Blogs
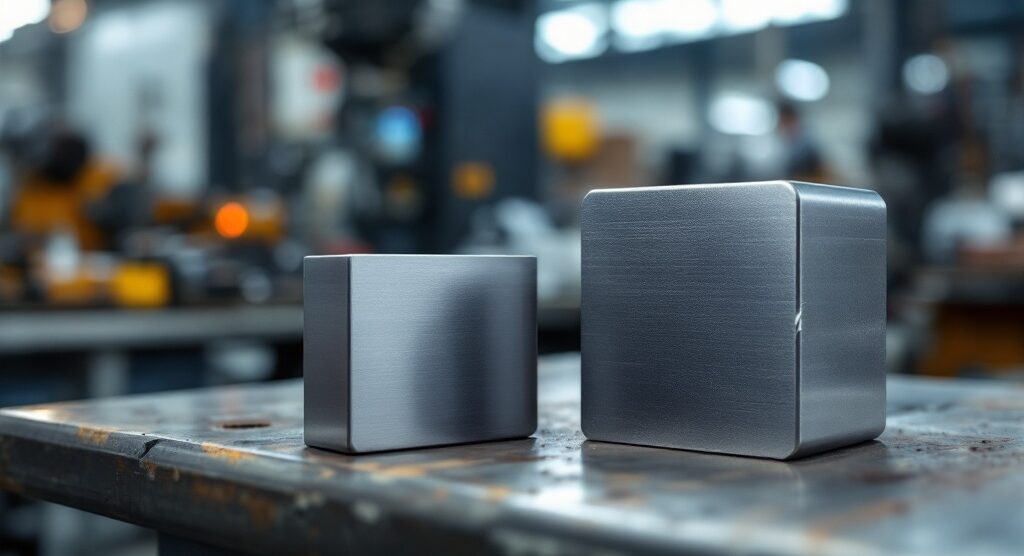
What You Need to Know: Is Titanium as Strong as Steel?
Introduction
In the dynamic landscape of materials engineering, the comparison between titanium and steel is not merely an academic exercise but a critical inquiry that shapes industry practices. As procurement managers evaluate the unique properties of these two metals, understanding their strengths, applications, and evolving market dynamics becomes essential.
- Steel
- Unparalleled tensile strength
- Versatility
Long been the backbone of construction and heavy machinery
Titanium
- Lightweight nature
- Exceptional corrosion resistance
- Positioned as a game-changer in sectors such as aerospace and medical devices
This article delves into the intricate balance between these materials, exploring their respective advantages and limitations, and providing insights that facilitate informed decision-making in material selection. With the ongoing advancements in alloy technology and the shifting demands of modern applications, the choice between titanium and steel has never been more nuanced or consequential.
Comparing the Strength of Titanium and Steel
In assessing the relative durability of this metal and steel, it is essential to determine if titanium is as strong as steel by reviewing factors such as tensile capacity, yield resistance, and the particular uses for which each material is most appropriate. Steel showcases a tensile durability of 121 on the Brinell scale, considerably greater than that of titanium’s 70, suggesting its exceptional performance in heavy-load situations. However, this metal excels in applications where a favorable strength-to-weight ratio is essential, along with its high-temperature resistance.
Its remarkable lightweight properties make it ideal for industries that prioritize weight reduction alongside strength, such as aerospace and medical fields. For instance, this metal is extensively utilized in surgical equipment and implants due to its biocompatibility and corrosion resistance, while also being a preferred choice for aircraft components and sports equipment. As mentioned by William Kroll, who introduced a new method for creating ductile metal in 1932, the advancement of this material has opened opportunities for high-performance uses across various sectors.
This historical context highlights titanium’s evolution, making it a viable alternative in environments requiring durability under stress. Conversely, stainless alloy, mainly made of iron, chromium, and carbon, provides outstanding resistance to corrosion because of the chromium content, rendering it appropriate for uses where corrosion is a concern. While the greater yield capacity of the metal makes it more appropriate for conventional heavy-load uses, the particular needs of each project will ultimately determine the selection of material.
Key Properties of Titanium That Influence Its Strength
Titanium is characterized by several essential properties that significantly influence its strength and overall performance. Most notably, it is approximately 45% lighter than steel, a factor that is particularly advantageous in weight-sensitive applications such as aerospace and automotive industries. The lightweight nature of this metal allows for enhanced fuel efficiency and improved performance in these sectors.
Furthermore, this metal is renowned for its exceptional corrosion resistance, which enables it to preserve its strength and integrity even in highly corrosive environments. This unique property positions this metal as an ideal material for industries such as marine and chemical processing, where exposure to harsh conditions is common. Recent advancements in metal alloys have further enhanced their performance, making them increasingly relevant for contemporary applications.
The upper limit of the TMP temperature range for this metal is set at 882 °C, beyond which phase transformation occurs, affecting its properties. Furthermore, a case study named ‘Temperature Effects on Alloys’ shows that at increased temperatures, every type of alloy displays distinctive tensile characteristics, with high durability materials maintaining both proof and tensile qualities at significantly higher temperatures than commercially pure variants. Although this metal may not reliably equal steel’s durability across all criteria, it raises the question of whether is titanium as strong as steel; nonetheless, its unique blend of low weight and high resistance to corrosion renders it an excellent option for certain uses, especially in situations where longevity and performance are crucial.
As Arulraj P succinctly states, ‘If yield capability is more than the specified (275-450 MPa, testing done at room temp. And the value 485 MPa) for Titanium Gr. 2 Plate (SB-265 GR.2), what is the reason the yield is more?’
