Blogs
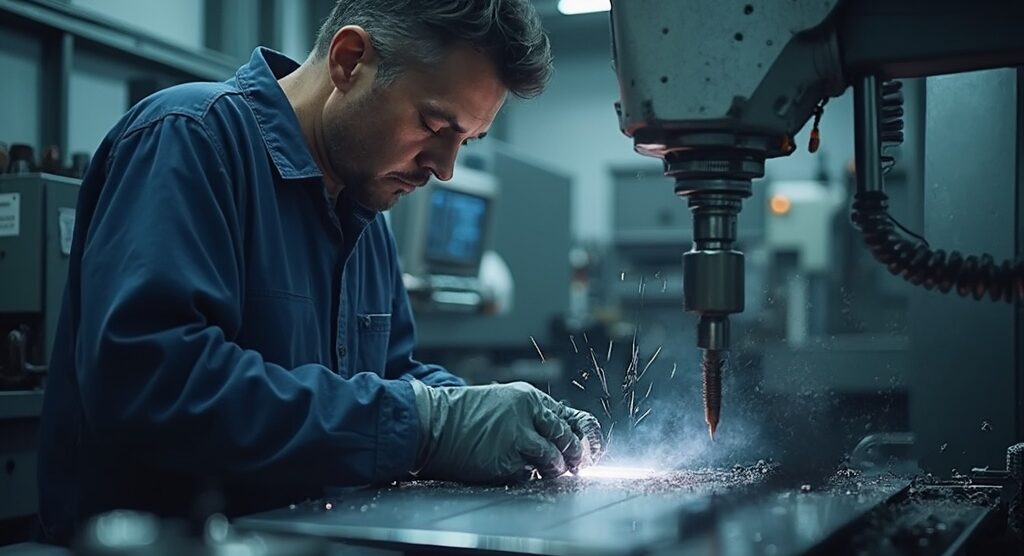
How to Cut Inconel 625: A Step-by-Step Guide for Machinists
Introduction
Inconel 625 stands out as a premier choice in the landscape of high-performance alloys, thanks to its exceptional strength, corrosion resistance, and ability to withstand extreme temperatures. Comprising a unique blend of nickel, chromium, molybdenum, and niobium, this alloy is integral to industries where reliability is non-negotiable, such as aerospace and chemical processing.
However, the complexities of machining Inconel 625 present challenges that demand a strategic approach. From selecting the right cutting tools to optimizing machining conditions, understanding the nuances of this material is essential for achieving superior results.
This article delves into the critical properties and applications of Inconel 625, effective machining techniques, tool selection, and best practices for setting up the machining environment and post-processing, providing valuable insights for professionals navigating the intricacies of this remarkable alloy.
Understanding Inconel 625: Properties and Applications
The nickel-chromium alloy 625 is distinguished by its remarkable strength, exceptional corrosion resistance, and capability to endure extreme temperatures. The alloy’s composition, which typically comprises:
- 58% nickel
- 20% chromium
- 8% molybdenum
- 3.6% niobium
is integral to its unique properties. Statistically, this alloy demonstrates an impressive average rupture strength of:
- 12 ksi (83 MPa) when exposed to 1600°F (871°C) for 1000 hours
- 9 ksi (62 MPa) at 1200°F (649°C)
- 10.5 ksi (72 MPa) at 1400°F (760°C)
This underscores its reliability under high-stress conditions across a range of temperatures.
This alloy finds extensive applications in critical sectors such as aerospace, where components must perform reliably in demanding environments, and chemical processing, where its resistance to oxidation and pitting is invaluable. Moreover, the marine engineering field utilizes alloy 625 for its durability against seawater corrosion. Notably, alloy 625 is a solid solution strengthened material that maintains its microstructure at low and high temperatures; however, between 923 to 1148 K, detrimental precipitates can form that affect its creep properties and strength.
For machinists and procurement managers, understanding these properties is crucial, as they influence production challenges such as work hardening and heat generation. Effective management of these factors is essential during the cutting inconel 625 process to optimize performance and ensure longevity in applications ranging from aerospace components to chemical processing equipment. Additionally, our copper nickel alloys boast exceptional properties that make them ideal for a wide range of applications, including marine, automotive, and electrical industries, with excellent resistance to corrosion and oxidation, as well as high thermal and electrical conductivity.
When considering materials for high-temperature resistance and electrical insulation, products like mica tapes offer superior insulation properties and flame resistance, making them indispensable in the construction of fire-resistant cables and electrical systems. As MatWeb, LLC suggests, it’s crucial to utilize original values or their raw conversions in calculations to reduce rounding error, ensuring precision in evaluations of 625’s performance.
