Blogs
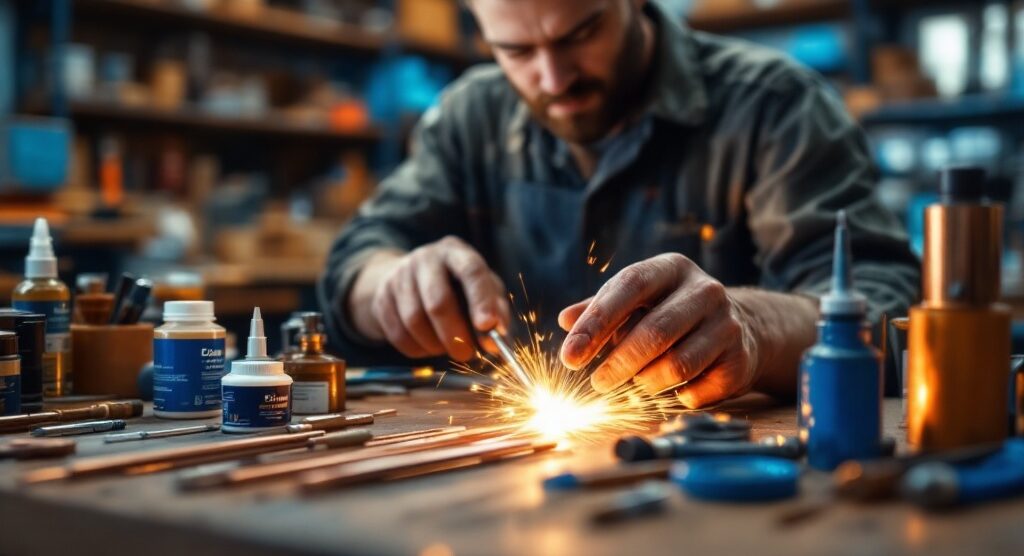
How to Determine the Right Braze Melting Point for Your Project
Introduction
The art of brazing is a critical skill in the realm of metal joining, where precision and material science converge to create strong, durable bonds. Understanding the melting points of various brazing materials is not merely an academic exercise; it is a strategic necessity that directly influences the performance and reliability of joints in applications ranging from aerospace to automotive industries.
As technology advances, so too does the complexity of materials and processes, making it essential for procurement managers to navigate the intricacies of melting point selection.
This article delves into the foundational aspects of brazing, exploring the significance of melting points, the implications of material choices, and the best practices that can enhance joint integrity.
Through a comprehensive examination of common pitfalls and innovative solutions, readers will gain valuable insights into optimizing their brazing processes to achieve superior outcomes.
Understanding Brazing: The Importance of Melting Points
Brazing is an advanced metal-joining method that depends on the regulated liquefaction of a filler substance to connect two or more base substances effectively. A fundamental principle of this process is that the braze melting point of the brazing filler must be lower than that of the base substances. This consideration is crucial, as choosing a suitable fusion temperature directly affects the connection’s strength and overall integrity.
A strategically chosen fusion point ensures optimal flow and penetration of the filler while maintaining the mechanical properties of the base materials. This method is backed by recent developments in brazing technology, which highlight accuracy in temperature selection to achieve strong and dependable connections. For instance, studies have shown that mechanical properties—particularly tensile and shear strength—are significantly affected by the filler composition and melting range.
One relevant case study, titled ‘Influences of Sn on the Mechanical Properties of Connections Brazed by Ag Filler Metals,’ illustrates that while the shear strength of brazed connections improves with increased Sn content, an excess can lead to brittleness due to the formation of undesirable phases. The study highlights that shear strength initially increases with Sn content but decreases when Sn exceeds optimal levels, which is critical for ensuring joint reliability. Furthermore, the energy consumption for depositing 1 kg of zinc filler using a high-temperature process is 269 KJ, emphasizing efficiency considerations in the joining process.
Additionally, Pashkov et al. noted, ‘To solve the high brittleness and poor formability problems of the Cu-P-Sn filler metals with a relatively high content of Sn, we prepared amorphous Cu-P-Sn (P14 filler metals) by the rapid condensation method.’ Moreover, while working in potentially explosive environments, the integration of Non-Sparking Tools is essential for safety during joining processes.
