Blogs
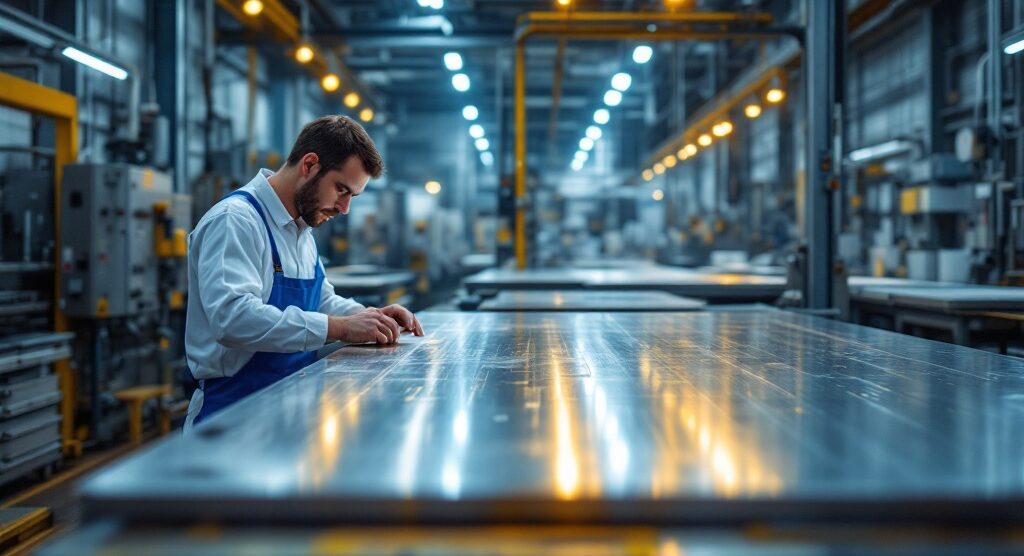
Understanding Monel Grades: A Comprehensive Tutorial on Properties and Applications
Introduction
Monel, a versatile nickel-copper alloy, stands at the forefront of materials engineering, renowned for its exceptional performance in demanding environments. With its unique composition, typically comprising around 67% nickel and 30% copper, Monel offers unparalleled corrosion resistance and strength, making it a critical choice for industries such as:
- Marine
- Chemical processing
- Aerospace
As procurement managers navigate the complexities of material selection, understanding the nuances of Monel’s various grades, manufacturing processes, and economic implications becomes essential. This article delves into the properties, applications, and future trends of Monel alloys, providing valuable insights for informed decision-making in procurement strategies.
What is Monel? An Overview of the Alloy
This nickel-copper alloy is distinguished by its remarkable corrosion resistance and superior strength, typically composed of approximately 67% nickel and around 30% copper, alongside trace amounts of iron, manganese, carbon, and silicon. This composition is crucial for procurement managers, as the high nickel content significantly contributes to the material’s performance in demanding environments. Since its inception in the early 20th century, this alloy has gained prominence in sectors where durability is paramount, particularly in marine, chemical, and aerospace applications.
Its unique ability to endure both acidic and alkaline environments ensures that this metal maintains structural integrity and reliability under challenging conditions. Furthermore, in industries dealing with explosive substances, Non-Sparking Tools are crucial alternatives, ensuring safety and compliance. Procurement managers should also take into account the economic factors influencing the prices of Monel grades, as rising unemployment and interest rates have negatively impacted the manufacturing sector, affecting costs.
Furthermore, it is essential to investigate pricing and inventory information for Beryllium Copper Strips, which are vital for uses demanding electrical conductivity and corrosion resistance. Suppliers of electrical insulation products, including high-temperature fabrics and papers, should also be identified to ensure comprehensive procurement strategies. As mentioned by Terence Bell in his examination of the history and uses of these metals, grasping these dynamics is crucial for making informed choices in material selection.
Exploring Monel Grades: Properties and Applications
Certain alloys are offered in various grades, each designed to satisfy the requirements of particular uses:
- Alloy 400: This is the most widely utilized grade, renowned for its remarkable resistance to corrosion across a diverse range of environments, including seawater and various acids. Its exceptional durability makes it a prime choice for marine applications, chemical processing, and the oil and gas sectors, where reliability is critical. A case study on alloy 400 highlights its exceptional corrosion resistance, particularly in seawater and acidic conditions, making it a preferred material in aggressive environments.
- K-500: Enhanced by the addition of aluminum and titanium, this grade offers superior strength and hardness. Alloy K-500 is especially appropriate for uses that require high tensile strength and resistance to stress corrosion cracking, making it perfect for essential components such as pumps and valves in challenging environments.
- Monel 404: Although less common than the previously mentioned grades, this alloy caters to specialized uses needing lower strength along with enhanced machinability. It is often selected for the manufacture of components that necessitate ease of shaping and forming, thus enhancing production efficiency.
