Blogs
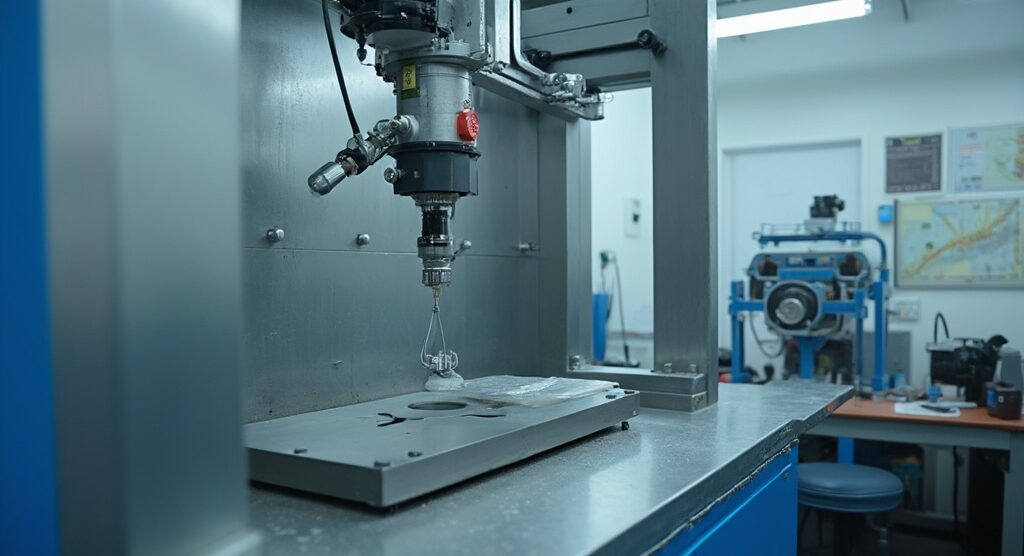
Understanding the Inconel 718 Stress-Strain Curve: An In-Depth Tutorial
Overview:
The article focuses on understanding the Inconel 718 stress-strain curve, which is crucial for predicting the alloy’s mechanical behavior under stress and temperature variations. It highlights key characteristics of the curve, such as the elastic limit and yield capability, and discusses how factors like heat treatment and predictive modeling enhance the alloy’s performance, making it suitable for demanding applications in industries like aerospace.
Introduction
Inconel 718 stands as a cornerstone in the realm of high-performance materials, particularly revered for its exceptional mechanical properties and resilience under extreme conditions. Understanding the intricacies of its stress-strain behavior is essential for engineers and procurement managers alike, as it informs critical decisions in material selection and application strategies. The stress-strain curve not only illustrates how Inconel 718 responds to stress but also highlights crucial factors such as:
- Yield strength
- Ultimate tensile strength
- The impact of temperature on its performance
With advancements in predictive modeling and heat treatment techniques, the capabilities of Inconel 718 are being further enhanced, paving the way for innovative applications in aerospace and beyond. This article delves into the fundamental aspects of Inconel 718’s mechanical behavior, the significance of heat treatment, and the role of predictive modeling, providing valuable insights for optimizing its use in demanding engineering environments.
Fundamentals of the Inconel 718 Stress-Strain Curve
The inconel 718 stress strain curve serves as an essential graphical representation of the alloy 718’s response to applied stress, detailing how it undergoes elastic and plastic deformation under various loading conditions. This curve includes key characteristics:
- The elastic limit, which indicates the maximum stress that the substance can endure while returning to its original shape.
- Yield capability, marking the transition from elastic to plastic deformation.
- Ultimate tensile capacity, the peak stress before failure.
- The fracture point, where the substance ultimately breaks.
These critical points are essential for accurately predicting the behavior of alloy 718 in operational environments, particularly where strength and durability are non-negotiable.
Recent studies indicate that at 650 °C, Alloy 718 begins to experience grain boundary sliding as it approaches its yield point, highlighting the importance of temperature in stress-strain analysis. Additionally, the coefficient of thermal expansion for Alloy 718 ranges from 7.1 to 16.0 x 10(-6)/°F, which further influences its performance under varying thermal conditions. A surface grinding test on IN718 alloy samples demonstrated the effectiveness of using a water-based coolant to dissipate heat during machining, providing practical insights into the processing techniques of the substance.
Furthermore, a case study on high-speed machining of alloy 718 has shown that grinding speeds between 5 to 25 m/s can enhance surface quality and reduce subsurface damage, reinforcing the necessity of understanding the Inconel 718 stress strain curve for real-world applications. Understanding these properties allows procurement managers to optimize material selection and application strategies, ensuring improved performance in high-stress environments.
Mechanical Properties and Behavior of Inconel 718
Alloy 718 is renowned for its remarkable mechanical properties, featuring a yield strength of approximately 1,200 MPa (174,000 psi) and an ultimate tensile strength that can surpass 1,400 MPa (203,000 psi). These robust characteristics are maintained even at elevated temperatures, making this alloy an ideal choice for high-performance applications such as aerospace and gas turbines. The coefficient of thermal expansion for Alloy 718 ranges from 7.1 to 16.0 x 10(-6)/°F, which is crucial for understanding its thermal properties in various applications.
Additionally, the Inter Pulsed gas tungsten constricted arc welding (IP-GTAW) process has shown a joint efficiency of 99.20%, significantly higher than traditional GTAW processes, making it a preferred method for welding alloy 718 components. This alloy’s unique strain rate sensitivity adds a layer of complexity, especially when considering the inconel 718 stress strain curve, as it exhibits different behaviors under varying loading conditions. Such nuances are critical for engineers to consider when making informed decisions regarding material selection and design, ensuring that the chosen materials will perform reliably under operational stresses.