For example, using non-sparking wrenches and screwdrivers can prevent ignition risks in volatile conditions. In conjunction with these tools, Domadia’s Mica Tapes offer high-temperature electrical insulation solutions, ensuring reliability and safety throughout the joining process. To explore our range of Mica Tapes and learn more about how they can benefit your business, visit our website or contact our expert team today.
Therefore, understanding and selecting the appropriate braze melting point is not merely a technical detail; it is a strategic decision that can markedly enhance the performance and durability of your brazed joints.
Exploring Different Brazing Materials and Their Melting Points
A thorough understanding of common joining materials is essential for effective metal union. Silver, copper, and aluminum alloys are frequently used, each presenting unique melting points and properties tailored for specific applications. Silver joining alloys typically have a braze melting point that falls within the range of 600°C to 800°C, making them ideal for scenarios that demand high strength and excellent thermal conductivity.
In contrast, copper alloys generally have a braze melting point of approximately 900°C, making them suitable for joining copper components, where robustness is critical. Significantly, Beryllium Copper, known for its remarkable load-bearing ability and excellent thermal conductivity, is especially beneficial for aerospace and precision applications, positioning it as a top choice for joining in these fields. Aluminum joining materials, which have a braze melting point that ranges from 450°C to 600°C, are particularly advantageous for lightweight applications.
It is essential to observe that the spacing for welding should be small, typically around 50–100 μm, highlighting the accuracy needed in these applications. Furthermore, EADS IWG (now Airbus) has developed a joining technology for C/SiC to metal, known as ‘SiCBraze,’ which is utilized in orbital propulsion systems, such as small thrusters for satellites, illustrating advanced applications in aerospace. Additionally, laser welding has emerged in the automotive industry, allowing for precise control over the joining process and producing high-quality joints with reduced porosity and cracking, despite its high capital costs.
In the context of ensuring safety and performance in high-risk environments, the use of high-quality insulation sleeves with features such as high dielectric strength, flame retardance, flexibility, and abrasion resistance becomes critical. These insulation sleeves not only protect electrical components but also contribute to the overall integrity of metal joining processes by minimizing the risk of electrical breakdown and enhancing the durability of connections. Recognizing these differences and progress is essential for choosing the suitable substance that fulfills your project’s needs, enhancing both performance and efficiency in the joining process.
Factors to Consider When Choosing a Brazing Melting Point
Choosing the suitable joining temperature is essential, particularly when considering the braze melting point and the thermal characteristics of the base materials involved. These characteristics greatly influence the selection of the braze melting point and ultimately affect the effectiveness of the connection. For applications where the connection will encounter elevated temperatures, such as the use of active brazing filler alloy (Ag–26.7Cu–4.5Ti; Ticusil), which infiltrates deeply into the C/C composite substrate after 300 s at 800 °C, it is often essential to consider the braze melting point to maintain integrity and functionality.
Moreover, factors such as the operational environment and any pertinent regulatory requirements must also be carefully assessed. For instance, silver-based alloys, while common, face limitations in high-temperature environments and are prone to chloride-ion-induced corrosion, which can compromise joint durability. In contrast, copper nickel alloys offer superior corrosion resistance and mechanical properties in marine environments, making them a preferred choice for certain applications.
Additionally, the high-temperature resistance of Domadia’s Mica Tapes, which feature excellent dielectric strength and flame resistance, provides an excellent solution for insulation in these challenging applications, ensuring reliability in critical aerospace and automotive environments. The differences in production methods of alloys, such as Alloy 47XD, which has a lamellar structure produced by powder metallurgy, and Alloy 48-2-2, made by electron beam remelting with increased ductility, are relevant when determining the braze melting point. Recent research has demonstrated that substances such as the Ti–Zr system can produce promising filler metals with a lower braze melting point, thus broadening choices for high-temperature applications.
This is supported by case studies indicating the potential for developing new filler metals that are particularly effective in these settings. As noted by Ning et al.,
The main factor affecting the hardness of the diffusion zone is the formation of Mg–Cu–Al ternary IMCs and Mg–Al binary IMCs at the interface.
By thoroughly evaluating these diverse factors, including the advantages of copper nickel alloys and the specific features of Mica Tapes, procurement managers can make informed decisions that ensure optimal performance and durability of the brazed connections.