- R-405: Similar to alloy 400 in its corrosion-resistant properties, R-405 is specifically designed to offer better machinability. This makes it a preferred choice for producing fasteners and various components where machining ease is paramount, thereby optimizing manufacturing processes.
- Monel 450: Recognized for its outstanding corrosion resistance and high strength, this material is often utilized in challenging settings like chemical processing and aerospace applications, where performance under strain is essential.
It’s crucial to mention that these materials are deemed pricey, with its piping being three times more expensive than comparable carbon steel piping. This economic consideration is crucial for procurement managers when assessing resources for their projects.
By comprehensively understanding monel grades and their associated costs, procurement managers can strategically align their sourcing decisions with the unique requirements of their projects, ensuring both optimal performance and cost-effectiveness.
The Manufacturing Process of Monel
The manufacturing process of monel grades includes several critical steps—melting, casting, and forming—that are essential for producing high-quality materials. At first, unrefined substances, mainly nickel and copper, undergo high-temperature melting in a furnace, resulting in a liquid mixture. This alloy is then cast into predefined shapes, such as ingots or billets, facilitating uniformity and quality in the final product.
Following the casting stage, the material undergoes various forming processes, including rolling, forging, or extrusion, to achieve specified dimensions and enhanced properties. Throughout these stages, rigorous quality control measures are paramount, ensuring that each batch adheres to stringent specifications and industry standards. For instance, the case study titled ‘Optimal Machining Parameters for Monel Grades 400 Superalloy‘ highlights the application of finite element method (FEM) and other analytical techniques to optimize machining parameters while considering carbon emissions, providing a real-world example of quality control in the production of monel grades.
Additionally, historical data from 2011 to 2023, with forecasts extending to 2033, illustrate the evolution of manufacturing processes and market trends. Specific quality control standards, such as ISO 9001, are commonly implemented in the production of monel grades to ensure consistency and reliability. As highlighted in industry analyses, the Marine Engineering sector represented approximately 41% of the global metal market in 2023, underscoring the significance of dependable manufacturing processes.
Procurement managers can leverage an understanding of these manufacturing steps and associated quality assurance practices to evaluate suppliers effectively, ensuring they meet both operational and regulatory requirements. As one specialist in the area noted, ‘It is resistant to corrosion and acids, and certain metal mixtures can endure a blaze in pure oxygen,’ emphasizing its distinctive characteristics that are essential in diverse uses.
Common Applications of Monel in Industry
Certain alloys are highly regarded across multiple industries due to their distinctive properties, which enhance performance and durability in demanding environments. Key applications include:
- Marine Engineering: Monel’s remarkable resistance to seawater corrosion positions it as a preferred material in shipbuilding, submarines, and offshore drilling platforms. Its performance in these applications reflects significant advancements in material science, contributing to safer and more efficient marine operations.
- Chemical Processing: The resilience of monel grades in acidic environments makes these metals invaluable for manufacturing equipment such as reactors, heat exchangers, and valves. This capability is critical in maintaining operational integrity in chemical plants, where equipment is regularly exposed to harsh conditions.
- Aerospace: The remarkable strength and corrosion resistance of monel grades make them essential for components in aircraft engines and turbine systems. As mentioned by Christopher Farnin, “The results of this work offer substantial contributions to the comprehension of this material’s solidification behavior, and assist in clarifying how composition can be managed to design microstructures and their resulting characteristics.” The elemental composition of polished and laser-ablated alloy 400 primarily consists of nickel and copper, with small amounts of carbon, iron, manganese, oxygen, silicon, and sulfur. These characteristics are vital in ensuring safety and performance in aerospace uses.
- Oil and Gas: Due to its durability under high-pressure and high-temperature conditions, monel grades of this alloy are preferred for components used in extraction and refining processes. Its reliability in these demanding applications underscores its importance in the oil and gas sector.
- Food Processing: In the food sector, equipment that must resist corrosion while maintaining sanitary conditions often utilizes monel grades, a type of nickel-copper alloy. Its properties ensure compliance with health standards, making it a trusted material in food manufacturing operations. Moreover, the use of optimization methods, as illustrated in the case study of PSO for AISI 4340 steel, emphasizes the potential for improving the performance of these materials through advanced manufacturing processes.
Advantages and Disadvantages of Using Monel
These metal mixtures offer several important benefits that render them a favored selection in diverse sectors:
Corrosion Resistance: This material is famous for its outstanding capacity to withstand corrosion in severe conditions, especially in maritime uses. This characteristic markedly reduces maintenance costs and significantly extends the lifespan of components, which is critical for organizations operating in corrosive settings. In comparison, copper nickel mixtures also exhibit high resistance to corrosion in marine environments, making them another viable choice for critical uses. A case study demonstrates that this metal surpasses stainless steel, which fluctuates in performance depending on its grade, supporting its reputation as a superior material for marine uses because of its resistance to seawater corrosion.
