Blogs
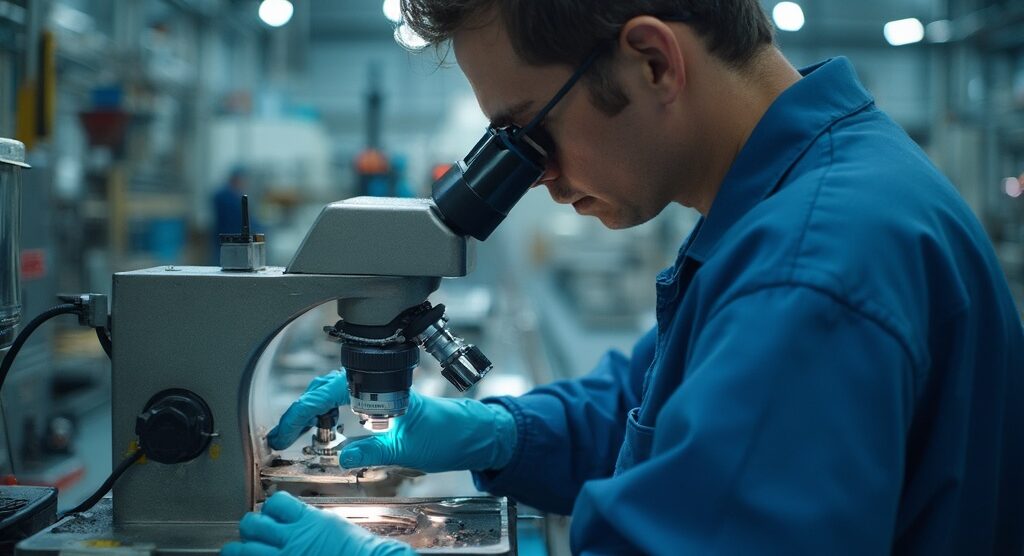
What Are DIN 17405 Nickel-Iron Alloy Standards? A Comprehensive Overview
Introduction
In the ever-evolving landscape of industrial materials, nickel-iron alloys have emerged as critical components across various sectors, from automotive to electronics. With the establishment of DIN 17405 standards, procurement managers are tasked with navigating the complexities of sourcing these alloys, ensuring both compliance and performance excellence. This article delves into the essential aspects of nickel-iron alloys, exploring their unique properties, manufacturing processes, and rigorous quality control measures.
It also highlights the significant role that non-sparking tools and advanced materials play in enhancing safety and operational efficiency in high-risk environments. As the demand for these alloys continues to surge, understanding future trends and developments becomes paramount for procurement professionals aiming to leverage these materials effectively and sustainably.
Overview of DIN 17405 Nickel-Iron Alloy Standards
Non-Sparking Tools are crucial in explosive settings, offering a secure substitute for uses where conventional tools present a hazard of igniting combustible substances. The importance of these tools cannot be overstated, particularly in industries such as:
- Oil and gas
- Chemical manufacturing
- Mining
Suppliers and producers of Non-Sparking Tools, along with electrical insulation and high-temperature substances, play a crucial role in ensuring compliance with safety standards.
Mica tape products, known for their high-temperature resistance and electrical insulation properties, are also vital in these applications, providing additional safety measures. Engaging with suppliers who prioritize these standards is critical for procurement managers, ensuring that the materials used not only meet but exceed safety benchmarks necessary for operational success.
Applications and Properties of Nickel-Iron Alloys Under DIN 17405
What makes DOMADIA Nickel Molybdenum Iron Alloy unique? Nickel-iron materials, particularly the DOMADIA Nickel Molybdenum Iron Composition, are integral to both the automotive and electronics sectors, primarily due to their exceptional properties, and they comply with the din 17405 nickel-iron alloy standards. This metal is distinguished by its unparalleled strength, corrosion resistance, and thermal stability, making it a favored option for essential uses.
These unique traits, including high permeability, low coercivity, and outstanding thermal stability, make them appropriate for a variety of uses, such as:
- Transformers
- Inductors
- Magnetic shielding
Their inherent resistance to corrosion ensures reliable performance across diverse environments. For example, in the automotive industry, the DOMADIA Nickel Molybdenum Iron Alloy is extensively utilized in sensors and actuators, where both precision and durability are essential.
As emphasized by Manoj Phagare, a Senior Research Analyst at Cognitive Market Research, ‘Understanding the uses of nickel-iron combinations is essential for procurement managers seeking to make informed choices that align with project specifications and performance criteria.’ Recent advancements in the characteristics of these materials have opened new avenues for their use, reinforcing their role in the growing consumer electronics market. The case study on the expanding consumer electronics market illustrates that nickel base shape memory materials, including DOMADIA, are extensively used in devices due to their high strength, toughness, and corrosion resistance.
The U.S. electronic goods exports surged significantly in 2023, underscoring the demand for nickel-iron composites and providing a strategic advantage for procurement professionals looking to leverage these materials effectively.
