Blogs
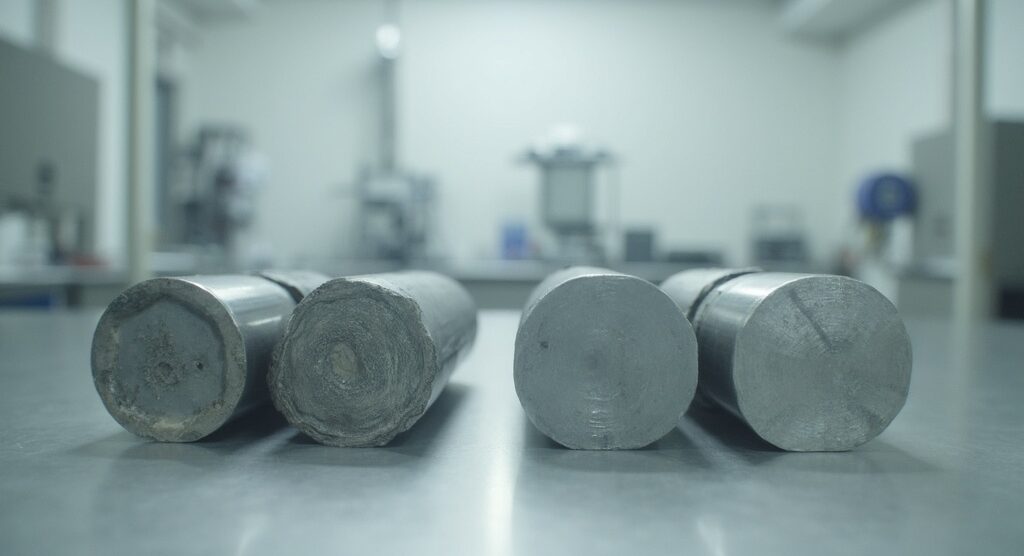
Is Steel Stronger Than Titanium? An In-Depth Comparative Study
Introduction
In the realm of material selection for industrial applications, the comparison between titanium and steel stands prominent due to their distinct physical properties and performance characteristics. Titanium, celebrated for its low density and high strength-to-weight ratio, is indispensable in sectors like aerospace and automotive where weight reduction is paramount. Conversely, steel, with its robustness and cost-effectiveness, remains a stalwart in construction and manufacturing.
This article delves into the nuanced differences between these two metals, examining their physical properties, strength and durability, corrosion resistance, and cost considerations, to provide procurement managers with a strategic approach to material selection based on specific application requirements.
Physical Properties Comparison
Titanium and iron exhibit distinct physical characteristics that significantly influence their use across various industries. Titanium, renowned for its low density, is substantially lighter than steel. This characteristic makes it an indispensable material in aerospace and automotive sectors, where weight reduction is a critical factor for performance and fuel efficiency. For instance, the ongoing challenges in the metal supply chain, exacerbated by geopolitical issues such as the conflict in Ukraine, have highlighted the material’s vital role in these industries.
Steel, especially high-strength alloys, presents a contrasting set of advantages. With a higher density, steel can offer greater robustness and durability in many applications. Its extensive use in construction and manufacturing sectors underscores its importance, despite its higher weight compared to other metals. Additionally, titanium’s higher melting point allows it to retain strength at elevated temperatures, a property that is particularly beneficial in high-performance environments. Conversely, steel, while versatile and strong, may experience a reduction in strength when exposed to high temperatures.
The distinct properties of these metals emphasize the significance of choosing the suitable substance based on the specific needs of the application. The ongoing advancements in material science, such as the development and characterization of new alloys, continue to expand the potential uses of these metals, ensuring their continued relevance in modern engineering and manufacturing.
Strength and Durability Analysis
When evaluating the strength and characteristics of a certain metal and an alloy, it is essential to take into account yield strength, tensile strength, and fatigue resistance. High-strength metal forgings, recognized for their excellent mechanical characteristics, can reach tensile strengths similar to those of high-strength alloys. These metal alloys are especially appreciated for their remarkable fatigue resistance, rendering them perfect for uses subjected to repeated stress, such as aerospace and automotive sectors.
This material, particularly carbon varieties and specific alloyed forms, excels in yield strength, enabling it to support greater loads in structural applications. However, steel can suffer from fatigue under cyclic loads, whereas titanium’s resistance to deformation under stress enhances its longevity in demanding environments.