Thermal and Electrical Conductivity: Unlike stainless steel, both this metal and copper nickel composites excel in thermal and electrical conductivity, making them beneficial for uses requiring efficient heat transfer and electrical performance. This property is crucial for industries where temperature regulation and electrical reliability are essential.
Ductility and Ease of Fabrication: Copper nickel mixtures are known for their good ductility and ease of fabrication, attributes that are advantageous when designing complex components. This material also provides remarkable strength and durability, guaranteeing that components preserve their integrity over time, even in demanding situations.
Antimicrobial Properties: A significant benefit of copper nickel compositions is their antimicrobial characteristics, which render them appropriate for uses where cleanliness is crucial. This property can significantly influence procurement decisions in industries that prioritize cleanliness and infection control, such as healthcare.
Conversely, several disadvantages must be considered:
Cost: One of the primary drawbacks of this alloy is its higher cost compared to standard stainless steels. Material cost plays a significant role when selecting between nickel-copper combinations, which are generally less expensive, albeit with different performance characteristics. The price differential can pose challenges for budgeting and project planning, as procurement managers must weigh the immediate financial implications against long-term benefits.
Machining Difficulty: Certain nickel-copper materials are generally harder to machine than softer metals, which can lead to increased manufacturing costs and require specialized tools and processes, complicating production timelines. In contrast, the simplicity of production for copper nickel materials may alleviate some of these difficulties.
Limited Availability: Depending on the specific grade, this material can have restricted accessibility in the market. This scarcity may affect supply chain logistics, making it essential for procurement managers to plan accordingly to avoid potential delays in production.
In summary, while the advantages of these alloys—such as exceptional corrosion resistance, high strength, and thermal and electrical conductivity—are compelling, the associated challenges, including higher costs and machining difficulties, necessitate careful consideration in procurement decisions. The inclusion of antimicrobial properties in copper nickel mixtures further enhances their appeal in specific applications, making them a strong contender in procurement discussions.
Future Trends in Monel Alloy Use
As industries develop, the demand for these alloys is set for significant growth across multiple sectors. Notably, several key trends are emerging:
- Increased Use in Renewable Energy: The global shift towards renewable energy sources positions this material as essential due to its superior corrosion resistance. These properties make it particularly suitable for uses in offshore wind turbines and solar panels, where durability is paramount in harsh environments. With Asia-Pacific witnessing the quickest growth in the alloy market, this trend is anticipated to increase.
- Advancements in Aerospace Technology: Ongoing innovations in aerospace technology are likely to broaden the uses of the alloy. With its strength-to-weight ratio and resistance to extreme temperatures, these alloys are becoming increasingly relevant in the design and manufacturing of next-generation aircraft and spacecraft, supporting their performance and safety requirements.
- Sustainability Initiatives: As industries prioritize sustainability, the demand for these materials may rise in recycling processes and eco-friendly manufacturing practices. Its durability and recyclability correspond flawlessly with contemporary sustainability objectives, establishing it as a favored option for eco-conscious purchasing strategies.
However, possible market disruptions may emerge from alternative substances contesting the applications of monel grades, especially in cost-sensitive industries. For instance, in Europe, alloy prices rose due to increasing raw material costs and recessionary fears, as highlighted in the Q3 2022 case study. By remaining attuned to these trends, procurement managers can strategically align their sourcing practices to effectively meet the anticipated demands of the market, ensuring they are well-prepared to leverage the unique properties of monel grades in future applications.
Conclusion
Monel alloys represent a critical material choice for procurement managers navigating the complexities of modern engineering challenges. With their unique composition and outstanding properties, including exceptional corrosion resistance and high strength, Monel grades such as Monel 400 and Monel K-500 are indispensable in industries ranging from marine to aerospace. Understanding the intricacies of various Monel grades and their applications enables informed decision-making that aligns with both performance requirements and budget considerations.
The manufacturing process of Monel, characterized by rigorous quality control and advanced techniques, underscores the importance of selecting reliable suppliers who adhere to industry standards. As highlighted throughout the article, the economic implications of using Monel must be carefully evaluated against its long-term benefits, particularly in demanding environments where durability and reliability are paramount.
Looking ahead, the evolving landscape of material science points to exciting trends that will drive the demand for Monel alloys, particularly within renewable energy and aerospace sectors. By staying abreast of these developments and understanding the advantages and challenges of Monel, procurement managers can strategically position their organizations to harness the full potential of this remarkable alloy, ensuring optimal performance in future applications. The insights presented in this article serve as a valuable resource for making informed procurement decisions that will stand the test of time.