Blogs
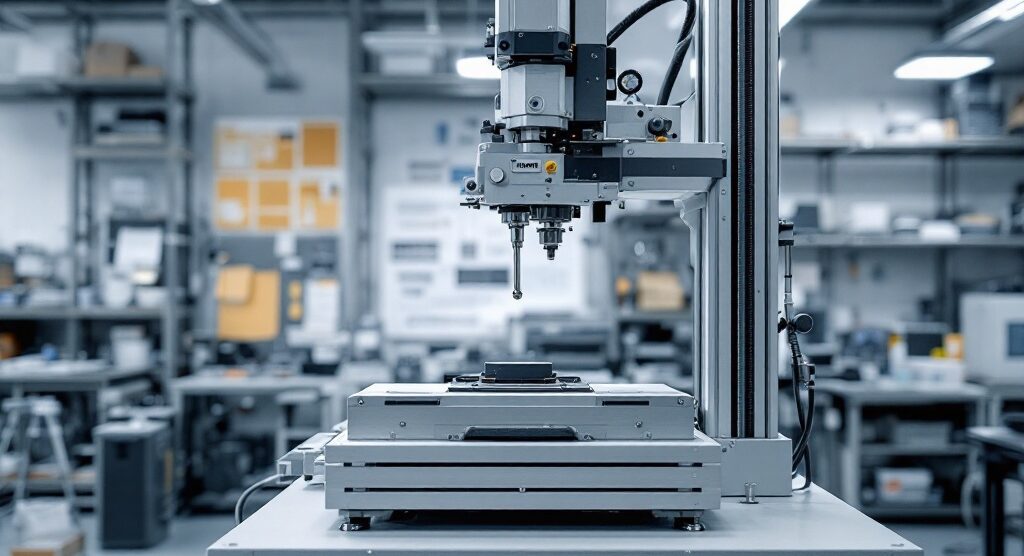
Tensile Testing of Metals: An In-Depth Tutorial for Engineers
Introduction
In the realm of material science and engineering, tensile testing stands as a cornerstone method for evaluating the mechanical properties of materials, particularly metals. This critical assessment not only measures strength and ductility but also informs engineers about a material’s behavior under stress, ensuring that the selected materials can withstand the demands of their applications.
As industries evolve, the integration of advanced technologies into tensile testing procedures enhances data acquisition and analysis, paving the way for more accurate and reliable results. With the stakes high in material selection, quality assurance, and design validation, understanding the intricacies of tensile testing becomes paramount for professionals dedicated to maintaining excellence in engineering practices.
This article delves into the fundamental aspects of tensile testing, offering a comprehensive overview of procedures, influencing factors, and the essential standards that govern this vital process.
Introduction to Tensile Testing: Understanding the Basics
Tensile testing of metals serves as a fundamental mechanical evaluation method that determines the strength and ductility of substances. This test involves subjecting a sample to a precisely controlled stretching load until it fails, providing critical insights into its mechanical properties. K.K. Chawla emphasizes the importance of tensile testing of metals in the Encyclopedia of Condensed Matter Physics, stating,
Tensile test is one of the most simple and important tests that can be conducted on a substance to obtain its mechanical characteristics.
The key parameters assessed during this process encompass:
- Yield strength
- Ultimate breaking strength
- Elongation
Understanding these properties is essential for engineers involved in tensile testing of metals, as they assess materials for diverse applications and must ensure that selected materials can endure specified loads without succumbing to failure.
Recent advancements in stress evaluation techniques, including new universal systems capable of assessing forces up to 2000 kN, are expected to enhance machine capabilities and integrate digital technologies, thereby improving data acquisition and analysis. Furthermore, a case study on the created ANN model for synthetic fiber ropes demonstrates limitations in forecasting beyond the examined data range, indicating future research directions that could also be relevant to strength testing. As the field evolves, it is crucial for professionals to stay informed about the latest research on tensile testing of metals, especially regarding its implications for tensile strength and ductility in practical engineering applications.
