Blogs
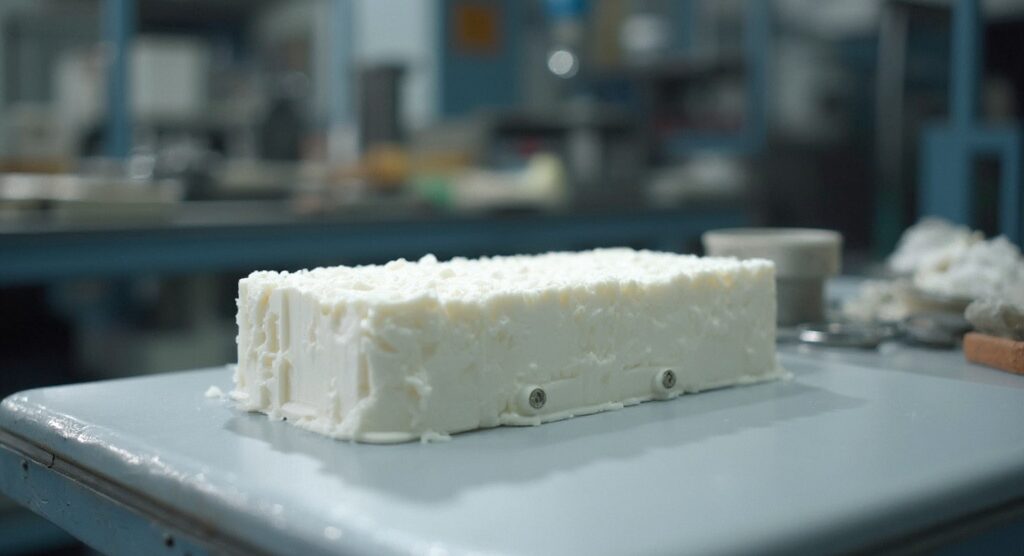
Understanding Beryllium Oxide Ceramic: A Complete Tutorial on Properties and Applications
Introduction
Beryllium oxide ceramic (BeO) stands at the forefront of advanced materials, celebrated for its exceptional thermal and electrical properties that cater to a multitude of industrial applications. With a remarkable thermal conductivity that facilitates efficient heat dissipation, BeO has become indispensable in high-power electronics and automotive technologies, where performance and reliability are paramount. Its ability to withstand extreme temperatures and mechanical stress, combined with resistance to chemical corrosion, further solidifies its status as a critical material in sectors ranging from aerospace to laboratory equipment.
As the demand for high-performance materials continues to surge, understanding the unique characteristics and applications of beryllium oxide, alongside complementary products like Mica Tape, is essential for procurement managers aiming to enhance operational efficiency and ensure safety in their sourcing strategies.
This article delves into the fundamental properties, diverse applications, manufacturing processes, safety considerations, and future trends surrounding beryllium oxide ceramic, providing valuable insights for informed decision-making in the procurement landscape.
Fundamental Properties of Beryllium Oxide Ceramic
Beryllium oxide ceramic, often referred to as BeO, is distinguished by several essential properties that render it an invaluable material for a variety of applications. Notably, it boasts an impressive thermal conductivity of up to 200 W/m·K, facilitating efficient heat dissipation. This characteristic is particularly crucial in the realm of electronics, where excessive heat can precipitate component failure.
As highlighted by Vajdi et al.,
The results showed a significant heat transfer rate, which was attributed to the high thermal conductivity of the mentioned ceramic.
Moreover, the performance of beryllium oxide ceramic demonstrates a remarkable heat transfer enhancement of approximately 100% compared to alumina at a mass flow rate of 97.3 kg/h, underscoring its superior capability in thermal management. Additionally, BeO exhibits exceptional electrical insulation properties, with a dielectric strength reaching approximately 20 kV/mm, making it highly suitable for insulating electronic devices.
Its high melting point, exceeding 2500°C, coupled with remarkable mechanical strength, ensures that it retains structural integrity even under extreme thermal and mechanical stress. Furthermore, the resistance of beryllium oxide ceramic to chemical corrosion significantly enhances its longevity and reliability in demanding environments. Recent studies, including the case study titled ‘Feasibility of Beryllium Oxide Ceramic in Heat Exchangers,’ reaffirm its potential, indicating that beryllium oxide ceramic can outperform traditional materials due to its unique properties.
This study emphasizes the effectiveness of beryllium oxide ceramic in heat exchangers, further confirming its use in advanced technologies. Given these advantages, beryllium oxide ceramic stands as a critical component in advanced electronic uses, warranting its consideration in procurement strategies. Moreover, tape products designed for high-temperature resistance and insulation play a crucial role in enhancing the performance of beryllium oxide ceramic in various applications.
