Blogs
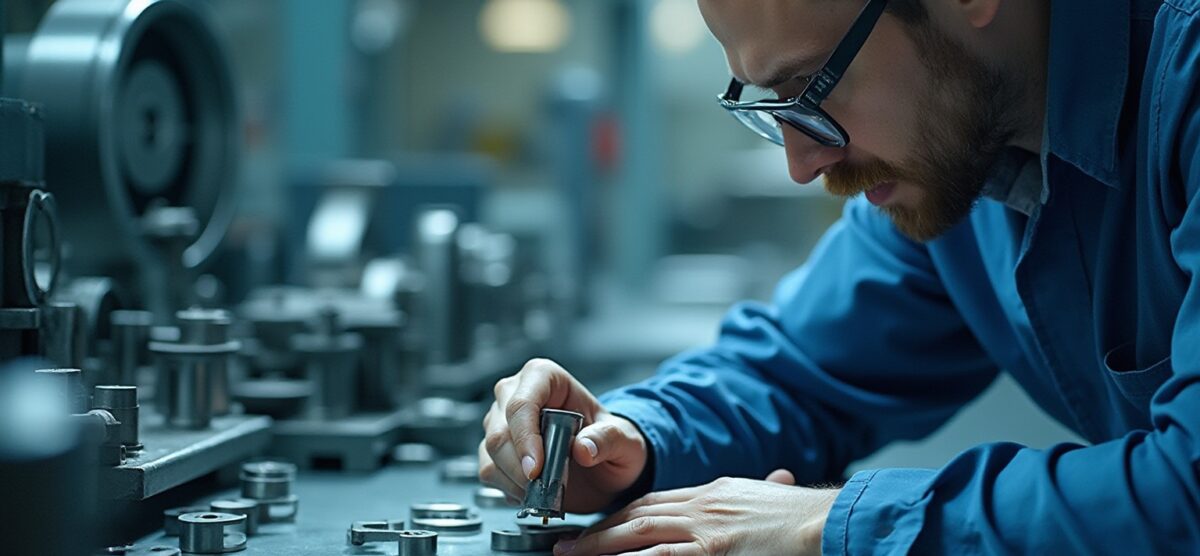
Nickel Alloys PDF Checklist: Essential Resources and Considerations
Overview
The article discusses essential resources and considerations regarding nickel alloys, emphasizing their properties such as corrosion resistance, high-temperature strength, and weldability, which make them suitable for various industrial applications. It highlights the importance of informed procurement decisions by detailing the specific grades of nickel alloys, their applications, and recent advancements in manufacturing processes, including 3D printing and sustainability initiatives.
Introduction
The significance of nickel alloys in various industries cannot be overstated. Renowned for their exceptional properties—including outstanding corrosion resistance, high-temperature strength, and excellent weldability—these materials are indispensable in demanding environments such as aerospace, marine, and chemical processing.
As procurement managers navigate the complexities of selecting the right alloys, understanding the specific attributes of different grades and their applications becomes crucial. This article delves into the properties and uses of nickel alloys, highlights the latest advancements in manufacturing techniques like 3D printing, and emphasizes the importance of environmental considerations in material selection.
By exploring these facets, procurement professionals can make informed decisions that enhance product performance and operational efficiency in their respective industries.
Overview of Nickel Alloys: Properties and Applications
Nickel materials are highly regarded in various industries for their exceptional properties, which include outstanding corrosion resistance, high-temperature strength, and excellent weldability. These characteristics make them especially valuable in challenging situations. The subsequent key characteristics of nickel-based materials are essential for procurement choices:
- Corrosion Resistance: These materials are designed to endure severe conditions, making them suitable for chemical processing and marine uses. Their resilience against oxidation and deterioration is especially critical in supercritical carbon dioxide conditions, which can compromise the integrity of materials. Recent news emphasizes that nickel-based mixtures show vulnerability to oxidation in these environments, highlighting the necessity for meticulous material selection.
- High-Temperature Strength: These materials preserve structural integrity under elevated temperatures, making them appropriate for components in turbine engines and other uses where thermal stresses are common. As noted by Kanesund, turbine blade failures often arise from mechanisms such as creep and type I hot corrosion, highlighting the importance of selecting the right materials. The growing demand for the metal, with an annual price rise in 2021 attributed to stronger use in EV batteries and high need for stainless steel, further emphasizes the critical role of these materials in modern applications.
- Weldability: The ability to easily join these substances through welding processes facilitates efficient manufacturing and assembly, ensuring the structural reliability of final products.
In addition to these properties, it is essential to consider the use of non-sparking tools in explosive environments, where traditional tools may pose safety risks. Non-sparking instruments crafted from particular metal mixtures are essential for avoiding ignition in such dangerous environments. Procurement managers should seek suppliers and manufacturers who specialize in non-sparking tools and high-temperature materials, as these products are vital for ensuring safety and compliance in explosive applications.
