Blogs
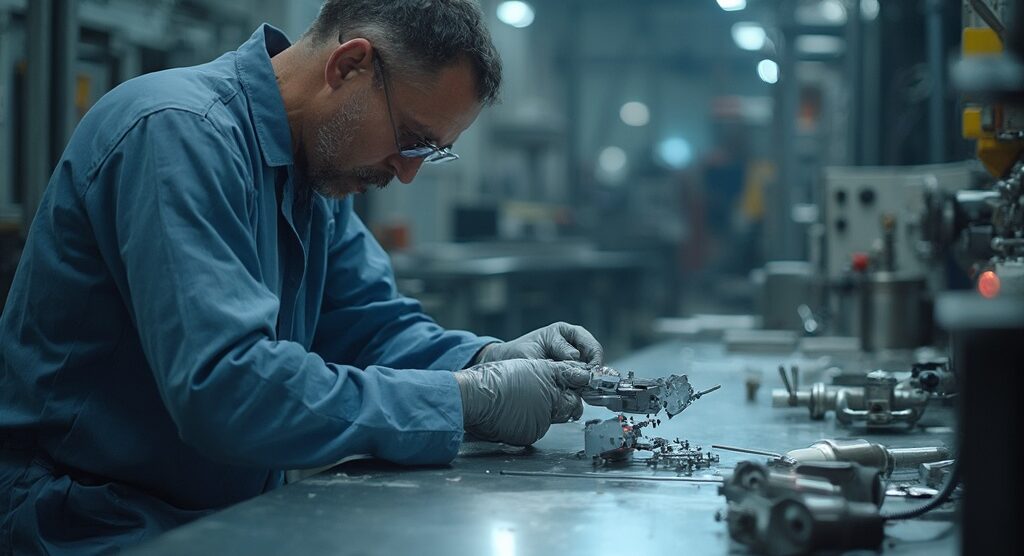
Inconel Alloy 718 Heat Resisting Alloy Powder: A Complete Tutorial on Properties and Applications
Overview:
Inconel Alloy 718 is a high-performance nickel-chromium alloy known for its exceptional oxidation and corrosion resistance, along with its ability to maintain strength and toughness at elevated temperatures, making it ideal for demanding applications in industries such as aerospace and automotive. The article details its composition, mechanical properties, and various manufacturing techniques, highlighting its versatility and critical role in components like gas turbine engines and surgical instruments, supported by advanced manufacturing processes that enhance its performance characteristics.
Introduction
Inconel Alloy 718 has emerged as a cornerstone material in industries where performance under extreme conditions is non-negotiable. Renowned for its exceptional oxidation and corrosion resistance, this high-performance nickel-chromium alloy is engineered to thrive in high-temperature environments, making it indispensable in sectors like aerospace, automotive, and biomedical engineering.
With a carefully balanced composition that includes nickel, chromium, and molybdenum, Inconel 718 not only withstands mechanical stresses but also maintains its integrity in corrosive settings. As industries increasingly turn to advanced manufacturing techniques, including additive manufacturing, understanding the nuances of this alloy—from its mechanical properties to its heat treatment processes—becomes critical for procurement managers aiming to leverage its full potential.
This article delves into the composition, applications, manufacturing techniques, and mechanical properties of Inconel Alloy 718, providing valuable insights into its transformative impact on modern engineering solutions.
Overview of Inconel Alloy 718: Composition and Key Properties
Inconel 718 is a high-performance nickel-chromium material distinguished by its remarkable oxidation and corrosion resistance, as well as its ability to maintain high strength and toughness under elevated temperatures. The material’s typical composition consists of:
- 50-55% nickel
- 19-21% chromium
- 4.75-5.5% molybdenum
complemented by trace amounts of titanium, aluminum, and iron. Each of these elements plays a crucial role in preparing the composite to endure extreme operational environments, thus making it a preferred material in sectors that demand performance under high-temperature and corrosive conditions.
Significantly, Inconel 718 possesses essential characteristics such as:
- A melting point ranging from approximately 1260-1310°C
- A density of 8.19 g/cm³
Its weldability further enhances its versatility, a characteristic increasingly valued in manufacturing processes, particularly in high-temperature environments where electrical insulation is critical. Recent observations indicate that the alloy exhibits good resistance to post-weld cracking, reinforcing its suitability for applications requiring robust integrity.
