Blogs
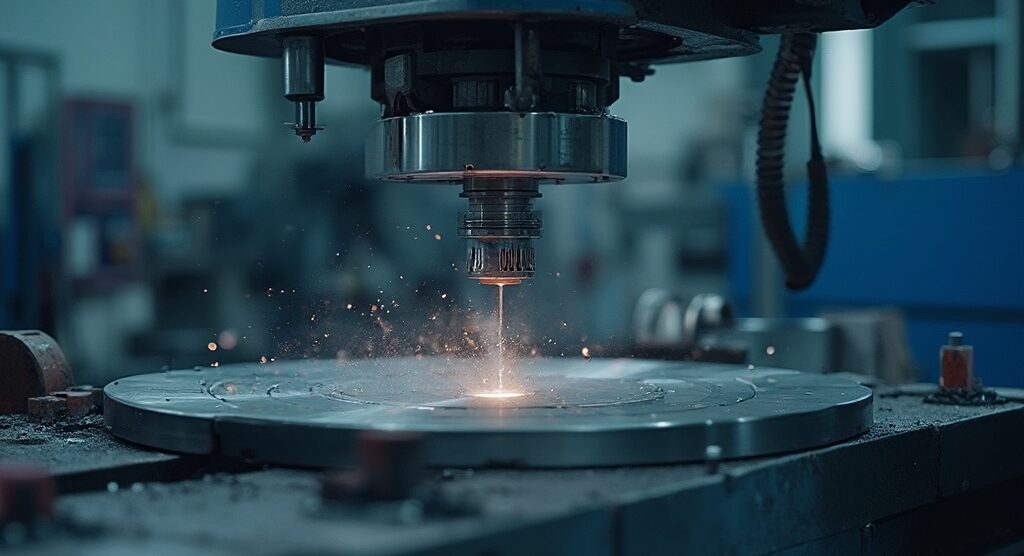
How to Determine Inconel 718 Machining Speeds and Feeds: A Step-by-Step Guide
Overview:
The article focuses on how to determine the optimal machining speeds and feeds for Inconel 718, a nickel-chromium alloy known for its high-temperature strength and corrosion resistance. It emphasizes the importance of understanding the alloy’s properties and challenges, such as work hardening and heat management, to effectively select cutting tools and optimize machining parameters, thereby enhancing tool longevity and manufacturing efficiency.
Introduction
Inconel 718, a high-performance nickel-chromium alloy, is recognized for its remarkable strength and corrosion resistance, making it a preferred choice in demanding industries such as aerospace and automotive. Its unique composition, which includes significant amounts of nickel and chromium, not only enhances its mechanical properties but also poses distinct challenges during machining.
Understanding the intricacies of this alloy is essential for procurement managers and machinists alike, as it influences everything from tool selection to machining parameters. This article delves into the complexities of machining Inconel 718, exploring the key factors that impact its performance, including:
- Work hardening
- Optimal cutting tools
- Advanced machining techniques
By addressing these critical aspects, organizations can enhance efficiency, reduce costs, and ensure the reliability of their operations in high-stakes environments.
Understanding Inconel 718: Composition and Properties
The nickel-chromium alloy 718 is distinguished by its remarkable high-temperature strength and corrosion resistance. The alloy’s composition typically consists of approximately:
- 50% nickel
- 19% chromium
- Trace amounts of iron, niobium, and molybdenum
These key elements collectively contribute to the alloy’s remarkable properties, making it particularly well-suited for rigorous applications in the aerospace and automotive sectors.
Understanding the nuances of this composition is essential, as it directly affects inconel 718 machining speeds and feeds and the alloy’s behavior under various cutting conditions. Significantly, this alloy displays a yield strength of approximately 1,200 MPa, enabling it to retain its mechanical integrity even at elevated temperatures. Additionally, the minimum elongation for solution treated plus precipitation heat treated alloy 718 is 12%, highlighting its ductility and performance.
