Blogs
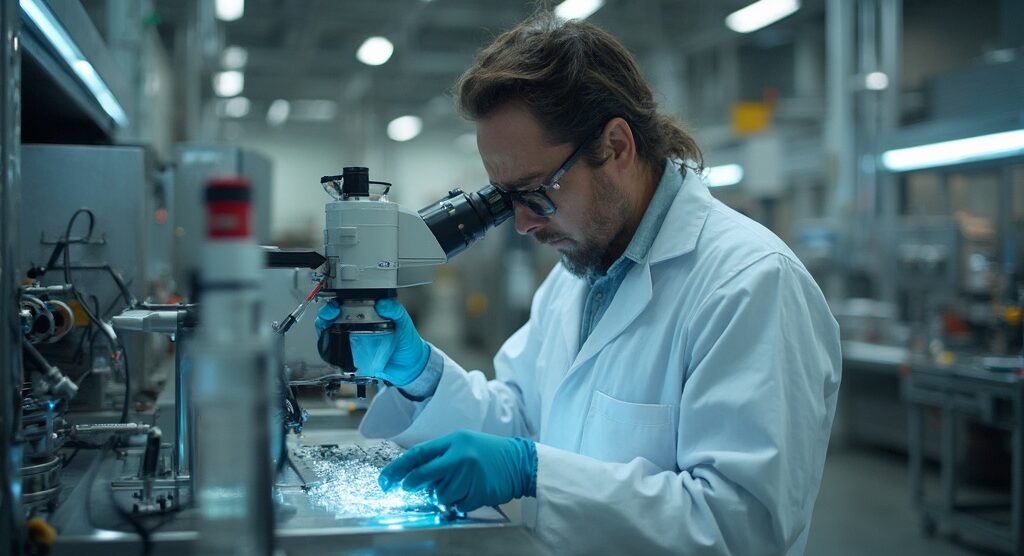
Understanding Titanium Alpha: A Complete Tutorial on Properties and Applications
Introduction
The versatility and performance of titanium alloys make them a focal point in modern manufacturing, particularly across aerospace, medical, automotive, and electronics industries. With their unique alpha and beta phases, titanium alloys can be tailored to meet specific application demands, offering exceptional strength, corrosion resistance, and biocompatibility.
As procurement managers navigate the complexities of sourcing these materials, understanding the mechanical properties, processing techniques, and cost considerations becomes imperative. This article delves into the critical aspects of titanium alloys, exploring their applications, the latest advancements in processing, and future trends that are shaping the industry landscape.
By equipping themselves with this knowledge, procurement professionals can make informed decisions that enhance supply chain efficiency and drive innovation.
Introduction to Titanium: Understanding Alpha and Beta Phases
Titanium exists primarily in two crystalline structures: the titanium alpha phase, which is hexagonal close-packed (HCP), and the beta phase, which is body-centered cubic (BCC). The titanium alpha phase is stable at room temperature and provides excellent strength and corrosion resistance, making it suitable for applications such as aerospace and medical devices. In contrast, the beta phase occurs at higher temperatures and offers improved ductility and formability, making it advantageous for manufacturing processes.
The change between these stages can be managed through metal mixtures and thermal processing, enabling producers to customize titanium-based materials for particular uses. Comprehending these stages is essential for choosing the appropriate metal blend based on performance specifications and environmental factors.
Applications of Alpha-Beta Titanium Alloys in Industry
Alpha-beta metal mixtures are characterized by their remarkable strength-to-weight ratio and outstanding corrosion resistance, rendering them essential in various applications. In the aviation sector, these materials are essential for elements like airframes and engine components, where efficiency and weight minimization are crucial. The market share of alpha-beta metal mixtures in aerospace keeps increasing, demonstrating the industry’s dependence on these substances to improve fuel efficiency and overall aircraft performance.
In the medical field, alpha-beta metal mixtures are increasingly preferred for implants and surgical tools because of their excellent biocompatibility and mechanical strength. Recent advancements in metal mixtures, as emphasized by Rihanna McHendrie, a Materials Engineering graduate, showcase a notable improvement in antimicrobial efficacy compared to conventional metal mixtures utilized in medical implants. McHendrie states, “The metal mixtures created in this project demonstrate a significant improvement in antimicrobial effectiveness compared to the frequently utilized metal blend employed in medical implants.”