This inquiry highlights the ongoing exploration of titanium’s capabilities and its implications for applications, reinforcing its role as a transformative material in various engineering contexts.
Understanding the Strength and Versatility of Steel
Steel’s reputation for durability and versatility leads to the question of whether titanium is as strong as steel, positioning it as the material of choice across diverse industries. With a compressive yield strength for M2 alloy typically around 3,250 MPa (471,000 psi) when tempered at 300°F (149°C), its high tensile strength is crucial for constructing resilient structures, including skyscrapers and bridges. The alloying procedure additionally enhances the characteristics of the metal, leading to various grades designed for particular uses.
For instance:
- Stainless alloy is celebrated for its exceptional corrosion resistance, making it ideal for environments exposed to moisture.
- High-carbon metal is prized for its remarkable hardness, suited for tools and high-stress applications.
The adaptability of this material extends beyond construction; it plays a pivotal role in automotive manufacturing and machinery, showcasing its integral position within the industrial landscape. As noted by structural engineers, the versatility of this material allows for innovative designs and solutions, affirming its status as a cornerstone element in modern engineering.
Furthermore, as highlighted by Next Level, ‘We can produce mill certificates for every piece of coil that we purchase,’ emphasizing the traceability and quality assurance in metal procurement. Recent advancements in metal durability and versatility continue to improve its uses, reinforcing its significance in upcoming construction endeavors.
Additionally, heat treatment methods, like quenching and tempering, can significantly change the microstructure of iron alloy, as demonstrated in a case study where quenching enhances yield resilience by forming a hard yet fragile martensite structure, while tempering boosts toughness without greatly compromising durability.
Notably, the Young’s Modulus of this metal is three times that of aluminum, further substantiating the claim that titanium is as strong as steel compared to other materials.
Applications: When to Choose Titanium Over Steel and Vice Versa
The selection between a specific metal and another relies on the particular requirements of each usage. In the aerospace sector, where weight reduction is crucial, this metal is often the material of choice, thanks to its exceptional strength-to-weight ratio and unparalleled corrosion resistance. For example, metal alloys surpass iron in severe conditions, as demonstrated by case studies showcasing their durability and resistance to moisture and chemicals.
However, the metal industry faces significant challenges, including high mining and processing costs and competition from cheaper materials. These factors make the exploration of innovations, such as the potential to combine the advantages of metal and titanium into a ‘super wear alloy,’ an intriguing avenue for material development. In contrast, this material is typically preferred in construction and heavy machinery due to its higher yield strength and cost-effectiveness, with prices ranging from $1 to $1.50 per kilogram for stainless variants.
This cost advantage makes steel particularly appealing for large-scale projects. Additionally, in fields such as medical devices, this metal’s biocompatibility renders it indispensable. As William Kroll observed in 1932, his groundbreaking method for producing flexible metal has facilitated its wider use in contemporary contexts.
As procurement managers navigate these material choices, understanding the distinct advantages of each, alongside the current challenges in the metal market, allows for more informed decision-making, ensuring optimal material selection tailored to specific operational requirements.
The Ongoing Debate: Titanium vs. Steel in Industry
The continuing dialogue about whether titanium is as strong as steel compared to other metals is gaining traction as industries adjust and new uses emerge. Titanium is increasingly acknowledged for its lightweight and corrosion-resistant features, making it perfect for specialized uses, especially in the aerospace industry where robustness and durability are crucial. Moreover, the rising application of this metal in medical devices and implants is another significant factor of market growth.
Conversely, steel remains a preferred choice across various industries due to its established strength and cost-effectiveness. Recent advancements in alloy technology and manufacturing processes have further complicated this debate, leading to the development of innovative metal alloys that enhance performance while striving to reduce overall costs. Industry professionals are now placing greater emphasis on lifecycle costs, sustainability, and application suitability, which adds layers to the decision-making process.
As the Asia-Pacific region emerges as a significant contributor to growth in the high-end metal alloy market—projected to account for over 35% of total revenue growth—its implications for material selection are profound. Key players like Arcam, ATI Metals, and Daido Steel are leveraging advanced manufacturing technologies and strategic partnerships to enhance their competitive positioning in this evolving landscape. Ultimately, the choice between titanium and steel involves more than just the question of whether titanium is as strong as steel; it requires a comprehensive assessment of performance attributes, economic viability, and environmental considerations.
Conclusion
The exploration of titanium and steel reveals a nuanced landscape where each material offers distinct advantages suited to specific applications. Steel, with its unparalleled tensile strength and versatility, remains the backbone of traditional industries such as construction and heavy machinery. Its adaptability and cost-effectiveness solidify its role as a primary choice for large-scale projects, where strength and budget are paramount considerations.
In contrast, titanium emerges as a transformative alternative, particularly in sectors like aerospace and medical devices, where its lightweight nature and exceptional corrosion resistance are critical. The historical advancements in titanium production have enabled its adoption in high-performance applications, addressing the growing demand for materials that prioritize strength-to-weight ratios and durability under stress.
As industries evolve, the decision between titanium and steel increasingly hinges on the specific requirements of each project. Procurement managers must carefully evaluate factors such as:
- Performance attributes
- Lifecycle costs
- Environmental impact of material choices
With ongoing innovations in both metals, the dialogue surrounding their applications will continue to shape industry practices, ensuring that the most suitable material is selected for each unique challenge. Ultimately, understanding the strengths and limitations of titanium and steel is essential for making informed decisions that align with modern engineering demands.