Blogs
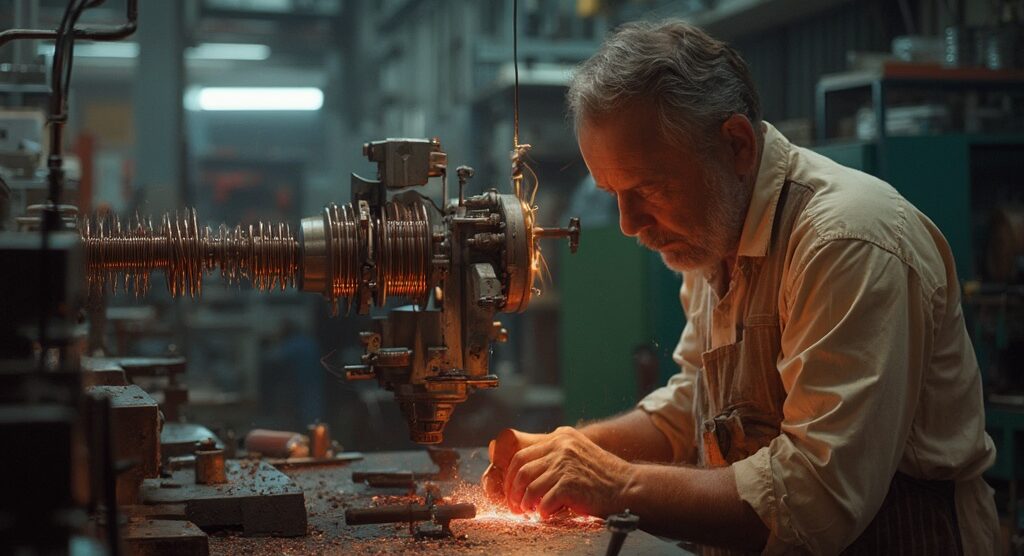
Understanding Beryllium Copper Compression Springs: A Complete Tutorial on Design and Applications
Introduction
In the realm of advanced materials, beryllium copper emerges as a premier alloy, renowned for its unique blend of strength, conductivity, and resistance to fatigue. This high-performance material is essential across diverse industries, from aerospace to electronics, where its remarkable properties enhance operational efficiency and safety.
As organizations seek to leverage these advantages, understanding the intricate characteristics and applications of beryllium copper becomes paramount. This article delves into the myriad benefits of beryllium copper, exploring:
- Its role in manufacturing compression springs
- The design considerations essential for optimal performance
- The innovative processes that underpin its production
By examining real-world applications and case studies, procurement managers will gain valuable insights into how beryllium copper can meet the rigorous demands of modern industry while ensuring compliance with safety standards.
Exploring Beryllium Copper: Properties and Benefits
Beryllium copper stands out as a high-performance alloy characterized by its exceptional strength, electrical conductivity, and fatigue resistance. Domadia is at the forefront of supplying and manufacturing Copper Beryllium Plates, typically composed of 0.5% to 3% of the element, achieving remarkable hardness and resilience. This specific composition makes it particularly well-suited for demanding uses, including aerospace and precision engineering.
Its unique thermal properties allow it to maintain performance even at elevated temperatures, while its impressive corrosion resistance ensures longevity in challenging environments. Recent studies confirm that a certain alloy outperforms many metal mixtures in durability, effectively resisting wear and galling, establishing it as the preferred option in demanding industrial environments. Significantly, the heat-treatability of the alloy improves its mechanical characteristics, enabling engineers to customize it to particular usage needs.
This adaptability is crucial across various sectors, including oil and gas, telecommunications, and electronics, where non-sparking characteristics are invaluable. Additionally, Domadia’s commitment to high-quality beryllium copper compression springs is evident through innovative manufacturing techniques and rigorous quality control processes, ensuring that every product meets the highest standards. A pertinent case study involves the ACOMP system, which provides automatic, continuous online monitoring of polymerization reactions, showcasing how beryllium alloy components can significantly improve efficiency and accuracy in modern manufacturing.
Furthermore, the importance of Non-Sparking Tools in explosive environments cannot be overstated, with the Beryllium Copper Non-Sparking Wrench exemplifying the safety features and applications critical in such settings.