The coefficient of thermal expansion for Alloy 718 ranges from 7.1 to 16.0 x 10(-6)/°F depending on temperature, which is crucial for understanding how the alloy behaves under temperature variations. Furthermore, this alloy has good resistance to oxidation and corrosion at various temperatures within the useful strength range, as noted by United Performance Metals, making it an ideal choice for applications in jet engines and gas turbine operations. Coupled with Domadia’s commitment to quality, each alloy undergoes rigorous testing and inspection processes, including assessments for mechanical properties and corrosion resistance, to ensure reliability and durability.
However, the alloy’s high yield strength can complicate the optimization of inconel 718 machining speeds and feeds, necessitating a strategic approach to enhance performance and efficiency during production. Additionally, for high-temperature applications that require extra safety measures, Domadia’s mica tape products offer superior insulation solutions, which not only enhance the safety of electrical components but also complement the high-performance characteristics of alloy 718 in critical environments.
Challenges in Machining Inconel 718: Work Hardening and Heat Management
Machining Inconel 718 presents unique challenges mainly due to its tendency for work hardening during machining processes. When exposed to stress, this superalloy can become considerably harder, complicating the manufacturing process and requiring careful control of processing conditions. Notably, the low-speed region (5 m/s) exhibits a high incidence of surface tears and material smearing, leading to increased surface roughness.
Moreover, excessive heat generation during processing not only accelerates tool wear but also diminishes overall tool life. To mitigate these issues, it is vital to employ optimal inconel 718 machining speeds and feeds alongside effective cooling strategies. As highlighted by Praveen K V U, ‘Cold rolling is found to be highly effective in eliminating the dual slope and enhancing the fatigue life at low strain amplitudes.’
This insight highlights the significance of heat management techniques in working with alloy 718. For example, the case study on high-speed processing of alloy 718 demonstrates that inconel 718 machining speeds and feeds can significantly enhance surface quality and reduce subsurface damage, providing practical evidence of improved machinability. Additionally, understanding that Alloy 718 can be welded in either the annealed or age condition—while noting that welding in the aged condition results in a softened heat-affected zone—further informs the strategic approach required in machining this material.
By recognizing these challenges and integrating effective techniques, machinists can adapt their practices to enhance performance and prolong tool longevity.
Choosing the Right Cutting Tools for Inconel 718 Machining
The careful selection of tools that can endure extreme temperatures and resist wear is crucial for optimizing inconel 718 machining speeds and feeds. Carbide tools are often the preferred choice for achieving optimal inconel 718 machining speeds and feeds due to their exceptional hardness and heat resistance, making them well-suited for this challenging alloy. A recent analysis highlighted that the contribution ratio of parameter f to burr width is 36.26% for down-milling, underscoring the critical nature of selecting the right tools to minimize burr formation.
- Tools designed with a positive rake angle can significantly reduce machining forces and enhance chip flow, which is essential when dealing with work-hardened materials.
- Furthermore, using coated tools, such as those with titanium aluminum nitride (TiAlN) or titanium nitride (Tin) coatings, offers added protection against wear and oxidation, further prolonging tool life.
- As recommended by industry expert bamavick, for general machining, AlTiN coated carbide performs well.
Take a doc as deep as you can WITH a light radial cut. Like many semi-finishing passes. You’ll get a higher rpm & feed = a faster cut part <.
Additionally, a 5 flute 4mm cutter designed specifically for super alloys is recommended for milling operations to improve inconel 718 machining speeds and feeds, thereby enhancing both efficiency and effectiveness. Recent findings also suggest that optimizing conditions for minimum burr formation involves careful consideration of significant input variables, as identified through analysis of variance. This strategic approach not only maximizes performance in manufacturing but also guarantees the durability of tools, aligning with best practices in the industry.
Insights from the case study titled ‘Sustainable Machining Strategies’ further emphasize the importance of integrating sustainable practices, highlighting opportunities for energy savings and emission reduction in manufacturing processes.