The heat treatment procedure involves:
- 1 hour at 1850°F
- Air cooling
- Regulated cooling
This procedure is crucial for enhancing its mechanical characteristics. Additionally, the elongation minimum for alloy 718, when solution treated and precipitation heat treated, is 12%, underscoring its ductility. Furthermore, as with Domadia’s product offerings, commitment to quality in manufacturing ensures that Alloy 718 is available in various forms including:
- Bars
- Wire
- Billets
- Strips
- Rods
- Sheets
- Plates
- Forging stock
- Welding wire
This demonstrates its versatility and practical applications across diverse industrial sectors.
The high-temperature resistance of Inconel alloy 718 heat resisting alloy powder makes it particularly suitable for applications in electrical engineering, where mica tape products are also employed for their electrical insulation characteristics, ensuring safety and performance in critical environments.
Applications of Inconel Alloy 718 in Modern Industries
In high-performance applications, especially in the aerospace industry, inconel alloy 718 heat resisting alloy powder is a crucial material. It is extensively utilized in gas turbine engines, where the inconel alloy 718 heat resisting alloy powder’s remarkable ability to endure extreme temperatures and mechanical stresses is essential. Components such as seals, shafts, and fasteners leverage these properties, ensuring operational reliability in demanding environments.
In fact, this alloy accounts for up to 50% of the weight in aircraft turbojet engines, underscoring its significance in critical engine parts. The fatigue strength of alloy 718 typically varies from 420 MPa to 655 MPa, highlighting its robust performance under stress. The automotive sector similarly benefits from alloy 718, employing it in exhaust systems and turbochargers where heat resistance and durability are vital for performance.
Recent advancements also highlight its application in automotive exhaust systems, reinforcing the material’s versatility. In biomedical contexts, this alloy is favored for implants and surgical instruments due to its biocompatibility, strength, and corrosion resistance. The unique combination of these properties makes inconel alloy 718 heat resisting alloy powder the material of choice in extreme environments, where reliability and performance are non-negotiable.
This is echoed by industry leaders, such as the Ariane Group (Airbus Safran Launchers), who are developing injectors for the liquid rocket engine on the propulsion systems of the Ariane 6 launcher. Furthermore, a recent case study titled ‘Review of Mechanical Properties of AM Alloy 718’ provides insights into the material’s performance across various additive manufacturing processes, contributing to the understanding of its mechanical behavior. These factors collectively highlight the transformative impact of alloy 718 on modern engineering solutions.
Manufacturing Techniques for Inconel Alloy 718: From Powder to Product
Inconel alloy 718 heat resisting alloy powder is produced through a variety of manufacturing techniques, prominently featuring traditional casting and forging. However, the rise of additive manufacturing (3D printing) has transformed the landscape, offering innovative methods to create intricate and complex components. The powder metallurgy process is notable for its ability to produce shapes that are often unattainable through conventional means, especially when utilizing inconel alloy 718 heat resisting alloy powder.
By selectively melting and fusing inconel alloy 718 heat resisting alloy powder layer by layer, this technique facilitates the creation of geometries that enhance design flexibility and functionality. Post-processing techniques, including machining and heat treatment, play a crucial role in refining the material to achieve optimal mechanical properties and surface finishes. Notably, the mean hardness value of the alloy 718 produced via laser metal deposition (LMD) was found to be 10% higher than that of its forged counterparts, underscoring the benefits of advanced manufacturing methods.
Understanding these processes is essential for procurement managers to ensure quality and performance in the final products, especially as the market trends continue to favor additive manufacturing solutions. As Pavel Diko, an academic editor, emphasizes, ‘effective statistical analysis of the morphological characteristics formed through high deposition rates and laser power can significantly inform the manufacturing strategies for this alloy.’ Moreover, recent advancements like the CNN model for predicting microstructural features emphasize the potential for enhanced mechanical characteristics and the necessity for better characterization of boundary conditions.
Additionally, the complex influence of laser power and powder feeding rate on the dilution ratio presents challenges that must be navigated in the additive manufacturing process, further enriching the discussion on these innovative techniques.
Heat Treatment Processes and Their Impact on Inconel Alloy 718
The heat treatment methods for Inconel alloy 718 heat resisting alloy powder include:
- Solution treatment
- Aging
- Stress relieving
Each is essential for enhancing its mechanical characteristics.
