Blogs
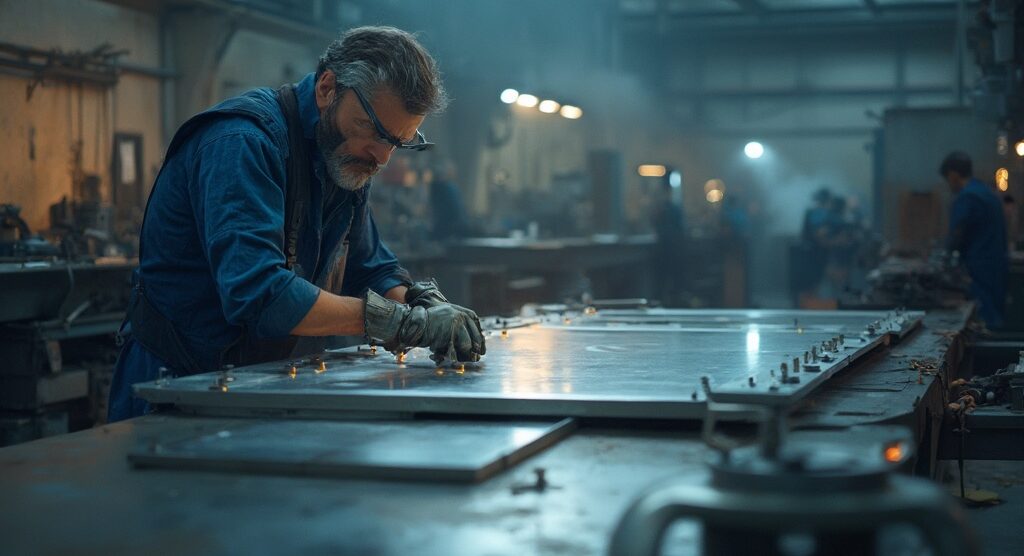
Understanding High Chrome Nickel Austenitic Alloys: An In-Depth Tutorial
Introduction
High chrome nickel austenitic alloys, often referred to as stainless steels, represent a cornerstone of modern engineering and manufacturing. With their unique composition of at least 16% chromium and 8% nickel, these alloys are engineered to deliver exceptional strength, corrosion resistance, and thermal stability, making them indispensable in a variety of demanding applications.
From aerospace components to marine environments, the versatility of these materials is underscored by their ability to withstand harsh conditions while maintaining integrity and performance. This article delves into the fundamental properties, applications, and manufacturing techniques of high chrome nickel alloys, offering insights into their critical role across industries and the strategic considerations essential for procurement professionals navigating this complex landscape.
As the demand for these advanced materials continues to grow, understanding their characteristics and applications becomes paramount for ensuring long-term reliability and success in various sectors.
Fundamentals of High Chrome Nickel Austenitic Alloys
High chrome nickel austenitic alloys, commonly recognized as stainless steels, contain a minimum of 16% chromium and 8% nickel. This composition ensures a face-centered cubic (FCC) crystal structure, imparting remarkable ductility and toughness to the materials. These high chrome nickel austenitic alloys demonstrate an optimal blend of strength, resistance to rust, and thermal stability, making them suitable for a wide range of applications, including chemical processing, aerospace, and marine settings.
Prominent grades such as 304, 316, and 310 are examples of high chrome nickel austenitic alloys that have been engineered with specific enhancements to thrive under varying environmental conditions. Notably, the high chrome nickel austenitic alloys, particularly alloy 59, stand out for their superior performance in oxidizing environments compared to alloys C-4 and 22, showcasing the strategic importance of selecting the right alloy for specific applications. A case study on the resistance to deterioration of high chrome nickel austenitic alloys highlights that this durability is primarily due to a chromium-rich oxide layer, which can be compromised by chlorides, leading to localized degradation.
High chrome nickel austenitic alloys play a crucial role in minimizing the spread of such deterioration, as raising their content typically improves resistance to pitting, crevice decay, and stress-related cracking. Furthermore, our copper-copper mixtures, which consist of roughly 90% copper and 10% metal, showcase remarkable characteristics suitable for numerous uses, with a tensile strength of about 550 MPa and outstanding resistance to rust and oxidation, alongside high thermal and electrical conductivity. These characteristics make them particularly well-suited for demanding environments across the marine, automotive, and electrical industries.
