Blogs
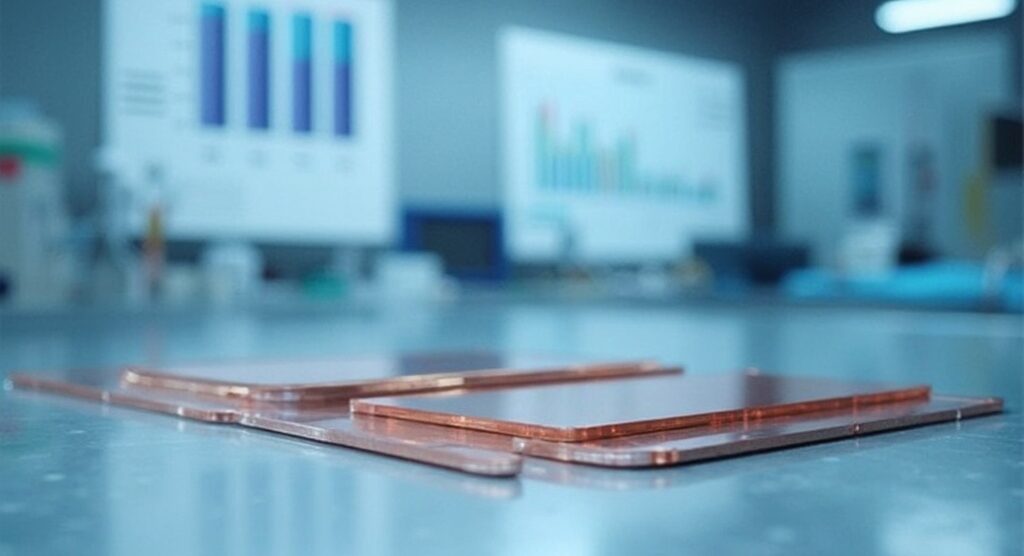
Understanding Copper Beryllium Density: An In-Depth Tutorial
Introduction
The unique properties of beryllium copper alloys position them as essential materials across various high-performance industries, from aerospace to automotive. Recognized for their exceptional strength, electrical conductivity, and corrosion resistance, these alloys are not only versatile but also critical in applications demanding reliability and precision. Understanding the nuances of their density—typically ranging from 8.3 to 8.5 g/cm³—can significantly influence material selection, performance, and overall project success.
This article delves into the fundamentals of beryllium copper density, explores various grades and their applications, and highlights the advanced manufacturing techniques that optimize these characteristics. Additionally, it addresses the crucial health and environmental considerations associated with handling these materials, empowering procurement managers to make informed decisions that balance performance, safety, and cost-effectiveness.
Fundamentals of Copper Beryllium Density
Copper is acknowledged as a high-performance alloy, defined by its exceptional mechanical properties, which include remarkable strength, superior electrical conductivity, and notable corrosion resistance. The mass per unit volume, or copper beryllium density, typically lies between 8.3 and 8.5 g/cm³, a range that differs depending on the specific grade and processing methods used. This compactness is a vital element as it affects the alloy’s weight-to-strength ratio, thermal conductivity, and overall effectiveness in challenging uses across different industries, including aerospace, automotive, and consumer electronics.
Significantly, the element content within the alloy, which typically ranges from 1.9% to 2.7%, plays a crucial role in determining the final copper beryllium density and its performance characteristics. Additionally, beryllium exhibits six times the specific stiffness of steel, further enhancing its appeal for high-reliability uses. At Domadia, we take pride in our adherence to international standards such as UNS and ASTM, ensuring that our Copper Plates meet the highest industry benchmarks.
Our dedication to excellence is demonstrated in our cutting-edge manufacturing methods and strict quality assurance, positioning us as a leader in providing high-performance Copper solutions customized for industrial uses. Copper plates are widely utilized in applications such as electrical connectors, precision tools, and aerospace components, where both strength and corrosion resistance are critical. For instance, Alloy 290 offers greater formability than Alloy 190 and is utilized for fabricating high-reliability components that require complex connections without sacrificing strength, demonstrating a cost-effective alternative for creating specially shaped electrical connectors and contacts.