Applications of Beryllium Copper Compression Springs in Various Industries
Beryllium copper compression springs are essential components in various industries, valued for their unique characteristics that enhance performance and longevity. In the electronics sector, where the electronic appliances segment generated USD 325 billion in Asia Pacific and USD 92 billion in Europe in 2022, these components play a vital role in connectors and switches, where dependable electrical performance is paramount. Additionally, in explosive environments, the use of Non-Sparking Tools is critical to ensure safety, and Beryllium Copper serves as an excellent alternative due to its non-sparking characteristics.
The distinct corrosion resistance of a specific alloy makes it especially beneficial for marine uses, permitting these components to withstand the difficulties presented by harsh saltwater settings and assuring their durability. Furthermore, in the medical sector, beryllium copper compression springs are essential in devices requiring precise control and durability, such as surgical instruments and diagnostic tools. Their remarkable ability to withstand repeated stress while maintaining operational efficiency positions them as a preferred choice for demanding tasks, reinforcing their critical role in modern industrial use.
Domadia’s commitment to providing high-quality customized Beryllium Copper Plates, backed by expert support, ensures that procurement managers can rely on us for their project needs. As noted by one of the largest companies in the defense industry:
- “Thank you for sending the market report and data. It looks quite comprehensive and the data is exactly what I was looking for.
I appreciate the timeliness and responsiveness of you and your team.”
Furthermore, our competitive pricing and extensive inventory of Beryllium Copper Strips ensure that we can meet your project requirements efficiently. Successful methods for handling priorities, as demonstrated in the case study named ‘Ensuring Smooth Teamwork in BI Collaborations,’ emphasize the significance of efficient procedures that can improve the management of metal uses in industrial environments.
Design Considerations for Beryllium Copper Compression Springs
Creating beryllium copper compression springs mechanisms necessitates thoughtful evaluation of various crucial elements, and at Domadia, we are here to assist you as a reliable partner in this endeavor. First and foremost, dimensions—such as wire diameter, coil diameter, and free length—are crucial in determining the performance and suitability of the coil for specific applications. The expected load capacity directly influences the selection of the alloy composition, essential for achieving the desired mechanical properties.
Notably, the high cost of radium metal, approximately $40 million per lb, highlights the economic implications of using beryllium copper compression springs and drives the search for viable alternatives. Additionally, the manufacturing technique used can significantly affect the final properties of the coil. As noted by Ampere Tseng, the level of rebound in sheet metals at various bending angles has been achieved by designing a modular ‘V’ bending die, which emphasizes the significance of accurate manufacturing processes.
Environmental factors, including temperature variations and exposure to corrosive substances, must also be considered, as they can dramatically affect functionality over time. Including permissible tolerances is essential to guarantee accuracy in production, while comprehending the intended use will assist in enhancing the spring’s performance. Moreover, at Domadia, we provide a wide selection of alloy products, including beryllium copper compression springs, as well as foils, sheets, rods, and wires, with custom fabrication choices accessible to fulfill your particular project requirements.
Our ready stock ensures that you have immediate access to the best Beryllium Copper solutions. Research on the mechanical characteristics of alloys, like those featured in the case study named ‘Alloys of Copper and Iron,’ shows that compositions with approximately 65% of the metal provide an exceptional mix of strength and electrical conductivity, which is crucial for uses involving certain metal applications. By tackling these factors and utilizing Domadia’s extensive solutions, engineers can proficiently manage the intricacies of beryllium alloy design, positioning themselves to satisfy the changing requirements of the industry in 2024 and beyond.
Advantages of Beryllium Copper in Spring Manufacturing
Beryllium copper compression springs are a standout choice in manufacturing due to their exceptional properties, particularly their high strength-to-weight ratio, which is vital for various industrial applications. This alloy not only demonstrates excellent electrical and thermal conductivity, making it ideal for electrical components and thermal management systems, but it also provides superior fatigue resistance, which is crucial for beryllium copper compression springs to maintain performance even under high stress and dynamic loading conditions. Recent studies indicate that the rebound values for these coils can range from 0.50 to 50, reflecting their resilience and adaptability in challenging environments.
The natural corrosion resistance of a specific alloy further improves the durability of components, rendering them appropriate for severe conditions. Additionally, the alloy’s machinability facilitates the precise fabrication of complex geometric shapes, an essential requirement in specialized engineering applications. Real-world instances show that metal springs perform exceptionally well, even when subjected to dynamic loads, confirming their reliability and effectiveness in demanding situations.