For example, copper nickel mixtures are widely utilized in marine uses for seawater piping systems because of their resistance to biofouling and corrosion. Furthermore, recent advancements in material production, particularly with CarTech Waspaloy now being produced in 30-inch diameter ingots, signify significant progress in overcoming previous production limitations. Material 800 has been chosen for SG tubes in German-designed PWRs and some CANDU-type reactors, illustrating practical applications of these substances in the industry.
The management of the primary metal industry is committed to responsible behavior in all its operations, ensuring the sustainability and reliability of these essential materials.
Applications of High Chrome Nickel Austenitic Alloys in Industry
High chrome nickel austenitic alloys play a crucial role in the aerospace industry, particularly in components that demand exceptional strength and resistance to corrosion. Common applications of high chrome nickel austenitic alloys include:
- Turbine blades
- Exhaust systems
These materials enhance performance and longevity. In the automotive sector, their use extends to:
- Exhaust systems
- Fuel lines
These areas require superior resistance to both heat and corrosive environments.
According to industry insights, high chrome nickel austenitic alloys are favored in chemical processing plants for:
- Storage tanks
- Piping systems
Where their durability is essential for handling aggressive substances. The increasing dependence on high chrome nickel combinations is reflected in market trends, particularly as Europe was the largest region in the aerospace materials market in 2023. Aerospace engineers have observed a growing use of high chrome nickel austenitic alloys due to their stringent performance requirements.
Airbus SE, a leading aircraft manufacturer, delivered 661 commercial aircraft to 84 customers in 2022 and registered 1,078 gross new orders, an 8% increase from the previous year, illustrating the industry’s reliance on advanced materials. As the aerospace sector expects a strong growth path forecasted for 2024-2033, the need for these advanced materials is anticipated to increase notably, corresponding with the overall development of the aerospace materials market in Europe. Furthermore, recent reports suggest an increase in the automotive sector’s use of high chrome metal mixtures, especially in exhaust systems, emphasizing their adaptability and essential role in contemporary manufacturing.
Furthermore, the ‘Aerospace Valves Global Market Report 2024’ offers insights into the uses of high chrome nickel austenitic alloys in aerospace valves, further enhancing the context of these materials in aerospace applications.
Mechanical Properties of High Chrome Nickel Austenitic Alloys
High chrome nickel austenitic alloys are renowned for their remarkable mechanical properties, particularly their tensile strength, which typically ranges from 520 MPa to 900 MPa, contingent on the specific composition and heat treatment process applied. These materials exhibit exceptional ductility, with elongation values generally exceeding 40%, allowing them to deform significantly before fracture. The substantial strength maintained by high chrome nickel austenitic alloys even at elevated temperatures renders them ideal for high-stress applications.
Moreover, the toughness of high chrome nickel austenitic alloys ensures that they can endure impact forces without catastrophic failure, making these alloys a preferred choice in demanding environments. For instance, recent studies confirm that 600M, enhanced with niobium, has been specifically developed to improve stress corrosion cracking (SCC) resistance in boiling water reactor (BWR) settings, showcasing the ongoing advancements in material technology. Additionally, U. Heubner notes that mixture 59 performs significantly better under oxidizing conditions compared to mixtures C-4 and 22, with sensitization beginning after two hours.
Furthermore, statistics reveal that chromium particles in nickel can be co-deposited using a high-speed sulphamate bath, heated at 1050°C for 12 hours or at 800°C for 36 hours, which contributes to the material’s overall properties. As a practical example, Alloy 625, a nickel–chromium–molybdenum alloy stabilized with niobium, is characterized by its low molybdenum content, which affects its pitting resistance. Initially created for high-temperature uses, it is now increasingly utilized in wet-corrosion services, illustrating the real-world implications of the mechanical properties discussed.
Furthermore, the incorporation of Mica Tape products, such as Mica Insulation Tape, Mica Sheet Tape, and Insulating Mica Tapes, recognized for their high-temperature resistance, flame resistance, and dielectric strength, can improve the safety and performance of electrical uses. These products are indispensable components in sectors reliant on robust thermal and electrical insulation solutions, such as aerospace and automotive industries. As the sector progresses, comprehending both the mechanical characteristics of metal mixtures and the functionalities of Mica Tape products is crucial for choosing the appropriate materials for specific uses.
