Blogs
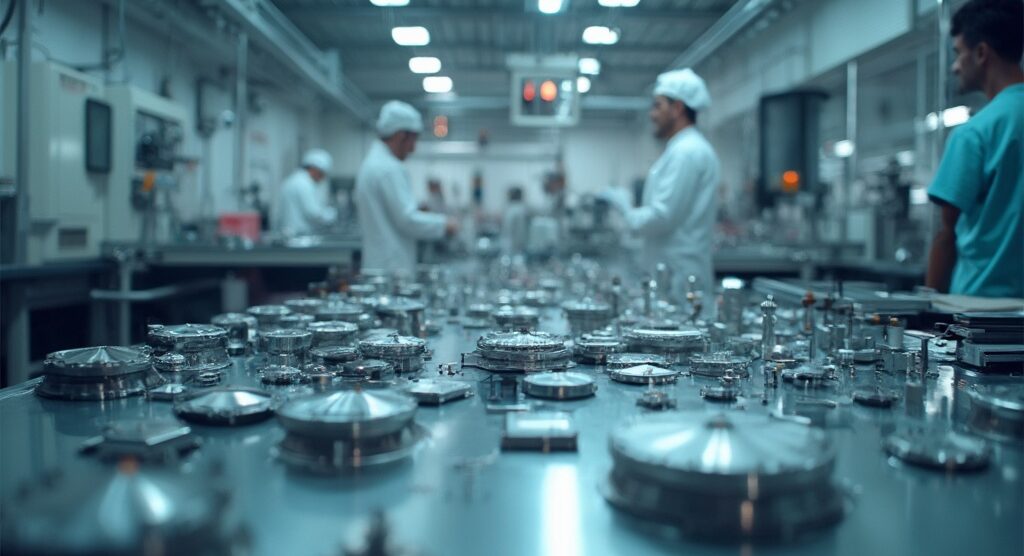
Innovations in Metal Processing Internationally: Trends and Techniques
Introduction
The metal processing industry is undergoing a remarkable transformation driven by a combination of technological advancements and sustainable practices. Innovations in materials and alloys are producing high-performance metals tailored for contemporary applications, with significant improvements in properties such as strength, ductility, and corrosion resistance. Sustainable fabrication processes are becoming increasingly crucial, with a focus on minimizing environmental impact through recycling, renewable energy sources, and green metallurgy techniques.
Integrating artificial intelligence and machine learning into metal processing is revolutionizing operations by enhancing efficiency, productivity, and predictive maintenance. In the metal casting industry, smart technologies, such as sensors, IoT devices, automation, and advanced simulation software, are enhancing precision and efficiency, leading to higher quality products. This article delves into these key advancements, highlighting their implications for various industries and the future of metal processing.
Advancements in Materials and Alloys
‘Advancements in metal processing have transformed the development of materials and compounds, resulting in high-performance metals tailored for contemporary applications.’. Innovations in metal mixtures have significantly improved properties such as strength, ductility, and corrosion resistance. For instance, advanced high-strength steels (AHSS) have become integral to the automotive industry, enhancing vehicle safety and fuel efficiency. The aerospace and defense sectors have greatly benefited from the development of lightweight materials like aluminum-lithium and titanium, where weight reduction is crucial.
High-entropy materials (HEMs) have demonstrated exceptional potential in numerous applications because of their enhanced strength and ductility. Researchers have employed laser-based additive manufacturing (AM) to create Head that are not only strong but also highly energy-efficient. This technology holds potential for producing safer, more fuel-efficient vehicles, and longer-lasting machinery. By using neutron and X-ray scattering alongside electron microscopy, scientists are gaining deeper insights into the performance mechanisms of these advanced materials.
Additionally, multi-principal element materials (Moms) are engineered to endure extreme conditions, such as those faced in space and the Arctic. These metal mixtures maintain their integrity under high heat, cold, and pressure, making them ideal for aerospace and nuclear power applications. The advancement of these materials involves a multidisciplinary approach, combining atomic-scale experiments with theoretical models to predict their behavior under high-temperature oxidative conditions. This research paves the way for next-generation alloys with exceptional resistance to extreme environments, ensuring their reliability and durability in critical applications.
Sustainable Fabrication Processes and Materials
Sustainability in material processing is transforming the sector, propelled by advancements focused on reducing environmental impact. Recycling scrap metals and incorporating renewable energy sources into manufacturing processes are gaining significant traction. Green metallurgy techniques, which focus on reducing waste and emissions during production, are reshaping sector practices. Additionally, the use of bio-based materials and eco-friendly lubricants in metalworking is on the rise, reflecting a strong commitment to sustainable practices aligned with global environmental goals.
The automotive industry’s shift toward Industry 4.0, for instance, highlights the potential for more sustainable vehicle designs through advanced technologies like virtual assembly. This approach not only reduces costly surprises but also minimizes waste by cutting down the number of physical prototypes needed. Furthermore, the global demand for sustainable materials is underscored by the significant increase in consumption over the past decades, such as the tripling of steel demand since 1971.