The durability of both materials can vary with environmental conditions. Titanium’s resistance to corrosion and deformation under stress makes it a favored option for high-performance uses, including medical and military fields. Conversely, specialized forging methods utilized to create high-strength components ensure their reliability and performance, highlighting their appropriateness for critical applications.
Corrosion Resistance Comparison
Corrosion resistance is a pivotal consideration when selecting materials for use in harsh environments. Titanium stands out due to its exceptional resistance, particularly in chloride-rich and acidic settings. This superior resistance stems from a protective oxide layer that forms on its surface, making this metal a prime choice for marine and chemical processing industries. This property is highlighted in the use of high-strength titanium forgings, which offer remarkable durability and are widely utilized in aerospace, automotive, and military applications.
On the other hand, this metal, particularly in its uncoated state, is susceptible to rust and corrosion. To mitigate this, this metal often requires protective coatings or is alloyed with elements like chromium to enhance its resistance. Despite these measures, the environmental conditions of the intended application often determine whether the metal or alloy is the more suitable choice. As noted in recent studies, while steel can be modified to resist corrosion, this metal inherently maintains its integrity without the need for additional treatments, making it a more reliable option in corrosive environments.
Weight and Cost Considerations
‘Weight and cost are pivotal factors in procurement decisions, especially in industries like aerospace where performance and fuel efficiency are crucial.’. Titanium’s lightweight properties offer significant advantages in these scenarios, contributing to enhanced fuel efficiency and overall performance. The increase in air travel demand, attaining 97% of pre-pandemic levels worldwide, highlights the necessity for resources that can assist in fulfilling the rising production requirements of aerospace firms.
However, titanium’s higher expense, both in raw resources and processing, often acts as a barrier in cost-sensitive applications. This financial challenge is amplified by the ongoing recovery from pandemic-induced supply chain disruptions. As a result, aerospace companies face the dual challenges of navigating these supply chain issues while managing the substantial backlog of aircraft orders.
In contrast, this material remains a more cost-effective solution due to its abundance and ease of manufacturing. This makes iron the option of preference in sectors such as construction and automotive, where weight is less crucial. The transition from prescriptive to performance-oriented design criteria further endorses the utilization of economical materials such as metal, enhancing material efficiency without sacrificing performance. This trend aligns with the broader industry move towards optimizing procurement strategies to balance cost and functional requirements effectively.
Applications and Uses of Steel and Titanium
The uses of titanium and iron are distinct due to their unique properties and performance characteristics. Titanium’s high strength-to-weight ratio and excellent corrosion resistance make it indispensable in aerospace, medical implants, and high-performance sports equipment. This is particularly crucial in the aerospace sector, which has experienced a significant resurgence post-pandemic, with air traffic reaching 97% of pre-pandemic levels globally. On the other hand, the material’s versatility, robustness, and cost-effectiveness drive its widespread use in construction, automotive manufacturing, and infrastructure projects. For example, the North American market has seen accelerated production and use of stainless steel, especially in the automobile and construction sectors. Each material meets specific needs in its respective industry, shaping procurement strategies based on intended use and performance requirements.
Conclusion
The comparison between titanium and steel reveals critical insights for procurement managers aiming to optimize material selection for their applications. Titanium stands out due to its low density and high strength-to-weight ratio, making it particularly advantageous in sectors such as aerospace and automotive, where reducing weight can lead to significant performance improvements. Its exceptional corrosion resistance further enhances its suitability for high-performance environments, where reliability is paramount.
In contrast, steel offers robustness and cost-effectiveness, making it the material of choice for construction and manufacturing applications. Its high yield strength allows it to support heavier loads, although it may be susceptible to fatigue under cyclic stress. The ongoing advancements in both materials highlight the importance of understanding their unique properties and how they align with specific application requirements.
Cost considerations also play a vital role in material selection. While titanium can provide superior performance and durability, its higher cost and the complexities of supply chains present challenges, particularly in the aerospace industry, which is currently experiencing a surge in demand. Steel, being more readily available and economically viable, continues to dominate in sectors where weight is less critical.
Ultimately, the decision between titanium and steel should be guided by a thorough analysis of the application’s requirements, including performance, environmental conditions, and budget constraints. By strategically evaluating these factors, procurement managers can make informed decisions that enhance operational efficiency and product performance.