Effective Machining Techniques for Inconel 625
To achieve optimal machining results with Inconel 625, it is essential to implement the following key techniques:
Selection of Instruments: Opt for carbide or ceramic implements specifically designed for high-temperature applications. Tools covered with titanium aluminum nitride (TiAlN) have been demonstrated to improve performance and prolong tool life, effectively decreasing wear during processing. As mentioned by machinist Dave, who has been working with Inconel 625, he primarily uses a 5/16″ Hanita Varimill with a TiAIN coating, which has significantly enhanced his efficiency.
Cutting Speed and Feed Rate: Begin machining with a cutting speed in the range of 30-50 SFM (Surface Feet per Minute). This range may be modified based on observed equipment wear and specific surface finish requirements. Utilizing a slower feed rate is advisable to mitigate heat generation, which helps prevent work hardening of the material. For reference, the best cutting parameters for cutting Inconel 625 to ensure edge durability correspond to a cutting speed of 250 m/min and a feed rate of 0.15 mm/rev.
Coolant Use: Employing a high-pressure coolant system is critical for managing heat and facilitating effective chip removal. This practice not only reduces thermal distortion but also considerably extends the lifespan of equipment, ensuring consistent performance in processing.
Depth of Cut: Implement shallower depths of cut to lessen the load exerted on the instrument and reduce heat accumulation. This strategy can significantly enhance processing efficiency and prolong the lifespan of the cutting implements. A machinist’s experience demonstrates that switching to ceramic inserts for turning this material resulted in a cycle time reduction from 13 minutes to just 6 minutes, showcasing the effectiveness of this approach.
Regular Equipment Inspection: It is essential to observe equipment wear carefully and substitute instruments as required to uphold manufacturing accuracy. This proactive approach helps prevent damage to the workpiece and ensures high-quality outcomes.
By adhering to these techniques and incorporating insights from real-world experiences and statistics, machinists can effectively navigate the challenges posed by cutting Inconel 625, ultimately achieving superior results while minimizing operational difficulties associated with cutting this high-performance alloy.
Choosing the Right Cutting Tools
Choosing the suitable cutting implements for cutting Inconel 625 is essential for attaining optimal performance and efficiency. Here are essential considerations:
Material of the Instrument:
Carbide instruments are highly recommended due to their superior hardness and resistance to high temperatures, making them ideal for Inconel 625, which has an aluminum content of a maximum of 0.40%. In situations necessitating exceptional toughness, ceramic implements can also be considered.Coatings:
Implementing equipment with advanced coatings such as Titanium Aluminum Nitride (TiAlN) or Aluminum Titanium Nitride (AlTiN) is vital. These coatings enhance the hardness of the cutting edge and reduce friction, significantly increasing the lifespan and performance during machining operations.Geometry:
The shape of the cutting implement plays a crucial role in efficiency. Instruments with sharp cutting edges and positive rake angles enable effective chip removal, which reduces cutting forces and minimizes wear.Equipment Size:
It is crucial to align the equipment size with the specific processing task. Adequately sized instruments guarantee stability and precision, which are crucial when dealing with difficult substances such as alloy 625.
By making informed choices regarding cutting tools, machinists can enhance their efficiency and effectiveness when cutting Inconel 625. Recent studies, including the assessment of the machinability of 625 composites with added NiTi-TiB, emphasize the importance of these factors. As noted in the case study titled “Mechanical Properties of 625 Composites,” composites exhibit enhanced mechanical properties, with microhardness values of 460 HV for 625 + 5 wt.% NiTi-TiB2 and 532 HV for 625 + 10 wt.% NiTi-TiB2, indicating improved performance for high-stress applications.
Expert Alexander Zhukov emphasizes the importance of these strategic selections, stating, ‘Study of the Machinability of a Composite 625 with Added NiTi-TiB Fabricated by Direct Laser Deposition.’ Such strategic selections are integral to optimizing manufacturing processes in today’s demanding production environments.
Setting Up the Machining Environment
To effectively establish the processing environment for cutting Inconel 625, adhere to the following essential guidelines:
Machine Calibration: The precision of machining operations hinges on properly calibrated equipment. As Mike Imholte, Sr. Calibration Technician at Boston Scientific, states,
The significance of calibration can’t be overstated. Our testing instruments and manufacturing processes must be precise.
Ensuring that your machinery meets stringent calibration standards is vital for maintaining dimensional accuracy and tolerances, thereby reducing the likelihood of cost and time overruns due to rejected parts, which can lead to significant financial losses. Additionally, labeling calibrated equipment with relevant information aids in tracking and audits, further enhancing operational efficiency.Workpiece Securement: Utilize appropriate fixtures or clamps to ensure that the workpiece is securely held in place. This is essential to prevent any movement that could compromise accuracy or cause damage to equipment, which can significantly affect production timelines and quality.