However, it is crucial to acknowledge the health implications associated with chronic disease, which is linked to prior sensitization, necessitating safety considerations in its use. To illustrate the benefits of a specific alloy, case studies on beryllium copper compression springs, as well as age-hardened materials C17200 and C17300, reveal that these substances achieve the highest strength among base alloys, valued for their elasticity, corrosion resistance, and conductivity. As noted by Sterner and Eisenbud (1951), the health risks associated with this substance were immunologically mediated, underscoring the importance of robust safety protocols in its industrial applications.
At Domadia, we take pride in our leadership in supplying and manufacturing high-quality beryllium copper compression springs tailored to your needs. Our commitment to innovative manufacturing and rigorous quality control ensures that you receive the best materials. For procurement managers, we also provide comprehensive pricing and inventory details for beryllium copper compression springs and strips.
Additionally, our Beryllium Copper compression springs, along with our Non-Sparking Wrench, offer safety features ideal for hazardous environments, further demonstrating the versatility of our Beryllium Copper solutions.
Manufacturing Processes for Beryllium Copper Compression Springs
The creation of a specific alloy compression components is a multifaceted process that includes several essential phases, such as:
- Wire drawing
- Coiling
- Heat treatment
Initially, the beryllium copper alloy is drawn into wire form, with diameters meticulously tailored to specific design requirements. This precision is crucial, as variations in diameter can significantly influence the performance of the coil.
Once the wire is produced, it undergoes coiling, where advanced automated machinery shapes it into the required coil configuration, ensuring uniformity and accuracy. Following this, heat treatment processes—such as aging and annealing—are implemented to optimize the mechanical properties of the components. These processes not only enhance strength and flexibility but also improve fatigue resistance, which is essential for applications demanding high reliability.
Quality control measures play a vital role throughout the manufacturing process, ensuring that each component meets stringent specifications and industry standards. In sectors where performance is non-negotiable, adherence to these standards is critical. Recent advancements in heat treatment technologies further augment the manufacturing process, enhancing the efficiency and effectiveness of spring production.
As a reliable associate for beryllium-based solutions, Domadia highlights the significance of high-quality results, strengthening its dedication to outstanding customer service and project success. Domadia provides a wide array of products, including non-sparking wrenches made from a special alloy, which are designed with safety features to prevent sparks in hazardous environments. The European Commission identifies this element as one of the 34 essential materials for the European Union, highlighting its importance in crucial uses.
Moreover, data suggest that beryllium-based alloys demonstrate exceptional fatigue resistance and conductivity relative to other substances, rendering them perfect for challenging uses. Real-world case studies, such as those conducted by leading manufacturers, demonstrate the successful implementation of these processes in producing high-performance beryllium copper springs, showcasing their reliability and effectiveness in various industrial applications. For further guidance, user manuals are available to assist procurement managers in understanding product usage and specifications.
Conclusion
Beryllium copper stands as a cornerstone in advanced material applications, particularly in the manufacturing of compression springs across diverse industries. Its unique combination of strength, electrical conductivity, and resistance to fatigue not only enhances operational efficiency but also ensures safety in critical environments. The detailed exploration of its properties highlights the alloy’s exceptional performance under stress and its adaptability to various industrial requirements, making it an invaluable asset for procurement managers.
The significance of design considerations in the application of beryllium copper compression springs cannot be overstated. Understanding the interplay of dimensions, load capacity, and environmental factors is essential for optimizing performance. Moreover, the innovative manufacturing processes, including:
- Wire drawing
- Coiling
- Heat treatment
set the foundation for producing high-quality components that meet stringent industry standards. Real-world case studies further illustrate how these processes yield reliable and effective solutions in sectors such as aerospace, electronics, and medical devices.
Ultimately, the advantages of beryllium copper extend beyond its mechanical properties; they encompass economic viability and safety in hazardous environments. As organizations navigate the complexities of modern manufacturing, leveraging the unique characteristics of beryllium copper will be instrumental in achieving operational excellence and compliance with safety standards. By prioritizing this high-performance alloy, procurement managers position their organizations for success in an increasingly demanding industrial landscape.