Manufacturing Processes for Nickel-Iron Alloys Under DIN 17405
Manufacturing nickel-iron combinations according to the din 17405 nickel-iron alloy standards encompasses several essential processes such as melting, casting, and heat treatment, each tailored to enhance the materials’ magnetic and mechanical properties. The controlled melting process, conducted in vacuum or inert environments, is essential for preventing oxidation and preserving the purity of the metal. Furthermore, heat treatment techniques, notably annealing, play a crucial role in attaining optimal magnetic characteristics while minimizing residual stresses.
JLC Electromet Pvt. Ltd., a notable producer, emphasizes that these essential application materials are indispensable for sectors including:
- Welding
- Heating
- Thermocouple
- Automotive
stating, ‘Critical Application materials for Welding, Heating, Thermocouple & Automotive.’ Furthermore, with stock levels reaching 272,096 tonnes in August 2020, comprehending these manufacturing methods and their effect on material properties is more vital than ever.
JLC Electromet Pvt. Ltd. is ISO:9001 certified and has established itself as a critical supplier, serving over 50 countries. By understanding these manufacturing techniques and their impact on material properties, procurement managers can effectively evaluate the quality of materials they source and ensure adherence to din 17405 nickel-iron alloy standards, which facilitates informed decision-making in their procurement strategies.
Quality Control and Testing Methods for DIN 17405 Alloys
Q1. What makes DOMADIA Nickel Molybdenum Iron Alloy unique? DOMADIA Nickel Molybdenum Iron Alloy is distinguished by its exceptional strength, corrosion resistance, and thermal stability, making it a preferred choice for critical applications across various industries.
Quality control for this material under the din 17405 nickel-iron alloy standards entails comprehensive testing protocols designed to ensure compliance with established specifications. Key testing methods include:
- Tensile Strength Assessments – Evaluating the material’s ability to withstand tension.
- Magnetic Property Evaluations – Assessing the magnetic characteristics of the metal mixture.
- Corrosion Resistance Tests – Evaluating the material’s durability against corrosive environments.
Each of these methods is critical in verifying that the materials exhibit the requisite mechanical strength and performance reliability. Procurement managers must be adept in these testing procedures to confirm that sourced items not only adhere to din 17405 nickel-iron alloy standards but also demonstrate consistent performance.
As emphasized by quality control expert Uwe Karst, ‘the integration of advanced analytical techniques is crucial for enhancing our understanding of material properties in battery research,’ which is particularly relevant for ensuring the quality of nickel-iron compositions. Insights from recent research highlight how these advanced techniques can significantly improve testing accuracy and reliability, thus mitigating risks associated with supplier selection. Therefore, implementing robust quality control measures is essential for fostering long-term supplier relationships and ultimately contributing to the success of projects dependent on nickel-iron materials.
Furthermore, maintaining compliance with the din 17405 nickel-iron alloy standards is critical, and ongoing monitoring of compliance statistics can provide valuable insights into the effectiveness of quality control processes.
Future Trends and Developments in Nickel-Iron Alloys
The trajectory of nickel-iron mixtures is poised for significant transformation, driven by advancements in manufacturing technologies, especially those that adhere to din 17405 nickel-iron alloy standards, notably additive manufacturing. This innovative method enables the development of optimized material compositions that yield enhanced performance traits, paving the way for lighter and more efficient components, particularly within the automotive and electronics sectors. According to recent market research, the Veterinary Auriscopes Market was valued at USD 0.25 Billion in 2022, reflecting a broader trend towards high-performance materials.
As industries increasingly embrace sustainability, a notable shift towards recycling and reusing nickel-iron alloys, following din 17405 nickel-iron alloy standards, is anticipated. This trend not only highlights the significance of sustainable practices but also requires a reassessment of sourcing strategies. For example, the case study titled “Managing High Emotions During Contract Negotiations” emphasizes that maintaining focus and professionalism is essential for keeping negotiations on track, which is vital for managers.
By remaining informed about these emerging trends and technologies, procurement managers can effectively adapt their sourcing practices, ensuring alignment with industry developments that foster both competitive advantage and long-term sustainability. Additionally, the optimistic outlook for high-performance materials underlines the importance of staying adaptable in a rapidly evolving landscape.
Conclusion
Nickel-iron alloys, particularly those adhering to DIN 17405 standards, play a pivotal role across various industries, from automotive to electronics. Their unique properties, such as exceptional strength, corrosion resistance, and thermal stability, make them indispensable in critical applications. The importance of non-sparking tools in enhancing safety cannot be overlooked, especially in high-risk environments like oil and gas or chemical manufacturing, where compliance with safety standards is paramount.
Manufacturing processes for these alloys are intricate, involving controlled melting and heat treatment techniques that optimize their magnetic and mechanical properties. Quality control measures, including tensile strength assessments and corrosion resistance tests, ensure that these materials meet the rigorous standards necessary for reliable performance. As procurement managers navigate these complexities, understanding the manufacturing and testing protocols becomes essential for making informed sourcing decisions.
Looking ahead, the future of nickel-iron alloys is bright, with advancements in manufacturing technologies and a growing emphasis on sustainability. The shift towards recycling and reusing these materials reflects industry trends that procurement managers must embrace to maintain a competitive edge. By staying informed about these developments, professionals can align their strategies with emerging market demands, ultimately contributing to safer and more efficient operational environments. The journey of nickel-iron alloys is not just about meeting current needs but also about fostering innovation and sustainability for the future.