Furthermore, companies such as Ariane Group (Airbus Safran Launchers) are developing injectors for the liquid rocket engine on the propulsion systems of the Ariane 6 launcher, showcasing the real-world application of a specific alloy in cutting-edge aerospace technology.
Impact of Heat Treatment on Inconel 718’s Stress-Strain Response
The heat treatment of Inconel 718 is a critical process that typically encompasses solution annealing followed by aging. This method is designed to modify the alloy’s microstructure through the precipitation of gamma prime (γ’) phases, which significantly improve its durability and hardness. Notably, the elongation of specimens austempered at variable temperatures reached approximately three times that of those austempered isothermally at 593 or 723 K, indicating the profound influence of heat treatment protocols on material properties.
The formation of twins during solid solution heat treatment, rather than during the aging process, has been shown to maintain thermal stability at hold times longer than six hours, further emphasizing the importance of this treatment in optimizing performance. The Inconel 718 stress strain curve of Alloy 718 reflects these changes, with samples subjected to optimal aging showing significantly higher yield and tensile properties. As emphasized by metallurgist Atroshenko, “the heat treatment and test temperature play pivotal roles in determining the performance characteristics of this superalloy under shock-wave loading conditions.”
Recent studies, including high-temperature shock-wave experiments at 650 °C, have further elucidated the strength characteristics of the alloy 718, showcasing its stability and performance under dynamic loading. Grasping these intricate interactions is crucial for engineers and procurement managers to guarantee that this alloy meets stringent engineering requirements in demanding applications. Copyright © 2006-2024 Scientific Research Publishing Inc. All Rights Reserved.
Predictive Modeling of Inconel 718 Stress-Strain Behavior
Predictive modeling serves as a crucial instrument in forecasting the inconel 718 stress strain curve, especially for alloy 718, which is recognized for its intricate performance characteristics. By leveraging statistical methods and advanced machine learning algorithms, engineers can achieve accurate predictions of how this alloy will react under various loading conditions and temperature ranges. Finite element analysis (FEA) stands out as a leading technique in this endeavor, allowing for detailed simulations that reflect the substance’s response.
Recent findings indicate that using a 45° inclined line scanning strategy during processing can significantly reduce residual stresses and deformation, demonstrating the practical benefits of predictive modeling. A physics-informed model introduced in a recent study, titled “Physics-Informed Model for Inconel 718,” highlighted the importance of dislocation motion and density progression during machining, providing insights that could enhance the machinability of Inconel 718 components. This model’s emphasis on microstructural evolution mechanisms is crucial for understanding substance behavior.
Furthermore, the complexity of predicting stress-strain responses is underscored by the inconel 718 stress strain curve tested at slow strain rates between 0.0001 and 0.1 s-1. As Gábor Harsányi, an Academic Editor, observes, “The integration of predictive modeling techniques is essential for advancing applications in science of materials.” By developing robust models grounded in empirical data, engineers can optimize designs effectively, minimizing the necessity for extensive physical testing.
This strategic approach not only accelerates the development process but also significantly reduces associated costs, making predictive modeling an invaluable asset in the field of science.
Applications of Inconel 718 Stress-Strain Analysis in Engineering
Alloy 718 is a crucial substance in the aerospace industry, especially in the production of gas turbine engines and high-performance automotive parts, mainly because of its excellent strength-to-weight ratio and outstanding corrosion resistance. Recent advancements in processing techniques, such as laser surface texturing and hot pressing, have underscored its potential to enhance thermal efficiency in aerospace applications. Stress-strain analysis, particularly through the inconel 718 stress strain curve, plays a vital role in engineering design, allowing engineers to assess the performance of alloy 718 under extreme conditions.
This analysis is crucial for choosing substances that meet stringent industry standards, thereby mitigating the risk of failures in service. For example, investment casting techniques can result in metallurgical flaws like porosity, segregation, and extremely coarse grain sizes, which emphasize the difficulties related to 718 processing. Understanding the material’s properties is essential for ensuring product reliability.
Additionally, a case study on additive manufacturing techniques, specifically laser powder bed fusion, has demonstrated significant promise in producing high-quality Inconel 718 components, showcasing its effectiveness in practical applications. Furthermore, macrographic and micro-hardness analyses conducted in this context illustrate the feasibility of producing bimetallic joints, adding another layer of technical detail relevant to procurement managers.
Conclusion
Inconel 718 stands as a premier choice for high-performance applications, particularly in the aerospace sector, due to its remarkable mechanical properties and resilience under extreme conditions. The stress-strain curve is essential for understanding how this superalloy behaves under various loading conditions, revealing critical factors such as yield strength and ultimate tensile strength. The insights gained from this curve enable engineers and procurement managers to make informed decisions regarding material selection and application strategies tailored to demanding environments.
The significance of heat treatment cannot be overstated, as it plays a pivotal role in enhancing Inconel 718’s mechanical properties. Through processes like solution annealing and aging, the alloy’s microstructure is optimized, leading to improved strength and stability under dynamic loading conditions. Coupled with advancements in predictive modeling techniques, engineers can accurately forecast the material’s performance, thus minimizing the need for extensive physical testing and expediting the design process.
Ultimately, the integration of stress-strain analysis, heat treatment, and predictive modeling creates a comprehensive understanding of Inconel 718’s capabilities. This knowledge not only supports the development of innovative applications but also ensures that the material meets the rigorous demands of modern engineering projects. As industries continue to evolve, leveraging these insights will be crucial for achieving optimal performance and reliability in high-stress applications.