Blogs
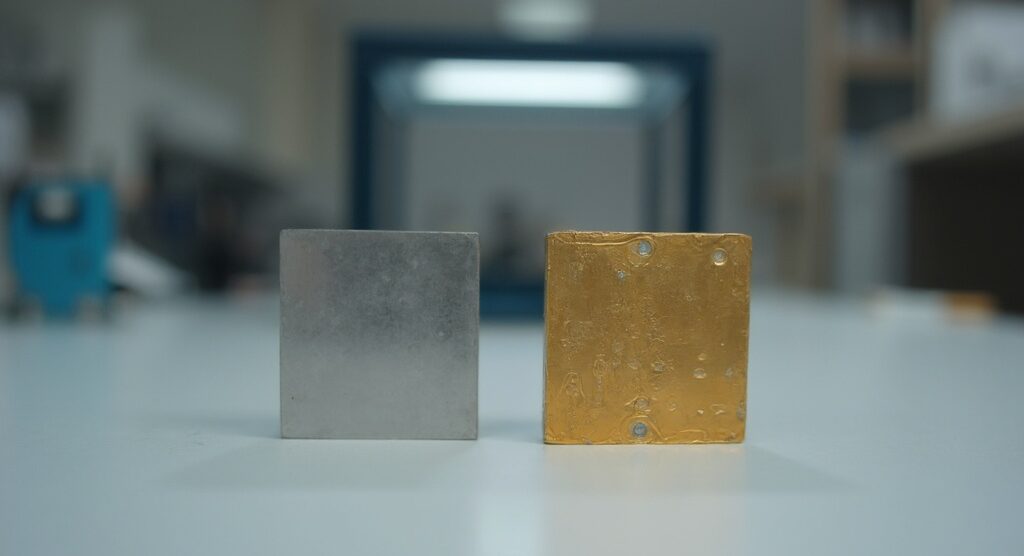
Evaluating Hardness: Is Titanium Harder Than Steel in Applications?
Introduction
Choosing the right material is a big deal in industrial projects. Two metals often compared are titanium and steel. Each has its own strengths, and the best choice depends on what your project needs.
Steel, especially carbon steel, is known for being hard, strong, and easy to work with. It’s used everywhere—from buildings to bridges to machines.
Titanium, while not as hard in its pure form, becomes much stronger when mixed with other elements. It shines in high-performance industries like aerospace, automotive, and medical because it’s both lightweight and incredibly strong.
When it comes to strength, weight, corrosion resistance, and cost, here’s how they compare—and what you should know before making a decision.
1. Hardness: Which Is Tougher?
Steel wins in raw hardness—especially carbon steel. Thanks to its carbon content and heat treatment, it can be adjusted to reach different levels of hardness. This makes it very versatile and a great option for heavy-duty parts.
Titanium, on its own, is softer than steel. But when alloyed with elements like aluminum and vanadium, it becomes much harder. These titanium alloys are used in parts that need to be both strong and lightweight, like airplane parts or medical tools.
🔍 Bottom Line:
Use steel if you need maximum surface hardness.
Use titanium alloys if you need hardness plus weight savings.
2. Strength and Durability: Who Handles Stress Better?
Steel has excellent tensile strength, meaning it can handle heavy loads without breaking. That’s why it’s used in construction, manufacturing, and machinery.
But titanium has a secret weapon—its strength-to-weight ratio. It offers nearly the same strength as steel but is about 45% lighter. This makes a big difference in industries where every gram matters, like aerospace or motorsports.
Titanium also handles repeated stress (fatigue) better than many steel types. So, if your material needs to flex, bend, or vibrate often, titanium is a smarter choice.
🔍 Bottom Line:
Choose steel for strong, heavy structures.
Choose titanium for lightweight strength and long-term durability.
3. Corrosion Resistance: Which Metal Lasts Longer?
Titanium is one of the best metals when it comes to resisting corrosion. It forms a natural oxide layer that protects it from saltwater, chemicals, and acids. That’s why it’s often used in marine environments, medical implants, and chemical plants.
Steel, on the other hand, can rust easily—especially carbon steel. To prevent this, it needs to be coated or alloyed (like turning it into stainless steel), which adds cost and maintenance.
A study by PNNL confirms that fighting corrosion is crucial for improving the life and reliability of materials. That gives titanium a serious edge.
🔍 Bottom Line:
Choose titanium if you need something that resists rust and chemical damage.
Choose steel if you don’t mind protective coatings or are working in less harsh environments.
4. Cost: What’s More Budget-Friendly?
Steel is cheaper and widely available. It’s easy to make and ship, so it’s perfect for large-scale, budget-sensitive projects.
Titanium, while high-performing, is more expensive. It’s harder to extract and process. And supply issues, like those caused by conflicts in Ukraine, can affect its availability. That’s a concern especially in the aerospace sector, as noted by Locatory.com’s CEO, Toma Matutyte.
But here’s the catch: steel’s maintenance costs (like coatings and repairs) can add up over time. In contrast, titanium lasts longer and needs less upkeep.
A survey by Sapio Research showed that 92% of plant maintenance teams saw better performance through proactive care—proof that material reliability matters.
🔍 Bottom Line:
Use steel for low-cost, general-purpose needs.
Use titanium when performance and low maintenance matter most in the long run.
Conclusion: Steel or Titanium—What Should You Choose?
Here’s a quick summary to help you decide:
Feature | Steel | Titanium |
---|---|---|
Hardness | High, adjustable via heat | Lower (pure), high when alloyed |
Strength | Excellent tensile strength | Great strength-to-weight ratio |
Corrosion Resistance | Needs coatings (unless stainless) | Naturally resistant |
Cost | Low upfront cost | Higher cost, but longer-lasting |
Weight | Heavier | Much lighter |
✅ Pick steel for construction, tools, machinery, and projects on a tight budget.
✅ Pick titanium for aerospace, medical, marine, and high-performance parts where weight, corrosion resistance, and long-term reliability matter most.
Looking for High-Performance Materials?
At Domadia, we offer a wide range of top-quality metals and alloys to meet your toughest industrial challenges. Whether you need strength, durability, corrosion resistance, or weight savings—we’ve got the right material for the job.
📩 Contact us today to get expert guidance or a custom quote for your next project!