Common Mistakes in Selecting Brazing Melting Points
A prevalent error in the joining process is the selection of a braze melting point without a thorough understanding of the thermal properties of the base materials involved. Such oversights can result in inadequate bonding or potential damage to the components, undermining the integrity of the joint. With joining technology having been in development for 5000 years, its significance cannot be overstated.
Additionally, the operating environment’s influence on the chosen braze melting point is often underestimated, contributing to suboptimal joining outcomes. The case study titled ‘Flow Characteristics of Filler Metals’ demonstrates that the flow behavior of filler metals is essential for filling gaps, with the solid-liquid ratio at soldering temperatures determining this behavior. Optimizing this flow is necessary to prevent voids and ensure connection strength, highlighting the balance needed between alloy fluidity and connection retention.
Furthermore, practitioners frequently neglect the critical role of proper joint design, which significantly affects heat distribution and the overall effectiveness of the joining process. Recognizing and addressing these common pitfalls is essential for making informed decisions that enhance the quality and durability of your applications. As Dalton O’Brien from Johnson Matthey Metal Joining aptly notes, ‘Proactive discussions about these aspects can lead to improved practices and outcomes in metal joining.
Best Practices for Successful Brazing
Achieving successful joining results hinges on stringent temperature control to ensure the braze melting point is maintained throughout the process. Using a reliable thermometer to monitor both the base substances and the brazing filler is essential. Contaminants on connection surfaces can severely compromise bond quality; therefore, ensuring that surfaces are impeccably clean is essential.
Preheating the base components can reduce thermal shock and improve filler flow, resulting in more robust connections. Furthermore, sufficient cooling time is essential to avoid strain on the connection, which ultimately aids in forming a strong and lasting bond.
In high-temperature applications, incorporating substances like Mica Tape can improve electrical insulation and offer extra safety measures during welding processes. Mica Insulation Tape, known for its high-temperature resistance, is invaluable in protecting sensitive components from heat damage while ensuring effective electrical insulation. It is commonly used in the manufacture of fire-resistant cables and other critical electrical insulation systems.
The combination of these materials with non-sparking tools, designed to prevent sparks and minimize ignition risks in explosive environments, is vital, further emphasizing safety and effectiveness in operations.
A notable case study on brazing SiO glass ceramic to Ti–6Al–4V alloy using AgCuTi filler foil illustrates these principles. The connection was brazed at 900 °C for 5 minutes, which is above the braze melting point, resulting in a maximum shear strength of 27 MPa. Various heating cycles were employed to study their effects on the interface and mechanical properties, highlighting the critical role of the braze melting point in determining performance.
Gray, a researcher in the field, emphasizes that the drop in strength associated with tighter clearances can be attributed to flux inclusions, further underscoring the necessity of meticulous temperature management.
In addition to these practices, employing non-destructive ultrasonic methods can assess void content in critical applications, enhancing the reliability of brazed connections. If accurate inspection methods for critical brazed connections cannot be developed, revisiting design may be necessary to allow for adequate inspection. By adhering to these best practices and incorporating high-quality insulating materials, including Mica Tape, along with the unique advantages of Non-Sparking Tools, procurement managers can significantly enhance the effectiveness and reliability of their brazing projects, leading to improved joint quality and longevity.
Conclusion
Understanding the intricacies of brazing and the critical role of melting points is essential for achieving optimal joint integrity in metal joining processes. The selection of the appropriate melting point not only affects the strength and reliability of the joints but also influences the efficiency of the brazing operation. By carefully considering the thermal properties of base materials, procurement managers can make informed decisions that enhance the performance of their brazed assemblies.
Common mistakes, such as neglecting the specific requirements of the operating environment or failing to adequately prepare joint surfaces, can lead to significant failures in brazing applications. It is imperative to adopt best practices, including:
- Stringent temperature control
- Thorough cleaning of surfaces
- Use of high-quality materials like Mica Tape
- Use of non-sparking tools
These measures not only improve joint quality but also ensure safety during the brazing process, particularly in high-risk environments.
In conclusion, mastering the art of brazing requires a strategic approach that emphasizes the importance of melting point selection and adherence to best practices. By doing so, procurement managers can significantly enhance the durability and performance of their brazed joints, ultimately leading to superior outcomes across various applications, from aerospace to automotive industries. Investing time and resources into understanding these principles will yield long-term benefits in joint reliability and operational efficiency.