Corrosion Resistance of High Chrome Nickel Austenitic Alloys
High chrome nickel austenitic alloys are characterized by their exceptional resistance to rust, especially in settings with high acidity and elevated chloride levels. The incorporation of chromium is critical, as it facilitates the formation of a passive oxide layer on the metal’s surface, effectively shielding it from further oxidative damage. For instance, material 316 is specifically designed to counter pitting and crevice deterioration, making it highly appropriate for marine uses where exposure to saltwater is common.
In contrast, copper nickel mixtures provide significant benefits in marine settings and electrical uses, including:
- High resistance to rust, especially in saline conditions
- Excellent thermal and electrical conductivity, which is crucial for efficient energy transfer
- Good ductility, allowing for ease of shaping and forming
- Ease of fabrication, facilitating various manufacturing processes
- Notable antimicrobial properties, making them ideal for situations where hygiene is paramount
Corrosion statistics indicate that chlorides can reach concentrations of approximately 4000–5000 ppm in aqueous phases, heightening the need for effective material selection. Furthermore, U-bend samples for degradation tests were prepared in accordance with ASTM G30-97, offering a standardized approach to assess the resistance of these materials.
In practical uses, consistent upkeep paired with the thoughtful selection of materials can greatly enhance rust resistance, guaranteeing durability and dependability in severe conditions. Insights from experts highlight the significance of comprehending these dynamics; as pointed out by specialists in the field, ‘Each author contributed to paper writing,’ emphasizing the collaborative effort in advancing knowledge in this area. Furthermore, the case study on galling in stainless steel demonstrates the possible corrosion problems that could occur in applications involving high chrome nickel austenitic alloys, emphasizing the essential importance of material choice.
Therefore, a comprehensive evaluation of metal properties, coupled with ongoing assessments of environmental conditions, is essential for optimal performance.
Manufacturing Techniques for High Chrome Nickel Austenitic Alloys
The production of high chrome nickel austenitic alloys encompasses a range of sophisticated processes, including casting, forging, and various machining techniques tailored to meet stringent industry standards. Key methods such as hot working and cold working are employed to achieve specific shapes and mechanical properties, ensuring that the final product meets performance expectations. Welding also plays a vital role in the fabrication of these mixtures, with techniques like TIG (Tungsten Inert Gas) and MIG (Metal Inert Gas) welding being favored for their ability to preserve the inherent corrosion-resistant qualities of the materials.
As noted by industry experts,
Stainless steel’s properties, such as its 100% recyclability, reusability, durability, corrosion resistance, and extremely low maintenance needs partly explain this amazing consumption growth.
Understanding these properties is essential for procurement managers, as they influence purchasing decisions and supplier capabilities. Additionally, statistics on scrap purchases in leading markets from 2014 to 2022 indicate a growing demand for these materials, reflecting market trends that procurement managers should consider.
The challenges encountered in the salt sector, including those from increased energy expenses and environmental issues, further demonstrate the significance of adjusting to industry dynamics, which is also applicable for the metal sector. Furthermore, staying abreast of recent innovations in welding methods and manufacturing techniques for high chrome nickel austenitic alloys is crucial for procurement managers. This knowledge not only aids in assessing supplier capabilities but also ensures compliance with evolving industry standards, ultimately contributing to more informed purchasing decisions.
Conclusion
High chrome nickel austenitic alloys are essential materials that underpin a vast array of industries, from aerospace to marine applications. Their remarkable properties, including strength, corrosion resistance, and thermal stability, make them indispensable in demanding environments. The article has explored the fundamentals of these alloys, detailing their unique compositions and mechanical properties, which allow them to perform reliably under extreme conditions. Furthermore, the discussion highlighted the strategic importance of selecting the appropriate alloy for specific applications, underscoring the critical role of procurement professionals in navigating this complex landscape.
The versatility of high chrome nickel alloys is reflected in their extensive applications across various sectors, particularly aerospace and automotive, where their exceptional durability is paramount. As market trends indicate a growing reliance on these advanced materials, understanding their applications and performance characteristics becomes increasingly important. Additionally, advancements in manufacturing techniques, including innovative welding methods and production processes, further enhance the capabilities of these alloys, ensuring they meet evolving industry demands.
In conclusion, the strategic selection and procurement of high chrome nickel austenitic alloys are vital for ensuring the long-term reliability and success of projects across multiple industries. As the demand for these materials continues to rise, staying informed about their properties, applications, and manufacturing techniques will empower procurement professionals to make informed decisions that drive operational excellence and sustainability. Embracing these insights will not only enhance material performance but also contribute to the overall advancement of engineering and manufacturing practices.