Additionally, a case study on the Ni Al-Ag mixture evaluated its tribological behavior in simulated seawater conditions, demonstrating desirable lubricating properties when slid against an aluminum ball. This practical example demonstrates the performance of nickel-based materials in real-world marine settings.
By grasping these characteristics and their implications, along with the latest advancements and challenges in the field, procurement managers can make informed choices when selecting materials detailed in nickel alloys pdf and non-sparking tools for specific uses in aerospace, marine, and chemical processing sectors.
Types of Nickel Alloys: Key Grades and Their Uses
Nickel alloys pdf encompass a variety of grades, each with unique properties tailored for specific applications. At Domadia, we specialize in a diverse range of copper nickel alloys, known for their corrosion-resistant and high-conductivity features, suitable for industries such as marine engineering and electronics. The following are some common grades:
Inconel 600: Renowned for its exceptional resistance to oxidation and degradation, Inconel 600 is widely utilized in chemical processing environments where exposure to aggressive media is prevalent. Its high tensile strength, elongation, and hardness, particularly in 3D printed forms, position it favorably against commercial superalloys. Recent measurements have demonstrated that 3D printed Inconel 600 displays remarkable tensile strength and Vickers hardness, improving its competitiveness in diverse uses.
Inconel 625: This grade features high strength and fatigue resistance, making it an ideal option for aerospace and marine sectors. Recent advancements have highlighted its usage statistics in aerospace, showcasing its critical role in achieving performance under extreme conditions.
Monel 400: Known for its good corrosion resistance in marine settings, Monel 400 is often employed in components such as valves and pumps, where durability is paramount.
Hastelloy C-276: Exceptional in resisting pitting and stress corrosion cracking, Hastelloy C-276 is particularly suited for chemical processing applications, ensuring reliability in harsh environments.
In terms of machining, the cutting speed has been identified as a significant factor, contributing 26.50% to performance outcomes in high-speed micro milling. Furthermore, a case study examining the impact of cooling conditions on tool performance during the machining of Inconel 600 revealed that cryogenic cooling significantly reduces tool wear and improves surface finish. Understanding the unique characteristics of nickel alloys pdf, along with the exceptional properties of our copper nickel compositions for marine, automotive, and electrical industries, is crucial for making informed procurement decisions. We encourage procurement managers to explore our extensive product catalog to find the perfect solutions that align with project specifications and operational requirements.
Nickel Alloys in Advanced Manufacturing: 3D Printing and Beyond
Nickel-based materials are at the forefront of advanced manufacturing techniques, significantly enhancing efficiency and performance across various industries. Key applications include:
- 3D Printing: Nickel alloy powders are pivotal in additive manufacturing, enabling the creation of intricate geometries that traditional methods cannot achieve. According to Fortune Business Insights, the expansion of 3D printing metals for personalized implants and advanced surgical tools is driving product adoption in healthcare.
In 2024, it is anticipated that the utilization of metal mixtures in 3D printing will rise by 30%, indicating an increasing trend in the market.
CNC Machining: High-performance metal mixtures are extensively utilized in CNC machining to create precision components, particularly in the aerospace and automotive sectors, where reliability and durability are paramount. This method not only optimizes material use but also enhances component functionality.
Hybrid Manufacturing: The integration of traditional and additive manufacturing techniques is gaining traction, allowing for optimized material utilization and superior performance. This approach is aligned with the industry’s shift towards sustainable practices, focusing on decarbonization and circular economy solutions. By investigating these sophisticated uses of metal mixtures, companies can achieve substantial cost reductions and enhance product performance, placing themselves advantageously within the changing manufacturing environment.
Furthermore, recent case studies have shown successful applications of metal mixtures in 3D printing, highlighting their effectiveness in practical uses.
Selecting Nickel Alloys: Environmental Considerations and Corrosion Resistance
When choosing nickel mixtures, it is vital to consider several key factors that directly impact material performance and longevity:
Environmental Exposure: Carefully assess the specific environmental conditions to which the mixture will be exposed. Factors such as temperature, humidity, and chemical exposure play a crucial role in determining the material’s suitability. A recent study on high-strength copper-nickel mixtures revealed that environmental factors, including biofouling and seawater conditions, significantly influenced deterioration behavior. The inquiry employed X-ray photoelectron spectroscopy to examine degradation product films, illustrating how these environmental factors can influence the metal’s integrity over time.