Initiatives to improve sustainability are also apparent in the area of additive production involving metals. Companies are investing in research and development to create more eco-friendly solutions, such as laser additive manufacturing (LAM), which builds objects layer by layer, reducing material waste. However, conventional powders employed in LAM necessitate extensive post-heat treatments, which are both time-consuming and energy-intensive. Researchers are now exploring more sustainable alternatives to address these challenges.
Moreover, resource refineries are actively researching ways to reduce their carbon footprint through carbon capture technology and renewable energy sources like wind, solar, and geothermal. These efforts are essential as raw materials remain scarce and energy efficiency becomes increasingly critical in meeting Net Zero targets.
In the realm of industrial applications, the segmentation of the global 3D printing market into various types, forms, and end-use industries, such as aerospace and automotive, further emphasizes the industry’s shift toward sustainability. The adoption of clean technologies and promoting repurposing, reuse, and recycling at the end of product life cycles are vital steps in decoupling economic development from material demand, ultimately leading to lower energy consumption and carbon dioxide emissions.
Artificial Intelligence (AI) and Machine Learning (ML) in Metal Processing
Artificial intelligence and machine learning are transforming processing operations by significantly enhancing efficiency and productivity. AI algorithms analyze vast datasets to optimize production processes, predict equipment failures, and improve quality control. For example, predictive maintenance powered by AI can drastically reduce downtime and maintenance costs. In one case study, an assessment of the abrasive process led to an annual savings of over $62,000 by identifying better abrasive solutions through data analysis. Furthermore, machine learning models assist in process optimization by examining historical data to identify patterns that lead to improved outcomes in yield and cost-effectiveness.
The integration of AI in metal processing is not only about efficiency but also about transforming the entire value chain. The shift towards AI-driven operations is part of the broader Industry 4.0 movement, which is transforming production from supply chain management to quality control. A significant contribution of AI is in predictive maintenance, which gathers high-resolution data to predict equipment failures accurately, thereby reducing costly downtimes and unnecessary maintenance.
Moreover, advancements in modular tooling systems and energy-saving technologies are enabling operators to adapt quickly to changing production requirements and reduce energy consumption. By investing in these technologies, manufacturers can boost productivity and remain competitive in the dynamic metalworking field. According to recent trends, utilizing AI-based solutions in production processes can lead to substantial improvements in customer satisfaction and overall business performance.
Smart Technologies in Metal Casting
The metal casting sector is experiencing a significant transformation with the integration of smart technologies that enhance precision and efficiency. The adoption of sensors and IoT devices in casting processes enables real-time monitoring and data collection, allowing manufacturers to make informed decisions and improve process control. This shift towards smarter production is revolutionizing the sector, as emphasized by recent developments at Aston University, where a project is underway to develop a sophisticated mathematical model to address the rapid oxidation of lightweight aluminum alloys during casting.
Automation and robotics are also playing a pivotal role in modernizing casting operations. These technologies streamline processes, reduce labor costs, and minimize the risk of workplace injuries. As emphasized by specialists, the shift towards digitization and connectivity in manufacturing facilities supports the objectives of optimizing efficiency and ensuring a safe work environment. The use of advanced simulation software further aids in predicting casting outcomes, reducing defects, and optimizing material usage, ultimately leading to higher quality products.
Real-world applications of these advancements can be seen in initiatives like the introduction of Hexagon’s Nexus Connected Worker, which connects shop floor processes with real-time information, boosting productivity. The sector’s emphasis on groundbreaking solutions is further illustrated by events such as the CERAMITEC trade show, where state-of-the-art ceramic 3D printing technologies are presented, providing high precision, consistency, and productivity.
In conclusion, the integration of smart technologies, automation, and advanced simulation software is propelling the metal casting industry into a new era of efficiency and precision, ensuring that manufacturers can meet the evolving demands of the market while maintaining high standards of quality and safety.
Conclusion
The metal processing industry is undergoing significant transformation driven by advancements in materials, sustainability, and technology. Innovations in high-performance metals, such as high-entropy and multi-principal element alloys, are enhancing properties that meet the demands of sectors like automotive and aerospace.
Sustainability has become a core focus, with practices aimed at reducing environmental impact through recycling, renewable energy, and green metallurgy. These efforts not only support global environmental goals but also improve operational efficiency and economic viability.
Artificial intelligence and machine learning are revolutionizing efficiency and productivity in manufacturing. By utilizing data analytics, companies can optimize processes, predict maintenance needs, and enhance product quality, aligning with the broader Industry 4.0 movement.
In the metal casting sector, the adoption of smart technologies is improving precision and efficiency. Real-time monitoring and automation allow manufacturers to respond quickly to market demands while maintaining safety and quality standards.
In summary, the future of metal processing relies on the integration of advanced materials, sustainable practices, and innovative technologies. Prioritizing these areas will enable the industry to address current challenges and move toward a more efficient and sustainable future.