For instance, Insulation Tapes are essential in the construction of coils and capacitors, where their remarkable thermal and insulating properties enhance the performance of beryllium oxide ceramic. These tape products ensure safety and performance in high-temperature environments, making them a valuable addition to any procurement strategy involving BeO. It is also important to note that higher amounts of h-BN (>5 vol%) can decrease bending strength and Vickers hardness due to poor sinterability, providing a balanced view of the material’s properties.
Diverse Applications of Beryllium Oxide Ceramic in Industry
The unique properties of beryllium oxide ceramic are increasingly recognized across multiple industries, particularly in electronics and automotive sectors. Within the electronics field, BeO serves as a vital substrate material for high-power electronic devices, where its exceptional thermal management capabilities, with a thermal conductivity of 15.4 W/(m∙°C) as the temperature increases, are indispensable. Notably, it is extensively utilized in high-frequency microwave components and semiconductor packaging, where efficient heat dissipation directly impacts performance and reliability.
The automotive sector also employs beryllium oxide ceramic in critical applications like sensors and actuators, which demand high-temperature resistance and excellent insulation. Complementing these uses, Mica Tape products, particularly Mica Insulation Tape and Mica Tape for Electrical, offer high-temperature resistance and electrical insulation, making them essential for various electrical engineering purposes, including fire-resistant cables and insulation systems. Their flame resistance and dielectric strength further enhance their suitability in demanding environments, including the aerospace and automotive industries.
Furthermore, the lightweight and high-strength characteristics of BeO make it an ideal selection for aerospace uses, enabling materials to endure extreme environments. The chemical resistance of BeO further enhances its utility in specialized laboratory equipment, ensuring durability and reliability for scientific research endeavors. As market demand for beryllium oxide ceramic continues to rise, especially in the automotive sector, understanding these uses and their implications becomes essential for strategic procurement.
Additionally, the British Geological Survey highlights the importance of political stability in countries with significant beryllium reserves, which can influence supply chain decisions. A mathematical model of BeO slurry flow illustrates its practical uses and results, capturing the dynamics of BeO slurry flow and offering a framework for predicting behavior during casting.
Manufacturing Processes for Beryllium Oxide Ceramic
The manufacturing of beryllium oxide ceramic involves several critical processes, particularly powder processing and sintering. Initially, high-purity beryllium oxide powder is synthesized through various chemical reactions or the thermal decomposition of beryllium salts. This powder is then shaped into the desired form using techniques such as pressing or injection molding.
Following shaping, the components are subjected to a sintering process, where they are heated to temperatures exceeding 1000°C within a controlled atmosphere. This step is vital as it enhances both the density and mechanical properties of the ceramic. Advanced sintering techniques, including hot pressing and hot isostatic pressing, are often employed to further optimize the density and strength of the final product.
Recent evaluations of the insulating performance of metal-insulator-metal (MIM) devices using BeO thin films demonstrate that sintering at elevated temperatures—specifically at 1500 °C—results in significantly low leakage currents of 49 pA at −20 V and 95 pA at +20 V. These findings, measured using a four-probe station system with a semiconductor parameter analyzer, indicate the potential of BeO as an exceptional gate oxide material.
Simultaneously, Insulation Tape products deliver an essential element for high-temperature power insulation, providing exceptional performance in uses spanning from home devices to industrial equipment. Their excellent flame resistance and dielectric strength make them essential for electrical uses, including the manufacture of fire-resistant cables and other critical electrical insulation systems.
For procurement managers, understanding these manufacturing processes, along with the advantages of high-quality insulating materials such as Tape and beryllium oxide ceramic, is crucial for sourcing materials that meet stringent performance specifications. Mica Tape’s specific performance metrics, such as its high dielectric strength and robust flame resistance, further enhance its value in high-temperature uses. As emphasized by S.Y.P., the success of these processes relies on effective supervision, funding acquisition, and a robust methodology.
Safety and Handling Considerations for Beryllium Oxide Ceramic
Non-sparking tools, such as the Beryllium Copper Non-Sparking Wrench, are essential in explosive potential environments. These tools provide significant safety features, minimizing the risk of igniting flammable materials. When selecting suppliers and manufacturers of electrical insulation and high-temperature materials, it is crucial to consider those who offer reliable non-sparking solutions, such as:
- Electrical insulation papers
- High-temperature fabrics
Additionally, procurement managers should be aware of the safety protocols and health risks associated with beryllium handling, ensuring that workplace safety is prioritized. Comprehending these uses and safety features will assist in making informed choices that improve safety in potentially dangerous environments.