Tensile Test Procedures: Step-by-Step Guide
Sample Preparation: Begin by cutting the metal sample to the specified dimensions, adhering strictly to the guidelines outlined in relevant standards such as ASTM D638, which applies to substances up to 14 mm thick. Precision in this step is crucial to ensure the reliability of test results.
Marking: Accurately mark the gauge length and other critical measurement points on the sample. This step is essential for ensuring that measurements taken during evaluation are reflective of the material’s properties.
Setup: Install the sample in the stress examination machine with careful attention to alignment. Proper alignment is essential to prevent bending moments that could skew test results. Recent advancements in testing machine technology, particularly the use of hydraulically actuated grips, are critical for enhancing grip strength when assessing advanced high-strength steels (AHSS). This is particularly important as AHSS requires more grip pressure to prevent slippage during testing.
Testing: Gradually apply stretching force to the sample until failure occurs. Throughout this process, record the load and corresponding elongation at regular intervals. This data is critical for understanding material behavior under stress, particularly during tensile testing of metals.
Data Analysis: After evaluation, compute the yield capacity, ultimate breaking force, and elongation from the recorded data using standard formulas. It is important to note that tensile testing of metals is typically performed at ‘quasi-static’ speeds. However, case studies, such as the one examining the influence of test speed on stress-strain curves during tensile testing of metals, have shown that higher test speeds can result in increased strength. This highlights the necessity for improved equipment and data collection methods to accurately characterize tensile responses in real-world applications such as stamping and crash events. Utilizing software like Maxtest can streamline operations by enhancing data analysis and ensuring compatibility with various material assessment machines, which is vital for maintaining efficiency and effectiveness in your processes.
Key Factors Influencing Tensile Test Results
Tensile testing results can be significantly influenced by several critical factors:
Sample Size: The dimension of the specimen plays a crucial role in determining its mechanical properties. Larger samples often show different strength characteristics compared to smaller specimens due to scaling effects. Recent research indicates that machining effects are more pronounced in smaller specimens, which can lead to discrepancies in yield capacity and ductility measurements.
Sample Shape: The geometry of the sample affects how stress is distributed throughout the material, impacting both stress concentration and failure modes. Variations in shape can lead to different fracture morphologies, including the presence of smooth regions and vein patterns in compressive fractures, particularly in bulk metallic glasses (BMGs). These observations emphasize the significance of considering sample shape in relation to the outcomes of tensile testing of metals.
Application Speed: The rate of load application is another crucial factor affecting tensile strength measurements. Research, including one on dynamic evaluation of common structural steels like S355JR and S235JR, reveal that increased strain rates correlate with heightened strain rate sensitivity, resulting in reduced ductility. The evaluation was conducted at varying strain rates from 0.001 to 10 s, demonstrating a clear trend of increased strain rate sensitivity and a reduction in ductility with higher strain rates. Conversely, a slower evaluation speed can yield more consistent and precise outcomes, minimizing the effects of strain rate on substance behavior.
Environmental Conditions: External factors such as temperature and humidity can alter substance properties, necessitating strict control during assessment to ensure valid results. For instance, the yield resistance of an alloy extruded at 1300°C was documented at 807 MPa with an elongation to failure of 2.6% at room temperature, highlighting the effect of environmental conditions on stress results.
In summary, comprehending how sample size and shape, evaluation speed, and environmental conditions affect tensile testing of metals results is crucial for procurement managers aiming to make informed choices in selection and assessment protocols.
The Importance of Tensile Testing in Engineering Applications
Stress testing is essential in engineering applications for numerous reasons:
Substance Selection: Engineers utilize stress test data to recognize and choose substances that not only fulfill design requirements but also function dependably under expected stress conditions. This data is particularly critical as maximum strength values for face-centered cubic (FCC) metal films can range from μ/40 to μ/120, significantly surpassing those for hard-drawn metals and approaching nearly 100 times the strength of annealed bulk metals. This comparison highlights the significance of choosing the appropriate materials for particular engineering applications.