Degradation Resistance: Assess the metal’s resistance to different forms of deterioration, including pitting, crevice degradation, and stress cracking. Significantly, copper mixtures demonstrate enhanced resistance to deterioration when contrasted with stainless steel, rendering them especially beneficial in marine settings. For instance, they are widely used in ship hulls and seawater piping systems due to their ability to withstand harsh conditions. In comparison, stainless steel may not perform as well in similar environments. Corrosion resistance data for materials containing nickel in 2024 suggest that specific compositions, especially those fortified with iron and similar metals within the oxide layer, demonstrate improved performance in difficult conditions, frequently decreasing the likelihood of material failure. This enrichment is vital as it affects the overall corrosion characteristics, making it important to take into account when choosing materials for specific uses.
Thermal and Electrical Conductivity: Copper copper-based materials also provide outstanding thermal and electrical conductivity, which is advantageous in fields such as electronics and heat exchangers. Their ductility and ease of fabrication further enhance their suitability for various designs and systems, including automotive brake lines and hydraulic systems.
Antimicrobial Properties: Another significant advantage of copper copper-based materials is their inherent antimicrobial properties, which help reduce the growth of harmful bacteria and biofilms, making them ideal for use in healthcare and food processing environments.
Compliance with Standards: Ensure that the selected materials meet relevant industry standards and regulations. Following established guidelines not only ensures quality but also boosts operational safety and dependability.
By systematically considering these factors, procurement managers can significantly enhance the performance and lifespan of nickel-based materials in their applications, utilizing insights from the nickel alloys pdf to leverage the unique benefits of copper-nickel materials for optimal outcomes.
Future Trends in Nickel Alloys: Innovations and Research Directions
Key trends and innovations in nickel alloys pdf are influencing the future of the industry, making it essential for procurement managers to stay informed. Notable trends include:
Development of New Materials: Ongoing research into novel compositions is yielding substances that not only enhance performance but also aim to reduce production costs. For example, Sandvik’s launch of the supermaterial Sanicro 625 bar (UNS 06625) in April 2022, able to endure temperatures up to 593°C (1100°F), illustrates this progressive innovation.
Sustainability Initiatives: The sector is progressively concentrating on recyclable metal mixtures and adopting eco-friendly manufacturing methods. This shift is driven by growing consumer demand for sustainable materials. A notable quote from a Global Consulting Firm emphasizes this trend:
The precise information given in Persistence Market Research’s reports has been priceless to us. We are very happy with this purchase, since the analysis in the report has been important in formulating our strategies.
This highlights the importance of aligning production strategies with sustainability initiatives, particularly as leading companies like PJSC Mining & Metallurgical Co Norilsk Nickel and Haynes International are investing in greener solutions. Domadia’s ultra-thin metal foils can play a crucial role in these initiatives, providing recyclable options that align with the industry’s sustainability objectives.Digital Manufacturing: The incorporation of digital technologies is revolutionizing metal production and application, enabling greater efficiency and accuracy. This trend not only supports sustainability efforts but also improves the overall quality of alloys. Domadia’s ultra-thin metal foils, designed for compatibility with advanced manufacturing processes, can help companies leverage digital tools to improve production efficiency.
In addition to these trends, procurement managers can benefit from exploring Domadia’s extensive range of ultra-thin metal foils, which includes nickel along with copper, aluminum, stainless steel, and titanium options suitable for aerospace, electronics, medical devices, and more. Domadia is committed to delivering high-quality custom metal foil solutions, backed by industry expertise and exceptional customer service. Understanding these developments and how global events, such as the COVID-19 pandemic, the Russia-Ukraine conflict, and high inflation rates, impact the market as outlined in the nickel alloys PDF is vital for informed decision-making. Companies like PJSC Mining & Metallurgical Co Norilsk Nickel, Haynes International, and Nippon Steels are at the forefront of these innovations, navigating challenges and seizing opportunities in this evolving landscape.
Conclusion
The exploration of nickel alloys reveals their critical role across various industries, driven by their exceptional properties such as:
- Corrosion resistance
- High-temperature strength
- Weldability
Understanding these attributes is essential for procurement managers tasked with selecting the right materials for demanding applications in sectors like aerospace, marine, and chemical processing. The advancements in manufacturing techniques, particularly in 3D printing, further enhance the versatility of nickel alloys, allowing for innovative designs that were previously unattainable.
Moreover, the significance of environmental considerations cannot be overlooked. As procurement decisions increasingly hinge on sustainability, the focus on:
- Recyclable nickel alloys
- Eco-friendly production processes
is becoming paramount. This trend not only aligns with global sustainability goals but also addresses the growing demand for materials that perform reliably in challenging conditions.
Looking ahead, the future of nickel alloys is bright with ongoing research and development leading to new compositions that promise enhanced performance and cost-efficiency. Staying informed about these innovations and market trends is crucial for procurement professionals aiming to make strategic decisions that enhance product performance and operational efficiency. By leveraging the unique properties and advancements of nickel alloys, organizations can position themselves competitively in an evolving landscape, ensuring safety, compliance, and sustainability in their operations.