Blogs
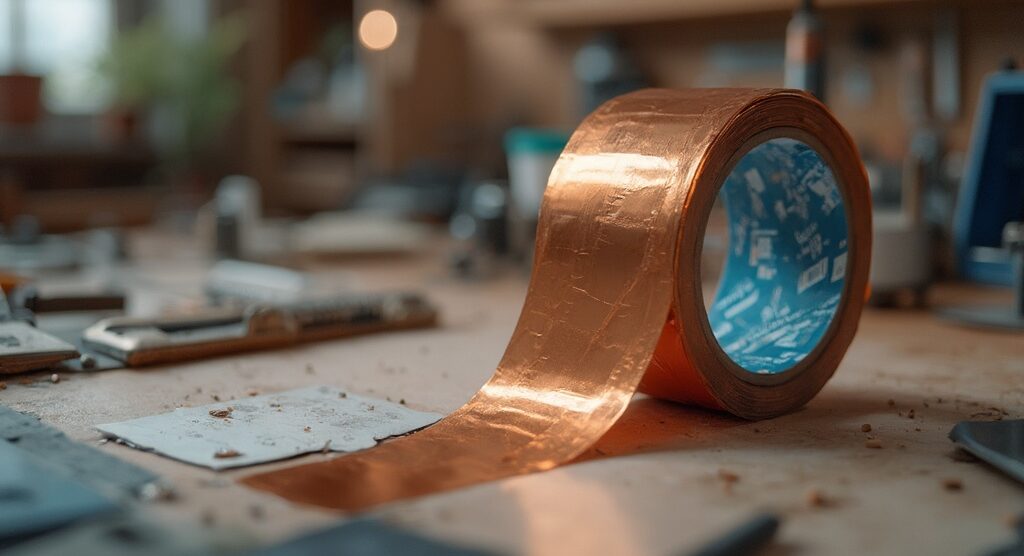
How to Use 3M Conductive Copper Foil Tape: A Step-by-Step Guide
Introduction
In the ever-evolving landscape of electronics, the choice of materials can significantly impact performance and reliability. 3M Conductive Copper Foil Tape emerges as a pivotal component, renowned for its exceptional electrical conductivity and versatile applications ranging from EMI shielding to circuit repair. Understanding its features, benefits, and practical applications is essential for professionals aiming to enhance their projects and streamline processes. This article delves into the key attributes of 3M Conductive Copper Foil Tape, providing a comprehensive guide on its usage, safety precautions, and maintenance tips, all while showcasing its indispensable role in modern electronic applications.
Understanding 3M Conductive Copper Foil Tape: Features and Benefits
The 3M conductive copper foil tape is renowned for its exceptional electrical conductivity and thermal performance, making it an indispensable element in various applications, including EMI shielding, grounding, and circuit repair. Its key characteristics include:
- High conductivity: Providing a low-resistance route for electrical signals, this material is essential in electronic uses, ensuring minimal resistance buildup. Recent measurements indicated resistance levels exceeding 100 mph for connections, underscoring the need for effective solutions. For procurement managers, understanding these resistance implications is vital in selecting products that ensure optimal performance and reliability.
- Versatility: The adhesive adheres well to a variety of surfaces, including metals, plastics, and glass, making it suitable for diverse indoor and outdoor projects. Furthermore, the use of Non-Sparking Tools, which are the optimal choice for non-sparking situations in explosive environments, is crucial to guarantee safety and avoid accidents during the installation or upkeep of electrical systems.
- Adhesive strength: With a strong adhesive, the material stays firmly in position even under difficult conditions, which is essential for preserving the integrity of electrical connections. This reliability is further enhanced when used in conjunction with DOMADIA’s Oxygen Free Copper (OFE/OHFC) for critical medical components, ensuring that connections remain stable and effective.
- Ease of application: Available in multiple widths and thicknesses, it can be easily cut and applied, providing the flexibility necessary to meet specific project requirements. Furthermore, exploring Domadia’s Mica Tapes for high-temperature electrical insulation solutions not only complements the capabilities of 3M conductive metal foil tape but also offers unique benefits such as enhanced thermal stability and resistance to electrical breakdown, particularly in demanding environments.
The advantages of utilizing 3M conductive copper foil tape are manifold, including enhanced reliability in electrical connections and improved performance in electronic devices. As emphasized by a prominent fabricator at BesCo, since this metal has four times the conductivity of nickel, 0.025mm of it would carry the same current as 0.10mm nickel. This considerable difference highlights the enhanced electrical properties of this metal, especially in scenarios demanding efficient current management, like PCBs where a minimum of 4 oz. metal trace is recommended. This recommendation highlights the significance of choosing the appropriate materials for ensuring robust performance in essential contexts. Moreover, practical uses, such as those depicted in the case study named ‘Building a Battery Box for My New Ebike Project,’ illustrate how 3M conductive copper foil tape can be effectively employed to satisfy both functional and aesthetic needs, emphasizing its significance in contemporary electronics.