Optimizing Machining Parameters: Speeds and Feeds for Inconel 718
To effectively enhance processing parameters for alloy 718, it is crucial to begin with the appropriate inconel 718 machining speeds and feeds, which typically range from 30 to 60 meters per minute (mpm). This range may vary based on the specific operation and tooling employed. An effective starting point for inconel 718 machining speeds and feeds is approximately 0.05 to 0.15 mm per tooth for feed rates.
Close monitoring of tool wear is imperative, as adjustments to these parameters should be made in real-time to enhance performance. As highlighted by industry expert Larry Dickman,
What kind of machine has 7k min RPM? A router?
Not going to happen. You need some rigidity with anything other than wood.
This underscores the necessity of choosing sturdy equipment for processing, particularly when managing inconel 718 machining speeds and feeds.
Furthermore, the average maximum cutting-force component for high-feed milling is 3174 N, which highlights the significant forces involved in the manufacturing process. Moreover, case studies, like the ‘Cutting Insert Characterization,’ demonstrate the performance traits of different cutting inserts, including:
- A coated WC insert
- An Al + SiC insert
- A Bidemics insert
All selected for their ability to improve productivity during processing. Adopting a systematic approach to parameter optimization not only leads to improved surface finish but also significantly reduces cycle times, thereby optimizing both productivity and cost efficiency.
Recent studies have indicated that methodologies such as GRA, TOPSIS, or fuzzy logic could further refine these processes, with GRA demonstrating promising results without the need for determining weighting factors. By implementing these best practices in inconel 718 machining speeds and feeds, procurement managers can ensure their manufacturing operations are both efficient and effective.
Advanced Machining Techniques for Inconel 718: Coolants and Methods
Advanced fabrication techniques are essential for optimizing inconel 718 machining speeds and feeds, thereby enhancing both performance and efficiency. High-pressure coolant systems, in particular, have been shown to manage heat generation effectively and improve chip removal, thereby minimizing the risk of work hardening. As reported by Qin et al., “internal spray cooling is able to significantly reduce thrust force and improve tool life by two times over conventional external cooling,” which emphasizes the importance of these systems in contemporary manufacturing practices.
Such advancements are essential, given that cutting fluid can account for 10-17% of total manufacturing costs, underscoring the importance of optimal coolant use. Additionally, techniques such as dry processing and minimum quantity lubrication (MQL) have demonstrated effectiveness in specific applications. A significant case study assessed MQL fluid delivery during the processing of EN 47 chromium–vanadium steel, revealing that MQL decreased surface roughness by 48.35% compared to dry processing.
This reduction is particularly significant since the average surface roughness values for high-quality Inconel 718 machining speeds and feeds are well below 1.0 micrometers. Furthermore, employing trochoidal milling methods allows for smoother cutting paths and reduced cutting forces, further enhancing productivity. By integrating these advanced techniques, machinists can achieve superior outcomes while adhering to high-quality machining standards, particularly in regard to inconel 718 machining speeds and feeds.
Conclusion
Machining Inconel 718 presents both challenges and opportunities for organizations engaged in high-performance industries. Understanding the unique properties of this nickel-chromium alloy, including its impressive strength and resistance to corrosion, is crucial for optimizing machining processes. The alloy’s composition directly impacts its machinability, necessitating strategic approaches to tackle issues such as work hardening and heat generation.
Effective machining of Inconel 718 hinges on the careful selection of cutting tools and parameters. Utilizing carbide tools with appropriate coatings, along with optimizing cutting speeds and feeds, significantly enhances tool longevity and machining efficiency. Advanced techniques, such as high-pressure coolant systems and innovative machining methods like minimum quantity lubrication, further improve performance by managing heat and enhancing chip removal.
By integrating these insights into their operations, procurement managers and machinists can not only enhance overall efficiency but also reduce costs and improve the reliability of their manufacturing processes. Mastery of the complexities associated with Inconel 718 is essential for sustaining competitive advantage in demanding environments, ensuring that organizations can meet the rigorous demands of aerospace and automotive applications with confidence.