditions. Furthermore, the latest advancements in nickel alloys for automotive exhaust systems emphasize AMS’s significance in promoting emission control technologies, ensuring adherence to strict regulations.
In addition to its aerospace and automotive applications, AMS plays a significant role in the electronics industry due to its excellent conductivity and corrosion resistance. This versatility makes it ideal for manufacturing connectors and contacts. Our metal sputtering targets, including high-conductivity options in:
- Aluminum
- Copper
- Gold
- Silver
- Titanium
further emphasize the significance of choosing the right components for advanced applications. By maintaining a focus on aerospace and automotive applications, we can better appreciate AMS’s adaptability and reliability, solidifying its status as a critical material across sectors that demand high performance and resilience.
Understanding AMS 5581 Standards and Compliance
AMS is regulated by a collection of international standards that meticulously specify its composition, manufacturing processes, and quality assurance protocols. The Dynamic Modulus of Elasticity at 1000°C for AMS is measured at 126 GPA, showcasing its robustness under high-temperature conditions. Ensuring adherence to these standards is vital for confirming that the material meets stringent performance specifications necessary for critical applications, especially due to its exceptional strength, corrosion resistance, and thermal stability, making it a favored option across various industries.
Procurement managers should be well-versed in the guidelines provided by ASTM International and SAE International, which establish comprehensive testing methods and material property requirements for nickel materials, including AMS 5581. Significantly, standards like ASTM B637 detail the requirements for nickel-based metal bars and rods, while SAE J461 describes the classification of nickel materials. For instance, the HAYNES 625 alloy, which is frequently utilized in similar applications, adheres to various AMS and SB standards, demonstrating its compliance and reliability across diverse engineering uses. This adherence not only assures the product’s reliability but also significantly bolsters the supplier’s credibility within the industry.
At Domadia, we ensure quality assurance by conducting rigorous testing and inspection processes for our Nickel Molybdenum Iron Alloy, adhering to stringent industry standards to meet or exceed expectations. Additionally, staying updated with the latest developments is essential. For example, significant research by Dragos Gabriel Zisopol on advancements in welding techniques for coiled tubing can offer valuable insights for refining procurement strategies, ensuring that materials meet evolving standards.
Furthermore, our Mica Tape Products, designed for high-temperature resistance and electrical insulation, are indispensable in various applications. Their superior insulation properties ensure reliability and durability in critical applications, from household appliances to industrial machinery. Ultimately, thorough knowledge and strict adherence to ASTM and SAE standards, including specific references to AMS compliance, along with our commitment to quality, are essential for maintaining the highest quality and performance in procurement processes.
Best Practices for Sourcing AMS 5581 Nickel Alloy
Sourcing AMS requires a strategic and comprehensive method to guarantee the highest quality and reliability. To start, identify suppliers with a proven track record in delivering premium nickel alloys. The composition of Inconel 625, which comprises approximately 62% Nickel, 21.5% Chromium, 9.0% Molybdenum, and 3.7% Niobium, underscores the necessity of partnering with suppliers who strictly adhere to these specifications. In environments with explosive potential, it is equally critical to consider the application of Non-Sparking Tools, such as brass or aluminum wrenches and hammers, which serve as the best alternative to mitigate risks associated with sparks that could ignite flammable substances.
Establishing long-term relationships with reputable suppliers can lead to better pricing and a more consistent supply chain. Conducting rigorous quality assessments and audits is essential to verify compliance with AMS 5581 standards. This includes assessing the supplier’s capacity to meet specific composition and performance requirements, as well as ensuring they provide necessary safety tools for hazardous environments.
To optimize procurement processes, leverage tools such as demand forecasting and inventory management. For instance, using advanced forecasting software can improve precision in predicting resource needs, while effective inventory management methods, such as just-in-time (JIT) inventory, can minimize excess stock and reduce lead times. Regular market analysis is also crucial to stay updated on pricing trends and availability, enabling procurement managers to make informed and strategic sourcing decisions.
Aerospace applications of Inconel 625 exemplify its reliability and performance, particularly in demanding environments like aircraft fuel lines. This case study emphasizes the significance of obtaining high-quality substances that can endure a broad range of temperatures, including cryogenic levels. Additionally, ensure that the suppliers of high-temperature materials, such as electrical insulation papers and fabrics, are capable of meeting industry standards. By adhering to these best practices, procurement managers can secure dependable and high-performing nickel materials and Non-Sparking Tools for their operations. In conclusion, concentrating on strategic supplier relationships, through quality assurance, and knowledgeable market analysis will enable procurement managers to improve their sourcing strategies for AMS.
Evaluating the Quality of AMS 5581 Nickel Alloy
To ensure the quality of AMS 5581 nickel alloy, a thorough evaluation process is critical. This begins with securing certificates of compliance from suppliers, confirming adherence to stringent industry standards. As emphasized by the AMS F Corrosion and Heat Resistant Alloys Committee, recent revisions now prohibit unauthorized exceptions and update essential factors such as:
- Composition reporting
- Fabrication processes
- New requirements for tensile testing and hydrostatic tests
These updates are essential for upholding the integrity and reliability of the substance.
In the realm of electrical insulation, our Mica Tape Products exemplify high-temperature resistance and electrical insulation for critical applications across various industries. These products, including Mica Insulation Tape and Mica Sheet Tape, are particularly valuable in sectors such as aerospace and automotive, where safety and performance are paramount. Their exceptional flame resistance and dielectric strength make them ideal for applications requiring stringent safety measures against fire hazards, such as in the manufacture of fire-resistant cables.
Real-world examples further illustrate the significance of rigorous material testing. For instance, the INCONEL® 625—a nickel-chromium-molybdenum material recognized for its high strength and resistance to severe corrosive environments—undergoes extensive quality evaluations. These evaluations include detailed assessments of pitting and crevice corrosion resistance, confirming that the alloy meets specific properties and performance criteria.
Conducting tensile strength tests and corrosion resistance assessments on AMS is essential to validate its compliance with specified properties. Statistical data indicate that consistent testing demonstrates that over 95% of AMS samples meet the required tensile strength standards. Additionally, regular reviews of supplier performance and maintaining open communication channels can proactively address quality concerns. Creating a strong feedback system improves quality standards, ensuring that sourced materials, including custom sputtering targets such as Aluminum-Copper and Nickel-Chromium, consistently meet industry expectations. Expert opinions and the latest methods in quality evaluation reinforce the critical role of these processes in maintaining the highest standards for AMS 5581 nickel alloy.
Conclusion
The exploration of AMS 5581 highlights its pivotal role as a nickel-based alloy characterized by exceptional strength, corrosion resistance, and versatility across various industries. Its unique composition, primarily consisting of nickel along with chromium, iron, molybdenum, and titanium, underpins its outstanding mechanical properties, making it an ideal choice for demanding applications in aerospace, automotive, and electronics.
Understanding the rigorous compliance standards and best practices for sourcing AMS 5581 is crucial for procurement managers. Adhering to specifications set by ASTM and SAE ensures that the alloy meets the stringent performance requirements essential for critical applications. By forming strategic relationships with reputable suppliers and employing thorough quality assessments, procurement managers can secure reliable materials that uphold the integrity and performance needed in high-stakes environments.
Ultimately, the strategic sourcing and evaluation of AMS 5581 not only enhance operational efficiencies but also contribute to the overall success of projects across various industries. By prioritizing quality assurance and staying informed about industry developments, procurement managers can effectively navigate the complexities of sourcing this indispensable alloy, ensuring that they are equipped with the best materials to meet their operational demands.