The capacity to customize solutions for distinct uses further establishes this material as an essential resource, backed by various real-world instances showcasing its effectiveness in EMI shielding and other uses.
Step-by-Step Guide to Using 3M Conductive Copper Foil Tape
To effectively utilize 3M conductive copper foil tape in your electronic projects, adhere to the following best practices:
- Prepare the Surface: Ensure the area for use is clean, dry, and free from contaminants. For optimal results, use isopropyl alcohol to thoroughly cleanse the surface, promoting better adhesion.
- Cut the Material: Precisely measure the necessary length of material for your particular use. Employ scissors or a utility knife to achieve a straight edge, facilitating a cleaner application process.
- Apply the Adhesive Strip: Position the adhesive strip carefully onto the prepared surface.
Begin at one end and apply firm pressure while smoothing out any air bubbles along the way; this ensures maximum adhesion and effectiveness. - Secure the Edges: In circumstances where the material may be subject to movement or external factors, reinforce the edges with additional adhesive or bonding agent to prevent peeling or lifting over time.
- Test the Connection: For applications involving electrical connections, it is critical to use a multimeter to verify conductivity, ensuring the material performs as intended in your circuit.
- Finish Up: Trim any excess adhesive to achieve a neat finish and clean the surrounding area to uphold a professional appearance. Store any remaining adhesive film in a cool, dry environment to preserve its integrity for future use.
Given the increasing demand for high-performance electronic-grade metal foil in the international market, using quality materials like 3M Conductive Metal Foil Adhesive is essential. Furthermore, think about investigating associated links to different kinds of conductive metal and metallic products for more choices.
Insights from the ‘Cable Ties Guide‘ case study emphasize the significance of choosing the appropriate materials for particular uses. Just as choosing the appropriate cable ties can enhance the efficiency of cable management, using 3M conductive copper foil tape can greatly improve the performance and reliability of your electronic projects. By following these detailed steps, you will ensure that your software meets the high standards of quality expected in the industry.
Common Applications of 3M Conductive Copper Foil Tape
The versatility and effectiveness of 3M conductive copper foil tape make it essential for various critical uses within the electronics industry. Key applications include:
EMI Shielding: This material offers a robust defense against electromagnetic interference, essential for protecting sensitive electronic components. By wrapping or layering the material around devices, users can significantly reduce the risk of interference, ensuring optimal performance. Notably, Lamart’s 777-LE conductive shielding film, which features an acrylic conductive adhesive, is also recognized for its effectiveness in EMI shielding, offering a comparative perspective on performance.
Grounding: Establishing a reliable grounding path in electrical systems is crucial for safety and functionality. The adhesive can be effectively applied to metal surfaces or components, offering enhanced grounding solutions that comply with industry standards. The extensive and expanding use of copper foil in electronic devices underscores the relevance of such solutions in today’s technological landscape.
Circuit Repair: For quick fixes on printed circuit boards (PCBs), the use of 3M conductive copper foil tape is invaluable. By applying the adhesive strip across damaged traces, technicians can restore electrical connectivity swiftly, minimizing downtime in production and development.
Audio Equipment: In the realm of audio engineering, the material is used to shield cables and connectors from interference, enhancing overall audio performance. This software is especially advantageous in high-fidelity systems where signal integrity is crucial.
Prototype Development: During the prototyping phase, this material enables the formation of temporary connections and circuits. Its ease of use facilitates rapid testing and iteration, empowering engineers to innovate and refine their designs efficiently.
Real-World Case Study: Copper foil is noted for its strong chemical resistance, making it a preferred choice in communication cables exposed to weather. This software efficiently prevents radio and magnetic waves, showcasing the material’s reliability in difficult settings.
These tools highlight the versatility and efficiency of 3M conductive copper foil tape, establishing it as a crucial resource for experts in electronics and engineering. As technological advancements continue to evolve, the role of conductive copper foil tape in EMI shielding and grounding solutions becomes increasingly vital.