Solution treatment typically occurs at temperatures between 980-1020°C, where the material is heated to dissolve precipitates before undergoing rapid cooling. This step is vital for ensuring a uniform microstructure.
Following solution treatment, aging is conducted at lower temperatures, around 720-760°C, facilitating the precipitation of gamma prime (γ’), which significantly enhances both strength and stability. Significantly, the alloy 718 with 12 wt% W demonstrates the best overall mechanical characteristics, emphasizing the significance of composition in attaining optimal performance. The tensile strength, yield strength, and elongation of laser powder bed fused (LPBFed) alloy 718 samples can reach impressive values of 1507.07 MPa, 1398.17 MPa, and 15.23%, respectively, surpassing traditional forging standards.
Stress relieving is equally important, particularly post-manufacturing, as it mitigates residual stresses and improves dimensional stability. As Keivan Davami notes, “the support of the Advanced Manufacturing program of the National Science Foundation, award CMMI 2029059, is invaluable for advancing research in this area.”
Furthermore, a case study on microstructure analysis of some alloy 718 revealed that heat treatment significantly reduces the number of pores and increases their size, indicating that pores aggregate during the process, which is essential for enhancing the material’s characteristics.
These heat treatment processes are not merely procedural; they fundamentally influence the material’s suitability for high-performance applications, emphasizing the significance of following best practices in the treatment of Inconel alloy 718 heat resisting alloy powder.
Mechanical Properties of Inconel Alloy 718: Strength and Durability
Inconel alloy 718 heat resisting alloy powder stands out for its remarkable mechanical properties, which include a high tensile strength that can reach up to 1,200 MPa and impressive fatigue resistance. This inconel alloy 718 heat resisting alloy powder maintains its mechanical integrity at elevated temperatures, capable of withstanding conditions up to 700°C, making it suitable for extreme applications. Additionally, this alloy exhibits a minimum elongation of 30%, enhancing its ability to endure high loads without failure.
Its composition includes:
- Boron in a range of 0.001 to 0.006
- Copper fixed at 0.15
- Cb + Ta ranging from 4.75 to 5.50
These elements contribute to its overall strength and durability. Furthermore, the use of inconel alloy 718 heat resisting alloy powder is particularly advantageous due to its resistance to stress corrosion cracking in corrosive environments, ensuring reliability and longevity in service.
To complement the use of Inconel 718 in high-temperature environments, Mica Tape products, including:
- Mica Insulation Tape
- Mica Tape for Electrical
- Mica Sheet Tape
offer superior electrical insulation and flame resistance.
Mica Insulation Tape is designed for high-temperature resistance, ensuring reliability in critical electrical applications. Mica Tape for Electrical provides excellent flame resistance and dielectric strength, essential for fire-resistant cables. Mica Sheet Tape offers robust solutions for insulating large flat surfaces, making it suitable for aerospace and automotive industries.
These characteristics render Mica Tape products perfect for uses where protection against fire risks is essential. However, care must be taken when welding this material, as welding in the aged condition can lead to a softened heat-affected zone, potentially compromising its strength. A case study on the welding of inconel alloy 718 heat resisting alloy powder highlights the necessity of considering these factors to maintain the alloy’s mechanical properties, positioning Inconel 718 as a superior choice for components that demand both durability and performance under challenging conditions.
Conclusion
Inconel Alloy 718 is a vital material for high-performance engineering, particularly suited for extreme conditions. With its unique composition of nickel, chromium, and molybdenum, it offers outstanding oxidation and corrosion resistance while maintaining high strength and toughness at elevated temperatures. This makes it essential in aerospace, automotive, and biomedical sectors.
The alloy’s versatility is evident in its applications, from gas turbine engines to automotive exhaust systems and surgical implants. The rise of additive manufacturing has further enhanced its production capabilities, enabling the creation of complex geometries that traditional methods cannot achieve.
Key to optimizing Inconel 718’s performance are its heat treatment processes, which ensure a uniform microstructure and enhance strength and stability. This understanding is crucial for procurement managers aiming to leverage the alloy’s full potential in demanding environments.
In summary, Inconel Alloy 718 is a cornerstone of modern engineering solutions. Its superior properties and adaptability highlight its significance in high-performance applications. As industries continue to evolve, the role of Inconel 718 will expand, reinforcing its importance in the future of advanced materials.