This advancement is crucial in reducing infection rates and improving patient outcomes. Furthermore, Dr. Reza Hashemi and his research team are investigating machine learning algorithms to enhance the screening process for hip and knee joint replacements, further highlighting the groundbreaking uses of metal composites in the medical domain.
The automotive sector also capitalizes on the benefits of metal mixtures, employing them in high-performance vehicles for structural parts and exhaust systems, thereby improving durability while reducing weight. Furthermore, the electronics sector benefits from the unique properties of this metal, employing it in the manufacture of connectors and housings that require resilience and lightweight characteristics.
The versatility of titanium alpha materials fosters continued innovation and adoption across these industries, positioning them as a strategic focus for procurement managers aiming to optimize their supply chains and support advancements in technology and performance.
Mechanical Properties of Titanium Alloys
Titanium alpha composites are known for their exceptional mechanical properties, which are critical for a variety of demanding applications. For instance, their tensile strength can surpass 1400 MPa, influenced by the specific composition and the processing techniques employed. Grade 38 metal, which contains 4% aluminum, 2.5% vanadium, and 1.5% iron, exemplifies this with its impressive strength and durability.
This high tensile strength is complemented by outstanding fatigue resistance, making these materials particularly suitable for components subjected to cyclic loading, such as those in aerospace engineering. Furthermore, metal mixtures demonstrate exceptional impact resilience, allowing them to withstand sudden forces without breaking. Their low thermal expansion coefficient and high melting point further enhance their performance, particularly in extreme environments.
Moreover, titanium alpha and its combinations are biocompatible, making them suitable for medical implants such as artificial joints and screws. Mitsuo Niinomi encapsulates the significance of these properties by stating,
The mechanical properties such as tensile characteristics, fracture toughness, fatigue characteristics and so on of various biomedical metal mixtures developed to date will be described in this paper in as much detail as possible.
Moreover, a recent study titled Cold Rolling Deformation and Annealing Behavior of a β-Type Ti–34Nb–25Zr Metal for Biomedical Applications has demonstrated how processing techniques can significantly improve mechanical properties, further validating the suitability of these materials in biomedical contexts.
Besides their biomedical uses, metal mixtures are increasingly utilized in the automobile sector for engine components and other parts to decrease weight and enhance fuel efficiency. For procurement managers, comprehending these mechanical traits, along with the various uses, is crucial when assessing potential suppliers and choosing the most suitable metal for particular purposes.
Processing Techniques for Titanium Alloys
Various techniques can be used to process titanium alpha alloys, each providing distinct advantages tailored to specific applications. Among these methods, forging stands out for its ability to enhance the mechanical properties of this metal, making it a preferred choice for critical components in aerospace applications. While casting is less commonly utilized for this metal due to its associated challenges, it offers the advantage of producing complex geometries, making it suitable for lower volume production runs.
Furthermore, additive manufacturing, often referred to as 3D printing, is rapidly gaining traction in processing of the metal. This technique allows for rapid prototyping and the customization of parts, addressing the growing demand for tailored solutions in various industries. A significant case study is the use of electropolishing, which effectively eliminates the titanium alpha layer from the metal, improving surface smoothness and enhancing corrosion resistance.
This process not only eliminates surface flaws but also greatly enhances the fatigue life and biocompatibility of metal components, making it essential for applications in medical manufacturing. With the current landscape indicating a shift towards advanced processing techniques, it is crucial for procurement managers to understand these methods. The choice of processing technique can significantly influence material costs, lead times, and overall performance, ultimately impacting the success of projects.
Additionally, a robust supplier network supports the adoption of these advanced techniques, providing essential services and ensuring that procurement strategies align with the latest industry trends and technological advancements. Incorporating relevant statistics on the usage of metal processing techniques will further enhance credibility and provide a quantitative perspective on the topic.