The cost-effectiveness of Copper solutions, particularly in comparison to other materials, makes it an attractive choice for procurement managers seeking durable and reliable options.
Exploring Beryllium Copper Grades and Their Densities
Beryllium copper alloys, particularly C17200 and C17300, are pivotal in metal die casting due to their distinct properties. C17200, recognized for its high strength, displays a copper beryllium density of approximately 8.47 g/cm³, serving as a benchmark against pure copper’s mass per unit volume of 8.96 g/cm³. This grade is essential for demanding applications in industries such as aerospace and automotive, where exceptional hardness and fatigue resistance are critical.
On the other hand, C17300, with a lower mass of around 8.2 g/cm³, is perfect for projects that emphasize the advantages of copper beryllium density for weight reduction. Comprehending these characteristics of mass is essential for procurement managers, as they directly affect material selection based on performance requirements. Additionally, the practical relevance of C17510, which contains 0.2% to 0.6% of a specific element and is used in offshore oil and gas applications, further underscores the importance of copper beryllium density for application suitability.
Furthermore, pricing for Copper Strips typically ranges between $X and $Y per pound, depending on market conditions and inventory levels, which procurement managers must consider when sourcing materials. It’s also vital to note the safety implications of handling beryllium copper, as strict safety practices are necessary to mitigate health hazards. By leveraging this knowledge, procurement managers can make informed decisions that balance performance needs with material cost considerations, particularly when sourcing non-sparking tools designed for explosive environments.
Applications of Beryllium Copper Alloys and the Role of Density
Beryllium copper alloys are essential in diverse industries, including electrical connectors, automotive components, and aerospace applications, where their unique properties make them invaluable. At Domadia, we recognize that the concentration of these alloys significantly affects their performance characteristics. For instance, the high concentration of the C17200 alloy provides exceptional strength, making it ideal for precision tools and high-performance springs that demand robustness.
Conversely, the C17300 alloy, known for its lighter weight, is often employed in applications that prioritize reduced mass, such as lightweight electrical connectors. This distinction is crucial, as engineers understand that choosing the appropriate mass can enhance the functionality and longevity of components. Recent projections indicate a 15% increase in demand for copper alloys in 2024, particularly for lightweight materials in automotive components, underscoring the importance of understanding copper beryllium density and its performance relationships.
As a Senior Engineer at a leading automotive firm stated, ‘Selecting the appropriate beryllium copper alloy based on copper beryllium density is critical for optimizing performance and ensuring durability in our products.’ Furthermore, case studies demonstrate that aerospace applications using copper alloys have achieved significant efficiency improvements and weight reductions in aircraft components. Domadia stands ready to assist your material selection with our extensive range of high-quality, customized Copper Plates, including foils, sheets, rods, and wires, ensuring your project’s success through expert support tailored to your specific needs.
For guidance on utilizing our products effectively, refer to our user manuals, and experience the difference quality and expertise can make in your next project. Contact us today to learn more about our offerings and how we can help elevate your project.
Manufacturing Techniques for Optimizing Beryllium Copper Density
To attain optimal compactness and performance in Copper alloys, a range of advanced manufacturing methods are employed, taking into account the copper beryllium density, including casting, forging, and machining. Domadia’s extensive inventory features a comprehensive range of Beryllium Copper products, including:
- Plates
- Rods
- Sheets
- Wires
- Foil
- EMI finger strips
- Specialized tools
This ensures that procurement managers can find the right solutions for their projects. The casting procedure is especially beneficial, improving the uniformity of material composition throughout the alloy—essential for uses requiring consistent performance.
Conversely, forging techniques refine the microstructure, yielding improved mechanical properties such as tensile strength and ductility. Strategic heat treatment processes can significantly alter both the density of the alloy, including copper beryllium density, and its strength, allowing tailored properties to meet specific usage requirements. Significantly, this metal contracts and deforms less than glass at temperatures of 33 K, making it ideal for low-temperature uses.