Quality Assurance: Performing regular strength tests is essential for confirming that materials comply with rigorous industry standards. This practice mitigates the risk of failure in final products, enhancing overall safety and performance. The accuracy of tensile testing of metals hinges on the precision of the measurement equipment, including load cells and extensometers, which must be meticulously calibrated to yield reliable results. The importance of these assessment procedures is further backed by results showing that the P-values of various laboratories conducting these analyses were consistently below 0.05, indicating statistically significant differences in strength data, as noted by Ahmad Adlie Shamsuri.
Design Validation: Strength assessment serves to validate design assumptions, confirming that components will perform as expected under load conditions. This guarantee is essential for engineers in creating products that not only fulfill client expectations but also adhere to industry regulations, thus promoting confidence in the engineering process.
Research and Development: In the field of innovation, tensile testing of metals is vital for evaluating strength and advancing new substances and processes. It offers crucial insights into substance behavior under stress, guiding engineers in selection and leading to advancements in engineering practices. Significantly, recent research has demonstrated that stringent evaluation protocols are crucial in the sector, as exemplified in the case study titled ‘Importance of Material Strength Assessment,’ which emphasizes its role in characterizing mechanical properties and ensuring quality assurance.
In conclusion, material strength assessment is a fundamental aspect of engineering, enabling informed decision-making in material choice, ensuring product quality, validating designs, and propelling research and development initiatives.
Standards and Guidelines for Tensile Testing
Tensile evaluation is a critical process governed by several pivotal standards and guidelines that ensure the accuracy and reliability of results. Among these:
- ASTM E8 / E8M: This standard delineates the methodologies for conducting tensile tests on metals, detailing the necessary equipment and procedures required for accurate assessments. Compliance with ASTM E8 is essential for the performance verification of machinery, thereby ensuring adherence to established industry benchmarks.
- ISO 6892: This international standard offers extensive guidelines for evaluating the strength of metallic materials, highlighting the significance of consistency in assessment methods across different laboratories. Recent changes in the ISO 6892 guidelines reflect ongoing efforts to enhance the precision and relevance of evaluation methods in line with evolving industry needs, thereby ensuring that procurement managers are equipped with the latest standards for effective decision-making.
- EN 10002: This European standard emphasizes strength assessment under various conditions, acting as an essential reference for conformity in the European market.
Adhering to these standards is not merely a procedural formality; it is a strategic necessity for the tensile testing of metals. Failure to comply can lead to material failures, economic repercussions, and significant regulatory challenges, as highlighted in various case studies. Furthermore, with international orders being delivered via courier services taking 4-7 weeks, understanding compliance timelines is crucial for procurement managers to ensure timely delivery and quality assurance.
As noted by TensileMill CNC, “We are more than just a service provider. We are your partner to ensure the highest standards of tensile evaluation accuracy and reliability.” This partnership is vital in navigating the complexities of compliance and testing. The implications of non-compliance are profound, often resulting in safety hazards, product recalls, and financial losses.
Thus, understanding and implementing these key standards is vital for procurement managers aiming to maintain operational integrity and product quality.
Conclusion
Tensile testing is an essential component of material science and engineering, providing critical insights into the mechanical properties of materials, particularly metals. By meticulously following standardized procedures—from sample preparation to data analysis—engineers can accurately assess yield strength, ultimate tensile strength, and ductility. Understanding the factors that influence test results, such as sample size, shape, testing speed, and environmental conditions, is imperative for making informed decisions in material selection and quality assurance.
As industries continue to evolve, the integration of advanced technologies into tensile testing enhances the reliability and accuracy of results. This progression not only improves data acquisition but also supports the development of innovative materials and processes. Compliance with established standards, such as ASTM E8 and ISO 6892, ensures that testing practices are consistent and aligned with industry benchmarks, safeguarding against material failures and economic repercussions.
Ultimately, tensile testing is more than a procedural requirement; it is a strategic necessity for procurement managers and engineers dedicated to excellence in their fields. By prioritizing rigorous testing protocols and staying abreast of technological advancements and standards, professionals can ensure the integrity of materials and the safety of their applications, thereby fostering trust and reliability in engineering practices. Embracing the complexities of tensile testing is vital for driving innovation and maintaining competitive advantages in a demanding marketplace.