Coolant System Setup: Confirm that the coolant system is fully operational and set to the correct pressure. Effective coolant management is essential for dissipating heat generated during cutting, which can otherwise lead to tool wear and compromised workpiece integrity.
Lighting and Safety: Adequate illumination in the workspace is non-negotiable for precision manufacturing. Additionally, implement robust safety measures, including protective gear for operators, to mitigate risks and enhance safety during the manufacturing process.
Calibration Process Case Study: The calibration process involves a standardized procedure that includes choosing a reference standard, comparing measurements, adjusting equipment, and documenting results. This systematic method guarantees that equipment satisfies necessary standards and upholds precision over time.
By creating a carefully organized production environment, machinists can greatly enhance operational efficiency and ensure outstanding quality results when cutting Inconel 625 alloy.
Post-Machining Processes
Following the machining of a high-performance alloy 625, which boasts outstanding strength and toughness in high temperatures up to 2000°F (1093°C), cutting inconel 625 and implementing effective post-processing steps are crucial for ensuring component integrity and performance in demanding applications, especially in explosive potential environments where safety is paramount. Here’s a structured approach:
Deburring: It is essential to eliminate any burrs or sharp edges from the machined component.
This not only enhances safety but also improves surface finish. Deburring can be accomplished using specialized Non-Sparking Tools designed for high-performance materials or sandpaper, ensuring a smoother edge without risking ignition in hazardous settings. Non-Sparking Tools are typically made from materials such as brass, bronze, or special alloys, which prevent sparks during use.Surface Finishing: To achieve superior surface quality and precise tolerances, it may be necessary to apply advanced surface finishing techniques such as grinding or polishing.
The process is critical, as surface finish significantly influences the component’s performance and longevity in high-stress environments. Expert insights suggest that,this alloy can be milled, although it’s known for being a challenging material to machine due to its high work hardening rate and abrasive nature
.
This challenge is further highlighted by the fact that cutting inconel 625 is generally harder to machine than titanium, necessitating specialized strategies and equipment. Therefore, employing the right finishing techniques, including the use of Non-Sparking Tools, is vital.Inspection: A thorough inspection of the machined part is imperative to ensure compliance with specifications and quality standards.
Utilizing precise measurement tools such as calipers and micrometers allows for accurate assessments, confirming that the components meet the required tolerances.Cleaning: Post-machining cleaning is necessary to eliminate any coolant residues or contaminants that could impair the part’s functionality.
Employing suitable solvents or cleaning agents tailored for high-performance alloys is recommended to maintain the integrity of the surface.Storage: Finally, the finished components should be stored in a controlled, dry environment to prevent corrosion or damage prior to application.
This precaution is especially crucial considering the extensive application of 625 alloy in corrosive settings, like those present in marine and chemical sectors. For instance, this alloy can be clad or lined on high-strength carbon steel pipes to enhance corrosion resistance.
This method combines the strength of carbon steel with the corrosion resistance of Inconel 625, proving effective in addressing corrosive issues while reducing costs. By adhering to these post-machining processes, including the strategic use of Non-Sparking Tools, machinists can assure the quality and readiness of components, especially when cutting Inconel 625, positioning them for success in their respective applications. Procurement managers can source Non-Sparking Tools from specialized suppliers and manufacturers who focus on providing high-quality electrical insulation and high-temperature materials, ensuring they meet the specific needs of explosive environments.
Conclusion
Inconel 625 is undeniably a standout choice for high-performance applications, characterized by its remarkable strength and exceptional resistance to corrosion and extreme temperatures. The alloy’s unique composition not only contributes to its reliability in critical sectors such as aerospace and chemical processing but also highlights the importance of understanding its properties for effective machining. Through strategic tool selection, optimal machining techniques, and a meticulously prepared environment, professionals can navigate the challenges posed by this complex material.
Key machining strategies, including the use of specialized cutting tools and the implementation of high-pressure coolant systems, are vital for mitigating heat generation and work hardening. Furthermore, ensuring proper calibration of machinery and secure workpiece placement can significantly enhance precision and operational efficiency. Post-machining processes, such as deburring and surface finishing, are equally critical to maintaining the integrity of components, especially in demanding environments where safety and performance are paramount.
Ultimately, the successful machining of Inconel 625 hinges on a comprehensive understanding of its properties, effective techniques, and best practices throughout the entire process. By adhering to these guidelines, procurement managers and machinists can ensure the production of high-quality components that meet the rigorous demands of their applications, reinforcing the value of Inconel 625 as a premier alloy in today’s manufacturing landscape.