Comparative Analysis with Alternative Materials
In the realm of high-performance uses, it is crucial to evaluate materials beyond beryllium oxide ceramic for optimal performance. Among the most common alternatives are:
- Aluminum oxide (Al2O3)
- Silicon carbide (SiC)
- Aluminum nitride (AlN)
However, it is also essential to consider specialized solutions like Domadia’s Tapes, which are engineered for high-temperature resistance and exceptional insulation.
These products are notable for their dependability in diverse uses, from engineering to industrial machinery. Mica Tapes are especially remarkable for their flame resistance and dielectric strength, making them perfect for essential power applications. Aluminum oxide, while remarkable for its outstanding insulation characteristics, has a thermal conductivity that is lower than that of beryllium oxide ceramic.
Interestingly, Tapily has previously compared ALD Al and HfO films and found HfO to generally be about 30 times rougher than Al, highlighting the significance of surface characteristics in material selection. Conversely, silicon carbide is renowned for its exceptional thermal stability, making it a preferred choice in high-temperature environments. Despite its advantages, SiC can be more expensive and presents machining challenges.
Aluminum nitride presents a compelling option with superior thermal conductivity and insulating characteristics; however, it lacks the chemical resistance that beryllium oxide ceramic offers. According to the AFM Surface Morphology Investigation, the surface roughness of ALD BeO and AlN films was measured at:
- 10 nm for ALD BeO
- 5.3 nm for AlN
Each of these materials possesses distinct strengths and weaknesses, as evidenced by the Young’s modulus for the ALD HfO film, reported at 166 ± 10 GPA.
The incorporation of Tapes in this evaluation enhances the discussion around high-temperature electrical insulation solutions. To explore our range of Mica Tapes and learn more about how they can benefit your business, visit our website or contact our expert team today. Aligning the selection process with specific submission requirements, cost factors, and material availability is crucial to ensure the most effective performance outcome.
Future Trends in Beryllium Oxide Ceramic Usage
As technological advancements accelerate, the demand for high-performance materials such as beryllium oxide ceramic is poised for significant growth, particularly in sectors like renewable energy, electric vehicles, and advanced electronics. The market for beryllium oxide is projected to expand at a compound annual growth rate (CAGR) of 9.7% from 2024 to 2030, driven by sustainability trends and regulatory support that further stimulate demand. Innovations in manufacturing processes are anticipated to enhance the efficiency and cost-effectiveness of BeO production, making it more accessible for a wider range of uses.
Simultaneously, the application of high-temperature insulating materials, such as Domadia’s Tape Products, is essential in guaranteeing the reliability and safety of these innovative technologies. Tapes made from mica, including:
- Insulation Tape, which provides excellent electrical insulation and thermal resistance
- Sheet Tape, intended for insulating large flat surfaces
are essential in applications ranging from household appliances to industrial machinery. However, the growing traction of beryllium-free alternatives, driven by health concerns and the development of new formulations for beryllium oxide ceramic materials, could redefine the market landscape.
This shift, as highlighted in recent case studies, underscores the need for procurement managers to adapt their sourcing strategies accordingly, while also considering the robust insulation properties of Mica tapes compared to beryllium oxide. Furthermore, ongoing research into novel uses for beryllium oxide—such as in radiation detection and medical devices—could unlock new market opportunities. Procurement managers must remain vigilant regarding these developments to effectively navigate the challenges and opportunities within an ever-evolving landscape.
To explore our range of Mica Tapes and learn more about how they can benefit your business, visit our website or contact our expert team today.
Conclusion
Beryllium oxide ceramic (BeO) emerges as a cornerstone of advanced materials, demonstrating exceptional thermal and electrical properties that cater to a wide range of industrial applications. Its remarkable thermal conductivity, coupled with high dielectric strength and resistance to extreme conditions, positions BeO as an invaluable asset in high-performance sectors such as electronics, automotive, and aerospace. The ongoing demand for efficient heat management solutions further underscores its relevance, particularly in high-power electronic devices and critical automotive components.
In manufacturing, the intricacies of BeO production—from powder synthesis to sintering—highlight the importance of advanced techniques in optimizing material performance. This knowledge is essential for procurement managers who must navigate the complexities of sourcing materials that meet stringent operational specifications. Safety considerations in handling BeO, alongside the use of complementary products like Mica Tape, are paramount in ensuring safe and effective applications, particularly in environments with high-temperature requirements.
Looking ahead, the future of beryllium oxide ceramic is promising, with anticipated growth driven by innovations in technology and the increasing adoption of electric vehicles and renewable energy solutions. However, the emergence of beryllium-free alternatives presents both challenges and opportunities for procurement strategies. Staying informed about market trends and technological advancements will be crucial for making informed decisions that enhance operational efficiency and safety. As the landscape evolves, the strategic integration of high-performing materials like BeO and Mica Tape will play a pivotal role in meeting the demands of tomorrow’s industries.