Recognizing these techniques is vital for procurement managers aiming to optimize material selection while maintaining cost efficiency. As Sterner and Eisenbud pointed out in their early work, ‘grasping the intricate interactions of materials can result in improved uses,’ especially in high-performance environments such as electronics. The characteristics of this element enable efficient thermal management, as shown in the case study ‘Beryllium in Electronics,’ which illustrates its application as a structural support and heat sink in printed circuit boards.
Additionally, pricing and inventory details for these products are available upon request, ensuring that procurement managers have all necessary information for informed decision-making. The significance of this element in critical electronic applications is further emphasized by the recognition of support from industry leaders such as Hewlett-Packard and BrushWellman, highlighting collaborative advancements in this field.
Environmental and Health Considerations of Beryllium Copper Density
This element is classified as a hazardous material due to its toxicity, and exposure can result in severe health complications, including chronic lung disease (CBD). This highlights the necessity for manufacturers and procurement managers to implement stringent safety protocols and adhere to regulatory standards when handling copper alloys, particularly in environments where non-sparking tools are essential.
The Beryllium Copper Non-Sparking Wrench, known for its durability and resistance to sparking, is an ideal solution for explosive potential environments.
This wrench typically features a lightweight design, corrosion resistance, and compliance with industry safety standards, making it a reliable choice for professionals. Comprehending the copper beryllium density is vital for conducting thorough risk assessments, as materials with higher density can introduce unique handling challenges. It is essential to monitor exposure levels and maintain compliance with environmental regulations, which are designed to protect workers and mitigate potential health impacts associated with this substance.
Recent updates in safety regulations reflect a growing awareness of these health risks, with statistics indicating that chronic exposure disease treatment often involves corticosteroids, such as a typical administration of 40 mg of prednisone daily or every other day. Furthermore, a CBD Diagnostic Center must be equipped with an on-site pulmonary specialist and facilities for clinical evaluations, emphasizing the importance of a proactive approach to health and safety in the workplace. This is vital as managing acute exposure to the element focuses on removal from the source and symptomatic treatment, highlighting the need for effective protocols.
In light of the findings reviewed in ‘Environmental Health Perspectives‘, procurement professionals must remain vigilant in their adherence to safety protocols, ensuring that they protect not only their workforce but also their organizations from the implications of non-compliance. As Adrian P Harrison notes, understanding the physiological impacts of beryllium is crucial for developing effective safety measures, reinforcing the importance of expert insights in managing health risks associated with beryllium exposure, particularly when utilizing non-sparking tools like the Beryllium Copper Non-Sparking Wrench. The broader category of non-sparking tools is essential in explosive environments, as they significantly reduce the risk of igniting flammable materials, thereby enhancing workplace safety.
Conclusion
Beryllium copper alloys represent a critical component in high-performance industries, offering unique properties that cater to demanding applications. The exploration of density variations among different grades, such as C17200 and C17300, reveals significant implications for material selection. Understanding these nuances not only enhances performance but also ensures that procurement managers can make informed decisions that align with both project requirements and cost considerations.
The advanced manufacturing techniques discussed, including casting, forging, and strategic heat treatment, further illustrate the importance of density in optimizing the mechanical properties of these alloys. As industries continue to evolve, the demand for lightweight yet strong materials is projected to grow, making it essential for decision-makers to stay informed about the latest developments in beryllium copper applications.
Moreover, the health and environmental considerations surrounding beryllium copper handling cannot be overstated. Implementing robust safety protocols is crucial for protecting workers while maintaining compliance with regulatory standards. As the industry adapts to these challenges, the commitment to safety and quality will remain paramount.
In conclusion, the strategic selection of beryllium copper alloys, informed by an understanding of their density and performance characteristics, will empower procurement managers to enhance project outcomes. Emphasizing both innovation and safety, the use of these alloys is set to play an increasingly vital role in shaping the future of high-performance applications across various sectors.