Safety Precautions When Using 3M Conductive Copper Foil Tape
When utilizing 3M Conductive Copper Foil Tape, it is crucial to observe the following safety precautions to ensure a secure working environment, particularly in light of advancements in semiconductor technology that enhance performance and energy efficiency in applications such as electric vehicles and renewable energy systems:
- Avoid Skin Contact: Although the bonding agent is typically safe, prolonged exposure can lead to skin irritation. It is advisable to wear gloves to prevent direct contact, thereby minimizing potential health risks related to bonding materials. This practice is particularly significant as the industry shifts towards more sustainable substrates, which may have different handling requirements.
- Work in a Well-Ventilated Area: Proper ventilation is essential to avoid inhaling any fumes emitted by the bonding agent. This practice not only safeguards respiratory well-being but also conforms to the most recent safety standards for adhesive substances in electronics, especially as the EU Ecodesign Directive highlights a circular economy and the safe utilization of materials.
- Handle with Care: Given the conductive nature of the material, it is essential to avoid touching exposed conductive surfaces during application. Always ensure that the power is turned off before applying the adhesive to any electrical components, as this reduces the likelihood of accidental short circuits. This caution is particularly relevant as the industry transitions to advanced materials like gallium arsenide and silicon carbide, which require careful handling.
- Store Properly: Proper storage is key to maintaining the integrity of the tape. Keep it in its original packaging and store it in a cool, dry place to prevent degradation of the adhesive and material properties. This is crucial in the context of sustainable practices, as improper storage of 3M conductive copper foil tape can lead to increased waste and resource consumption.
By adhering to these safety precautions, users can significantly minimize risks and create a safer working environment while effectively utilizing this tape. These measures are not merely suggestions; they signify a dedication to safety consistent with industry best practices and the changing environment of electronic materials, as shown by real-world examples such as the anti-counterfeit label and energy-autonomous temperature logger that illustrate the importance of safe handling in electronics.
Maintenance and Storage Tips for 3M Conductive Copper Foil Tape
To preserve the integrity and functionality of your 3M Conductive Copper Foil Tape, adhere to the following expert recommendations:
- Inspect Before Use: Prior to application, conduct a thorough inspection of the tape for any signs of damage or degradation. If any compromise is detected, discard the recording to avoid suboptimal performance.
- Store in a Controlled Environment: Safeguard the film from extreme temperatures and humidity, which can negatively impact its sticking characteristics. Ideally, maintain storage conditions within a temperature range of 15-25°C (59-77°F). It’s crucial to note that sealants and bonding agents should not be stored at temperatures lower than 40°F or higher than 100°F to ensure optimal performance, as highlighted in industry guidelines.
- Avoid Direct Sunlight: To prevent deterioration of both the bonding substance and copper material, store the product in a dark location or keep it in its original packaging, as prolonged exposure to sunlight can reduce its effectiveness.
- Use Within Recommended Timeframe: Although the tape boasts a lengthy shelf life, utilizing it within the manufacturer’s advised timeframe guarantees optimal performance and reliability. As mentioned by Naji Kharouf in ‘Shelf Life and Storage Conditions of Universal Adhesives: A Literature Review,’ proper storage conditions are essential for maintaining the effectiveness of the bonding agents.
By implementing these maintenance and storage strategies, you can ensure that your 3M conductive copper foil tape remains effective and readily available for your operational needs. Additionally, consider organizing adhesive products in separate sections with clear labels, as illustrated in a case study that demonstrated how incorrect storage and lack of clear labeling can lead to confusion. The outcome of this case study emphasizes that proper labeling and organization help minimize the risk of selecting the wrong products, thereby enhancing overall efficiency.
Conclusion
3M Conductive Copper Foil Tape is undeniably a critical asset in the realm of electronics, delivering exceptional performance through its superior electrical conductivity and versatility. The key features, including high conductivity, robust adhesive strength, and ease of application, position this tape as an essential tool for various applications, from EMI shielding to circuit repair. The guidance provided on its usage, safety precautions, and maintenance underscores the importance of proper handling to maximize its effectiveness and longevity.
The practical applications of 3M Conductive Copper Foil Tape further illustrate its indispensable role in the industry. Whether utilized for:
- Grounding
- Audio equipment shielding
- Prototype development
This tape not only enhances the reliability of electrical connections but also streamlines project execution. The real-world case studies highlighted demonstrate its adaptability and efficacy across diverse scenarios, reinforcing its status as a go-to solution for professionals.
In summary, embracing 3M Conductive Copper Foil Tape equips procurement managers and engineers with a reliable solution that addresses modern electronic challenges. By understanding its features and adhering to best practices, users can significantly improve their project outcomes while ensuring safety and compliance. As technology continues to advance, the role of this conductive tape will only grow, making it a pivotal component in the future of electronic applications.