Cost Considerations in Titanium Procurement
The cost of metal alloys is influenced by a variety of factors, including raw material prices, processing techniques, and prevailing market demand. Procurement managers should recognize that this metal tends to be more costly than alternative metals due to the complexities involved in its extraction and processing. In 2021, foreign direct investment (FDI) into the U.S. aviation industry alone reached nearly US$22 billion, highlighting the significant economic interest in this sector and its influence on titanium alpha prices.
Additionally, ongoing aircraft modernization programs in North America are driving demand, which can lead to price fluctuations. The aviation sector is projected to grow at a CAGR of 4.1% during 2022-2027, further emphasizing the importance of these programs in shaping market trends. Staying abreast of global supply chain dynamics is crucial for managing procurement costs effectively.
Strategies for cost-effective procurement include:
– Fostering long-term relationships with suppliers
– Negotiating bulk purchase agreements
– Considering alternative alloys that may offer comparable performance at lower costs
For instance, the Defense Research and Development Organization (DRDO) stated, “In June 2021, Mikoyan MIG launched 3 New Stealth Aircraft. DRDO has introduced a High Strength Metastable Beta Titanium Alloy, referred to as titanium alpha, which includes Vanadium, Iron, and Aluminum, Ti-10V-2Fe-3Al on an industrial scale for uses in structural forgings for the aviation industry. This innovation could potentially impact pricing strategies in the aerospace sector.”
By thoroughly grasping these cost factors and market dynamics, managers can make strategic procurement choices that align with their budgetary limitations while capitalizing on emerging opportunities in the metal market.
Future Trends in Titanium Alloys
The metal alloy market is undergoing significant transformation, propelled by technological advancements and surging demand across various sectors. A prominent trend is the increasing implementation of additive manufacturing, which facilitates the creation of intricate geometries unattainable through conventional production methods. This innovation is particularly pivotal in the aerospace and automotive industries, where the emphasis on lightweight materials enhances fuel efficiency and performance.
Furthermore, sustainability has emerged as a crucial factor, with a growing emphasis on recycling metal scrap to mitigate environmental impacts and reduce costs. Notably, a case study reveals a shift in consumer behavior, with younger consumers increasingly prioritizing eco-friendly materials and ethical sourcing, compelling manufacturers to innovate and adopt greener practices. Furthermore, regional hotspots for the metal composite market, including:
- North America
- Europe
- Asia-Pacific
- Latin America
- Middle East & Africa
emphasize the varied dynamics at work.
As the market evolves, procurement managers must remain vigilant about these trends, enabling them to refine their sourcing strategies and capitalize on emerging opportunities. With projections indicating a 4% annual growth in Germany’s titanium alpha alloys market, the necessity to adapt and innovate becomes ever more pressing. Key players such as:
- Time
- Confluent Medical
- Allegheny Technologies
are contributing uniquely to this competitive landscape, providing potential sourcing partners for forward-thinking procurement managers.
Conclusion
The exploration of titanium alloys reveals their unmatched versatility and essential role in various industries, including:
- Aerospace
- Medical
- Automotive
- Electronics
The distinct alpha and beta phases of these alloys allow for tailored mechanical properties, enhancing their performance in demanding applications. Procurement managers must grasp these intricacies to select the appropriate alloys that align with their specific requirements, ensuring optimal outcomes in their projects.
Moreover, the advancements in processing techniques such as:
- Additive manufacturing
- Forging
- Electropolishing
are reshaping the landscape of titanium procurement. These innovations not only improve product performance but also influence cost structures and supply chain dynamics. By understanding these processing methods, procurement professionals can make informed decisions that enhance efficiency and reduce lead times.
Cost considerations remain pivotal in the procurement of titanium alloys, as fluctuations in market demand and raw material prices can significantly impact budgets. Strategic relationships with suppliers and the exploration of alternative alloys can mitigate these costs, allowing for more effective procurement strategies.
Lastly, staying attuned to future trends, including sustainability efforts and technological advancements, is crucial for procurement managers. Embracing these changes will not only enhance competitive advantage but also align procurement strategies with evolving market demands. By leveraging the insights gained from this article, procurement professionals can navigate the complexities of sourcing titanium alloys, driving innovation and supporting their organizations’ goals.